Additive Manufacturing in the Medical Industry
AM enables the production of highly complex and customized designs that can precisely match the patient’s anatomy, ensuring optimal fit and function. AM also allows for the geometric complexity that is necessary to create lattice structures not only needed to reduce weight but also to create a porous surface that improves bone integration within the human body. These benefits offered by AM improve patient outcomes and reduce the need for additional surgeries or modifications.
Mastering the Process. Replicating Perfection
Industrializing AM to allow for serial production requires a repeatable and reliable platform. AddUp’s FormUp 350 Powder Bed Fusion (PBF) machine was built for productivity. Our 4-laser system reduces fusion times by up to 75%, when compared to a single laser system, providing maximum throughput to meet the demands of the medical device market. This results in an increased operational equipment efficiency (OEE) and overall lower total cost of ownership (TCO).
The FormUp 350 offers enormous flexibility in terms of powder use. It can be used with the market-standard medium powder, but is also capable of handling a finer powder. Thanks to our roller recoater technology, a smooth surface finish with fine features and lattice resolution is achievable directly as printed. The AddUp FormUp 350 offers the freedom to design implants with geometric complexity and minimal support structures, reducing the need for extensive post-processing.
We understand the needs of medical device manufacturers and provide a trusted pair of hands along the AM adoption journey. Our experts work with you to develop your application and we have the knowledge and experience to help you reduce your time to market while offering a validation pathway with IQ, OQ, and PQ processes, along with powder reuse guidelines.
Maximum Throughput
The FormUp 350 more than doubles the output of single laser systems, meeting the demand for the medical industry while lowering costs for medical device manufacturers.
Superior Surface Finish
Achieve a smooth surface finish with fine features and lattice resolution as printed thanks to our roller recoater technology.
Reduced Supports
Design with complexity, freedom and minimal supports. Drastically reduce post-processing requirements and save material costs.
A Partner You Can Trust
Experience and validation pathway with IQ, OQ, and PQ processes along with accelerated qualification thanks to AddUp’s certified facilities.
Open Machine Parameters
Some competitors keep the workings of their machines secret, but we don’t. Do more with our open platform by twisting and turning the knobs as you see fit.
Quality Assurance
In-process monitoring gives our users peace of mind and real-time quality assurance, providing confidence in part quality, build-to-build and part-to-part.
“The FormUp350 is one of the only machines on the market that can run both the typical LPBF powder cut and a much finer cut of powder. This gives us flexibility to meet certain challenging applications we may come across in the future.”
Rachel Levine
Key Applications in the Medical Industry
AM can improve the effectiveness of replacement surgeries because additively manufactured implants are lighter, more stable and have improved osteointegration. This means implants have a longer life cycle with less risk of defect or implant complications and therefore provide a better patient outcome and quality of life.
The FormUp 350 is currently being used by AddUp customers around the world to create hundreds of certified orthopedic implants each year. AddUp has extensive experience in large orthopedic implants including acetabular hip cups, tibial knee implants and shoulder implants. We are also experienced in a variety of spinal implants as well as patient specific (custom) implants. The FormUp 350 offers increased product differentiation and advanced design features thanks to our roller recoater technology which allows for fine features and lattice resolution.
Acetabular Hip Cups
These implants are used during a hip replacement surgery most commonly needed to treat arthritis, osteoarthritis and rheumatoid arthritis. AddUp’s FormUp 350 can build 34 hip implants in only 12 hours thanks to a 350mm squared build plate and 4-laser capabilities. These implants are created with out support structures on the underside, drastically reducing the amount of post processing needed and material used.
Knee Tibial Tray
The tibial tray is an important part of the implant needed for a knee replacement surgery. When additively manufactured, this component of the implant provides improved osseointegration which results in better patient outcomes after surgery. The FormUp 350 can build 22 tibial trays in only 17 hours. These implants are printed with minimal supports which greatly reduces the amount of post processing needed, reducing overall costs for the device manufacturer.
Shoulder Implants
Shoulder implants are a critically important part of preserving shoulder function. Every patient’s shoulder joint has unique characteristics, and the ability to customize implants is a significant advantage of AM. AM allows for the customization of these implants to be designed and manufactured specifically tailored to an individual patient’s anatomy while including intricate internal structures and porous surfaces for better integration with the surrounding bone.
Spine Implants
Spinal fusion joins two or more vertebrae together using bone graft inside of a titanium implant. This surgery can treat disorders like degenerative disc disease, scoliosis, spondylolisthesis, and fracture. AddUp has extensive experience creating spinal implants of varying sizes with unique break-away support structures. This combined with the productivity achievable on the FormUp 350 provides reduced costs for medical device manufacturers. The FormUp 350 can print 152 large spinal implants is just 32 hours.
Patient Specific Implants
Patient Specific Implants (PSI) are implants that are made from a patient’s CT scan data moved into a CAD file and then additively manufactured. PSIs are typically too complex to machine and cut, therefore they are ideally made through AM. AddUp has experience in manufacturing patient specific ankles, shoulders, and spinal fusion devices. The FormUp 350 has a large build plate providing the ability to print many different implants of varying shapes and sizes on the same build. The ability to manufacture multiple individual surgical cases on a single build plate streamlines the process from the manufacturing site to the hospital. This can provide each patient with a completely tailored implant that meets their unique needs while reducing surgery costs and recovery times.
Acetabular Hip Cup Implant
Acetabular Cups plate History Acetabular cups are used during the total hip replacements to sit against the..
Patient Specific Implants
This case study highlights the advantages of using additive manufacturing (AM) for Patient Specific Implants (PSI) in the orthopedic industry. By shifting from traditional manufacturing to AM, orthopedic OEMs can…
Spine Implants
This case study focuses on spine implants and the challenges faced in their manufacturing process today. Additive Manufacturing (AM) offers benefits such as lattice design and surface roughness, leading to…
Tibia Tray
This case study focuses on tibia trays in orthopedic manufacturing and the challenges faced in producing highly complex and customized implants. Additive Manufacturing (AM) using biocompatible materials like titanium offers…
Materials used in the Medical Industry
Typical materials used in orthopedical implants must be light, durable, and very biocompatible. Materials used in the production of surgical instruments must be durable, cost effective, and have a good lifespan.
Titanium Ti64ELI
Titanium Ti64ELI is most commonly used in orthopedical implants due to its characteristics. It is a strong, lightweight, material that is very biocompatible. AddUp has optimized parameters for this material at both 30 and 60 micron layers.
Stainless Steel 316L
Stainless Steel 316L is a surgical steel and can be used to create cost effective surgical instruments.
Stainless Steel 17-4 PH
Stainless Steel 17-4 PH is also a good material to create surgical instruments. Not only is it cost effective, it also has exceptional strength.
INDUSTRIAL MACHINES
With more than 20 years experience in Additive Manufacturing, our machines have been designed to master detail and optimize productivity.
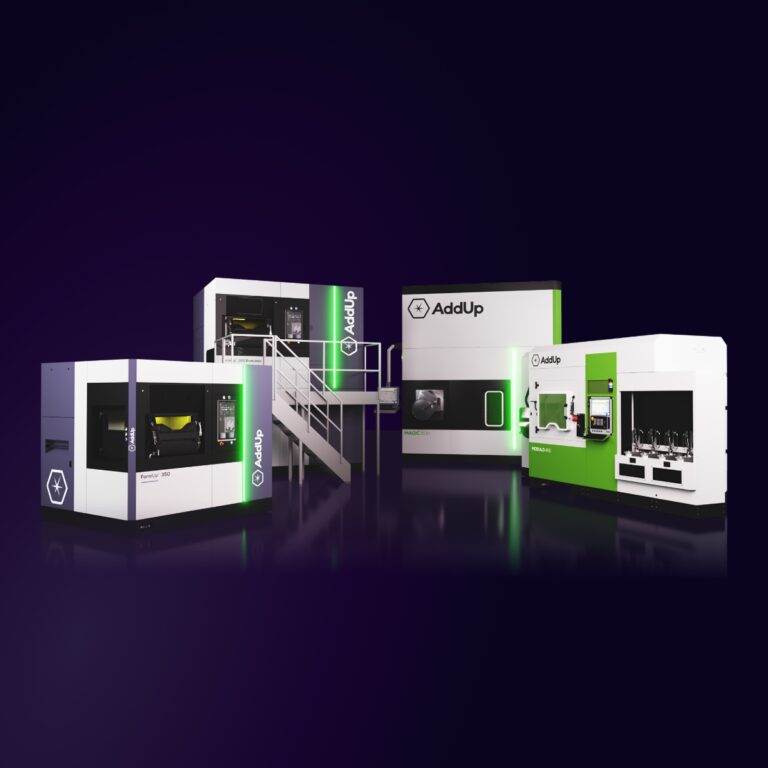
SMART SOFTWARE
Within the medical industry, the qualification and regulation of implants and devices is mandatory. AddUp is leading the way with in-process monitoring, providing confidence part quality with a full suite of quality assurance monitoring software to lessen, or even eliminate, the need for rigorous testing after a part is printed. From part preparation to simulation, monitoring, and production, every link of the AddUp digital chain offers a high level of performance with user-friendly software.
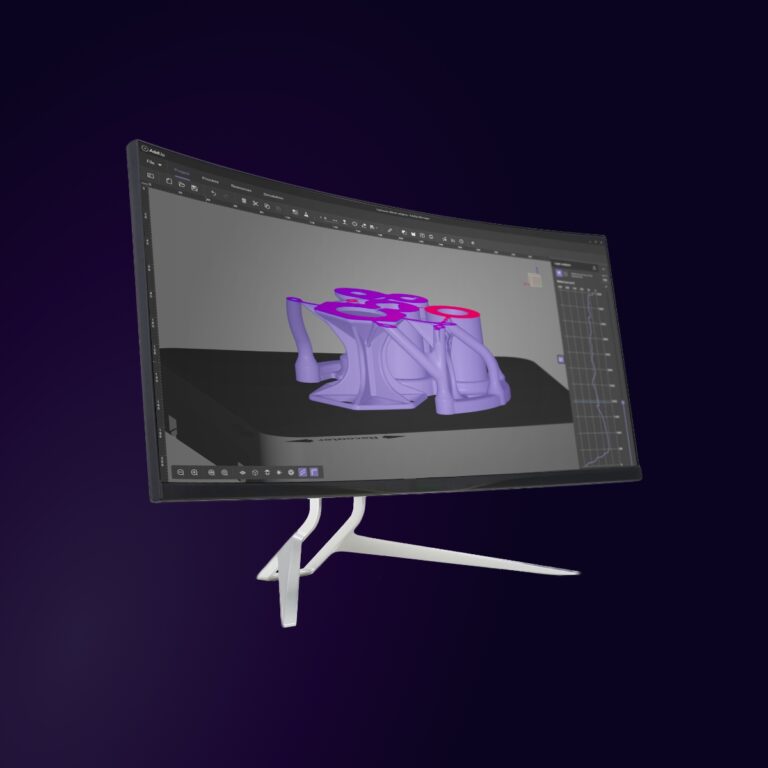
Get Started with AddUp
Realize the potential digital manufacturing has to offer. Get started with AddUp and learn how AM delivers innovative solutions to solve manufacturers toughest challenges.
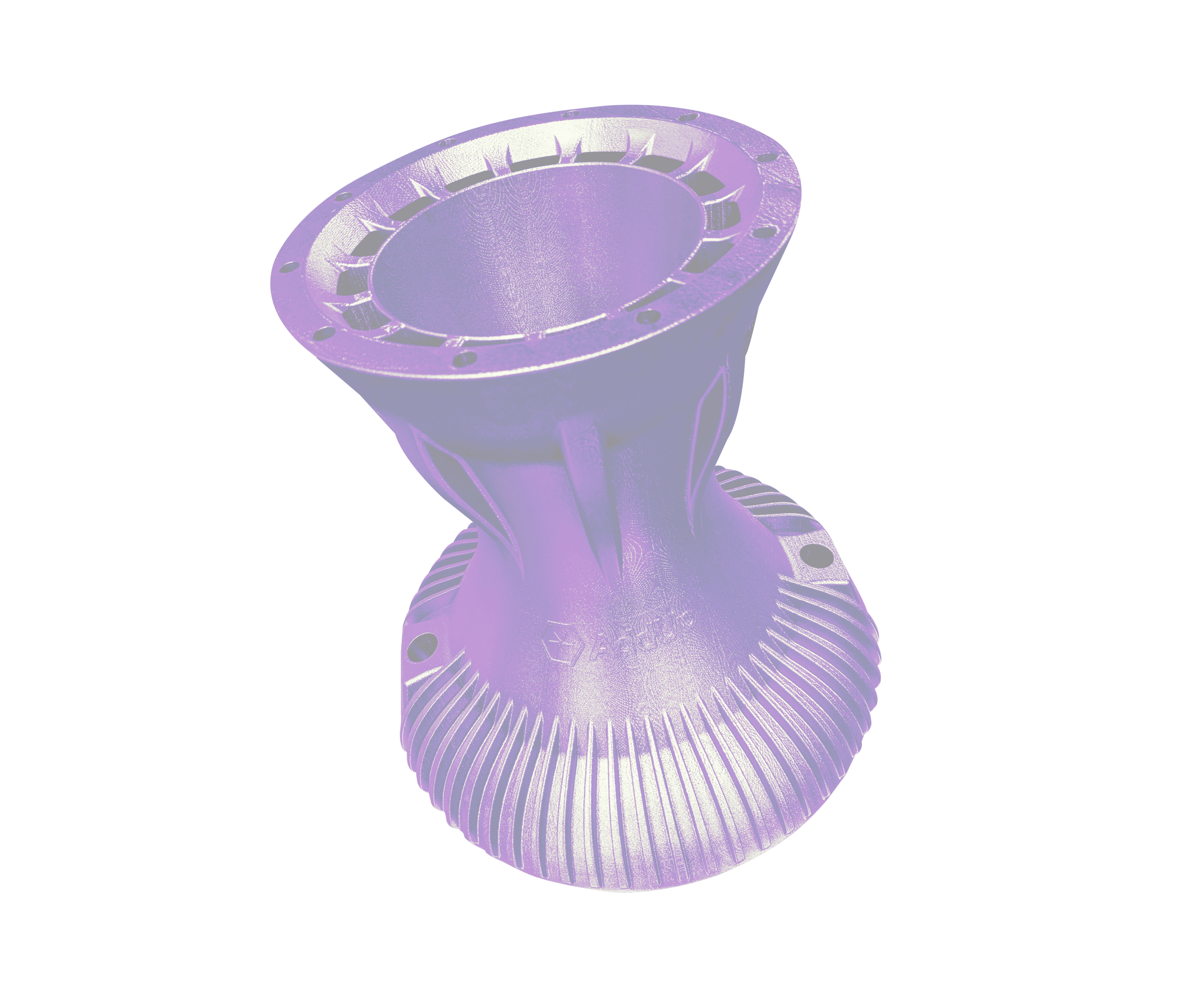