Mit der DED-Technologie können Teile mit komplexen Formen ohne zusätzliche Werkzeuge gedruckt werden.
Der griechische Hersteller Spyros Panopoulos Automotive hat AddUp beauftragt, 3D-gedruckte Teile zu produzieren, darunter einen 5-in-1-Krümmer. Die Herausforderung für AddUp bestand darin, ein Design und einen 3D-Druck des gesamten Systems zu erstellen. Lesen Sie die Fallstudie darüber, wie die DED- Technologie den Druck von Teilen mit komplexen Formen ohne zusätzliche Werkzeuge ermöglicht.
INDUSTRY
Motorsport – Automotive
CHALLENGE
To 3D print an innovative 5-in-1 manifold to optimize engine performance
KEY BENEFITS
- Complex geometry
- Printed part in one go
- Resistance to high temperatures
Printed In One Go
Creative Shape
Performance
Geschichte
Der griechische Hersteller Spyros Panopoulos Automotive arbeitet an der Entwicklung des ersten Ultracars der Welt mit dem Namen Chaos, das in nur 1,55 s von 0 auf 100 km/h beschleunigen kann. Diese reine Leistung ist besser als die Formel 1. Um diese Grenzen zu überschreiten, muss dieses außergewöhnliche Auto deutlich leichter werden, ohne seine hohe mechanische Integrität zu verlieren. Um dieses Ziel zu erreichen, hat Spyros AddUp gebeten, 3D-gedruckte Teile herzustellen, einschließlich eines 5-in-1- Krümmers.
Je fortschrittlicher der Motor ist, desto wichtiger ist der Einfluss der Auspuffanlage auf die Gesamtleistung des Motors. Die Auspuffanlage besteht aus einer Reihe von Metallrohren, die die Abgase vom Zylinderkopf nach außen führen. Der Auspuffkrümmer bezieht sich auf den Bereich, in dem die Primärrohre (vom Zylinderkopf zum Krümmer) zu einem einzigen Rohr, dem Auspuff, zusammenlaufen. Um den Wirkungsgrad des Motors zu verbessern, muss die Auspuffanlage in Bezug auf den Gasfluss und die Akustik – die Bewegung der Schallwellen innerhalb der Auspuffanlage – optimiert werden.
Herausforderungen
Die Herausforderung besteht darin, sowohl die Leistung der Primärkrümmer als auch die des Sammlers zu verbessern. Wir müssen nicht nur die verschiedenen Gasströme in den Auspuff strömen lassen, um die Druckverluste zu begrenzen, sondern auch die Längen und Biegeradien der einzelnen Primärkrümmer anpassen. Diese Konstruktionsänderungen werden es dem Motor ermöglichen, viel effizienter zu entleeren und zu füllen, um das Drehmoment zu erhöhen, insbesondere bei hohen Drehzahlen. Die Herausforderung für AddUp wird darin bestehen, das Design zu erstellen und das gesamte System (Primärkrümmer und Sammler) in 3D zu drucken.
Lösung
Nach der herkömmlichen Methode werden diese Kollektoren in der Regel im Kesselbau hergestellt (gebogene Rohre, geschweißte Rohre…), der auf die Verwendung von Rohren mit konstanter Dicke und einfachen Querschnitten beschränkt ist.
Ein weiterer Nachteil ist, dass diese Methoden auch Werkzeuge erfordern. Die Schweißnähte und andere Baugruppen können an den eingeführten Schwachstellen versagen, da sie hohen thermomechanischen Belastungen ausgesetzt sind. Bei der additiven Fertigung wird das gesamte System in einem Arbeitsgang gedruckt, so dass das Risiko eines Ausfalls während des Betriebs geringer ist.
Da das Teil sehr groß war (380 mm x 240 mm), entschieden sich die AddUp-Experten dafür, es auf einer Modulo 400-Maschine mit der DED-Technologie (Directed Energy Deposition) herzustellen. DED ist ein additives Verfahren, bei dem ein metallisches Ausgangsmaterial (Pulver oder Draht) mit einer Energiequelle, häufig einem Laser, auf ein Substrat oder ein bestehendes Teil aufgeschmolzen wird. Bei der Modulo 400 ersetzt eine Düse die Spindel einer 5-Achsen-CNC- Fräse, wobei das Metallpulver und die Drähte auf das Substrat aufgebracht werden.
Der Laserstrahl wird durch verschiedene Kanäle auf der Düse gelenkt, um das Substrat oder das vorhandene Teil zu treffen und Material hinzuzufügen.
Die DED-Technologie ermöglicht das Drucken von Teilen mit komplexen Formen wie wechselndem Querschnitt und variabler Wandstärke, ohne dass zusätzliche Werkzeuge benötigt werden. Diese Merkmale lassen sich außerhalb der additiven Fertigung nur schwer, wenn überhaupt, nachbilden.
Ergebnisse
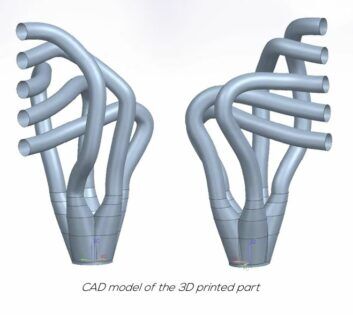
Als Metall für die Krümmer wurde Inconel® 718 gewählt, eine Superlegierung mit guter Oxidationsbeständigkeit und hohen mechanischen Eigenschaften auch über 800
°C. Um maximale Leistung zu erzielen, müssen die Motoren bei hohen Temperaturen und unter hohen Belastungen arbeiten. Die Eigenschaften von Inconel 718 ermöglichen es den Ingenieuren, ein Bauteil zu entwickeln, das diese Hindernisse überwindet und gleichzeitig eine Geometrie mit Blick auf hohe Leistung realisiert.
Bei der Wahl des DED geht es um eine doppelte Frage: Größe und Kosten. Das Modulo 400 ist mit einer kleinen 10-Vx-Düse ausgestattet, mit der wir eine gute Oberflächenqualität für alle Merkmale des großen Teils erzielen konnten. Das fertige Teil hat nach 15 Stunden Produktionszeit eine Wandstärke von 1 mm und einen konstanten Querschnitt, aber eine variable Geometrie entlang eines Rohrs mit kleinen Krümmungsradien. Ein solches Ergebnis ist mit einem herkömmlichen Verfahren nicht zu erzielen.