INDUSTRY
Automotive
CHALLENGE
Decrease production time and cost while improving performance when compared to traditional manufacturing by optimizing scan strategy.
KEY BENEFITS
- Optimized scan strategy for better surface finish for Impeller geometries
- Proved PBF as a viable option for Impeller’s in the automotive industry in terms of both cost and performance
- Compared test and inspection methods for geometric and density uniformity of additive versus traditional parts
Increased Productivity
This case study explores the feasibility of using additive manufacturing, specifically the Form Up 350 PBF machine, to produce over 100,000 Impeller wheels annually for Ford, replacing traditional machining techniques.
History
Ford uses traditional methods to manufacture over 100,000 Impeller wheels per year. Ford, Oak Ridge National Labs, and AddUp conducted a study to determine the feasibility of producing the impeller wheels through additive manufacturing using the FormUp 350.
Ford would leverage their extensive history of over a century of automotive experience. Oak Ridge National Labs would optimize the scan strategy and the DOE of contour passes. AddUp brings the expertise in design, manufacturing, and automation for large scale production using their industrial FormUp 350 PBF machine.

Challenges
Ford currently manufactures by utilizing traditional machining techniques to create their impeller wheels. The challenge proposed to AddUp was to investigate the performance of PBF technology as a replacement to mass manufacture these parts. The goal was to decrease production time and cost while improving performance when compared to traditional manufacturing. Thus, a single contour pass is sufficient given a position beyond the hatch lines to remove hatch patterning. Tolerances were also sufficient from the printer.
The result should be to effectively create 100,000 Impellers through additive manufacturing and create an optimal printing strategy for performance, leveraging the design freedom from AM while optimizing the scanning strategy for surface finish and productivity.
SOLUTIONS
The original test part was made from maraging steel to test the feasibility of geometries which resulted in demonstrating the viability of additively manufacturing a complete turbo wheel without the need for supporting low-angled features. The surface finish still had to be optimized and geometric tolerances in the as-printed conditions as close to the CAD model as possible. L-PBF often uses a contour followed by infill melt strategy to obtain parts with superior surface finish. If an insufficient overlap is used between the contour and infill, it can result in porosity at the contour-infill interface thereby making the part susceptible to premature failure. The part was tested with 1 contour pass and 5 contour passes. When melting with 5 contour passes, the surface had increased porosity compared to a single pass.
The Results
With the need for a rugged, heat resistant material, Inconel 718 was chosen. When printed with Inconel 718, a support structure on the bottom of the wheel was required. AddUp printed a simulation test build of 9 impeller wheels using Inconel 718. Following post processing, two wheels were selected to be balance tested.
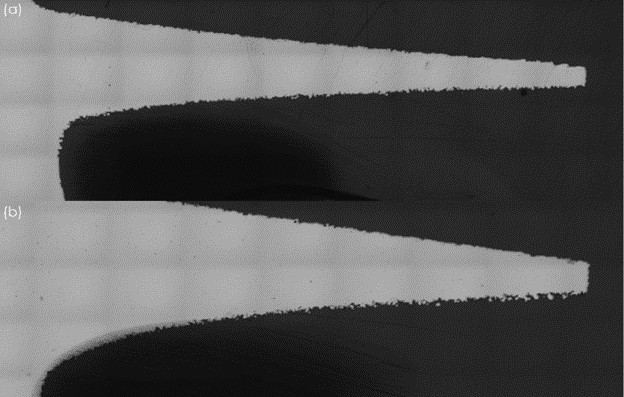
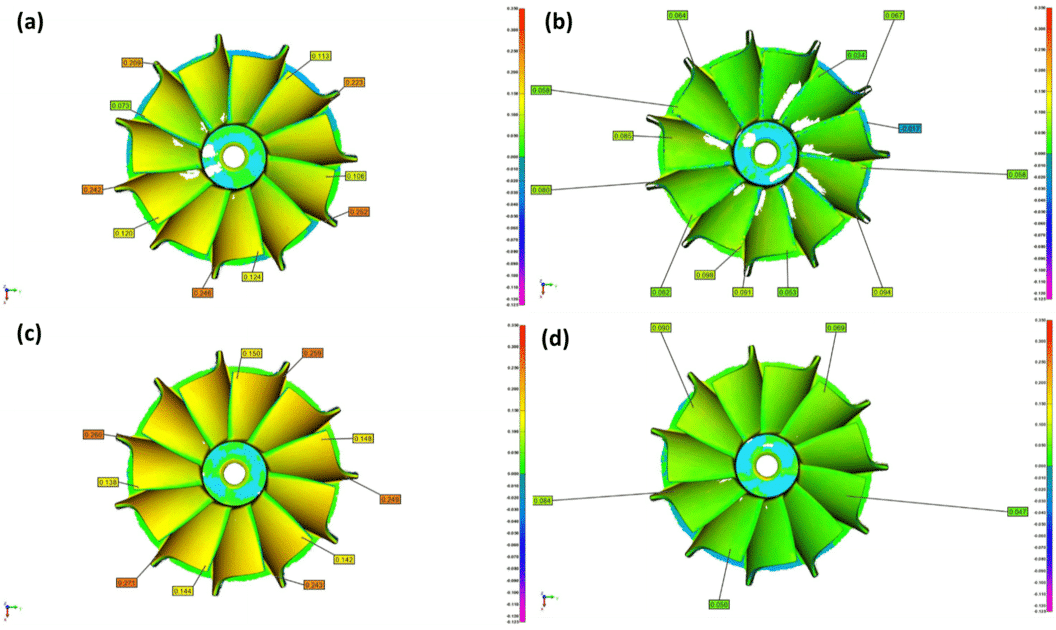
(a) Optical micrograph of single contour pass downskin
(b) Optical micrograph of downskin using five contour passes. Although more contour passes may be useful, the position of the outermost contour drives surface finish as shown by partially melted particles clinging to the surface in.
Geometric tolerances measured from light-scanning of turbo wheels with the outer contour extending the following distance beyond CAD boundary:
- (a) #08 at 36µm
- (b) #11 at 11µm
- (c) #13 at 61µm and
- (d) #19 at 36µm but melted outer to inner.
PART NAME | IMPELLER |
---|---|
3D printer make and model | AddUp FormUp 350 |
Build Plate size | 350 x 350 mm2 |
Number of parts per batch | 25 |
Print time per batch | 32.28 hours |
Material Cost estimate for Inconel 718 | $70/kg |
Mass of part | 0.311 kg |
Mass of support material | 0.05 kg |
Depowder time per batch | 0.5 hours |
Support Removal time per batch | 30 hours |
Post processing time per batch (heat treatment) | 12 hours |
Annual volume required | 100,000 units a year |