Addup hat einen doppelt gekrümmten Wärmetauscher 3D-gedruckt, der für gekrümmte Oberflächen geeignet ist, eine sehr gute thermische Leistung aufweist und in einem Arbeitsgang hergestellt wurde.

Für thermische Geräte hat die additive Fertigung einen großen Vorteil. Sie ermöglicht die Entwicklung komplexer Kanalformen und verbessert so die thermische Leistung und reduziert das Volumen. Sie ermöglicht auch die Herstellung von Formen, die auf herkömmliche Weise für diese Art von Geräten nicht herstellbar sind (z. B. doppelt gekrümmte Kanäle). Laden Sie diese HEWAM-Projektfallstudie herunter, einen Wärmetauscher mit komplexen Geometrien, der von PrintSky (Joint-Venture AddUp SOGECLAIR) und Temisth entwickelt wurde.
INDUSTRY
Aeronautics
CHALLENGE
3D print a heat exchanger with innovative design
KEY BENEFITS
- Modular heat exchanger concept
- A double-curved heat exchanger
- Part printed in one go with thin walls
- When damaged, replacement of the unit instead of the whole arrangement
Custom Shape
Assembly
Performance
Thin Walls
Geschichte
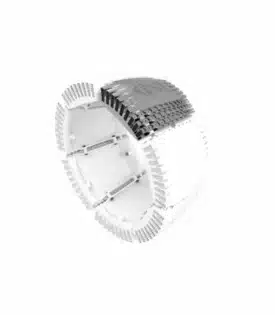
Ein Wärmetauscher ist ein System, das zur Übertragung von Wärme zwischen einer Quelle und einem Arbeitsmedium dient. Wärmetauscher werden sowohl bei Kühl- als auch bei Heizprozessen eingesetzt. Je nach Anwendung können die Flüssigkeiten getrennt sein, um eine Vermischung zu verhindern, oder sie können auch in direktem Kontakt stehen. In der Luftfahrtindustrie werden Wärmetauscher in Flugzeugen eingesetzt, um die Wärme aus dem das Ölsystem des Motors, um kalten Kraftstoff zu erwärmen. Dies verbessert die Kraftstoffeffizienz und verringert auch die Möglichkeit, dass sich Wasser im Kraftstoff einlagert, was zum Einfrieren führen könnte.
HEWAM (Heat Exchanger With Additive Manufacturing) ist ein Projekt, das darauf abzielt, einen Wärmetauscher zu entwickeln, der das gesamte Potenzial der additiven Fertigung nutzt und eine Geometrie aufweist, die sich für eine Vielzahl von Oberflächen und Volumina eignet, die in der Luft- und Raumfahrtindustrie. Dieses Projekt wurde von PrintSky und Temisth entwickelt. PrintSky ist ein Joint-Venture zwischen der AddUp-Gruppe, einem Experten für die additive Fertigung von Metallen, und SOGECLAIR, einem der international führenden Anbieter von Lösungen mit hohem Mehrwert für die Luft- und Raumfahrt sowie den zivilen und militärischen Transport. Temisth ist ein Unternehmen, das sich auf die Entwicklung maßgeschneiderter thermischer Lösungen durch additive Fertigung spezialisiert hat.
PrintSky war für den Designaspekt des Projekts verantwortlich und entwickelte eine eigene Methodik zur Bestimmung der mechanischen, thermischen und fertigungstechnischen Eigenschaften des Metallteils.
Die Produktion wurde dann an die Experten von AddUp übergeben, die dieses Bauteil für die Luftfahrt auf ihrer FormUp® 350 Maschine 3D-gedruckt haben. Ziel war es, einen kompakten Wärmetauscher nach dem PBF-Verfahren (Laser Powder Bed Fusion) mit einer innovativen Form und vor allem so effizient wie „traditionell“ hergestellte Wärmetauscher herzustellen. Im Anschluss an die Produktion wurde HEWAM auf einer von Temisth entwickelten Testschleife getestet.
Herausforderung
Das Ziel von HEWAM war es, eine Flüssigkeit wie Öl, das mit 110°C in den Wärmetauscher eintritt, mit Umgebungsluft von -50°C zu kühlen. Der Massendurchsatz des Öls ist festgelegt. Der Luftmassenstrom wird durch den dynamischen Druck des im Bereich des Wärmetauschers ankommenden Luftstroms und die Druckverlusteigenschaften des Geräts bestimmt. Ziel war es, 2200 W der Ölzirkulation (32 g/s ~2,4 l/min) auf einem Modul des Wärmetauschers zu entfernen, indem ein ausreichender Luftstrom durch den Wärmetauscher gewährleistet wird. Das wichtigste physikalische Problem bei diesem Wärmetauscher war die Gewährleistung eines ausreichenden Luftstroms innerhalb des Wärmetauschers mit einem hohen Wärmeübertragungskoeffizienten.
Lösung
Die Gruppen entwickelten eine spezifische Methodik, um die thermischen Anforderungen mit den mechanischen Einschränkungen und der Machbarkeit der additiven Fertigung für HEWAM zu gewährleisten. Es wurde ein spezielles Design entwickelt, das die Schwankungen der Lufttemperatur (von -50°C bis +25°C) und damit der Dichte berücksichtigt. Die Kanalbreite war erhöht, um die Luftbeschleunigung und den Druckabfall zu begrenzen. Um die thermische Leistung aufrechtzuerhalten, haben die Rippen eine anpassungsfähige Geometrie entlang des Luftstroms, um Änderungen der Luftgeschwindigkeit und der Kanalgröße zu berücksichtigen. Das physische Design des Bauteils wurde so gestaltet, dass es für eine Vielzahl von Oberflächen und Volumina geeignet ist, die in der Luft- und Raumfahrtindustrie verwendet werden. Es wurde so konzipiert, dass es eine doppelte Formkurve aufweist, die es ermöglicht, dieses Teil an die Krümmung von Flugzeugtriebwerken anzupassen.
HEWAM wurde zweimal gedruckt, wobei zwei verschiedene Materialien verwendet wurden. Erstens: Inconel 718. Dieses Material ist mehr als dreimal so schwer wie Aluminium und weniger leitfähig, weist aber für die additive Fertigung interessantere Eigenschaften auf. Mit Inconel sind dünne Wände (<0,5 mm) und Rippen (0,15 mm) möglich, ohne dass Leckagen auftreten. Die Konstruktion des Wärmetauschers mit diesen dünnen Merkmalen ermöglicht ähnliche Leistungs- und Gewichtseigenschaften, wie sie mit Aluminium möglich sind.
Ein letzter Vorteil dieses 3D-gedruckten Teils ist die Möglichkeit, den Wärmetauscher zu aktualisieren, ohne ein neues Werkzeug entwickeln zu müssen.
Ergebnisse
Das Endergebnis ist ein doppelt gekrümmter Wärmetauscher, der für gekrümmte Oberflächen geeignet ist, eine sehr gute thermische Leistung aufweist und in einem Arbeitsgang gedruckt wird. Eine modulare Lösung: Die Wärmetauscher können nebeneinander angeordnet werden, um eine hohe Austauschleistung zu erzielen. Die gekrümmte Form eignet sich für den Einbau in Triebwerkspylonen von Flugzeugen. Die Tests bestätigten die Dichtheit des Teils und seine Leistung, die insbesondere im Vergleich zu konventionellen Herstellungsverfahren sehr gut waren.
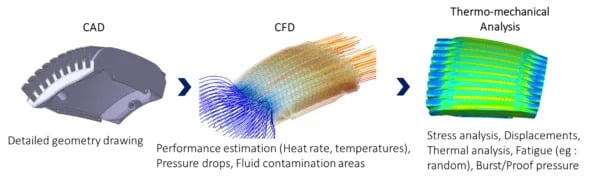
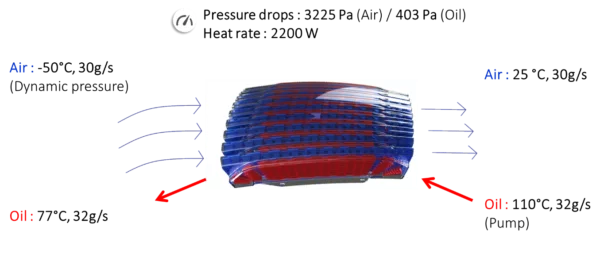
Für thermische Anlagen hat AM einen großen Vorteil. Es ermöglicht die Entwicklung komplexer Kanalformen, die die thermische Leistung verbessern und das Volumen reduzieren. Das AM-Verfahren bietet auch die Möglichkeit, Formen herzustellen, die auf herkömmliche Weise für diese Art von Geräten unmöglich sind (z. B. doppelt gekrümmte Kanäle).
Darüber hinaus ermöglicht die Technologie der additiven Fertigung auch die Herstellung eines Teils aus einem einzigen Block in einem Arbeitsgang. Dadurch wird jede weitere Manipulation des Teils vermieden, die es verändern könnte, wie z. B. Montage oder Bearbeitung. Es wird auch nicht geschweißt, was bedeutet, dass bei diesem neuen Wärmetauscher keine Flüssigkeit austreten kann. Da AM die Möglichkeit bietet, in einem Stück zu drucken, werden nur die funktionalen Bereiche des Metallteils gedruckt (Strömungsflächen und Befestigungsflächen), was zu erheblichen Materialeinsparungen führt.