Ready-for-Flight Antenna in Powder Bed Fusion
Thales Alenia Space is a french aerospace manufacturer that has played a significant role in space exploration for more than 40 years. As new technologies usher in the new era of space exploration, reducing overall lead time and increasing throughput becomes especially important in staying competitive in the growing market. Learn how Thales used the FormUp 350 and aluminum AS7 to achieve their additive manufacturing goals in this case study.
INDUSTRY
Space
CHALLENGE
Design and build a monolithic antenna using additive manufacturing that meets ECSS qualifications and supports the customer’s goal of achieving TRL 3 maturity for additively manufactured antennas.
KEY BENEFITS
- Global distortions of the antenna: ±0.3mm
- Reduced weight: less 600 gr
- Production rate: 1 antenna /day /machine
- Reduced post-processing
Reduced lead time
Creative Shape
Printed in One Piece
Thin Walls
History
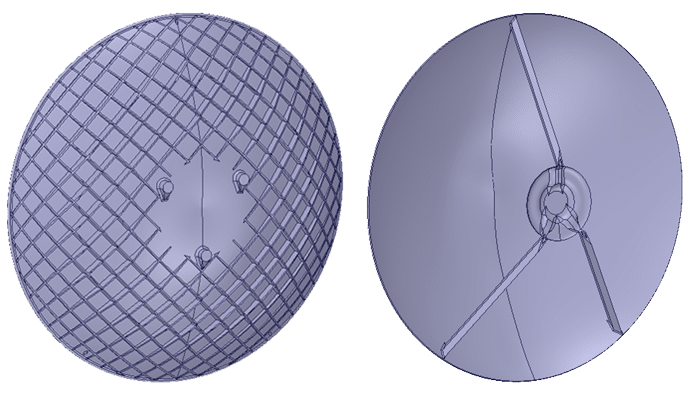
Typically, Thales Alenia Space manufactures this type of antenna in multiple parts. Then, each piece is bonded or bolted together in complex and time-costly steps. While making precise components is not so difficult, assembling them into a precise antenna is time-consuming and has major impacts on global lead time and throughput for serial production. This is why Thales turned to additive manufacturing as a solution.
Challenge
Develop a 325mm diameter antenna with a 1mm wall thickness through additive manufacturing, ensuring minimal distortions and a surface finish that meets ‘ready-to-fly’ standards without requiring post-processing. By meeting these standards, TAS will be positioned to achieve a Technology Readiness Level (TRL) 3 for additive manufactured Cassegrain antennas.
Solution
AddUp worked closely with Thales Alenia Space to provide a counter-deformed simulation.
First a lightweight design was generated around initial specifications: main and sub reflectors surfaces, available design space, interfaces localization. Next, an isogrid structure was designed at the back of the main reflector to add stiffness to the system. Then a numerical simulation was done to anticipate the distortions of the antenna during the production.
Finally, a counter-deformed file is obtained from the initial simulation. The goal is to adapt the original design in the opposite direction of the simulated distortions. During the production, the distortions due to the internal constraints and the counter-deformed design cancel each other, keeping the real part as close as possible to the original design.
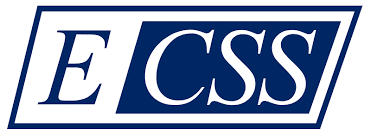
In order to get the best surface finish, requiring minimal post-processing, AddUp and Thales Alenia Space used their ECSS-qualified recipe on the FormUp 350, in aluminum AS7.
The performance of this recipe, coupled with the machine’s full-field 4 lasers, also enable high productivity. Series production simulations carried out by AddUp show a production rate of more than 2 antennas per day per machine.
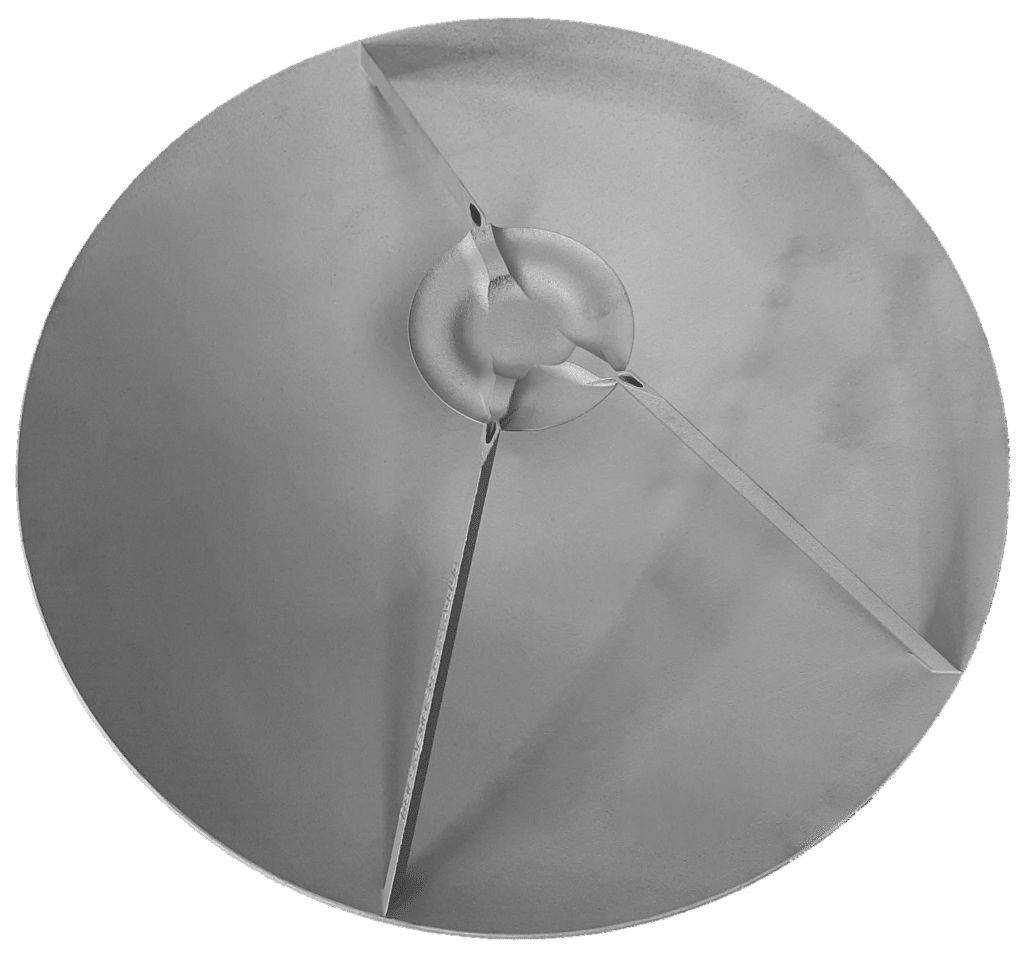
Results
The final design achieved a lightweight antenna, weighing just 385 grams. The isogrid structure was meticulously optimized to minimize weight by varying the sizes around the reflector, thereby reinforcing only the necessary areas. The connecting arms between the main reflector and the sub-reflector were engineered and designed to minimize coupling effects in near field, optimizing overall antenna far field radiated performances. The distortions were successfully minimized, with a deviation of ±0.3mm over 90% of the antenna, which was well-received by both parties involved. Additionally, the global surface finish and roughness met the target of Ra 6.3 for both reflectors, achieving a completely satisfactory result.
Learn about Thales 3D Morocco’s FormUp 350 ECSS Qualification here.