INDUSTRIE
Outillage et moulage
Défis
Il a été difficile de trouver un projet potentiel chez GIRA car la plupart des prises et des interrupteurs sont produits avec une surface poli miroir. Actuellement la fabrication additive ne permet pas encore d’obtenir des résultats impeccables en termes d’intégrité des surfaces.
Nous avons donc trouvé une variante de prise pour le montage en saillie pour laquelle la qualité de surface obtenue en fabrication additive est intéressante. En raison de la hauteur de la pièce le noyau ne peut pas être suffisamment refroidi du côté de la fermeture du moule avec les méthodes conventionnelles.
Productivité accrue
Réduction du temps de fabrication
Conformal cooling
L’histoire
Le savoir-faire dans le domaine de l’outillage de Gira est synonyme de fabrication innovante de produits et de sous-ensembles de haute qualité technique avec une précision industrielle. Un point fort particulier réside dans l‘agilité et la flexibilité avec laquelle il est possible pour Gira d’étudier des concepts économiques pour la réalisation d’outillages du prototypes jusqu’à la petites séries sans oublier leur cœur de métier qui se trouve dans la réalisation d’outillages pour la production de grandes séries. Gira peut également réaliser sans problème des outils pour des pièces moulées à plusieurs composants.
L’objectif de ce projet était de modifier un outil existant afin d’obtenir des temps de cycle plus courts avec un noyau conçu pour la fabrication additive.
L’outil existant permet déjà de fabriquer l’article dans la qualité requise. Et bien que le refroidissement conventionnel du noyau de moule ne soit pas optimal, le temps de cycle se situe lui déjà dans une zone économique.
Il y a cependant encore du potentiel pour améliorer le temps de cycle et ce en intégrant un circuit de refroidissement plus performant et réalisable uniquement en fabrication additive.
Défi
La pièce finale fabriquée par le moule est une prise en polycarbonate avec une épaisseur de paroi d’environ 3mm. Le noyau de l’insert présente une grande surface de contact avec le polycarbonate. Toute cette surface doit être refroidie de manière homogène afin d’obtenir une conduction thermique optimisée par rapport au noyau traditionnel. Pour obtenir une dissipation de chaleur plus homogène, il est important de disposer les canaux de refroidissement à la même distance de toutes les surfaces et de choisir l’espacement entre les canaux en conséquence.
En suivant ces règles, on obtient un circuit de refroidissement très efficace, mais qui peut aussi être très complexe. Après le processus d’impression 3D, la pièce doit être soigneusement dépoudrée, et plus le refroidissement est complexe, plus le dépoudrage des canaux peut être compliqué. Cette étape de la chaîne de process est cruciale à la fois pour la fonctionnalité de la pièce et pour la sécurité des travailleurs exposés à la poudre.
La livraison de pièces irréprochables et la protection des travailleurs sont des priorités absolues pour AddUp.
Solution
Les propriétés géométriques du noyau ont été utilisées pour la construction des canaux. Il existe un axe de symétrie autour duquel un canal peut être répété. Cette propriété est fréquemment utilisée pour réduire les coûts de design, mais aussi pour obtenir des canaux parfaitement équilibrés, puisqu’ils sont tous identiques.
Comme ce noyau est installé dans un moule existant, les entrées et sorties de refroidissement sont prédéfinies. Pour alimenter les quatre canaux en liquide de refroidissement, un circuit de quatre canaux parallèles est installé dans le noyau. De cette manière, il est possible de raccorder tous les canaux aux alimentations en liquide de refroidissement existantes.
Une fois les canaux conçus, il convient d’anticiper l’opération de dépoudrage. L’orientation d’une pièce sur la plateforme d’impression 3D est déterminée par sa géométrie, les tolérances souhaitées et la quantité de supports que l’on souhaite utiliser. Dans le cas de ce noyau, l’orientation à privilégier est évidente en raison de l’encoche pour la fiche et de l’angle pour le démoulage. Cette orientation a cependant l’inconvénient de rendre la pièce difficile à dépoudrer, car les entrées et les sorties se trouvent sur le plateau.
Afin de garantir que l’opérateur n’entre pas en contact avec la poudre, seules les pièces parfaitement dépoudrées peuvent être sorties de la zone d’impression. Dans cette zone, les opérateurs sont équipés de vêtements de protection et d’appareils respiratoires, ce qui n’est pas le cas dans les autres étapes du process de fabrication.
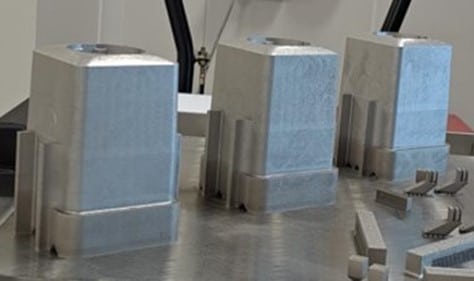
Afin de dépoudrer parfaitement les quatre canaux du système de refroidissement, la pièce doit d’abord être sciée de la plateforme de construction. Afin d’éviter que la poudre ne s’échappe de la pièce, une membrane a été installé à l’entrée et à la sortie des canaux. Celles-ci ne sont retirées de la pièce qu’une fois celle-ci de retour dans la zone poudre afin de la dépoudrer en profondeur.
Cet exemple montre que même une pièce très complexe peut être dépoudrée sans exposition directe à la poudre car la sécurité des collaborateurs doit toujours être une priorité.
Results
Une amélioration de la régulation de la température et une réduction du temps de refroidissement sont garanties.
A l’avenir, dès qu’une opportunité de modifier un moule existant grâce à la fabrication additive se présente à un stade précoce du développement, celle-ci doit être étudiée et simulée
Ce projet a montré qu’une autre approche de la conception peut être avantageuse.
Une autre collaboration avec AddUp est prévue dans les prochaines semaines et devrait permettre d’identifier d’autres pièces éligibles pour bénéficier des avantages de la fabrication additive.
Amélioration du contrôle de la température
Réduction du temps de refroidissement
Compréhension des méthodes de conception pour la fabrication additive