Innovations Dans la Fabrication des Dispositifs de Fusion Vertébrale | Blog
La machine FormUp 350 Powder Bed Fusion (PBF) révolutionne la fabrication de dispositifs de fusion vertébrale de grande taille, en offrant une efficacité, une précision et une rentabilité accrues.
Introduction
Les dispositifs de fusion vertébrale jouent un rôle crucial dans le domaine médical, car ils apportent un soutien et une stabilité essentiels lors des opérations de la colonne vertébrale. Traditionnellement, les dispositifs de fusion vertébrale de grande taille étaient produits à l’aide de machines de fusion sur lit de poudre (PBF) de petit format ou usinés à partir de barres de polyéthylène. Bien que ces méthodes soient efficaces, elles présentent plusieurs difficultés, notamment des coûts élevés et des temps de production longs. Cependant, l’avènement de technologies de fabrication avancées, telles que la machine FormUp 350 PBF, a révolutionné le processus de production, offrant une efficacité et une précision accrues, ainsi que de meilleurs résultats pour les patients.
Méthodes de Fabrication Traditionnelles : PBF et PEEK
Le processus de fabrication conventionnel des grands dispositifs de fusion vertébrale reposait sur le PBF ou l’usinage à partir de barres de PEEK. Ces méthodes, bien qu’efficaces, n’étaient pas sans inconvénients. Le processus de production était lent et coûteux, ce qui entraînait une augmentation du prix de l’implant fini. En outre, lorsqu’ils étaient produits en PEEK, ces types d’implants ne présentaient pas les caractéristiques d’intégration Osseo idéales, qui sont cruciales pour la réussite de l’implant. En outre, l’instabilité de la chaîne d’approvisionnement en PEEK a posé d’autres problèmes dans le processus de fabrication.
L’avènement de la Fabrication Additive
L’introduction de la fabrication additive a marqué un changement important dans la production de grands dispositifs de fusion vertébrale. Cependant, la fabrication de ces dispositifs sur des plates-formes plus petites avec 1 ou 2 lasers a augmenté le coût de l’implant fini. Ces implants étaient hauts en Z, ce qui a entraîné une augmentation des temps de construction, encore accrue avec un petit nombre de lasers. En outre, l’utilisation d’un processus de recouvrement par raclage/brossage et la nécessité d’un usinage par décharge électrique (EDM) pour retirer les LLIF de la plaque de construction ont augmenté le temps et le coût de production globaux.
Le FormUp 350 : Un Pas en Avant Dans la Fabrication de Dispositifs de Fusion Vertébrale
La machine FormUp 350 PBF s’est imposée comme une alternative supérieure aux plates-formes plus petites équipées de 1 ou 2 lasers. Grâce à une plaque de construction de 350 millimètres carrés, la FormUp 350 peut contenir 1,5 fois plus de grands implants rachidiens que les plates-formes plus petites. L’utilisation de 4 lasers permet d’imprimer 152 grands implants rachidiens en seulement 32 heures, ce qui réduit considérablement le temps de production et augmente le rendement.
Le FormUp 350 utilise une technologie de rouleau de poudre qui permet une complexité géométrique en utilisant des supports minimaux et une finition de surface optimale. Cette technologie permet de réaliser des structures complexes conçues avec soin et d’obtenir une rugosité de surface qui contribue à améliorer les résultats pour les patients. Il n’est plus nécessaire d’avoir recours à un spray poreux au plasma ou à une surface trabéculaire à base de feuilles, et la rugosité de la surface n’est pas un sous-produit du processus. Cela permet de réduire les processus de fabrication nécessaires à la réalisation d’un produit fini, de réduire les coûts tout au long de la chaîne d’approvisionnement et de favoriser des résultats plus efficaces pour les patients.
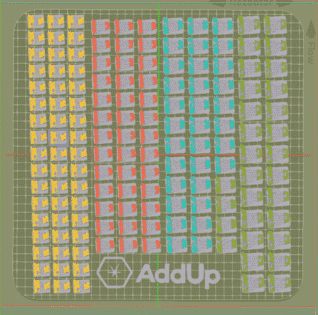
L’impact de FormUp 350 sur L’industrie des Dispositifs Médicaux
L’adoption du FormUp 350 pour la fabrication de grands dispositifs de fusion vertébrale a des implications considérables pour l’industrie des dispositifs médicaux. En réduisant les délais et en augmentant la précision, la FormUp 350 permet aux fabricants de répondre plus rapidement aux demandes du marché et de produire des produits de meilleure qualité. En outre, la capacité d’imprimer des structures complexes et d’obtenir une rugosité de surface optimale améliore les performances des implants, ce qui se traduit par de meilleurs résultats pour les patients. Il s’agit d’une avancée significative, car elle permet non seulement d’améliorer la qualité de vie des patients, mais aussi de réduire le nombre de reprises chirurgicales, ce qui se traduit par des économies tant pour les patients que pour les prestataires de soins de santé.
Résultats
Les implants rachidiens de grande taille produits à l’aide d’une petite capacité de fabrication, d’un faible nombre de lasers et de systèmes de revêtement traditionnels coûtent plus cher que lorsqu’ils sont produits à l’aide de la FormUp 350.
La machine FormUp 350 est idéale pour les applications médicales car elle offre un processus amélioré et rentable pour la fabrication en série de pièces médicales hautement complexes et/ou personnalisées.
Pièces fabriquées par laser sur le FormUp 350 :
- 2 Laser – 76
- 4 Laser – 38
Temps de construction sur la FormUp 350 :
- 2 lasers – 52.95
- 4 lasers – 32,35
Rendement annuel de la FormUp 350 :
- 1 équipe par jour pendant 52 semaines par an
- 1 – 1,5 du laser éteint au laser allumé (retournement de la construction)
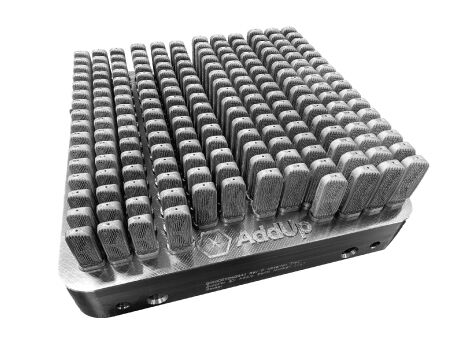