Industrie
Impression 3D métal
CHALLENGE
Réduire les coûts de production, les délais d’exécution et optimiser la dissipation thermique d’un échangeur thermique.
à
KEY BENEFITS
- Réduction de la taille de 64%
- Poids de la pièce divisé par 6
- Installation simplifiée
- Réduction des coûts et du temps de production
- Fiabilité accrue grâce à la conception monobloc
Réduction de la masse
Formes complexes
Canaux internes
Performance
HISTORIQUE
Le projet de réalisation d’un échangeur thermique pour la machine FormUp® 350 est né de la volonté de profiter du savoir-faire développé par PrintSky, une société commune créée par AddUp, fabricant de machines d’impression 3D métallique, et Sogéclair, fournisseur de solutions innovantes pour une mobilité plus sobre et plus sûre. Il s’agissait d’évaluer l’intérêt d’une solution optimisée en fabrication additive en la comparant avec le système actuel, produit par des méthodes conventionnelles.
La pièce choisie pour ce cas d’application est le refroidisseur du flux d’évacuation des fumées de fusion. Dans une machine de fusion laser sur lit de poudre (L-PBF), comme la FormUp 350 d’AddUp, la chambre de fabrication est traversée par un flux de gaz d’inertage chargé d’évacuer les fumées générées lors de la fusion. Ce flux de gaz, qui circule en circuit fermé et à haute vitesse (plusieurs mètres par seconde) nécessite un système de refroidissement efficace.
DEFI TECHNIQUE
Une des principales contraintes du projet était de maintenir un coût de production de l’échangeur inférieur ou équivalent à la solution conventionnelle, tout en optimisant ses performances afin d’améliorer la dissipation thermique, et en adaptant ses dimensions pour simplifier son installation dans les machines.
Pour réaliser ce projet, les ingénieurs d’AddUp sont partis d’une page blanche. Ils ont défini le niveau de performances à atteindre pour concevoir un échangeur thermique qui réponde parfaitement exactement aux besoins de l’application, sans se conformer aux standards du marché. Les canaux internes, les ailettes, ainsi que les interfaces ont été personnalisés pour optimiser la compacité de la pièce tout en assurant une amélioration des performances. Les concepteurs se sont appuyés sur les compétences clés développées par PrintSky afin d’optimiser la géométrie, l’encombrement, mais aussi les temps de fabrication (en utilisant des recettes à haute productivité). Les canaux internes, les ailettes, ainsi que les interfaces ont été personnalisés pour optimiser la compacité de la pièce tout en assurant une amélioration des performances. Tout cela en intégrant le retour d’expérience d’AddUp dans le domaine de la fabrication d’échangeurs.
SOLUTIONS
Les experts d’AddUp et de Printsky ont choisi d’optimiser la géométrie de l’échangeur, son encombrement, mais également les temps de fabrication. Pour cela, ils ont employé des recettes à haute productivité, et ont également intégré dans chacun des choix de conception le retour d’expérience d’AddUp dans le domaine des échangeurs. C’est ainsi que les formes des ailettes de refroidissement ont été conçues pour faciliter le retrait de la poudre non fusionnée, par exemple.
Cet échangeur innovant ainsi que ses connecteurs ont été dessinés sous CATIA, et le refroidissement a été simulé avec des logiciels édités par Altair. L’ensemble a été pensé pour être imprimé en une seule pièce, réduisant ainsi les temps d’assemblage par rapport aux échangeurs traditionnels réalisés par mécano-soudage.
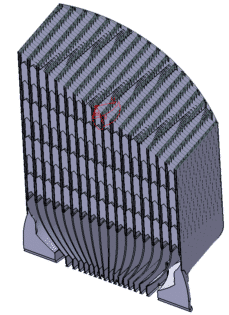
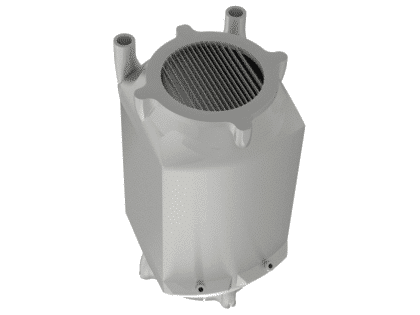
RESULTATS
Ce nouvel échangeur optimisé en termes de dissipation thermique et de réduction des pertes de charge, grâce aux outils et compétences internes Printsky, présente un gain de volume de 64 %, par rapport au système précédent, avec une masse divisée par six. Le choix de l’aluminium a permis d’aboutir à une solution compacte mais efficace, adaptée à toutes les contraintes imposées par l’environnement de la machine FormUp 350, avec un prix équivalent à une solution conventionnelle.
Aujourd’hui le refroidisseur est en fin d’industrialisation et passera en essais afin d’évaluer ses performances réelles sur la machine de fabrication additive. Une dernière phase d’optimisation est prévue pour ajuster les géométries et les choix de fabrication sur la base de ces essais.
Conçu en aluminium, un matériau à la fois léger et bon conducteur thermique, l’échangeur est compact et permet de refroidir efficacement les gaz chauds circulant dans la FormUp 350.
Les gains observés par rapport au système précédent sont :
– Une réduction de 64 % de l’encombrement.
– Une masse divisée par 6.
– Un prix équivalent comparé à une fabrication avec des process conventionnels
– Une fiabilité accrue grâce à une conception monobloc.