INDUSTRY
Automotive
CHALLENGE
Decrease production time and cost while improving performance when compared to traditional manufacturing by optimizing scan strategy.
KEY BENEFITS
- Optimized scan strategy for better surface finish for Impeller geometries
- Proved PBF as a viable option for Impeller’s in the automotive industry in terms of both cost and performance
- Compared test and inspection methods for geometric and density uniformity of additive versus traditional parts
Increased Productivity
In dieser Fallstudie wird die Machbarkeit des Einsatzes der additiven Fertigung, insbesondere der Form Up 350 PBF-Maschine, zur Herstellung von über 100.000 Impeller- Rädern pro Jahr für Ford untersucht, die die herkömmlichen Bearbeitungsmethoden ersetzen.
Geschichte
Ford verwendet traditionelle Methoden zur Herstellung von über 100.000 Impeller-Rädern pro Jahr. Ford, Oak Ridge National Labs und AddUp führten eine Studie durch, um die Machbarkeit der Herstellung von Laufrädern durch additive Fertigung mit dem FormUp 350 zu ermitteln.
Ford würde seine umfassende Erfahrung aus über einem Jahrhundert Automobilbau nutzen. Oak Ridge National Labs würde die Scanstrategie und die DOE der Konturdurchgänge optimieren. AddUp bringt das Fachwissen in den Bereichen Design, Fertigung und Automatisierung für die Großserienproduktion mit seiner industriellen FormUp 350 PBF-Maschine ein.

Herausforderungen
Ford fertigt derzeit seine Flügelräder mit traditionellen Bearbeitungsmethoden. Die Aufgabe, die AddUp gestellt wurde, bestand darin, die Leistung der PBF-Technologie als Ersatz für die Massenfertigung dieser Teile zu untersuchen. Das Ziel war es, die Produktionszeit und -kosten zu senken und gleichzeitig die Leistung im Vergleich zur traditionellen Fertigung zu verbessern.
Daher reicht ein einziger Konturdurchgang aus, wenn die Position außerhalb der Schraffurlinien liegt, um die Schraffurmusterung zu entfernen. Die Toleranzen des Druckers waren ebenfalls ausreichend.
Das Ergebnis sollte die effektive Herstellung von 100.000 Impellern durch additive Fertigung und die Entwicklung einer optimalen Druckstrategie für die Leistung sein, die die Designfreiheit von AM nutzt und gleichzeitig die Scanstrategie für Oberflächengüte und Produktivität optimiert.
Lösung
Das ursprüngliche Testteil wurde aus martensitaushärtendem Stahl hergestellt, um die Machbarkeit von Geometrien zu testen, was dazu führte, dass die Machbarkeit der additiven Fertigung eines kompletten Turborads ohne die Notwendigkeit von niedrig abgewinkelten Stützen nachgewiesen werden konnte. Die Oberflächenbeschaffenheit musste noch optimiert werden, und die geometrischen Toleranzen im gedruckten Zustand sollten dem CAD-Modell so nahe wie möglich kommen. Bei L-PBF wird häufig eine Kontur- gefolgt von einer Infill-Melt-Strategie verwendet, um Teile mit hervorragender Oberflächengüte zu erhalten. Wird eine unzureichende Überlappung zwischen Kontur und Füllung verwendet, kann dies zu Porosität an der Schnittstelle zwischen Kontur und Füllung führen, wodurch das Teil anfällig für vorzeitiges Versagen wird. Das Teil wurde mit 1 Konturdurchgang und 5 Konturdurchgängen getestet. Beim Schmelzen mit 5 Konturdurchgängen wies die Oberfläche im Vergleich zu einem einzelnen Durchgang eine erhöhte Porosität auf.
Ergebnisse
Da ein robustes, hitzebeständiges Material benötigt wurde, fiel die Wahl auf Inconel 718. Beim Druck mit Inconel 718 war eine Stützstruktur an der Unterseite des Rades erforderlich. AddUp druckte einen Simulationstest von 9 Laufrädern aus Inconel 718. Nach der Nachbearbeitung wurden zwei Räder für einen Wuchttest ausgewählt.
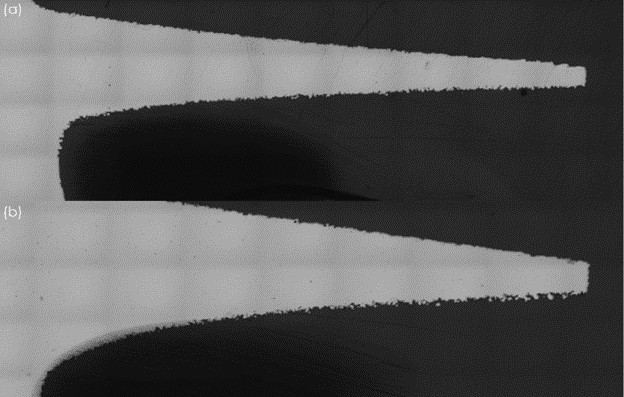
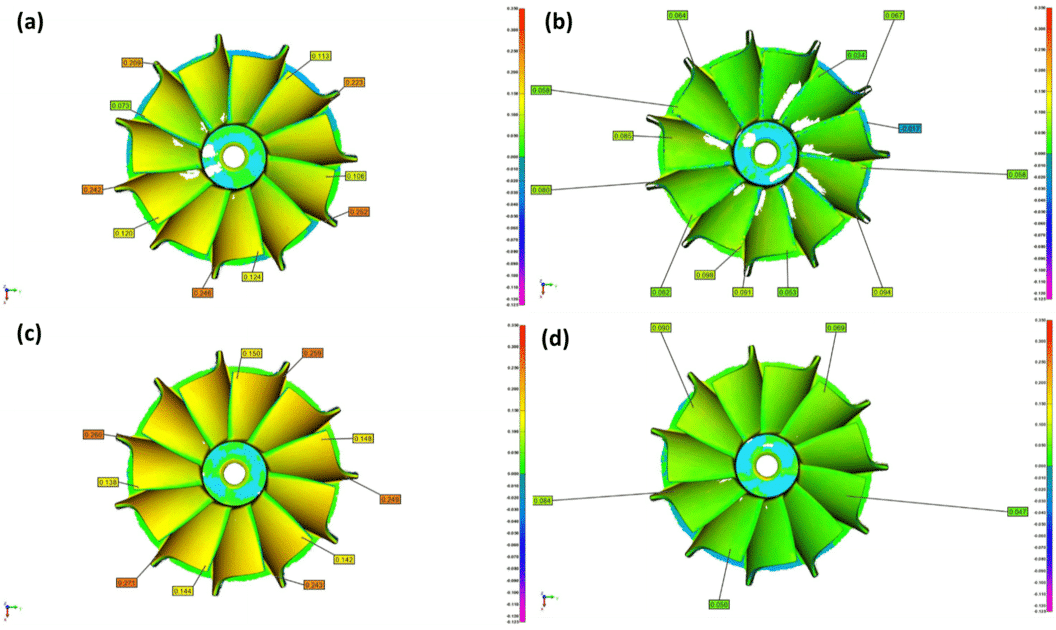
PART NAME | IMPELLER |
---|---|
3D printer make and model | AddUp FormUp 350 |
Build Plate size | 350 x 350 mm2 |
Number of parts per batch | 25 |
Print time per batch | 32.28 hours |
Material Cost estimate for Inconel 718 | $70/kg |
Mass of part | 0.311 kg |
Mass of support material | 0.05 kg |
Depowder time per batch | 0.5 hours |
Support Removal time per batch | 30 hours |
Post processing time per batch (heat treatment) | 12 hours |
Annual volume required | 100,000 units a year |