“AddUp has demonstrated a set of capabilities that enable us to address unique design and application challenges faced by our growing base of aerospace, space, and defense customers.”
Greg Morris
“AddUp group has enabled our complex designs to become a reality using metal Additive Manufacturing, a state-of-the-art process. This will change the way we create and customize a motorcycle. Our creativity is now limitless, which was impossible with traditional metal manufacturing processes.”
Simon Dabadie
“The FormUp350 is one of the only machines on the market that can run both the typical LPBF powder cut and a much finer cut of powder. This gives us flexibility to meet certain challenging applications we may come across in the future.”
Rachel Levine
“AM is in a state of exponential growth with the biggest challenges in adoption being qualification and certification. NSL is focused on partnering with companies who are passionate about driving innovation for metal 3D printing.
Over my past three years working with AddUp they have demonstrated a commitment to industrializing additive technology. The evolution of the FormUp 350 has made significant advancements in its full-field, 4-laser system and its monitoring suite which helps to accelerate the qualification process. Advancements like this prove AddUp to be a major player in the growing AM industry.”
Ed Herderick
“As an early adopter of AddUp machines, I really appreciate capabilities and proactive team spirit, to deliverer parts in a serial mode.”
Aurelien Fussel
“The only French manufacturer of powder bed laser fusion machines (LPB-F) offering rare expertise both on the process and its applications with a machine capable of safely producing high quality parts in a repeatable and reliable way.”
Jean-Christophe Augé
“AddUp’s proprietary technology is a game changer for the medical AM space. Their quad-laser system can print our parts up to 4x faster, and look much better than other platforms we were previously printing on. Our partnership with AddUp has been instrumental in our success and future growth.”
David Nutter
“The FormUp 350 is a dream come true for us. It’s on the cutting edge from both a software and hardware perspective. The large build volume and quad laser system allow us to get production jobs done faster than the competition, while the roller recoater lets us push the design envelope to the next level.”
Noah Smith
THE FORMUP DIFFERENCE
State-of-the-art surface finish at high productivity, that’s what you get when you buy FormUp 350.
Click and move your mouse to rotate the image
Every component of the FormUp 350 has been designed to deliver parts with an incomparable surface finish, limiting the need for time-consuming post-production stages. The FormUp 350 offers enormous flexibility in terms of powder use. Depending on the application, it can be used with the market-standard medium powder. In this case, users can choose between a conventional but flexible scraper spreading system, or a repeatable and robust roller spreading system.
When configured in roller mode, the FormUp 350 can handle fine powders with a D90 of less than 16µm. This makes it possible to reduce lay-up thickness and greatly improve the surface finish of the parts produced.
- Compatible with standard (D90 < 63µm) and fine (D90 < 16µM) powders
- Flexibility in the use of different spreading systems
- Improved surface finish
- Reduced quantity of media required
- Versatile recipe parameters to suit different applications
Productivity can be optimized in several ways: reducing waiting times between production runs, maximizing melting speed, optimizing dispensing speed, etc. But there are also other factors to consider after production has been completed, such as the support removal stage or the amount of post-processing to be applied. The FormUp 350 addresses each of these points and offers users numerous technological building blocks to maximize the OEE of their equipment.
- Each of the 4 lasers cover the entire platform: no overlap management to anticipate
- Automatic balancing of head loads on each element to be melted
- Bi-directional recoating with hidden-time cycle preparation
- Adaptive strategies according to part height or angle
- Build chamber cooling circuits for rapid release of the FormUp 350
Customer Successes
Read about the success our customers have had with the FormUp 350 on a variety of applications
Acetabular Hip Cup Implant
Acetabular Cups plate History Acetabular cups are used during the total hip replacements to sit against the..
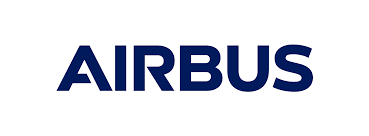
ADS Spherical Tank
AddUp 3D printed a spherical tank that can hold the operating pressure of 60 bar for two-phase fluid loop applications using fluids in a supercritical state at maximum non-operating system...
Aerospace Support Part
See how AddUp and PrintSky develop a good rigidity/mass balance with a high technical and economic value for an aeronautical part. The CEA (French Alternative Energies and Atomic Energy Commission) has joined forces...
Aircraft Floor Bracket
This proof of concept demonstrated by Add Up showcases the value of using Additive Manufacturing (AM) for aeronautics by applying topological optimization to an aircraft floor bracket. History An aircraft floor bracket...
Extrusion Die
This study explores the use of additive manufacturing, specifically Powder Bed Fusion (PBF), to create extrusion dies with improved performance and cooling capabilities. History Extrusion is a popular manufacturing method for parts...
Metal 3D Printing
FormUp Heat Exchanger
This case study presents the development of an optimized heat exchanger for the Form Up® 350 machine,. The goal was to improve heat dissipation and adapt the dimensions for easy installation.
French Navy Scraper
How reverse engineering process and metal 3D printing allow to produce an identical and durable strategic part for a boat. As this part was no longer in stock, nor produced by...
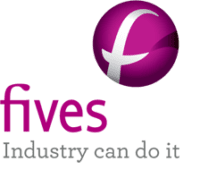
TOOLING
Grinding System Coolant Nozzle
A one-piece optimized coolant nozzle that delivers coolant flow into precise locations. The nozzle was officially installed grinding machine, optimizing its performance. History Fives is an international industrial engineering group with over 200+...
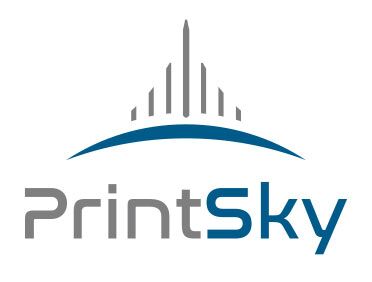
Heat Exchanger
Read the case study to understand how to obtain a viable heat exchanger with good thermal and mechanical properties in a reduced time frame. AddUp and PrintSky join forces to increase...
TOOLING
Heat Exchanger Aluminum AlSi7Mg
The goal is to demonstrate an interest in the PBF technology to create heat exchangers with improved compactness, good thermal performance, and metal 3D printed in one go. Answering the aerospace...
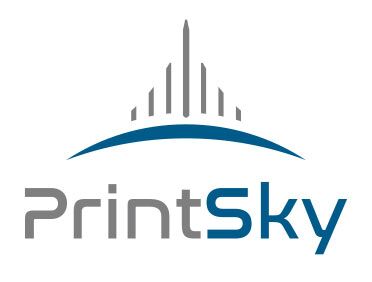
HEWAM Heat Exchanger (Inconel)
Addup 3D printed a double-curved heat exchanger, suitable for curved surfaces with very successful thermal performance and produced in one go. For thermal equipment, additive manufacturing has a huge advantage. It...
Hydraulic Block
Hydraulic blocks are present in most machines and devices, throughout a variety of industries. In the case of this hydraulic block, the entire part is 3D printed in a single...
Impeller Wheel
This case study explores the feasibility of using additive manufacturing, specifically the Form Up 350 PBF machine, to produce over 100,000 Impeller wheels annually for Ford, replacing traditional machining techniques. History Ford...
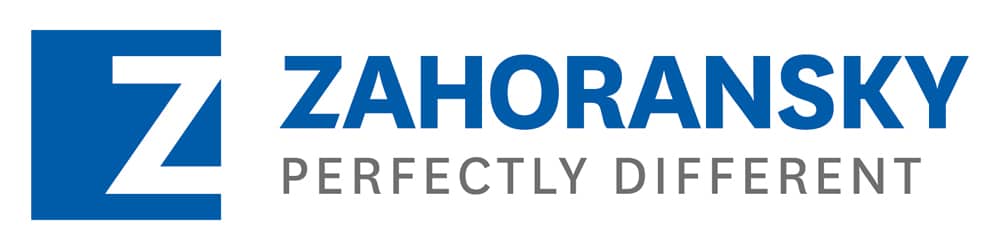
Injection Mold
See how to improve the cooling of the inserts on a mold using additive technology while increasing the mold’s performance and decreasing the cycle time. Short injection times are crucial for...
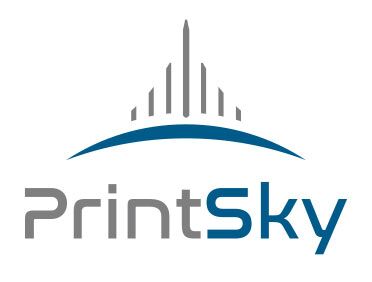
Joystick
The freedom of design linked to metal 3D printing allows the production of customized handles, of different dimensions, without tooling, thus limiting the costs and manufacturing lead times of the...
Michelin Tires Sipes
Discover how Michelin produces over one million tire sipes a year for their production molds using metal 3D printing When Michelin found that the metal AM machines on the market did not meet their high-quality...
Orano Manifold Spare Part
The goal of the project is to verify the technical and economic feasibility of additive manufacturing of complex geometric replacement parts for equipment that is no longer manufactured. The project aims...
Patient Specific Implants
This case study highlights the advantages of using additive manufacturing (AM) for Patient Specific Implants (PSI) in the orthopedic industry. By shifting from traditional manufacturing to AM, orthopedic OEMs can...
Rocket Nozzle
AddUp optimized the design of a rocket nozzle to improve the performance of a micro-launch vehicle. Metal additive manufacturing can lead to fuel and production savings in aerospace. In this case...
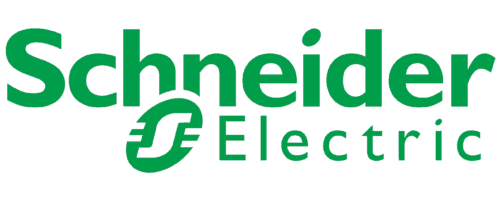
Schneider Inductor
See how this 3D printed inductor has met all quality specifications, and its industrial performance has surpassed initial expectations. An induction heating coil is a production tool that allows performing a...
Siebenwurst Injection Mold
This case study explores the benefits of using 3D printed injection molds with optimized cooling channels. The project between Siebenwurst and AddUp aimed to improve productivity and quality in the...
Space Camera Support
An additively manufactured camera support, designed to withstand acceleration and vibration during launch to space and to hold a camera and its lens in position during the production phases of...
Spine Implants
This case study focuses on spine implants and the challenges faced in their manufacturing process today. Additive Manufacturing (AM) offers benefits such as lattice design and surface roughness, leading to...
Tibia Tray
This case study focuses on tibia trays in orthopedic manufacturing and the challenges faced in producing highly complex and customized implants. Additive Manufacturing (AM) using biocompatible materials like titanium offers...
A Full Set of Advanced Technologies
At AddUp, we know that the needs of manufacturers, driven by stringent regulatory requirements, are very diverse. Each requires a high level of performance, security, and confidence.
Resulting from 7 years of development and continuous improvement, the FormUp 350 offers users a complete set of technological assets, proven layer after layer on our machines currently in production with customers across the world.
MASTER THE POWDER
Powder is a key element of final parts quality. It is a very sensitive element which can be highly degraded when exposed to oxygen, smokes, … The Autonomous Power Module (APM), developed exclusively for the FormUp in partnership with AZO, is in charge of the full powder management. Unlike other solutions, the APM keeps powder in fully inerted condition from start to finish. It guarantees a constant supply of powder, without interrupting production, regardless of the quantities to be produced.
Furthermore, complete inerting of the APM for powder storage, conveying, and handling with use of a glove box during the loading and unloading of the powder ensures that the powder is not exposed to the environment or to operators. The APM’s powder sampling device allows for easy sampling of powder at any time through the glovebox, minimizing risk of exposure to powders. The APM also has automatic cycles for circuit purge and emptying ensuring that the powder handling system is always clean.
OPERATOR SAFETY
Managing the fumes generated during melting is a particularly important step. Depending on the material used, the number of lasers operated and the surface area to be fused, the quantity of fumes produced can saturate an inefficient treatment system and potentially create serious risks for operators.
The FormUp 350 features a top-of-the-range treatment system capable of efficiently collecting the fumes created, while automatically ensuring the cleaning and passivation phases. This system is based on 6 parallel filters with a service life of 3 years under intensive conditions.
- Industrial fume management
- Real-time and historical cycle traceability
- 3-year filter life
- Automatic passivation and cleaning sequences
PRESS THE BUTTON
On the FormUp 350, every effort has been made to minimize operator workload and maximize operational efficiency.
As soon as the tray is loaded, NCore, the FormUp 350’s on-board software, automatically handles all operations: plate hooking and referencing, inerting sequence, hooking grid firing and production start-up. If required, automatic mode can be replaced by manual mode, while maintaining a high level of assistance. The user interface then exposes a succession of predetermined steps, which can be sequenced according to the user’s needs. A customizable production start-up checklist can also be presented to confirm the machine’s operating status prior to production. At the end of production, the optimized cooling sequence takes over, freeing up access to the de-soldering sequence as soon as possible. Production reports, containing all the information required for traceability purposes, are generated in parallel.
- Automatic product launch sequences
- Simplified workflow for manual use
- Customizable start-up checklists
- Automatic end-of-production management with full reporting
TRACEABILITY FROM START TO FINISH
AddUp software has a view of what is occurring inside the machine, analysis of the execution of production, and analysis of the quality of layering. Each of these solutions and the parameters can be tailored to different needs of various manufacturing roles.
Manufacturing Managers will follow the load of their workshop and make sure they do not encounter any bottlenecks. Quality Experts will have access to a Build Report which includes every single event during production, with an OK / INCOMPLETE / FLAG status automatically generated. Finally, Process Experts will have full control over dozens of variables, with advanced features to cross reference Key Process Parameters or KPPs.
YOUR MACHINE. YOUR IP.
Thanks to the open approach of our software, our customers can develop complex parameterizations to meet their most demanding requirements.
Respect for our customers’ intellectual property created with AddUp solutions is at the heart of our concerns. That’s why AddUp guarantees total watertightness of information within the machine and requires no Internet connection or information sharing under production conditions.
For customers who so wish, AddUp offers a remote maintenance option based on high-level secure solutions.
Technical Specifications
The modular design of the FormUp 350 allows each manufacturer to configure the machine according to their needs.
Opt for a controlled investment, with a machine designed to be scalable. Whatever the chosen configuration, you can add new modules, options or equipment to your machine at any time, thus delaying its obsolescence. AddUp is committed to ensuring that all future improvements offered on this range are compatible with your machine.
Standard Machine Configuration
SIZE | |
---|---|
Machine dimensions | L 6.3 x W 2.2 x H 2.45 m |
Weight | 5 tons (w/o powder) |
Build volume | L 350 x W 350 x H 350* mm (~43 L) – no bolt holes |
POWDER | |
---|---|
Powder recoating device | Bidirectional roller or scraper (brush or silicone) |
Autonomous Powder Module (APM) | For all types of powder, continous supply (after AddUp validation) |
Sieving | Ultrasonic sieving device integrated in APM |
Powder recovery | Powder recovery during production |
Vacuum | Inerted and integrated |
LASERS | |
---|---|
Optical type | Up to 4 Ytterbium continous fiber lasers |
Laser power | 500 W |
Spot diameter | 70 μm |
Platform coverage | 100% coverage by each laser |
3D scanners | 2 axes for X/Y displacement + 1 axis for focus |
Max speed | 10 m/s |
Accuracy | 35 μm |
Wavelength | 1070 nm |
PART PROPERTIES | |
---|---|
Avg. time between production | 1 hour or less |
Precision | Up to 0.1 mm** |
Density | Up to 99.99%** |
**: geometry dependent |
FILTRATION | |
---|---|
Laser glass protection | Cross jet system |
Fume and fusion residue | Filtration device w/automatic unclogging Calcium carbonate residue passivation |
Filter lifetime | > 3 years |
GAS SUPPLY | |
---|---|
Gas type | Argon or nitrogen with programmable O2 levels |
Laminar flow | Adjustable from 0.5 to 3 m/s |
SOFTWARE | |
---|---|
CAM solutions | AddUp Manager or Ntwin |
Remote maintenance | AddUp Remote Control |
VISUALS | |
---|---|
Visualization | Real-time supervision HD camera for taking photos |
Materials Available
The FormUp 350 was designed to handle a variety of metallic powders. AddUp offers ready-to-use parameters for each of those, but customers can also define or fine-tune those depending on their needs.
LEARN MORE ABOUT MATERIALS FOR THE FORMUP 350Smart Software
AM is an incredibly advanced technology to master due to the various scales we must deal with, generating millions of vectors corresponding to miles of trajectories, at a speed of several meters per second, being drawn by a “pencil” having a diameter of a hair. Many components such as the platform, laser, air flow, for inerting conditions will have to work together to create the part as desired. To assure all these components are working in synergy, AddUp offers an end-to-end solution to its customers, with many flexibilities:
ADDUP MANAGER
Easy-to-use CAM software that can manage large 3D files with high resolutions levels and accurate production time estimates. AddUp Manager also provides access to advanced print and recoating strategies to improve surface finish.
NCORE
The brain behind the machine. NCore allows you to generate your own productions check lists, so that your staff will have everything before they can launch a production. It also gives a fully traceable dataset of the print generating pictures of after melting and recoating along with live access to a camera with remote control.
ADDUP DASHBOARDS
Based on Grafana, a fully customizable data visualization solution, AddUp Dashboards provides hands-on machine conditions. Create your own visualization sets, define variables you want to see and set your conditional alerts. Read and write administration can also be set to adjust different needs for different profiles.
RECOATING MONITORING
The Recoating Monitoring system prevents production stops from recoating. This solution, based on picture analyses, automatically detects flaws during production, including powder drops or lack of powder, for example. KPIs are also directly available in the AddUp Dashboards, so you can set up alerts.
MELTPOOL MONITORING
The Meltpool Monitoring system allows you to track spatial and temporal information including Power, IR, Positions, and laser status. There is real-time visualization of the production condition at micro-scale, with unique possibilities to improve process performance and track parts quality.
QUALIFICATIONS
AddUp operates with a strong focus on quality, efficiency and customer-centricity. AddUp’s processes and systems have been reviewed and validated for compliance to applicable ISO standards. We hold multiple certifications around the globe and can help speed up the process of qualifying your part applications based on the needs for your specific industry.
BEYOND THE MACHINE
AddUp experts are ready to support you throughout your AM journey. Even after your machine is up and running, our team is committed to providing a gold standard of service. We pride ourselves on our industry leading response times and strive to exceed customer expectations by delivering exceptional experiences. You can count on AddUp to be the partner you rely on to consistently deliver high-quality service.
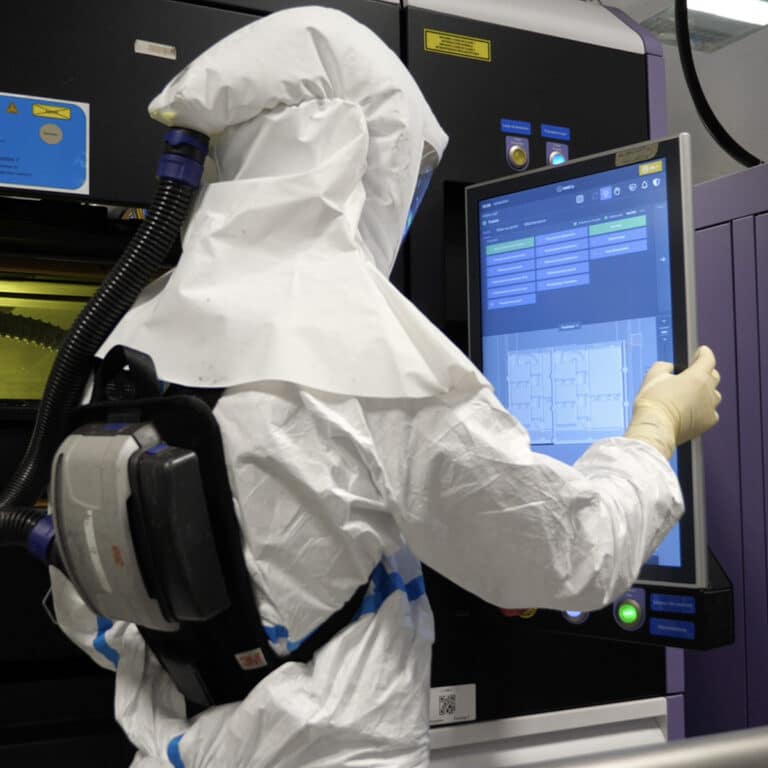
Enter the Smart Era in Metal Manufacturing
Today’s metal 3D printers make parts that can’t be made by traditional manufacturing methods. Metal Additive Manufacturing is the way of the future and AddUp is leading the way.
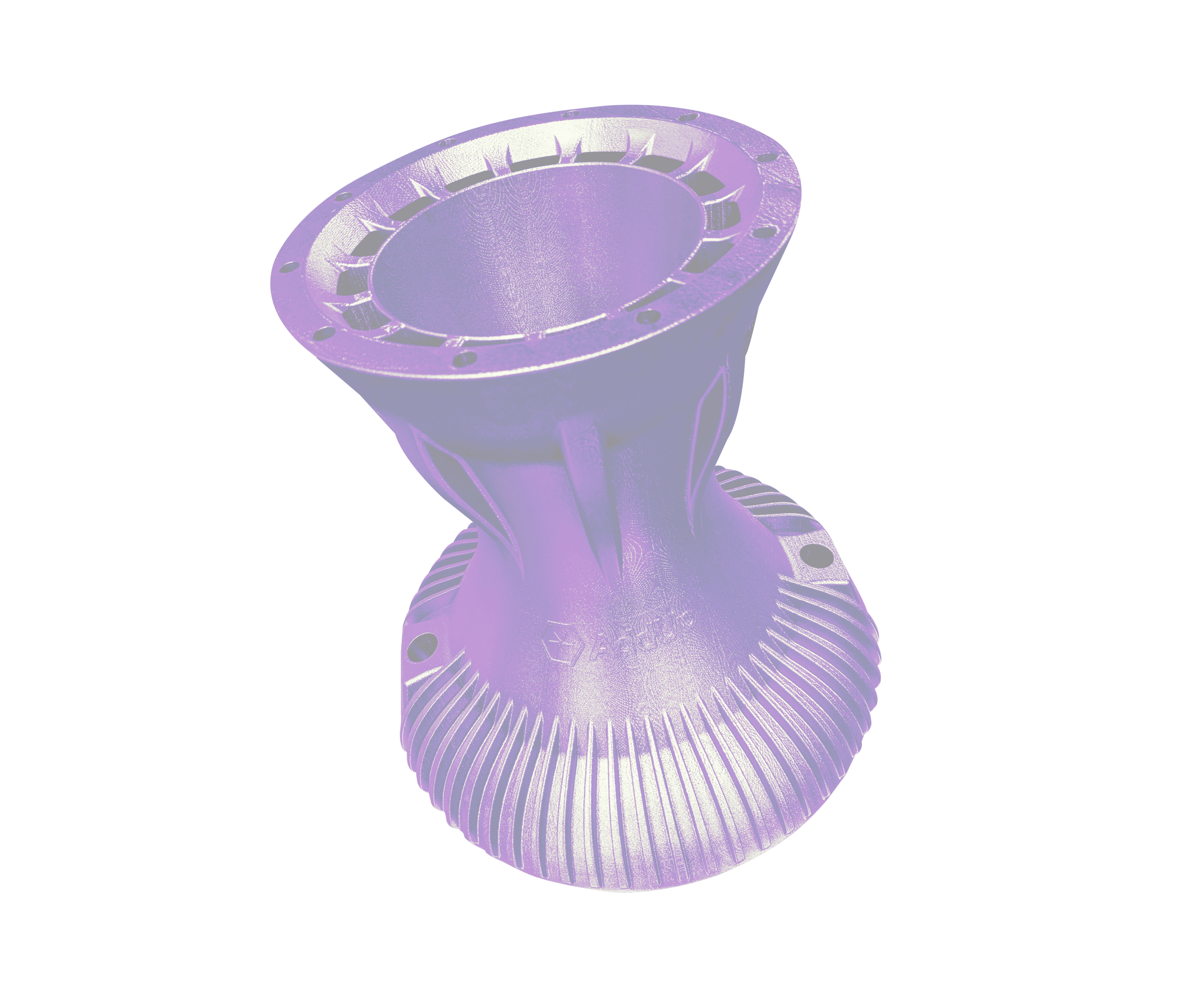