The power of metal additive manufacturing
Metal additive manufacturing, offers the ability to produce complex parts, reduce costs, and address challenges related to complexity, performance, tooling costs, and supply chain.
Metal additive manufacturing is a relatively new technology compared to conventional production methods such as machining, casting, or forging. This does not prevent it from developing at a fast pace: all industrial sectors are interested in this process, whether to solve problems of complexity, performance, tooling costs, or supply chain.
How does additive manufacturing work?
The word “additive manufacturing” refers to a set of processes that have in common the ability to produce parts by adding material (polymer, metal, ceramic, concrete, etc.) from a digital file.
It is unusual for such a young technology to spread so quickly. Metal additive manufacturing, or metal 3D printing, is only 20 years old, and applications are increasing in all sectors, from medical to aeronautics, automotive, defense, energy, space, and tooling. For all these manufacturers, 3D printing metal parts is a way of producing previously impossible parts to manufacture and reducing costs at different stages of the product’s lifecycle.
One principle, several families of technologies
The first 3D printing technologies appeared in the 1980s. They were used to manufacture plastic parts. It was only at the end of the following decade that the first metal 3D printer appeared. Just as there are different technologies for 3D printing plastic parts, several types of machines can be used to manufacture metal parts by adding successive layers of material. The ISO/ASTM 52900 standard defines several families of technologies and here is an Additive Manufacturing Technologies overview:
Powder Bed Fusion (LB-PBF and EB-PBF)
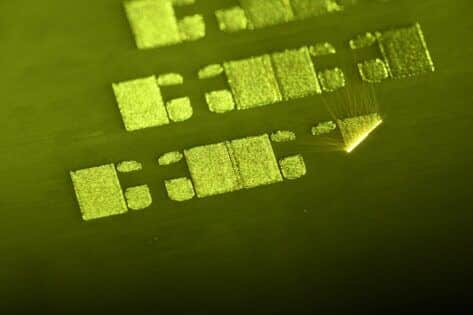
PBF technology
With powder-bed fusion technologies, the parts are manufactured by overlapping horizontal layers. The geometry of the section to be solidified on each layer is defined by a digital file. In the machine, each layer is carried out in two stages. The first is to spread a layer of metal powder on a tray with a spreading device (roller, scraper, or brush), and the second is to melt the metal where necessary. This melting is achieved by the action of a laser or an electron beam. The part is thus constructed by a succession of spreading and fusion cycles.
The acronym LB-PBF (Laser Beam — Powder Bed Fusion) is generally used to refer to the laser powder bed fusion process, and the acronym EB-PBF (Electron Beam — Powder Bed Fusion) to refer to electron beam powder bed fusion.
Advantages
- Ability to make very complex parts
- Parts with high mechanical properties
- Parts with low roughness
- Wide choice of materials
Directed Energy Deposition (DED)
DED technology
Directed energy deposition involves creating a melt pool on a substrate using an energy source (laser beam, plasma, or electric arc) and then feeding the melt pool with a filler material (metal powder or metal wire). This material is brought by a depositing nozzle and passes through the energy beam to approach its melting temperature. This technology is referred to as DED (Directed Energy Deposition), which can be declined as DED-P (Powder) for machines that use metal powder and DED-W (Wire) for machines that use metal wire.
Advantages
- Suitable for the manufacture of large parts
- Allows the addition of material to existing parts (repair or addition of functions)
- Parts with high mechanical properties
- Ability to gradually mix several metals in the same part
- Compatibility with conventional machine tool architectures
Binder Jetting (BJ)
Binder jetting technology is a “powder-bed” method, based on alternating powder spreading and solidification cycles. Unlike powder bed fusion processes, the powder is solidified here by the deposition of a binder. So there is no melting of the metal in the machine. The binder is a polymer-based product that will need to be disposed of during a complementary step called debinding. The latter involves placing the part in a furnace to evaporate the binder while agglomerating the powder particles to each other. This process is commonly referred to as Binder Jetting and is attracting growing interest due to its good productivity.
Advantages
- High productivity
- Total freedom of design (production without supports)
- Parts with low roughness
Material Extrusion (MEX)
MEX is a method directly inspired by plastic filament production, which consists of depositing strands of polymer material loaded with metal particles.
Sheet Lamination (SHL)
The process of sheet lamination consists in making a complex part by assembling layers that are manufactured separately from each other, by conventional techniques (machining, laser cutting, or other). Applied to metal, this process allows for complex injection molds with moving elements or cooling channels that are impossible to manufacture from a block of raw material. This process can be declined in different forms. For example, some machines manufacture parts by successive welding of thin sheets of metal on top of each other.
PBF and DED lead the market
The two most common metal 3D printing processes used by PBF technology represent around 85% of the global metal additive manufacturing market. This dominant position has enabled it to mature more quickly and to continue to attract significant investment. As a result, 3D printer for metal is becoming increasingly productive and high quality, a trend which is expected to continue for many years.
Additive Manufacturing Processes and Materials
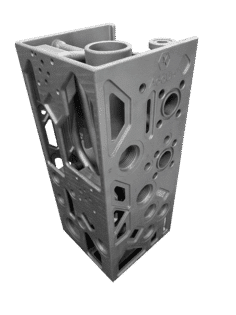
The main reason why PBF technology appeals to manufacturers is that it enables them to make parts that could not be manufactured before. Indeed, the principle of production from thin layers of metal (of the order of 50 microns thick) offers great freedom of design and allows designers to imagine more complex, lighter, higher-performance parts, or to produce single operation parts that are costly to assemble. Moreover, this technology is compatible with a wide variety of materials (Steel, Titanium or Aluminum alloys, superalloys, precious metals, etc.). Finally, the level of control of the melting process that is achieved today by the machines makes it possible to obtain parts with high mechanical specifications. By applying the appropriate heat treatments after the printing process, the materials can have equivalent features to forged parts.
DED technology, the second most widely used family of technology in the world, is complementary to PBF in many ways. Whatever the energy source (a laser, an electric arc, or an electron beam), regardless of the type of raw material (powder or wire), the amount of material deposited at each passage of the tool is 5 to 20 times greater than in PBF. Therefore, the parts are less complex than in PBF, but they are manufactured much faster. And the machines available on the market today offer working enclosures larger than one cubic meter, dimensions that are difficult to achieve with powder bed technologies. Finally, they can be used for applications that are impossible to replicate with most other technologies, such as adding material to an existing part (for repair or coating), creating multi-material parts (composed of layers of different metals, or gradually changing from metal A to metal B).
Let’s identify relevant applications
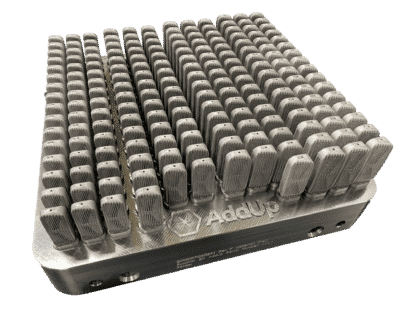
Metal additive manufacturing technologies are expensive. The machines have complex technological building bricks, they require heavy investment in terms of infrastructure and post-processing equipment, and metal powders are more expensive than raw metals. A printed metal part will therefore have a higher cost price than an equivalent part made by machining, casting, or forging. Therefore, metal 3D printing should be reserved for applications that generate value, by identifying gains throughout the product’s life cycle to compensate for the additional manufacturing cost. Fortunately, the list of potential gains is long: mass reduction, raw material savings, optimization of thermal exchanges, increased service life, acceleration of prototyping phases, reduction of assembly times, the addition of functions, improvement of ergonomics, customization of products…
In some cases, it is possible to generate value by printing parts that were previously manufactured by conventional techniques, without the need to modify or optimize the part. This applies to all manufacturers with complex supply chains who wish to reduce transport costs, supply critical spare parts rapidly, or manufacture parts in remote areas. Additive technologies also make it easier to replicate parts for which blueprints are no longer available.
Finally, for all parts that require specific molds or tools, 3D printing can make low-volume production economically viable by eliminating the costs associated with the production of these molds and tools.
Top industries using Additive Manufacturing
Metal additive manufacturing opens new possibilities for design, but the companies that derive the greatest potential from this technology are those that spread the culture of additive manufacturing throughout their departments: R&D, innovation, marketing, industrialization, production, quality Assurance, industrial property… In this way, all these professions will be able to imagine opportunities to generate value thanks to metal 3D printing. Of course, it will be necessary to be able to analyze the feasibility of all the ideas that are generated. Indeed, contrary to popular belief, additive manufacturing is not a way to free yourself from all design limitations. Of course, it allows us to free ourselves from certain constraints specific to subtractive technologies, but it is accompanied by numerous new constraints (considering the gravity and thermal effects on manufacturing, for example). Moreover, each process family has its requirements, which must be known to be able to choose the best available technology for an application.
Advantage of Additive Manufacturing: Mastering the value chain
Created in 2016 on the initiative of Michelin and Fives, two major French industrial groups, AddUp offers a range of technologies and services that is unprecedented in the metal additive manufacturing market. From a technology point of view, first, by offering a range of L-PBF and DED machines. In addition to being the most used, these two processes are perfectly complementary in terms of applications. In terms of services, AddUp stands out for its choice to propose the production of parts in addition to machine sales. This part of manufacturing activity enables us to respond to industrialists whose applications cannot justify the investment in a machine, but not only. It allows manufacturers to be supported at all stages of their projects, from the design stage (with redesign assistance services, for example), to the delivery of finished parts, since AddUp disposes internally of the know-how to ensure the finishing of parts. Finally, by mastering both machine construction and parts manufacturing, AddUp can accompany its Industrial customers in the qualification of their applications and can even propose a new kind of supply chain, with, for example, the possibility for customers to reserve capacity in AddUp workshops to support a ramp-up or absorb possible variations in demand.
AddUp is an industrial company created to meet the expectations of industrial companies. Quality, productivity, repeatability, and reproducibility are at the heart of our concerns, whether for the design of our machines or the production of your parts. Above all, our experts are here to help you integrate additive manufacturing into your business and can assist you in the qualification processes of your projects. Visit our website to learn more about metal additive manufacturing: https://addupsolutions.com/
HISTORY of Additive Manufacturing
The 1st patent on 3D printing (known as “additive manufacturing”) was filed on July 16, 1984. The dealers are French: Jean-Claude André, Olivier de Witte, and Alain le Méhauté for the company CILAS ALCATEL. The same year, in the United States, on August 1, 1984, it was the American Chuck Hull who filed the patent on the stereolithography 3D printing technique. Then the extension of the printing file “.stl” will be created, and the company 3D Systems, a manufacturer of 3D printers. In 1995, the metal 3D printing technology or DMLS (Direct Metal Laser Sintering) appeared. The technology is adapted to metal, with an even more powerful laser.
Read more about additive manufacturing history.