INDUSTRY
Aerospace
CHALLENGE
Reducing the mass and lead time while optimizing
an Aircraft Floor Bracket
KEY BENEFITS
- 61% mass reduction of the part
- Part printed without any supports
- Industry leading surface finish
Reduced Lead Time
No Support
Weight Reduction
This proof of concept demonstrated by Add Up showcases the value of using Additive Manufacturing (AM) for aeronautics by applying topological optimization to an aircraft floor bracket.
History
An aircraft floor bracket secures the cabin floor to the fuselage and is present in large quantities in all aircraft. AddUp developed this proof of concept demonstrator to illustrate the value of using Additive Manufacturing for aeronautics by carrying out a topological optimization study with no supports. This part traditionally weighs around 3 kg and is typically machined from a 12 kg metal block.
Challenges
The weight of an aircraft poses various challenges, including structural integrity, fuel efficiency, payload capacity, and performance during takeoff and landing. Excessive weight can strain the aircraft’s structure, increase fuel consumption, limit payload capacity, and require longer runways.
Safety considerations, such as balance and stability, are crucial, and the cost and economics of weight must also be considered. To address these challenges, aircraft designers and operators focus on using lightweight materials, efficient designs, and operational practices that strike a balance between weight reduction, performance, and safety.
In most metal 3D printing machines, supports must be added to the part to produce surfaces with an inclination of less than 45° from the horizontal. These supports represent a significant cost and contribute to the time of part delivery.
SOLUTIONS
Topology optimization, the mathematical method that optimizes material within a given space with the goal of maximizing performance, was utilized to remove significant amounts of material.
First, a CAD model was created, incorporating the desired shape and the stress constraints the part needs to withstand.
Next, topological optimization algorithms evaluated the stress distribution throughout the part and systematically removed excess material from low-stress regions while reinforcing high-stress areas.
This resulted in a lightweight design that maintains structural integrity under anticipated loads. The part was then printed on the FormUp 350 powder bed fusion machine, using a fine powder and roller combo to reduce the need for supports. This combination also provided a smooth and uniform surface finish, which plays a critical role in the fatigue behavior LPBF parts and reduces the need for post-processing.
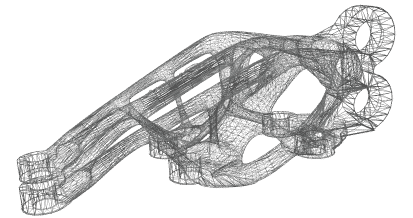
The Results
By utilizing the fine powder and roller recoater combination found only on the FormUp 350, there were no support structures required; overhangs can go as low as 30° or even 15°. By removing the need for support structures, 250 g of raw material was saved. This reduced the build time by 3 hours and saved another 30 minutes for support removal. This also lowers the overall total lead time, an important metric in the Aerospace industry.
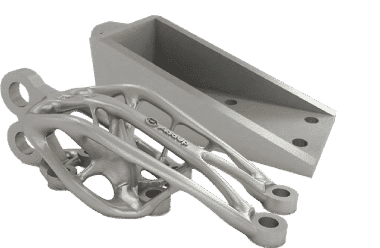
Build Time on the FormUp 350 (at 50 μm)
11.50 Hours
Weight Reduction
From 3 Kg down to 1.17 Kg
A 61% weight reduction!
Raw Material Savings
10.83kg
Saved Time
3+ hours