La finition de surface est cruciale dans la fabrication additive de dispositifs médicaux et d’implants, car elle doit atteindre ou dépasser les normes fixées par les méthodes traditionnelles de fabrication soustractive, garantissant de meilleurs résultats pour les patients et réduisant les risques de contamination.
En raison de la nouveauté de la Fabrication Additive, l’état de surface sera toujours comparé à la fabrication soustractive. Cela s’observe même dans les normes ASTM pour la Fabrication Additive. En effet, L’ASTM F3001, qui est la norme pour le Ti6Al4V ELI (Extra Low Interstitial) utilisé dans le procédé de fusion sur lit de poudre (PBF), fait constamment référence à l’ASTM F136, qui est la norme pour l’alliage Ti6Al4V ELI corroyé pour les applications d’implants chirurgicaux. Cette dernière détermine les niveaux d’exigence pour l’industrie de la Fabrication Additive, à savoir que le produit fini doit être équivalent ou supérieur aux produits fabriqués à partir de barres.
Implants médicaux : un meilleur état de surface pour de meilleurs résultats pour les patients
Du côté des implants de l’industrie médicale, la Fabrication Additive a été apporté de l’innovation. Les ingénieurs en développement de produits ne cherchent plus à pulvériser leurs pièces avec un spray poreux au plasma pour obtenir des avantages ostéo-intégrateurs, ils conçoivent directement des structures complexes qui imitent l’os. Ces structures complexes ne peuvent pas être fabriquées de manière traditionnelle et peuvent être validées plus facilement que la pulvérisation de plasma poreux.
Les imprimantes 3D industrielles métalliques améliorent progressivement leur finition de surface pour se rapprocher de ce qu’on peut trouver sur des pièces forgées. Des progrès sont réalisés dans les systèmes de mise en couche, les systèmes de monitoring de fusion et la gestion des poudres afin de produire les meilleures surfaces imprimées possibles.
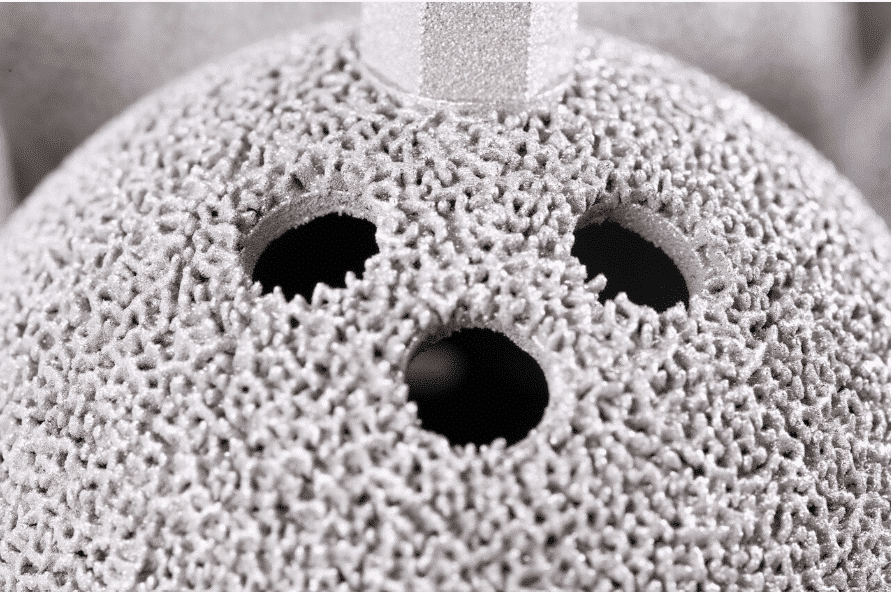
Petit à petit de nouveaux traitements de surface post-impression sont développés pour l’industrie de la Fabrication Additive, ainsi bientôt, les pièces fabriquées en FA ou en traditionnel seront impossibles à distinguer les unes des autres.
L’état de surface est impératif pour les dispositifs médicaux implantables, et ce pour plusieurs raisons. En voici quelques-unes : propagation de pathogènes, rejet de l’implant, corrosion de la pièce, contamination de la surface, réduction de la durée de vie et biocompatibilité. La plupart de ces raisons sont directement liées au bien-être du patient. Le processus inhérent à la Fabrication Additive (couche par couche) crée des vides dans le matériau qui peuvent être difficiles à nettoyer et à stériliser. Les bactéries peuvent donc s’y cacher en abondance. Il est extrêmement important que l’implant puisse être nettoyé à 100% avant d’être utilisé dans un contexte chirurgical. Ensuite, il y a toujours une notion d’esthétique de l’implant lui-même. Un implant esthétiquement « beau » donne intuitivement l’impression d’être propre, fonctionnel et bien fabriqué.
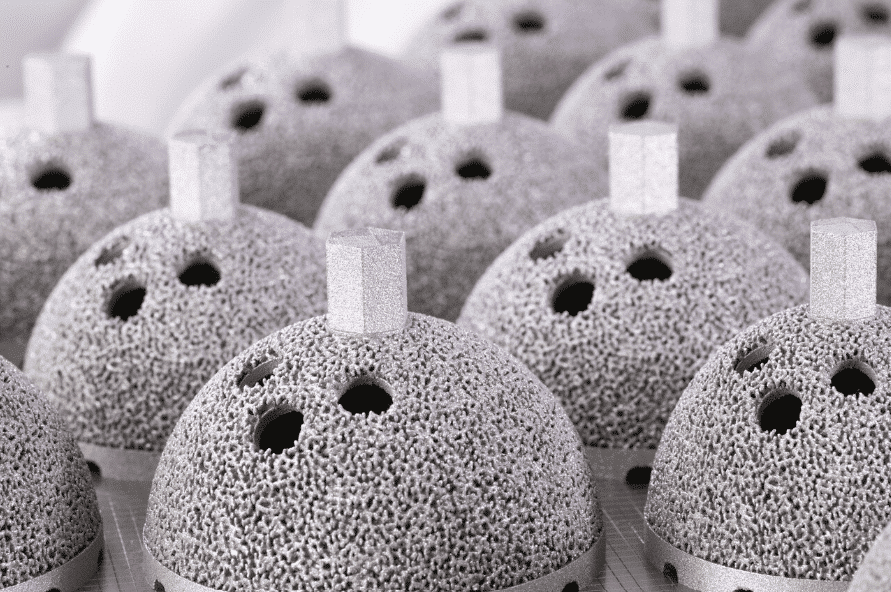
Minimiser les Traitements de Finition pour Réduire les Coûts et les Délais D’exécution
Les traitements de finition de surface les plus courants pour les implants fabriqués en additif sont le sablage, la finition vibratoire et la passivation chimique. Le sablage et la finition vibratoire visent tous deux à donner à l’implant une finition uniforme. Ils permettent d’harmoniser les surfaces fabriquées et imprimées tout en éliminant les bavures et les arêtes vives. Le sablage est généralement effectué à l’aide de micro billes de verre, tandis que la vibro-abrasion est réalisée à l’aide de supports en céramique. La passivation chimique est une étape de nettoyage qui permet de s’assurer que l’implant est exempt de tout matériau résiduel avant d’être stérilisé. Au fur et à mesure de l’amélioration du processus de Fabrication Additive, on peut espérer que les opérations de finition des surfaces secondaires pourront être réduites au minimum. Cela peut contribuer à réduire les coûts et les risques de contamination.
Finition de Surface des Instruments Chirurgicaux
Les instruments chirurgicaux et les dispositifs de traumatologie doivent être encore plus proches des spécifications de finition de surfaces des pièces forgées. Il n’est pas nécessaire que ces dispositifs présentent des caractéristiques ostéo-intégratives telles que des structures complexes. Les instruments réutilisables doivent pouvoir être nettoyés entre les interventions chirurgicales et conserver leur tranchant. Les dispositifs de traumatologie tels que les plaques et les vis doivent pouvoir être retirés une fois la blessure guérie. En raison de ces exigences, ces types de dispositifs sont généralement fabriqués à partir de nuances d’acier inoxydable 316L, 17-4 PH et 420. Les progrès technologiques permettent aux imprimantes 3D métalliques industrielles d’utiliser des poudres fines et d’obtenir une meilleure finition de l’état surface, plus proche d’un dispositif fabriqué traditionnellement.
La solution AddUp
Obtenir des pièces directement sorties de l’imprimante avec un état de surface optimal est une priorité pour AddUp. En effet, un état de surface optimal signifie moins de post-traitement et donc une réduction des coûts pour nos clients. La FormUp 350 offre une technologie avancée avec un système de mise en couche par rouleau, ce qui permet à de nombreuses pièces de répondre aux exigences de finition de surface directement en sortie d’impression.
Le contrôle de la pénétration de la matière fondue dans les couches inférieures est un facteur clé de la qualité de surface d’une pièce imprimée en 3D métal. Mal maîtrisée, elle conduit à de fortes variations de l’indice de rugosité Ra, avec une grande sensibilité à l’angle de surface. Grâce au système de mise en couche par rouleau d’AddUp, l’homogénéité du lit de poudre est grandement améliorée, ce qui limite ce type de variation et permet d’obtenir une finition de surface plus lisse lors de l’impression. Les pièces imprimées sur la FormUp 350 peuvent atteindre une valeur Ra de 3µm.
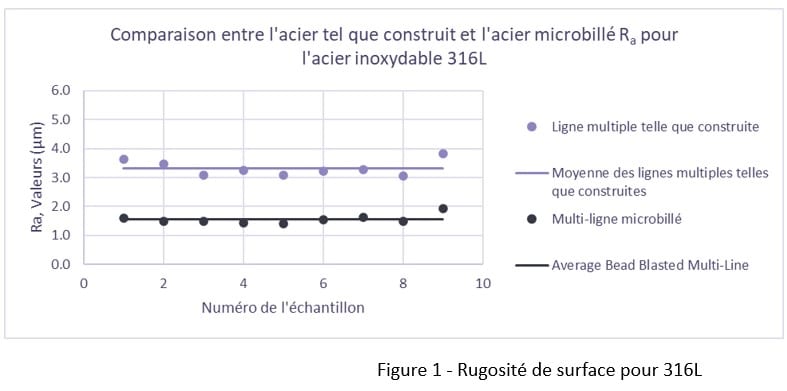
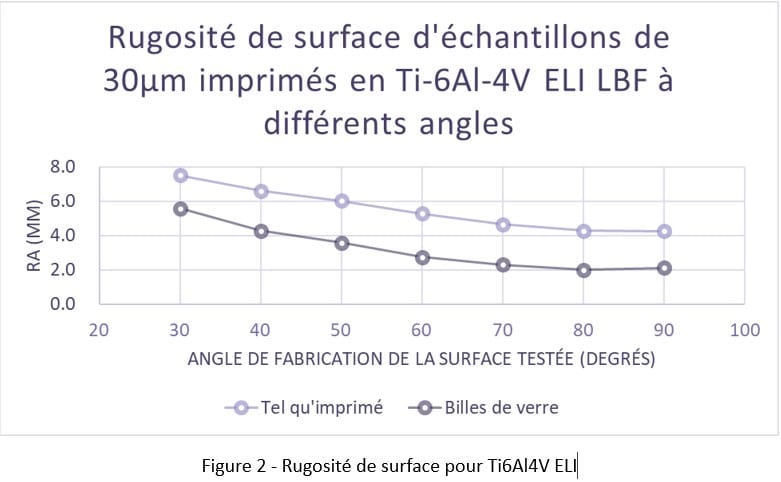
De plus, AddUp utilise une poudre plus fine (PSD 5-25µm) par rapport aux poudres moyennes largement utilisées dans l’industrie (PSD 15-45µm ou 20-63 µm). Cela permet de réduire considérablement la taille des vides entre les particules et donc d’améliorer la perméabilité du lit de poudre, de réduire la pénétration erratique du bain et de diminuer la puissance du laser. L’utilisation de ces poudres fines permet non seulement d’améliorer l’état de surface des pièces imprimées sur la FormUp 350, mais aussi de réduire considérablement le recours aux supportage.
Pour en savoir plus sur la machine FormUp 350 d’AddUp et les applications médicales, cliquez ici.