The Importance of Surface Finish When Manufacturing Medical Devices and Implants
Surface finish is crucial in additive manufacturing of medical devices and implants, as it must meet or exceed the standards set by traditional subtractive manufacturing methods, ensuring better patient outcomes and reducing contamination risks.
Due to the novelty of additive manufacturing, surface finish will always be compared back to subtractive manufacturing. This is even reflected in ASTM standards for additive manufacturing. ASTM F3001 which is the standard for Ti6Al4V ELI (Extra Low Interstitial) used with Powder Bed Fusion constantly references ASTM F136 which is the standard for Wrought Ti6Al4V ELI Alloy for Surgical Implant Applications. This sets the bar for the additive manufacturing industry that the final finished good must be equivalent or better than products manufactured from bar stock.
Medical Implants: Better Surface Finish for Better Patient Outcomes
On the implant side of the medical industry, additive manufacturing has been innovative. No longer are product development engineers looking to spray their parts with plasma porous spray to gain osteointegrative benefits, they are intentionally designing complex structures that mimic bone. These complex structures cannot be traditionally manufactured and can be more easily validated unlike plasma porous spray.
Industrial metal 3D printers are steadily improving their surface finish to be closer to wrought directly from the printing process. Advances are being made in recoating systems, melt-monitoring systems, and powder handling to produce the best as-printed surfaces as possible. As additional post-printing surface treatments are developed for the additive manufacturing industry, differently manufactured parts will be indistinguishable from each other.
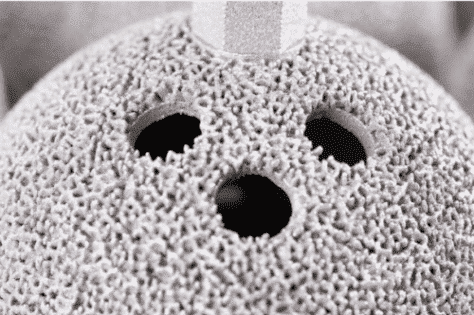
Surface finish is imperative for implantable medical devices for several reasons. A few are pathogen spread, implant rejection, part corrosion, surface contamination, reduced lifespan, and biocompatibility. Most of these reasons are directly related to patient well-being. The inherent process of additive manufacturing (layer by layer) creates voids in the material that can be difficult to clean and sterilize. This creates plentiful spaces for bacteria to hide in. It is of utmost importance that the implant can be thoroughly cleaned before it is in a surgical setting. Then there is always the aesthetic of the implant itself. A cosmetically good-looking implant intuitively portrays itself as clean, functional, and well manufactured.
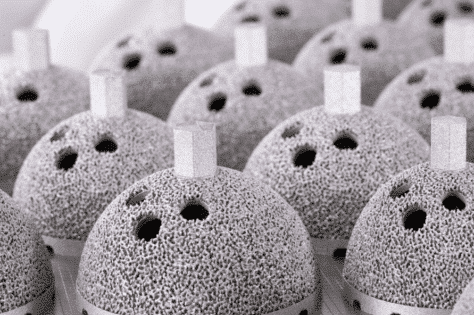
Minimize Finishing Treatments to Reduce Cost and Lead Time
Some common surface finishing treatments for additively manufactured implants include blasting, vibratory finishing, and chemical passivation. Both blasting and vibratory finishing aim to give the implant a uniform finish. They can help to blend between manufactured and printed surfaces while helping to remove any burrs or sharp edges. Blasting is typically completed with a glass bead whereas vibratory is done with some type of ceramic media. Chemical passivation is done as a cleaning step to ensure that the implant is free of any in-process materials from manufacturing before going to . As the additive manufacturing process improves, there is optimism that secondary surface finishing operations can be minimized. This can help reduce costs and potential avenues for contamination.
Surface Finish for Surgical Instruments
Surgical instruments and trauma devices must be even closer to wrought surface finish specifications. These devices do not want any type of osteointegrative features like complex structures. Reusable instruments must be able to be cleaned between surgeries and retain their sharpness. Trauma devices like plates and screws must be able to be removed once the injury has healed. These requirements tend to lead to these types of devices being made from 316L, 17-4 PH, and 420. Technology advances are allowing these industrial 3D printers to utilize fine powders and resolve a better surface finish closer to a traditionally manufactured device.
AddUp’s Solution
Achieving parts directly off the printer with optimal surface finish is a priority for AddUp. That’s because industry-leading surface finish means less post processing and therefore cost reduction for our customers. The FormUp 350 provides advanced technology with a roller recoating system that allows many parts to meet surface finish requirements as printed.
Controlling the penetration of the melt into the lower layers is a key factor in the surface quality of a 3D metal-printed part. Poorly managed, it leads to high variations in Ra index, with high sensitivity to surface angle. Using AddUp’s roller spreading system, the homogeneity of the powder bed is greatly enhanced, limiting this type of variation and allowing for a smoother surface finish as printed. Parts printed on the FormUp 350 achieve an Ra value as low as 3µm.
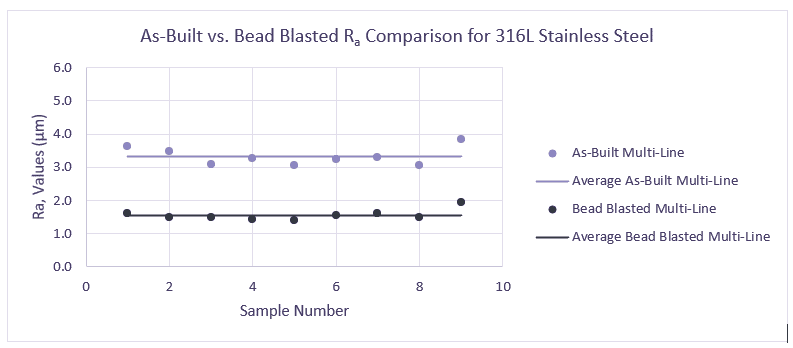
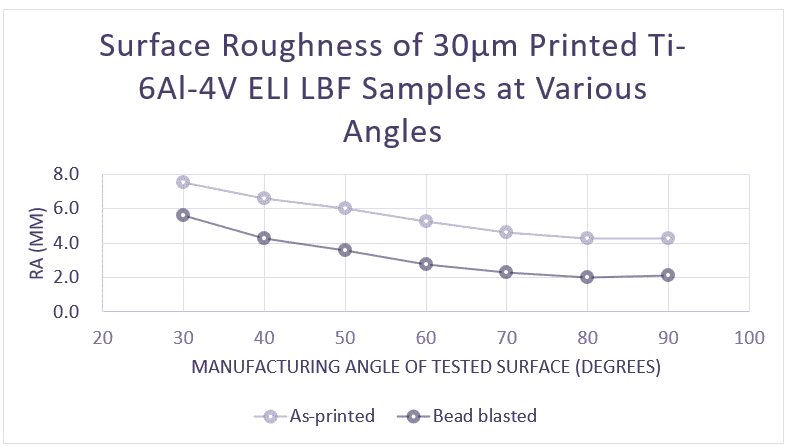
In addition, AddUp uses finer powder (PSD 5-25µm) instead of the widely-used industry standard medium powders (PSD 15-45µm or 20-63 µm). This makes it possible to considerably reduce the size of the voids between particles therefore improving the permeability of the powder bed, reducing erratic bath penetration and lowering laser power. The use of these fine powders not only enhances the surface finish for parts printed on the FormUp 350, but it also greatly reduces the need for support structures.
Learn more about AddUp’s FormUp 350 for medical applications here.
Driving Innovation and Advancement
Manufacturers are continuously encouraged to improve their processes and technologies. In the case of AM, certifications push for research and development in areas such as material science, process optimization, and design guidelines. By setting stringent criteria for certification, manufacturers are motivated to innovate and refine their practices. This drive for innovation not only benefits the individual companies but also contributes to the overall advancement of the manufacturing industry.