Erfahren Sie, wie Sie die Kühlung der Einsätze in einer Form mit Hilfe der Additivtechnologie verbessern und gleichzeitig die Leistung der Form erhöhen und die Zykluszeit verkürzen können.
Kurze Einspritzzeiten sind im Formenbau entscheidend für die Rentabilität, insbesondere bei Spritzgießwerkzeugen. Die Zahoransky AG, ein deutscher Hersteller von Spritzgießwerkzeugen, benötigte einen Formeinsatz mit acht Bohrungen mit Formringen. Lesen Sie die Fallstudie über ein gemeinsames Projekt von Zahoransky und AddUp, wie man die Kühlung der Einsätze auf einer Form mit Hilfe der additiven Technologie verbessern und gleichzeitig die Leistung der Form erhöhen und die Zykluszeit verringern kann.
INDUSTRY
Tooling
CHALLENGE
To improve the cooling of the inserts on a mold using AM technology while increasing the performance of the mold and decreasing the cycle time.
KEY BENEFITS
- Ready to use mold after heat treatment
- Near contour cooling in the insert
- Reduction of time & cost production
Creative Shape
Function Integration
Lead Time
Performance
Geschichte
In der Formenbauindustrie und insbesondere bei Spritzgießwerkzeugen sind kurze Einspritzzeiten entscheidend für die Rentabilität. Sie entscheiden, wie viele Spritzgießmaschinen und Formen Sie benötigen und wie hoch der Endpreis des Teils ist. sein wird. Das Kühlsystem im Konturenkerneinsatz hat den größten Einfluss auf diese Zeiten. Die Kühlkanäle werden heute oft noch konventionell durch Bohren in 2D hergestellt und können nicht immer nahe an der Kontur verlaufen und somit gleichmäßig und schnell abkühlen.
Die Zahoransky AG mit Sitz in Todtnau-Geschwend, Baden-Württemberg/Deutschland, ist ein Hersteller von Spritzgießwerkzeugen, Blisterverpackungsmaschinen und Produktionsanlagen. Zahoransky ist Weltmarktführer im Formen- und Werkzeugbau für die Zahnbürstenindustrie. Rund 80 Prozent der weltweit produzierten Zahnbürstenformen stammen von Zahoransky.
Herausforderungen
Zahoransky benötigte einen Formeinsatz mit acht Bohrungen mit Formringen. Bislang mussten diese gut gekühlt und aufwändig mit O-Ringen abgedichtet werden. Die Herausforderung bestand darin, die Kühlung der Einsätze mit Hilfe der additiven Fertigungstechnologie so zu verbessern, dass die Zykluszeiten und die Produktivität der Werkzeuge deutlich erhöht werden. Die aufwändige Montage der O-Ringe sollte entfallen und damit die Herstellungskosten gesenkt werden.
Die Qualität der Teile sollte in der gewohnten Form beibehalten werden. Außerdem mussten die Formen aus einem für das Spritzgießen geeigneten Stahlwerkstoff hergestellt werden, der die für diese Produktion erforderliche Korrosions- und Verschleißfestigkeit aufweist.
Lösung
AddUp optimierte die Kühlkanäle und gestaltete sie so nah wie möglich an den Originalkonturen mit Hilfe der AM 3D-Optionen, einschließlich der einzigartigen Fähigkeiten des AddUp Manager für adaptive Strategien. Alle Kanäle mussten die gleiche Länge und Kühlleistung haben, um eine gleichmäßige Kühlung zu gewährleisten. AddUp setzte Simulationssoftware und thermische Designoptimierung ein, um eine genaue und gleichmäßige Kühlung für diese Form sicherzustellen.
Als nächstes wurde die neue Form auf AddUps PBF-Maschine (Laser Powder Bed Fusion), der FormUp ® 350 New Generation, mit einer produktiven AM- Aufbaustrategie mit vier Lasern gedruckt. Diese Form wurde in nur 30 Stunden gedruckt.
Ergebnisse
AddUp hat die Produktionszeit für diese Form im Vergleich zur herkömmlichen Herstellungszeit erheblich reduziert. Auch die Nachbearbeitung dieser Form wurde dank der Rollentechnologie des AddUp FormUp 350 erheblich reduziert.
AddUps einzigartige Kombination aus feinem Pulver und einem Walzenbeschichter sorgt für ein hervorragendes Oberflächenfinish und reduziert die für die Nachbearbeitung benötigte Zeit erheblich. Die Form wurde aus dem Stahlwerkstoff 1.2709/Margin300 gedruckt. Dieser Werkstoff ist ein qualifizierter Werkzeugstahl, der eine gute Standzeit in der Form bietet.
Zahoransky war sowohl mit der Qualität der Form als auch mit der Produktionszeit zufrieden.
Der nächste Schritt in diesem Projekt ist die Herstellung eines weiteren Prototyps mit zusätzlichen Optimierungen und aus einem neu entwickelten Werkzeugstahl 1.2083/PM420. Dieser neue Werkstoff ist ein qualifizierter Stahl für Spritzgusswerkzeuge, der weit verbreitet ist und eine gute Korrosions- und Verschleißbeständigkeit aufweist.
Für weitere Informationen zur additiven Fertigungstechnologie für die Werkzeug- und Formenbauindustrie stehen wir Ihnen gerne zur Verfügung.
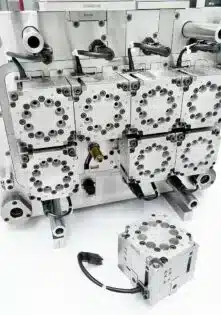
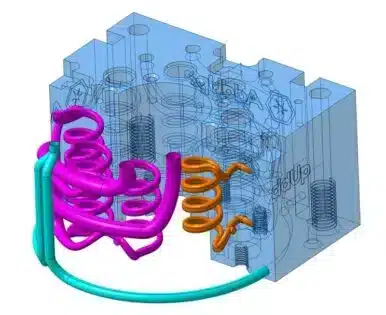