This case study presents the development of multi-metal, multi-technology piston head The goal was to improve wear resistance and performance, as well as internal cooling channels.
INDUSTRY
Automotive
CHALLENGE
Utilize two different Additive Manufacturing technologies and materials to create a single part.
NO SUPPORTS
PERFORMANCE
MASS REDUCTION
History
Pistons are traditionally manufactured using casting, where molten metal is poured into a mold and allowed to solidify. The piston will then go through machining operations such as milling, boring, and honing to achieve the precise dimensions and surface finish required for its use in an engine.
Challenges
Traditional piston manufacturing faces several challenges, including material selection, precision machining, waste generation, and energy consumption. Selecting the right material for durability and heat resistance is crucial. Achieving the needed dimensions through machining can be costly and time-consuming, leading to tool wear and maintenance issues. These processes also generate waste and have environmental impacts, making them less sustainable. Meeting cost and lead time constraints can be a significant challenge for traditional piston manufacturing.
Solution
A potential solution to address the challenges associated with piston manufacturing and performance is to adopt new manufacturing techniques. Additive manufacturing allows for intricate and customized piston designs with internal cooling channels, reduced waste, and improved efficiency. It can also enable the use of different materials and complex geometries not easily achievable through conventional manufacturing methods. AddUp has created a concept part using both Powder Bed Fusion (PBF) and Directed Energy Deposition (DED) to show the value and benefits Additive can bring to the manufacturing industry and using the right tools for the right job.
Results
The piston was printed in two stages. The first stage used Powder Bed Fusion and the FormUp 350 to print the core of the piston. No supports were used during the entire printing process.
Lattice was added into the geometry to provide an overall lighter weight structure. Reducing the mass can lower stress on engine components, putting less stress on other engine components like the connecting rods and crankshaft. Fuel efficiency is also enhanced by reducing the mass the engine needs to move, leading to better mileage. Internal channels were added to increase the performance and improve heat dissipation, lowering the piston’s temperature, expansion, and emissions. These channels are essential for managing heat and ensuring the reliability, durability, and performance of internal combustion engines.
After the core of the piston was complete, the next stage was to deposit wear resistant ring grooves with Directed Energy Deposition. While the full part could have been printed fully in PBF, it would require support material on the rings. Without the use of supports and the need for powder bed recoating, DED was able to reduce both the print and post processing time required by depositing only the amount of material needed for the rings directly onto the base.
DED was able to deposit a second material with the ability to provide enhanced wear resistance and heat dissipation properties in the piston ring grooves. Not only can DED be used to add high performance material, but can also allow for the repair of piston ring grooves in damaged engine blocks by restoring the grooves to their original dimensions.
Watch the video showing the real piston in Powder Bed Fusion and Directed Energy Deposition here:
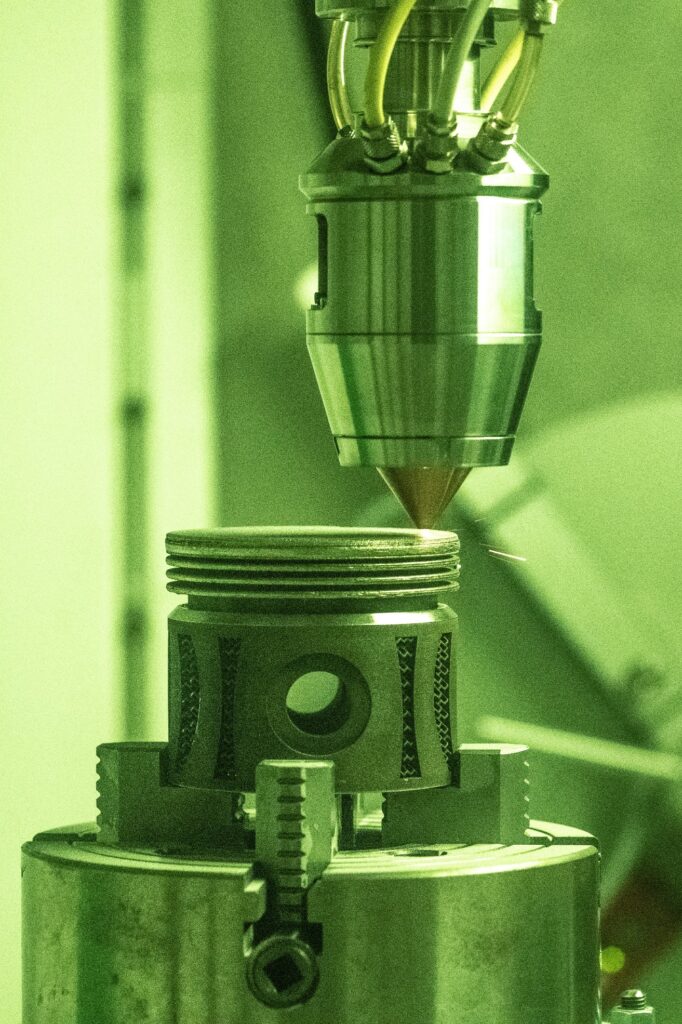
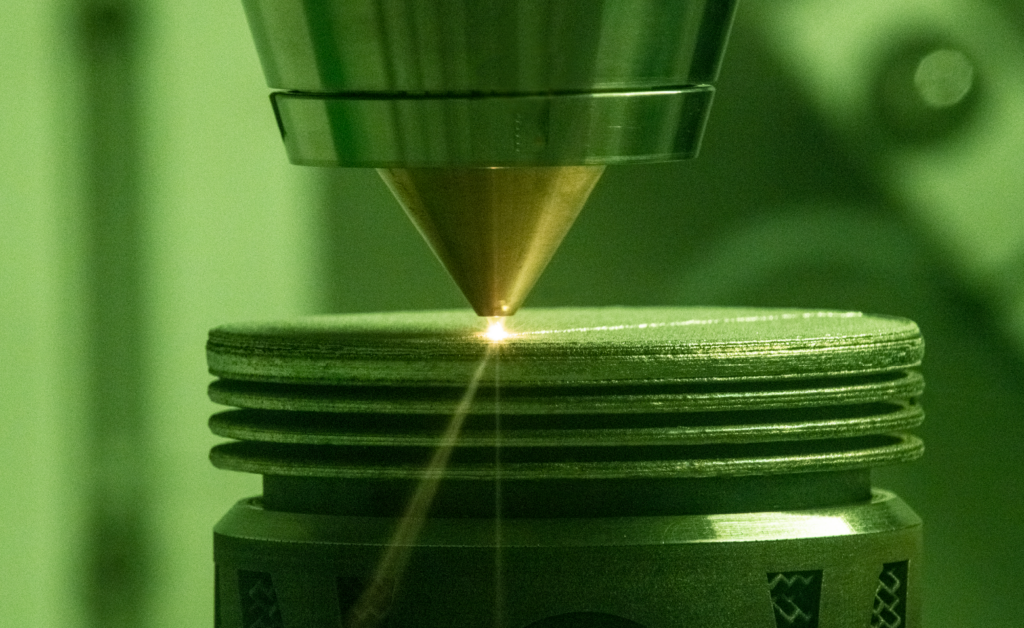
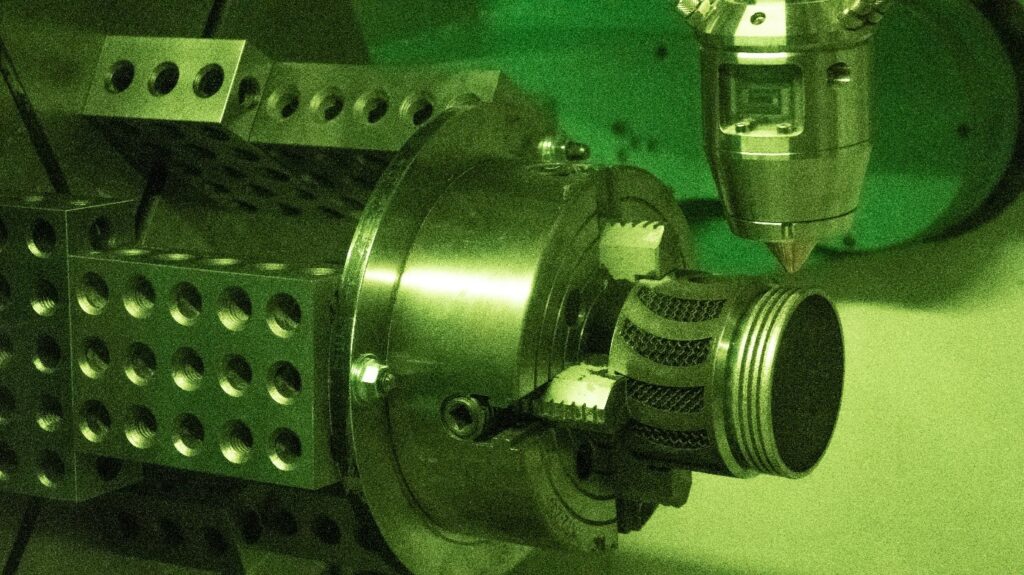
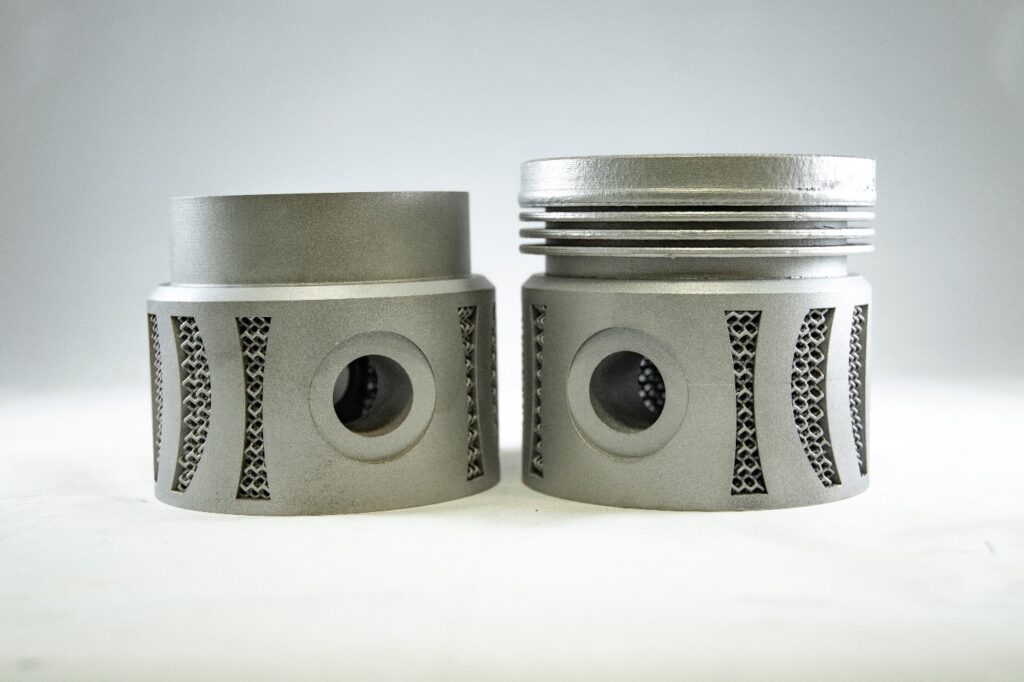
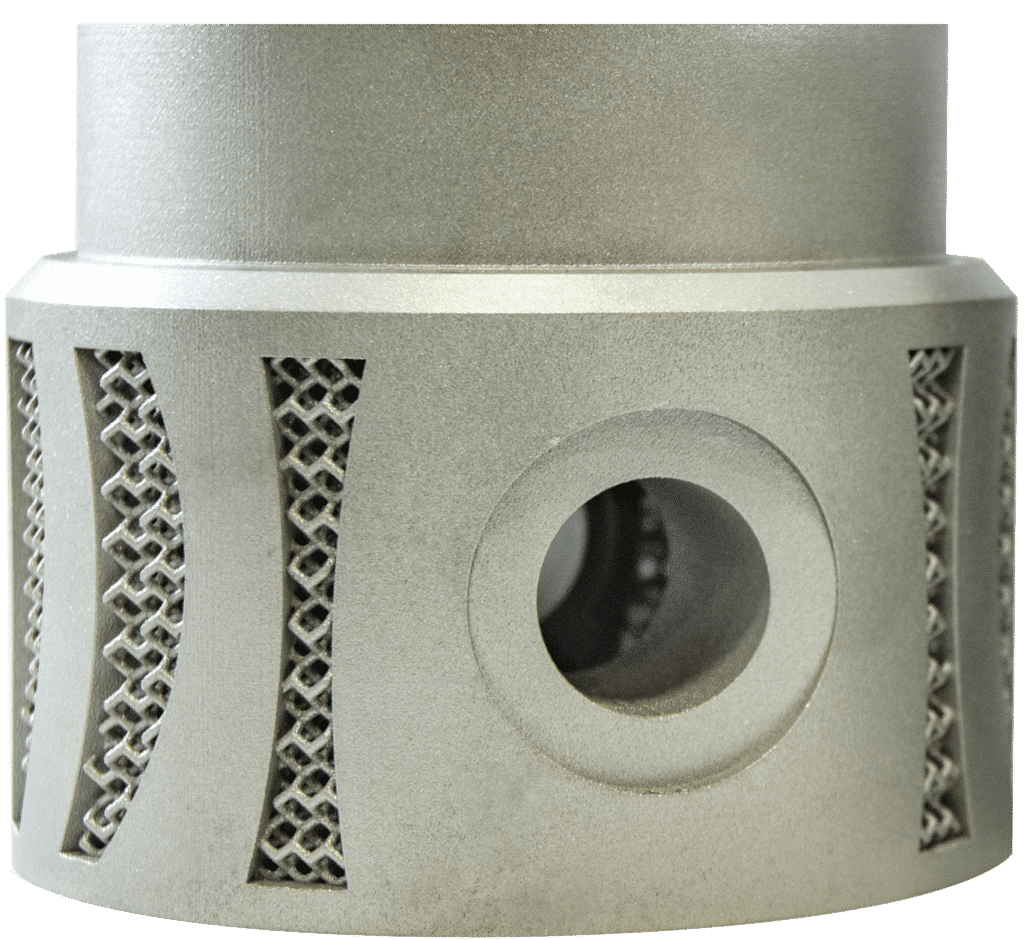
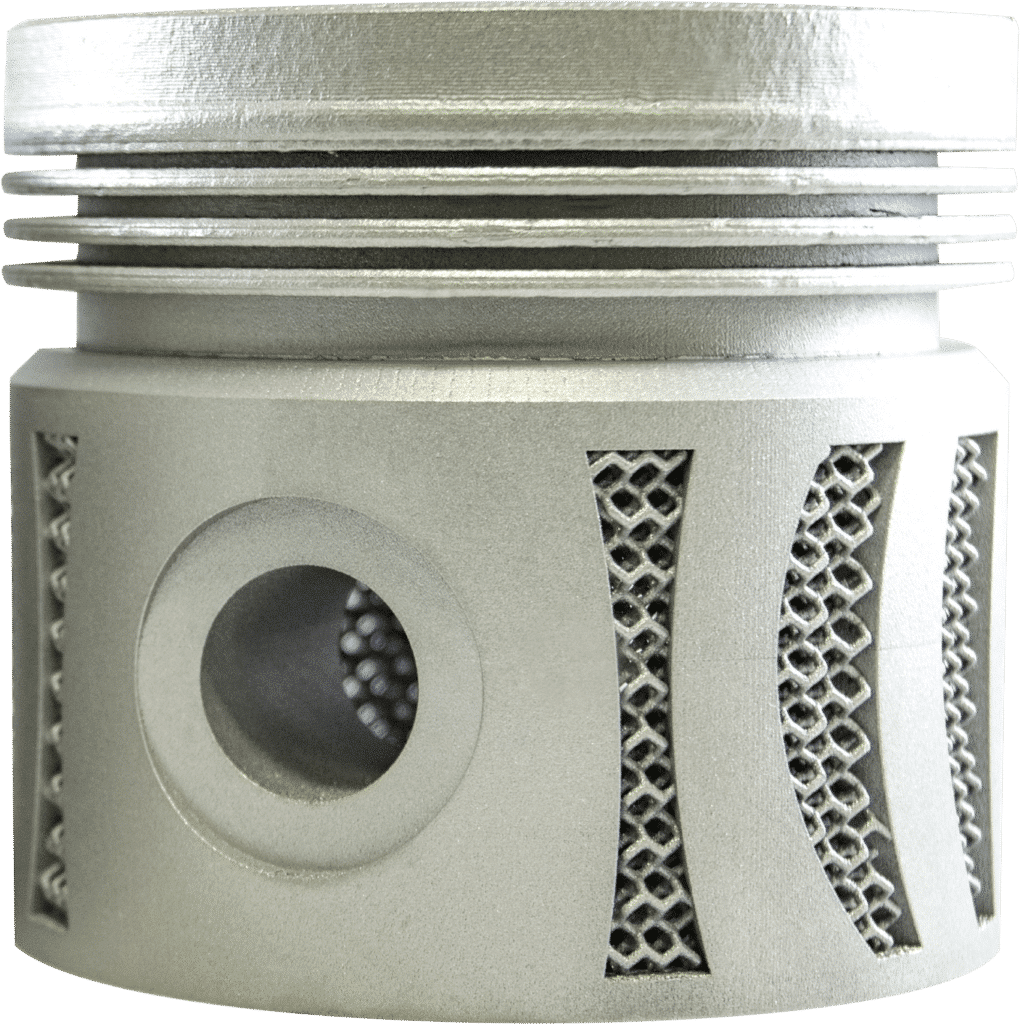
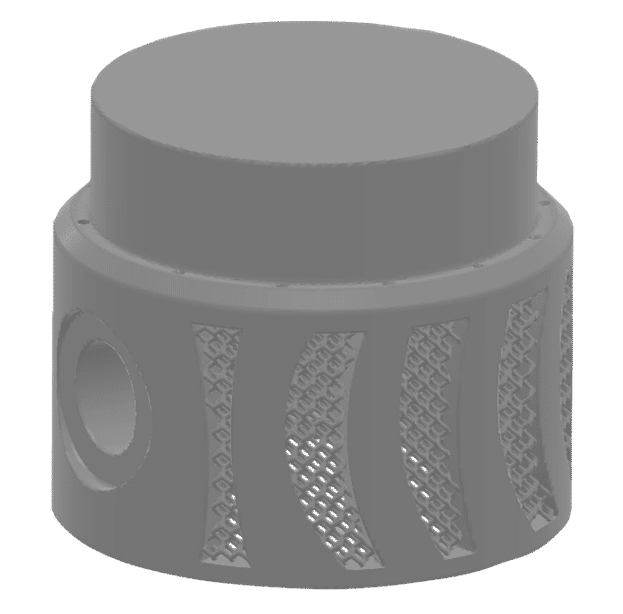
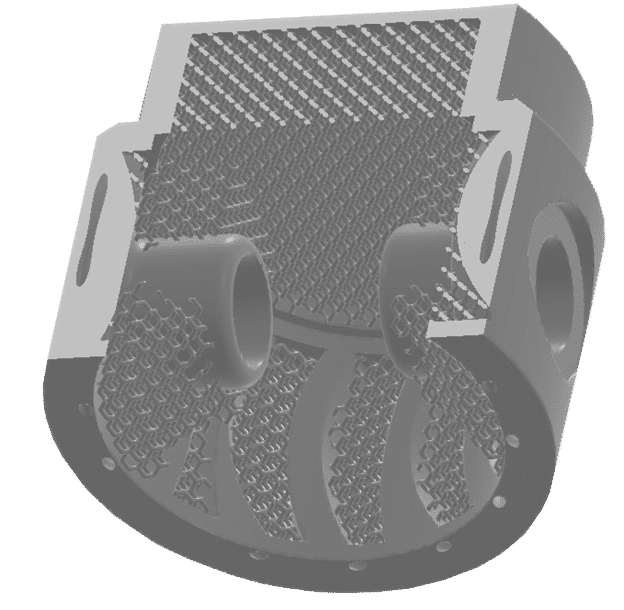
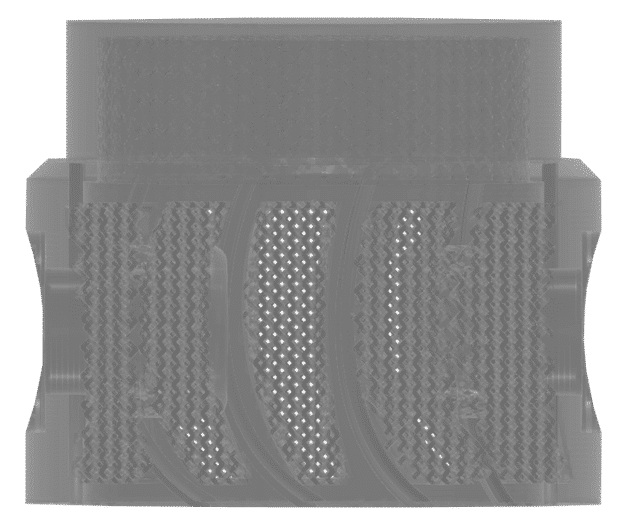
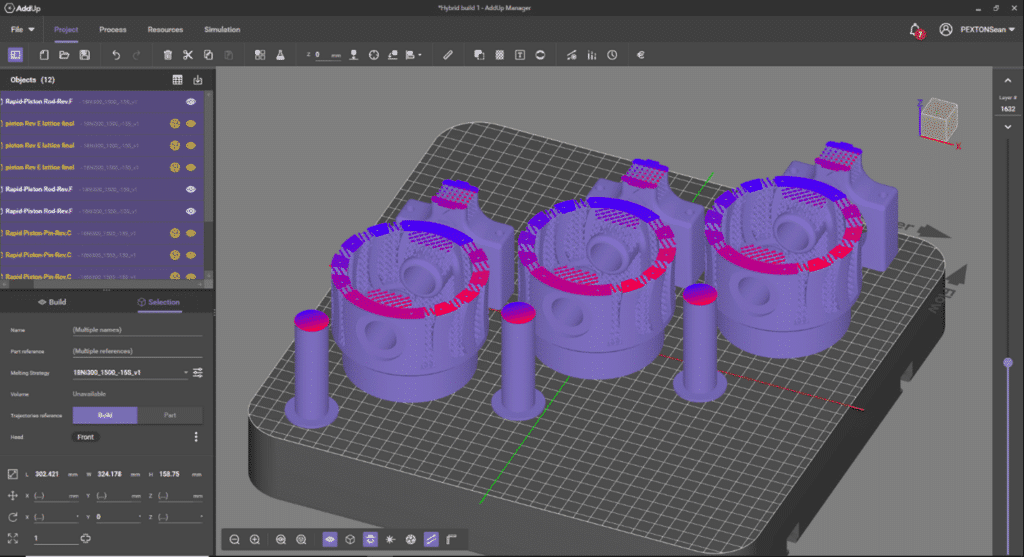
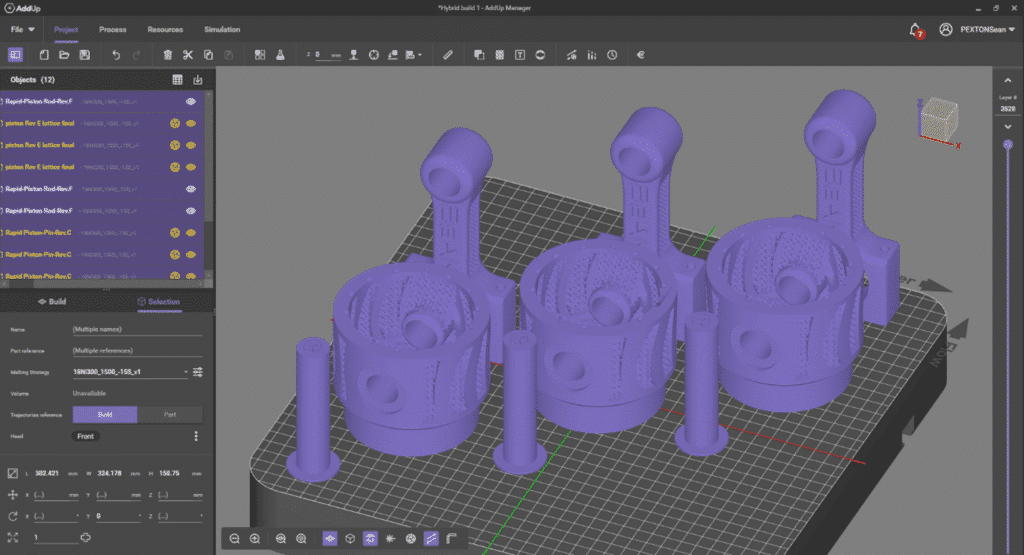
Internal cooling channels
Improved wear resistance and performance
Features added to existing part