This case study presents the development of an optimized heat exchanger for the Form Up® 350 machine. The goal was to improve heat dissipation and adapt the dimensions for easy installation.
INDUSTRY
Aerospace
CHALLENGE
To reduce production costs and lower lead time while optimizing neat dissipation for a neat exchanger.
KEY BENEFITS
- 64% reduction in size
- Weight of the part divided by 6
- Simplified installation
- Reduced production costs and time
- Enhanced reliability with monobloc design
CREATIVE SHAPE
INTERNAL CHANNEL
MASS REDUCTION
PERFORMANCE
History
The project to produce a heat exchanger for the FormUp® 350 machine arose from the desire to take advantage of the know-how developed by PrintSky, a joint venture created by AddUp, a manufacturer of metal 3D printing machines, and Sogéclair, a supplier of innovative solutions for cleaner, safer mobility. The aim was to assess the benefits of an optimized additive manufacturing solution by comparing it with the current system, produced by conventional methods.
The part chosen for this application is the cooler for the fusion fume exhaust stream. In an L-PBF machine, such as AddUp’s FormUp 350, an inert gas flow passes through the manufacturing chamber, evacuating the fumes generated during melting. This gas flow, which circulates in a closed circuit at high speed (several meters per second), requires an efficient cooling system.
Challenges
One of the main constraints of the project was to keep the production cost of the exchanger lower than or equivalent to the conventional solution while optimizing its performance to improve heat dissipation and adapting its dimensions to simplify installation in machines.
For this innovative project, the AddUp’s engineers started from scratch. They defined the level of performance to be achieved to design a heat exchanger that perfectly met the needs of the application, without conforming to market standards. The internal channels, fins and interfaces have been customized to optimize the compactness and the part performance.
Designers drew on PrintSky’s core competencies to optimize geometry, footprint, and production times (using high-productivity recipes). Internal channels, fins, and interfaces were customized to optimize part compactness while ensuring enhanced performance. All this was achieved by inte-grating AddUp’s experience in heat exchanger manufacturing.
Solution
AddUp and Printsky’s designers chose to optimize the exchanger’s geometry and footprint, as well as manufacturing times. To achieve this, they used high-productivity recipes and incorporated AddUp’s experience in the field of heat exchangers into each of their design choices. The shapes of the cooling fins, for example, were designed to facilitate the removal of unfused powder. This innovative exchanger and its connectors were designed in CATIA, and cooling was simulated using Altair software. The whole unit was designed to be printed in a single piece, thus reducing the assembly times compared with traditional mechanically welded exchangers.
Results
This new heat exchanger, optimized in terms of heat dissipation and pressure loss reduction thanks to Printsky’s in-house tools and expertise, offers a 64% gain in volume over the previous system, with its mass divided by six. The choice of aluminum has resulted in a compact yet efficient solution, adapted to all the constraints imposed by the FormUp 350 machine environment, at a price equivalent to a conventional solution.
Today, the cooler is in the final stages of industrialization and will be put through its paces in trials to assess its actual performance on the additive manufacturing machine. A final optimization phase is planned to adjust geometries and manufacturing choices based on these tests.
Designed in aluminum, a material that is both light and a good thermal conductor, the compact exchanger efficiently cools the hot gases from FormUp 350.
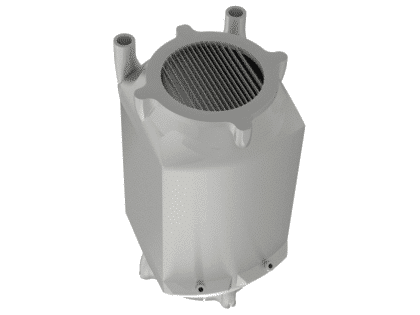
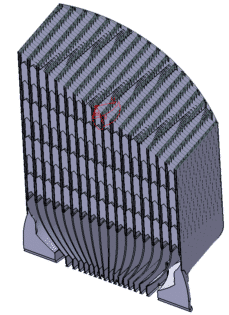
64% smaller footprint.
Mass divided by 6.
Equivalent price.
Enhanced reliability with monobloc design.