Die Oberflächenbeschaffenheit ist bei der additiven Fertigung von Medizinprodukten und Implantaten von entscheidender Bedeutung, da sie die Standards herkömmlicher subtraktiver Fertigungsverfahren erfüllen oder übertreffen muss, um bessere Ergebnisse für die Patienten zu erzielen und Kontaminationsrisiken zu verringern.
Aufgrund der Neuartigkeit der additiven Fertigung wird die Oberflächengüte immer wieder mit der subtraktiven Fertigung verglichen werden. Dies spiegelt sich sogar in den ASTM-Normen für die additive Fertigung wider. Die ASTM F3001, die Norm für Ti6Al4V ELI (Extra Low Interstitial) für das Pulverbettschmelzen, verweist ständig auf die ASTM F136, d i e Norm für die Knetlegierung Ti6Al4V ELI für chirurgische Implantatanwendungen. Diese Norm setzt die Messlatte für die additive Fertigungsindustrie so hoch, dass das fertige Produkt gleichwertig oder besser sein muss als Produkte, die aus Stangenmaterial hergestellt werden.
Medizinische Implantate: Bessere Oberflächenbeschaffenheit für bessere Patientenresultate
Im Bereich der Implantate hat die additive Fertigung in der Medizintechnik neue Wege beschritten. Die Produktentwicklungsingenieure sind nicht mehr darauf aus, ihre Teile mit plasmaporösem Spray zu besprühen, um osteointegrative Vorteile zu erzielen, sondern sie entwerfen bewusst komplexe Strukturen, die den Knochen nachahmen. Diese komplexen Strukturen können nicht auf herkömmliche Weise hergestellt werden und lassen sich im Gegensatz zu plasmaporösem Spray leichter validieren.
Industrielle 3D-Metalldrucker verbessern ständig ihre Oberflächenbeschaffenheit, so dass sie direkt nach dem Druckprozess dem Kneten näher kommen. Es werden Fortschritte bei den Wiederbeschichtungssystemen, den Schmelzeüberwachungssystemen und der Pulverhandhabung gemacht, um die bestmöglichen druckfertigen Oberflächen zu erzeugen. In dem Maße, in dem zusätzliche Oberflächenbehandlungen nach dem Druck für die additive Fertigungsindustrie entwickelt werden, werden unterschiedlich hergestellte Teile nicht mehr voneinander zu unterscheiden sein.
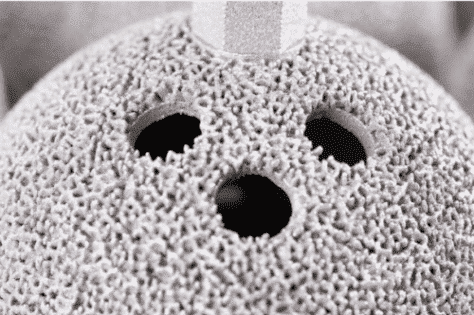
Die Oberflächenbeschaffenheit ist für implantierbare medizinische Geräte aus mehreren Gründen von entscheidender Bedeutung. Einige davon sind die Verbreitung von Krankheitserregern, die Abstoßung von Implantaten, die Korrosion von Teilen, die Verunreinigung der Oberfläche, die verkürzte Lebensdauer und die Biokompatibilität. Die meisten dieser Gründe stehen in direktem Zusammenhang mit dem Wohlbefinden der Patienten. Durch den inhärenten Prozess der additiven Fertigung (Schicht für Schicht) entstehen Hohlräume im Material, die schwer zu reinigen und zu sterilisieren sind. Dadurch entstehen reichlich Räume, in denen sich Bakterien verstecken können. Es ist äußerst wichtig, dass das Implantat gründlich gereinigt w e r d e n kann, bevor es in einem chirurgischen Umfeld eingesetzt wird. Und dann ist da noch die Ästhetik des Implantats selbst. Ein kosmetisch gut aussehendes Implantat stellt sich intuitiv als sauber, funktionell und gut verarbeitet dar.
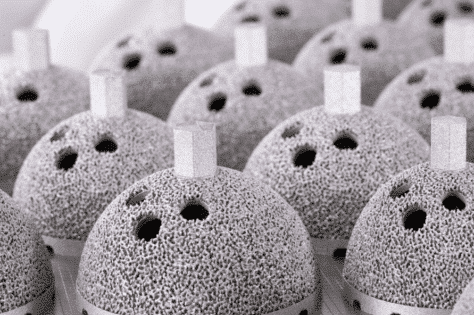
Minimierung von Nachbearbeitungen zur Reduzierung von Kosten und Vorlaufzeiten
Zu den üblichen Oberflächenbehandlungen für additiv gefertigte Implantate gehören Strahlen, Gleitschleifen und chemische Passivierung. Sowohl das Strahlen als auch das Gleitschleifen zielen darauf ab, dem Implantat eine einheitliche Oberfläche zu verleihen. Sie können dazu beitragen, dass die hergestellten und die gedruckten Oberflächen miteinander verschmelzen und gleichzeitig Grate oder scharfe Kanten entfernt werden. Das Strahlen erfolgt in der Regel mit einer Glasperle, während die Vibration mit einer Art Keramikmedium durchgeführt wird. Die chemische Passivierung wird als Reinigungsschritt durchgeführt, um sicherzustellen, dass das Implantat vor der Verarbeitung frei von prozessbedingten Materialien aus der Herstellung ist. Mit der Verbesserung des additiven Fertigungsverfahrens b e s t e h t d i e Hoffnung, dass die sekundären Oberflächenbearbeitungsschritte minimiert werden können. Dies kann dazu beitragen, Kosten und potenzielle Kontaminationsquellen zu reduzieren.
Oberflächenbehandlung für chirurgische Instrumente
Chirurgische Instrumente und Traumavorrichtungen müssen sogar noch näher an den Spezifikationen für die Oberflächenbeschaffenheit von Schmiedearbeiten sein. Diese Geräte dürfen keine osteointegrativen Merkmale wie komplexe Strukturen aufweisen. Wiederverwendbare Instrumente müssen zwischen den Eingriffen gereinigt werden können und ihre Schärfe beibehalten. Traumavorrichtungen wie Platten und Schrauben müssen entfernt werden können, sobald die Verletzung verheilt ist. Diese Anforderungen führen in der Regel dazu, dass diese Art von Geräten aus 316L, 17-4 PH und 420 hergestellt werden. Dank des technologischen Fortschritts können diese industriellen 3D-Drucker feine Pulver verwenden und eine bessere Oberflächenbeschaffenheit erzielen, die einem traditionell hergestellten Gerät näher kommt.
AddUp’s Lösung
Die Herstellung von Teilen direkt aus dem Drucker mit optimaler Oberflächengüte hat für AddUp Priorität. Das liegt daran, dass eine branchenführende Oberflächengüte weniger Nachbearbeitung und damit Kostenreduzierung für unsere Kunden bedeutet. Der FormUp 350 bietet eine fortschrittliche Technologie mit einem Walzenbeschichtungssystem, das es vielen Teilen ermöglicht, die Anforderungen an die Oberflächenbeschaffenheit im Druck zu erfüllen.
Die Kontrolle des Eindringens der Schmelze in die unteren Schichten ist ein Schlüsselfaktor für die Oberflächenqualität eines 3D-Metalldruckteils. Schlecht gemanagt, führt dies zu hohen Schwankungen des Ra-Indexes, mit hoher Empfindlichkeit gegenüber dem Oberflächenwinkel. Durch den Einsatz des AddUp- Walzenauftragssystems wird die Homogenität des Pulverbettes erheblich verbessert, was diese Art von Schwankungen einschränkt und ein glatteres Oberflächenfinish beim Druck ermöglicht. Auf dem FormUp 350 gedruckte Teile erreichen einen Ra-Wert von nur 3µm.
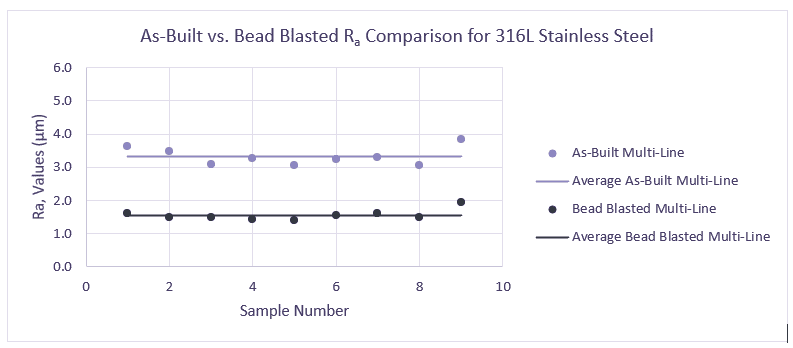
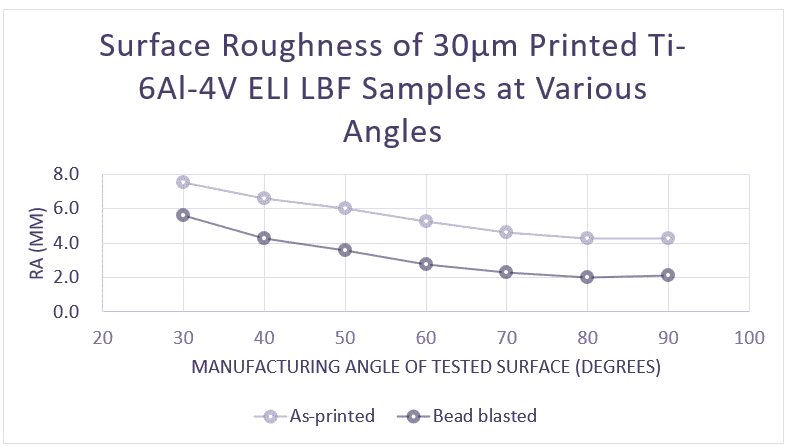
Darüber hinaus verwendet AddUp feinere Pulver (PSD 5-25µm) anstelle der in der Industrie weit verbreiteten mittleren Pulver (PSD 15-45µm oder 20-63 µm). Dadurch kann die Größe der Hohlräume zwischen den Partikeln erheblich reduziert werden, was die Durchlässigkeit des Pulverbettes verbessert, die unregelmäßige Baddurchdringung verringert und die Laserleistung senkt. Durch die Verwendung dieser feinen Pulver wird nicht nur die Oberflächengüte der auf dem FormUp 350 gedruckten Teile verbessert, sondern auch der Bedarf an Stützstrukturen erheblich reduziert.
Erfahren Sie hier mehr über AddUps FormUp 350 für medizinische Anwendungen.
Innovation und Fortschritt vorantreiben
Die Hersteller werden kontinuierlich dazu angehalten, ihre Prozesse und Technologien zu verbessern. Im Fall von AM fördern Zertifizierungen die Forschung und Entwicklung in Bereichen wie Materialwissenschaft, Prozessoptimierung und Designrichtlinien. Durch die Festlegung strenger Kriterien für die Zertifizierung werden die Hersteller motiviert, ihre Verfahren zu erneuern und zu verfeinern. Dieses Streben nach Innovation kommt nicht nur den einzelnen Unternehmen zugute, sondern trägt auch zum allgemeinen Fortschritt der Fertigungsindustrie bei.