Learn how AddUp worked with German toolmaker Gira to modify an existing mold to achieve shorter cycle times and improved heat conduction using additive manufacturing.
INDUSTRY
Tooling & Molding
CHALLENGE
It was difficult to find a potential project at Gira, since most of the sockets and switches are produced with a high-gloss finish, something the AM community hasn’t tackled yet.
We found an intriguing application in a socket variant for surface mounting. Due to the core on the locking side cannot be sufficiently tempered by conventional means. There is no way for machine channels to homogenously cool the part across the height of the mold.
KEY BENEFITS
- Improvement in temperature control
- Reduction of cooling time
- Understanding AM Specific Design Approaches
INCREASED PRODUCTIVITY
REDUCED MANUFACTURING TIME
CONFORMAL COOLING
History
Gira’s toolmaking stands for the innovative production of technically high-quality products and assemblies with industrial precision. A particular strength lies in the great speed and flexibility with which they create solutions for large series, small series, and prototype tools, all cost-effectively. Gira is also capable of creating tools for multi-component molded parts.
The aim of this project was to modify an existing mold to achieve shorter cycle times with the core of the part now being designed to be produced by AM.
With the existing mold, the part can be produced to the required quality specifications, but the conventional cooling of the mold core results in suboptimal heat conduction. Eventhough the cycle time is already in an economic range, Gira noted that further improvement can be made in this area.
There lies the potential to improve heat conduction in the core through an improved cooling channel design, and thus a reduction in the cooling time is made possible through additive manufacturing.
Challenge
The end-use part produced by the mold is a polycarbonate socket, and has a wall thickness of approximately 3mm. The core of the insert has a large contact area with the polycarbonate andthis entire surface must be cooled homogeneously in order to achieve optimized heat conduction compared to the conventional core. In order to achieve largely uniform heat dissipation, it is imperative to design the cooling channels with equal spacing to the respective surfaces and to properly choose the spacing between the channels.
Following these rules leads to highly effective cooling but there are other manufacturing considerations to be taken into account. After the 3D printing process, the part must be thoroughly depowdered, and as the complexity of the circuit of cooling channels increases, so does the complexity of depowdering of these channels. This step in the process chain is critical to both the functionality of the part and the safety of workers exposed to the powder.
Delivering flawless parts and protecting workers is AddUp’s priority.
Solution
The geometric properties of the core were used to inspire the design of the channels. There is an axis of symmetry in the core around which a channel can be mirrored. This feature is more often used to save construction costs, but is also convenient in achieving perfect balancing of the ducts, since they can all be modeled in the same way.
Since this core is built into an existing mold, the cooling inlets and outlets are predetermined. To supply the four channels with coolant, a quadruple parallel circuit is built into the core. In this way, it is possible to connect all the channels to the existing coolant supplies.
In the process of designing the channels, de-powdering must be considered. The alignment of a part on the 3D printing platform is determined by its geometry, the desired tolerances, and the amount of support structure. In the case of this core, the optimal orientation is obvious due to the recess for the plug and the angle for demolding. However, this alignment has the disadvantage of making the part difficult to depowder because the inlets and outlets are located on the plate.
To ensure that the operator does not come into contact with powder, only properly de-powdered parts can be removed from the confined zone. In this zone, the operators are equipped with protective clothing and respirators, PPE that is not required in the rest of the process chain.
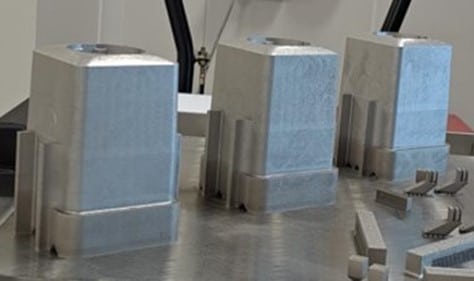
In order to thoroughly de-powder the fourfold parallel cooling system, the component must first be sawed off the build platform. To prevent loose powder from escaping from the component, an orifice plate was installed. That orifice plate wasn’t removed until the component was back in the powder zone, preventing any powder from escaping until ready to thoroughly de-powder the part.
This project is a good example of a very complex component being depowdered without compromising safety, because the safety of the employees must always be the top priority.
Results
An improvement in temperature control are guaranteed by employing intricate complex conformal cooling channels using the design freedom of AM. This project shows that designing molds with AM in mind can lead to ample downstream benefits. Gira will be exploring opportunities in their early development stages knowing they can use AM to increase performance of their molds. Gira and AddUp will continue to work together as they find more and more applications where AM can help their customers.
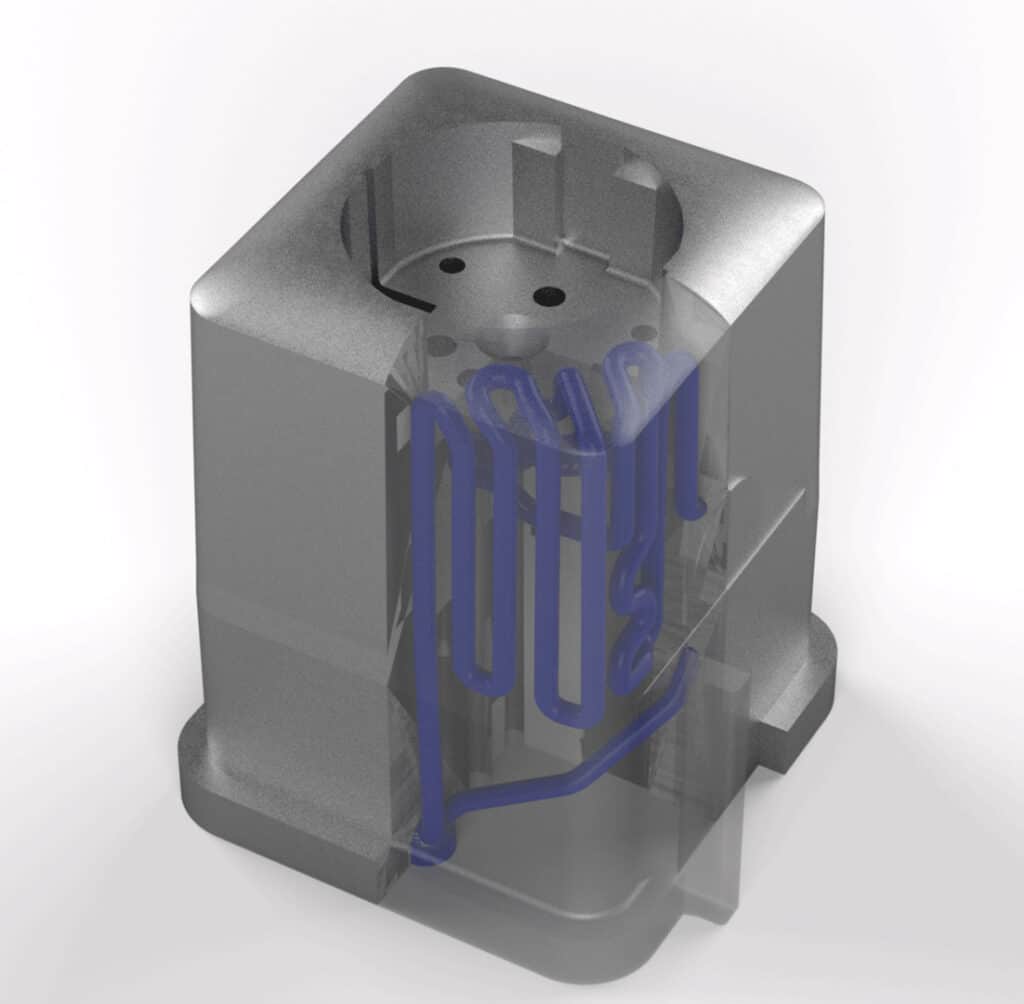
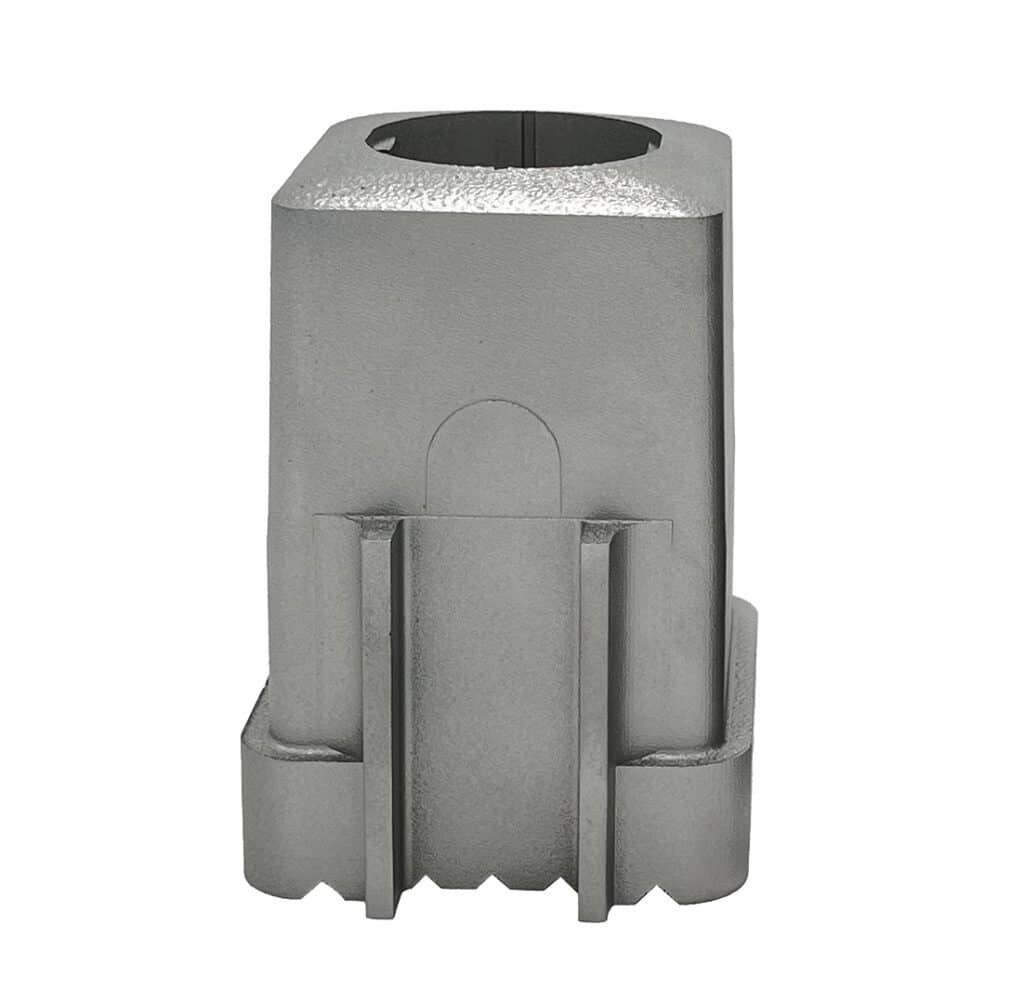
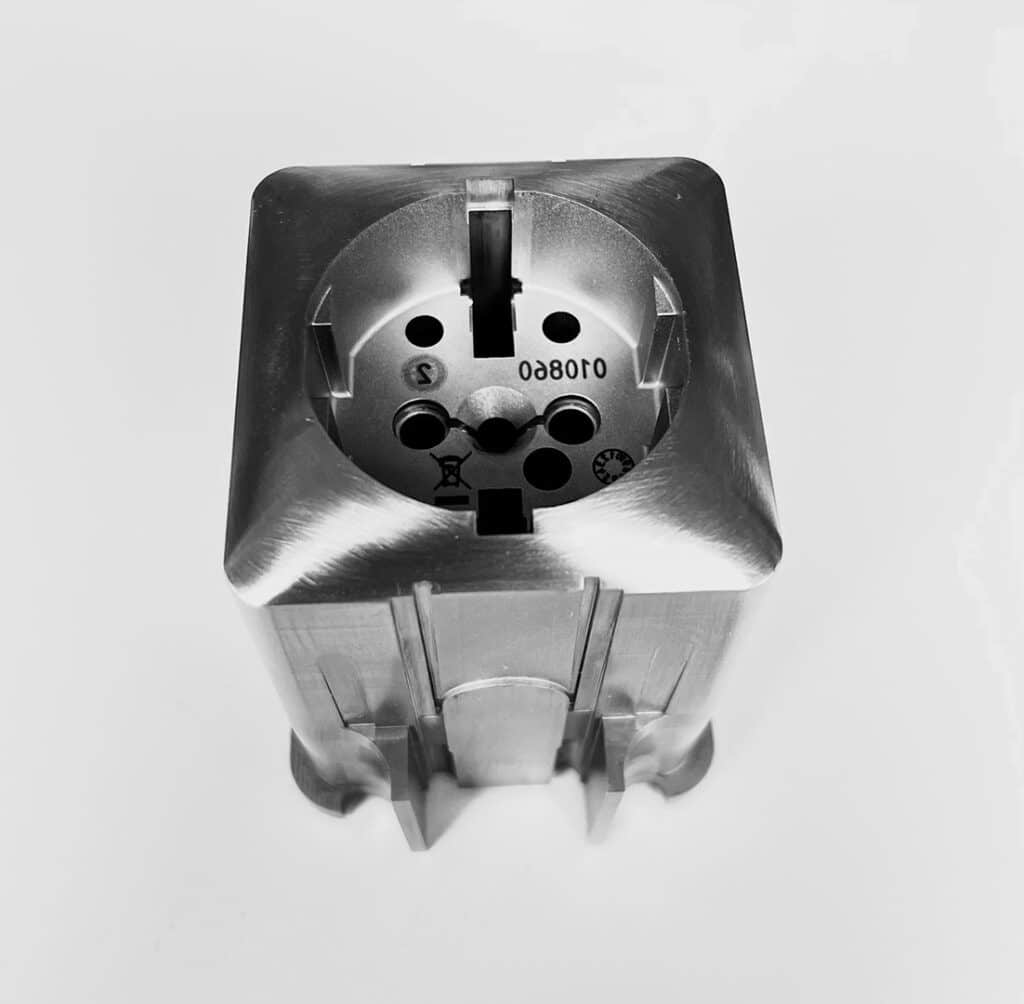
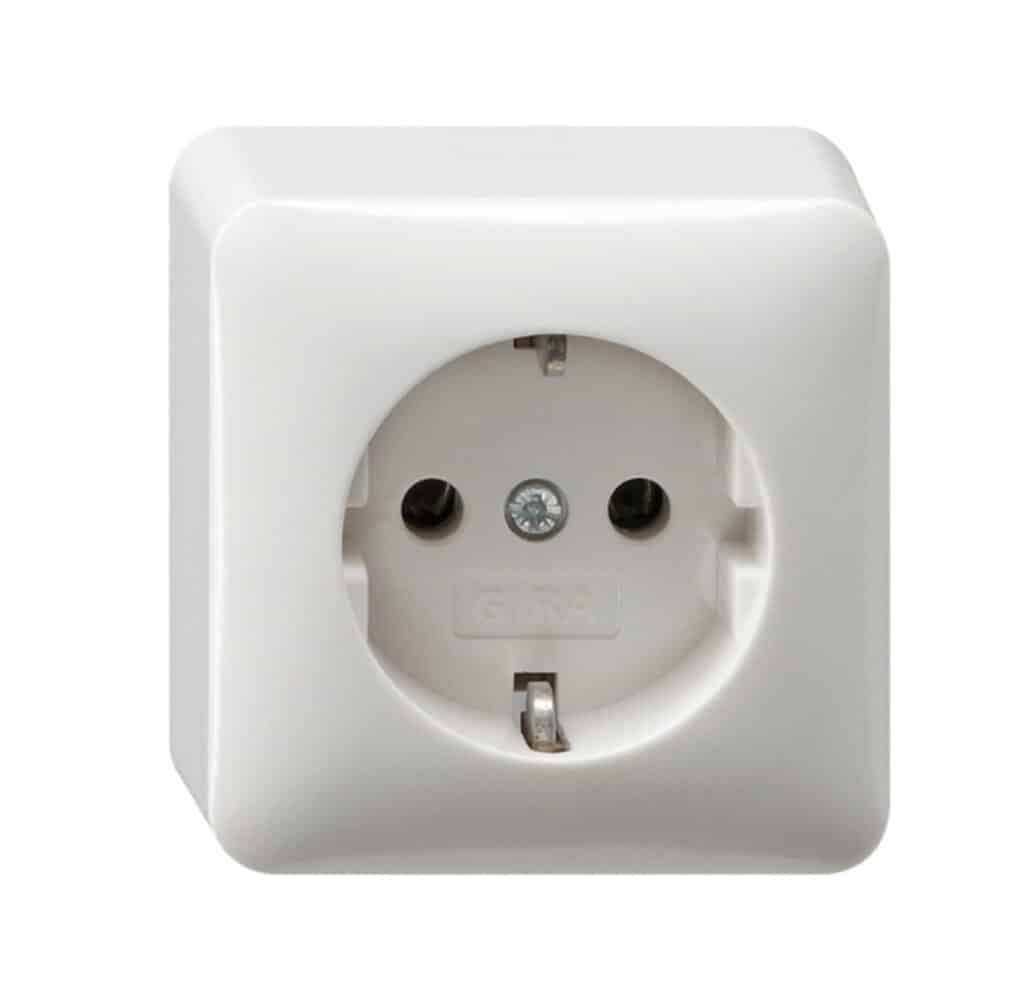
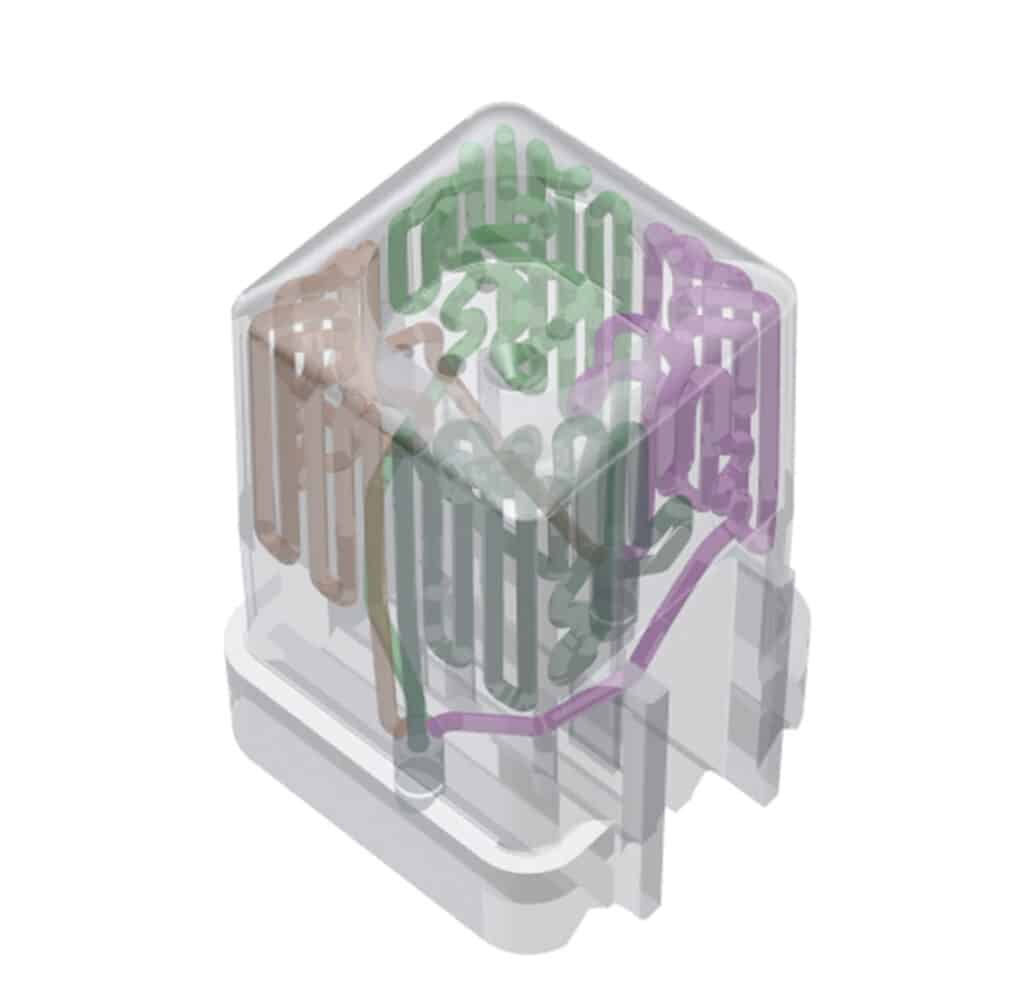
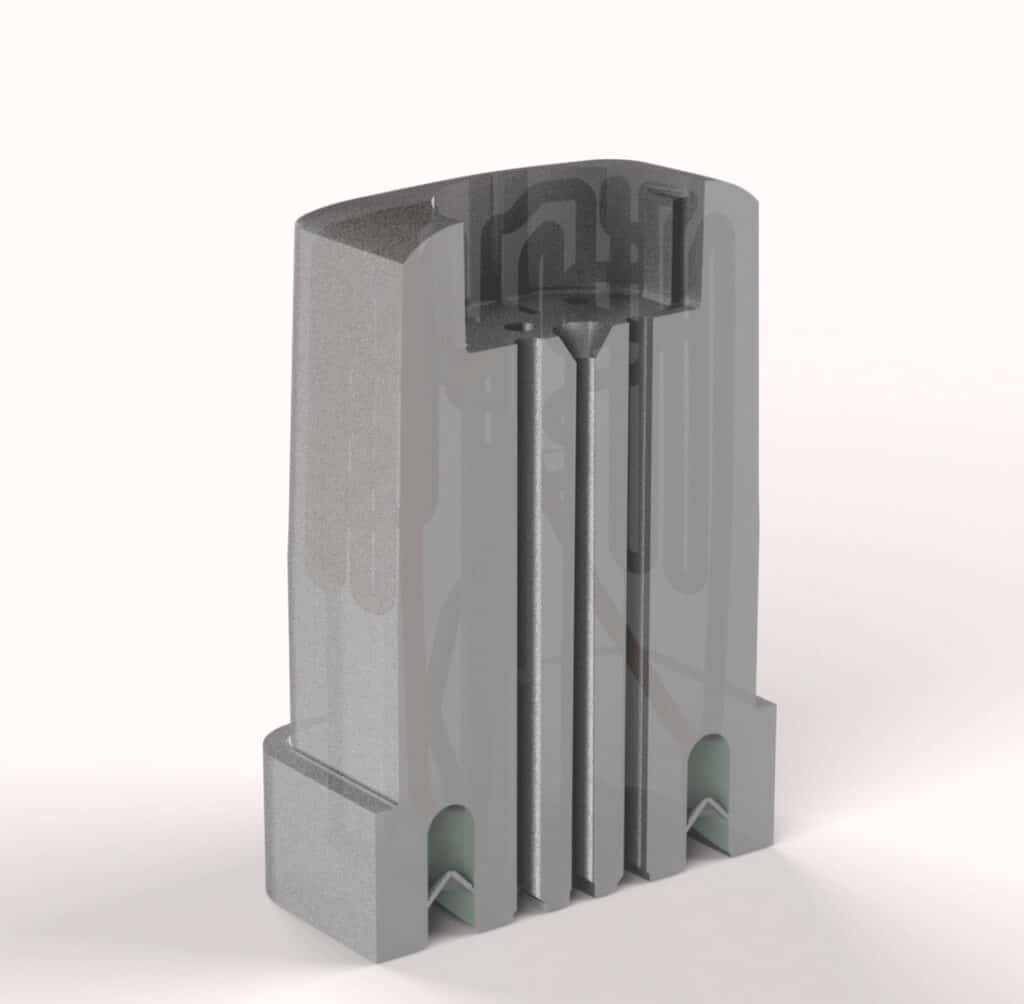
-
Design of parallel and balanced cooling circuits.
-
Stock material as small for post-processing
-
Addition of references and clamping surfaces