AddUp a développé avec ses partenaires un échangeur thermique à double courbure performant, imprimé en une seule fois.

Pour les équipements thermiques, la fabrication additive présente un énorme avantage. Il permet le développement de formes de canaux complexes et améliore ainsi les performances thermiques et réduit le volume. Il permet également de fabriquer des formes impossibles à réaliser traditionnellement pour ce type d’équipement (ex : caniveaux à double courbure). Téléchargez cette étude de cas du projet HEWAM, un échangeur de chaleur aux géométries complexes développé par PrintSky (Joint-Venture AddUp SOGECLAIR) et Temisth.
INDUSTRIE
Aéronautique
CHALLENGE
Imprimer en 3D un échangeur thermique innovant
KEY BENEFITS
- Concept d’échangeur de chaleur modulaire
- Un échangeur de chaleur à double courbure
- Pièce imprimée en une seule fois avec des parois fines
- En cas de dommage, remplacement de l’unité au lieu de l’ensemble de l’installation
FORMES COMPLEXES
ASSEMBLAGE
PERFORMANCE
PAROIS FINES
HISTOIRE
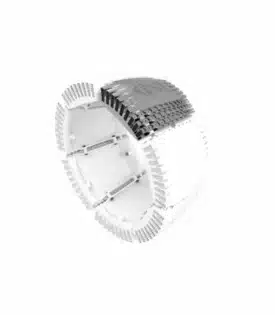
Un échangeur thermique est un système utilisé pour transférer la chaleur entre une source et un fluide. Les échangeurs thermiques sont utilisés dans les procédés de refroidissement et de chauffage. Selon l’application, les fluides peuvent être séparés pour éviter qu’ils ne se mélangent ou ils peuvent également être en contact direct. Dans l’industrie aéronautique, les échangeurs thermiques des avions ont pour fonction de prélever la chaleur du circuit d’huile des moteurs afin de chauffer le carburant froid. Cela permet d’améliorer l’efficacité du carburant et de réduire le risque d’avoir de l’eau dans celui-ci, ce qui pourrait provoquer la création de gel.
Heat Exchanger With Additive Manufacturing ou HEWAM est un projet visant à développer un échangeur thermique en faisant appel au potentiel de la fabrication additive, avec une géométrie qui s’adapte à une large gamme de surfaces et de volumes utilisés dans l’industrie aérospatiale. Ce projet a été développé par PrintSky et Temisth. PrintSky est une joint-venture entre le groupe AddUp, expert en fabrication additive métallique, et SOGECLAIR, un des leaders internationaux dans l’intégration de solutions à haute valeur ajoutée dans les domaines de l’aéronautique, de l’espace, du transport civil et militaire. Temisth est une société spécialisée dans le développement de solutions thermiques personnalisées utilisant la fabrication additive.
PrintSky s’est chargé de la partie conception du projet, en développant sa propre méthodologie pour déterminer les caractéristiques de la pièce métallique, en termes de mécanique, de thermique et de fabricabilité. La production a ensuite été confiée aux experts d’AddUp qui ont imprimé en 3D cette pièce aéronautique sur leur machine FormUp® 350. L’objectif était de produire un échangeur thermique compact selon le procédé PBF (Laser Powder Bed Fusion) avec une forme innovante et surtout aussi efficace que les échangeurs de chaleur fabriqués traditionnellement. Après la production, HEWAM a été testé sur un banc d’essai développé par Temisth.
DÉFI TECHNOLOGIQUE
L’objectif pour HEWAM était de refroidir de l’huile entrant dans l’échangeur à 110°C avec de l’air ambiant à -50°C. Le débit massique de l’huile est fixe. Le débit massique de l’air est donné par la pression dynamique du flux d’air qui arrive dans la zone de l’échangeur et les caractéristiques de perte de charge du dispositif. 2200W de l’huile. (32g/s ~2,4 L/min) à éliminer sur un module de l’échangeur, tout en assurant un débit d’air suffisant à travers celui-ci. Le principal problème physique sur cette nouvelle pièce était d’assurer un flux d’air suffisant à l’intérieur avec un coefficient de transfert de chaleur élevé.
LA SOLUTION
Les partenaires ont développé une méthodologie spécifique afin d’assurer les exigences thermiques avec les contraintes mécaniques et la faisabilité de la fabrication additive pour HEWAM. Un design spécifique a été créé en tenant compte de la variation de la température de l’air (de -50°C à +25°C) et donc de sa densité. La largeur du canal a été augmentée pour limiter l’accélération de l’air et la chute de pression. Dans le but de maintenir les performances thermiques, les ailettes ont une géométrie adaptative le long du flux d’air afin de prendre en compte la vitesse de l’air et les changements de taille des canaux. La pièce a été conçue pour s’adapter à une large gamme de surfaces et de volumes utilisés dans l’industrie aérospatiale. La forme courbe de la pièce est adaptée à une installation dans les mâts réacteurs des avions.
HEWAM a été imprimé deux fois, avec deux matériaux différents. Tout d’abord, l’Inconel 718. Ce matériau est 3 fois plus lourd que l’aluminium et est moins conducteur, mais pour la fabrication additive, il présente des caractéristiques plus intéressantes. Avec l’Inconel, il est possible de réaliser des parois fines (<0,5mm) et des ailettes (0,15mm) sans avoir de fuite. Ainsi on se rapproche des performances et de la légèreté de l’aluminium. La conception de l’échangeur de chaleur avec ces caractéristiques fines permet d’obtenir des performances et des caractéristiques de poids similaires à celles de l’aluminium. Un dernier avantage de cette pièce imprimée en 3D est la possibilité de mettre à jour l’échangeur sans avoir à développer un nouvel outillage.
LES RESULTATS
Le résultat final est un échangeur thermique à double courbure performant, imprimé en une seule fois. Une solution modulaire : les échangeurs peuvent être disposés les uns à côté des autres afin de délivrer une grande puissance thermique. La forme incurvée est adaptée pour l’installation dans les pylônes des moteurs d’avions. Les tests ont permis de valider l’étanchéité de la pièce ainsi que ses performances, toutes deux très satisfaisantes, notamment par rapport aux moyens de fabrication plus conventionnels.
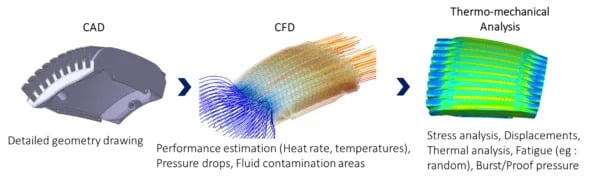
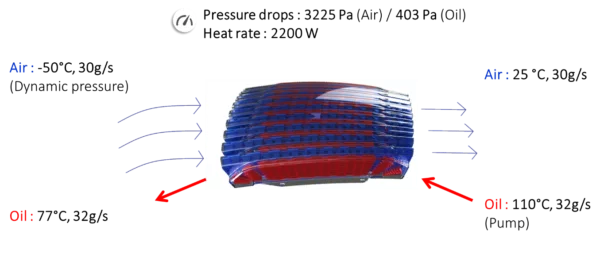
Pour les équipements thermiques, l’impression 3D métallique présente un avantage considérable. Il permet de développer des formes de canaux complexes, ce qui améliore les performances thermiques et réduit le volume. La fabrication additive offre également la possibilité de fabriquer des formes impossibles à produire de manière traditionnelle pour ce type d’équipement (par exemple, des canaux à double courbure).
En outre, la technologie additive permet également la fabrication d’une pièce en une seule fois. Cela évite toute autre manipulation de la pièce qui pourrait l’altérer, comme l’assemblage ou l’usinage. Pas de soudure non plus, ce qui signifie aucun risque de fuite de liquide dans ce nouvel échangeur. Enfin, seules les zones fonctionnelles de la pièce métallique sont imprimées (surfaces d’écoulement des fluides et surfaces de fixation), ce qui permet de réaliser d’importantes économies de matériaux.