Revolutionizing Aerospace & Defense Through 3D Printing
Additive manufacturing offers clear benefits to the aerospace industry including improved design, reduced weight via topological optimization, enhanced performance, and more efficient production processes. Aerospace components often require intricate and complex shapes that are difficult or impossible to achieve using traditional manufacturing methods. AM allows the creation of highly intricate structures, such as generative designs for lightweighting, that can optimize aerodynamics and thermal management.
The defense sector can face supply chain disruptions due to geopolitical issues or emergencies. AM reduces lead times by eliminating the need for some tooling and enabling on-demand production. AM also offers the unique ability to produce critical components on-site or near the point of use, reducing dependence on external suppliers.
Better Surface Finish. Better Performance.
Aerodynamic efficiency and optimal thermal transfer between a source and fluid are key benefits additive manufacturing provides to applications in the aerospace industry. The FormUp 350 is capable of using a finer particle PSD and this coupled with our roller recoater technology allows for design complexity while achieving best-in-class surface finish, as printed. This is important for aerospace applications because the smooth finish facilitates and optimizes airflow, thereby maximizing heat transfer efficiency. Optimal surface finish also important because reduces surface irregularities, such as roughness, burrs, or surface defect, improving the fatigue strength and thermal integrity for many aerospace applications.
Topological optimization is often used to aid in weight reduction for aerospace applications. AddUp is experienced in optimizing parts for AM using this process. Additionally, AddUp’s technology allows for extreme overhang geometry while limiting the number of support structures needed. This greatly reduces post-processing required for support removal and subsequently overall production time.
In aerospace, manufacturers are constrained by rigorous qualification requirements. Safety and reliability are paramount, even the smallest details can have significant impact and dramatic consequences. AddUp is the experienced partner manufacturers can count on. Our experts are knowledgeable on qualifications and certifications required for the aerospace industry and can speed up the process of qualifying your part applications with our certified facilities. The AddUp suite of in-process monitoring software directly answers the needs of the aerospace industry by providing confidence in part quality through every stage of the manufacturing process.
Superior Surface Finish
Our fine powder and roller recoater system allows for parts to be designed with thin walls, fine feature resolution, and a superior, smooth surface finish as low as 4um Ra, as printed. This optimizes airflow and maximizes heat transfer efficiency.
Better Performance
AddUp’s machines can create aerospace parts with more intricate designs and tighter tolerances. This optimizes weight savings without compromising structural integrity, improving fuel efficiency and enhancing overall performance.
Improved Reliability
The careful control and optimization of surface finish in fluidic aerospace applications pave the way for safer, more efficient, and more reliable aircraft and propulsion systems, ultimately advancing the capabilities and success of the aerospace industry.
Quality Assurance
In-process monitoring gives our users peace of mind and real-time quality assurance, providing confidence in part quality, build-to-build and part-to-part.
Greater Productivity
AddUp’s additive manufacturing machines were designed to meet an OEE level demanded for serial production with maximum throughput.
Safety as a Priority
Safety is AddUp’s top priority and our machines are manufactured with their users in mind. Every component of our machines were designed to protect our most important asset, people.
Key Applications in Aerospace & Defense
AddUp has expertise and experience optimizing aerospace applications to maximize performance while being safer and more reliable to meet the needs of such a highly regulated industry. Utilizing a fine powder with a roller recoater for controlled and uniform powder deposition, the FormUp 350 can achieve superior surface finishes to maximize heat transfer, improve engine performance, enhance fuel efficiency, reduce drag, and ensure the longevity and reliability of critical components.
As an expert of two different additive technologies, AddUp has the unique ability to optimize aerospace applications using both Powder Bed Fusion (PBF) and Directed Energy Deposition (DED). Where PBF is ideal for heat exchangers with thin walls and fine features, DED is ideal for larger scale propulsion components such as rocket nozzles.
Heat Exchangers
A key application in the aerospace industry, a heat exchanger is a device designed to transfer heat between two or more fluids that are at different temperatures. Best-in-class surface finish as printed, as low as 4um Ra, and fine feature resolution <200um from the FormUp 350 facilitates and optimizes airflow and maximizing heat transfer efficiency.
Impellers and Blades
Impellers are rotating components designed to increase or decrease the flow and pressure of a fluid in an engine. They are excellent applications for additive manufacturing thanks to the ability to create highly complex and customized blade designs to improve fluid dynamics, performance and efficiency. A smooth surface is essential for optimal performance in these applications. Superior surface finish from the FormUp 350 minimizes turbulence, pressure losses, and energy wastage. This enables optimal gas flow, which translates into improved engine power, fuel efficiency, and overall performance.
Propulsion Components
A propulsion component, such as a rocket nozzle, is used to generate thrust and propel an object forward. These types of applications require a performance material to ensure durability and longevity. AddUp’s DED technology is ideal for manufacturing propulsion components because it allows for the creation of near-net shapes with optimized geometry on a large scale. AddUp DED machines come equipped with house-designed nozzles for better meltpool control and precision.
Satellite and Antenna Supports
Traditional manufacturing methods like CNC machining have limitations in achieving intricate and lightweight designs without sacrificing structural rigidity. AM allows for design freedom, crucial for optimizing satellite components to meet specific performance, weight, and size requirements. AddUp’s fine powder and roller recoater allow for design complexity while achieving best-in-class surface finish, as printed, and limiting the number of supports required.
Pumps and Turbomachinery
Pumps are used to transfer fluids from one location to another by increasing the fluid’s pressure and flow rate. Additive manufacturing offers numerous advantages for turbomachinery including design flexibility and improved performance. Some of these applications require complex assemblies which can be consolidated into a single component using AM, reducing overall production costs. AM is also used for these types of applications to optimize internal structures leading to more efficient parts requiring less energy consumption.
Manifolds
A manifold is a component used for industrial applications to distribute, collect, or control the flow of fluids, gases, or other substances. Additive manufacturing allows for lightweight yet strong designs to optimize performance for these applications. AM also enables the integration of functional features directly into the manifold, such as valves, sensors, connectors, and brackets. This reduces the need for additional assembly steps and potential points of failure.
Metal Additive Manufacturing Applications
The use cases for Additive Manufacturing are varied across different industries. See how AddUp customers have had success using our PBF and DED technologies.
Aircraft Floor Bracket
This proof of concept demonstrated by Add Up showcases the value of using Additive Manufacturing (AM) for aeronautics by applying topological optimization to an aircraft floor bracket. History An aircraft floor bracket…
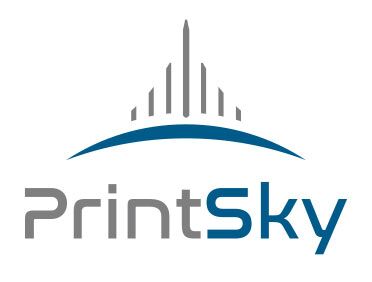
Heat Exchanger
Read the case study to understand how to obtain a viable heat exchanger with good thermal and mechanical properties in a reduced time frame. AddUp and PrintSky join forces to increase…
Rocket Nozzle
AddUp optimized the design of a rocket nozzle to improve the performance of a micro-launch vehicle. Metal additive manufacturing can lead to fuel and production savings in aerospace. In this case…
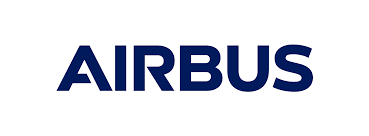
ADS Spherical Tank
AddUp 3D printed a spherical tank that can hold the operating pressure of 60 bar for two-phase fluid loop applications using fluids in a supercritical state at maximum non-operating system…
Aerospace Support Part
See how AddUp and PrintSky develop a good rigidity/mass balance with a high technical and economic value for an aeronautical part. The CEA (French Alternative Energies and Atomic Energy Commission) has joined forces…
Échangeur de chaleur FormUp
Optimiser le flux d’évacuation des fumées de fusion. Le projet de réalisation d’un échangeur thermique pour la machine FormUp® 350 est né de la volonté de profiter du savoir-faire développé par PrintSky, une société commune créée par AddUp, fabricant de machines d’impression 3D métallique, et Sogéclair, fournisseur de solutions innovantes pour une mobilité plus sobre et plus sûre. Il s’agissait d’évaluer l’intérêt d’une solution optimisée en fabrication additive en la comparant avec le système actuel, produit par des méthodes conventionnelles.
TOOLING
Heat Exchanger Aluminum AlSi7Mg
The goal is to demonstrate an interest in the PBF technology to create heat exchangers with improved compactness, good thermal performance, and metal 3D printed in one go. Answering the aerospace…
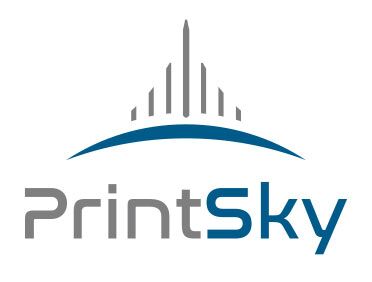
HEWAM Heat Exchanger (Inconel)
Addup 3D printed a double-curved heat exchanger, suitable for curved surfaces with very successful thermal performance and produced in one go. For thermal equipment, additive manufacturing has a huge advantage. It…
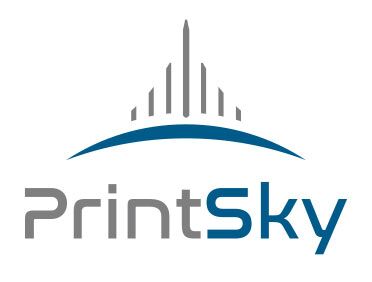
Joystick
The freedom of design linked to metal 3D printing allows the production of customized handles, of different dimensions, without tooling, thus limiting the costs and manufacturing lead times of the…
Space Camera Support
An additively manufactured camera support, designed to withstand acceleration and vibration during launch to space and to hold a camera and its lens in position during the production phases of…
“AddUp has demonstrated a set of capabilities that enable us to address unique design and application challenges faced by our growing base of aerospace, space, and defense customers.”
Greg Morris
Materials used in Aerospace & Defense
Some aerospace applications require a performance material that ensures durability and longevity. For other applications, it’s important to have a material that is lightweight but still high performing.
AlSi7Mg0.6
AlSi7Mg0.6 is a lightweight material commonly used in aerospace and industrial applications. Its low weight combined with design benefits of using additive manufacturing (i.e. increased geometric complexities and topology optimization) can greatly increase the range of use applications.
AlSi10Mg
AlSi10Mg is a Al-Si based alloy with good mechanical properties and thermal conductivity. It is a suitable materials for applications requiring low weight, high strength and load bearing components. It is widely used in the aerospace and automotive industries.
Inconel 718
Inconel 718 is a Ni-based alloy commonly used for high-temperature applications. Typically, its operating range is 650°C to 700°C where its high yield strength combined with a good creep vs. fatigue resistance ratio allows for an extremely versatile alloy suitable for a variety of applications.
Titanium Ti64
Ti6-4 is commonly used for aerospace applications thanks to its good mechanical properties and strength (UTS/density).
316L Stainless Steel
316L is a stainless steel well-suited for fluid transfer applications because it has good corrosion resistance allowing for long service life.
INDUSTRIAL MACHINES
With more than 20 years experience in Additive Manufacturing, our machines have been designed to master detail and optimize productivity.
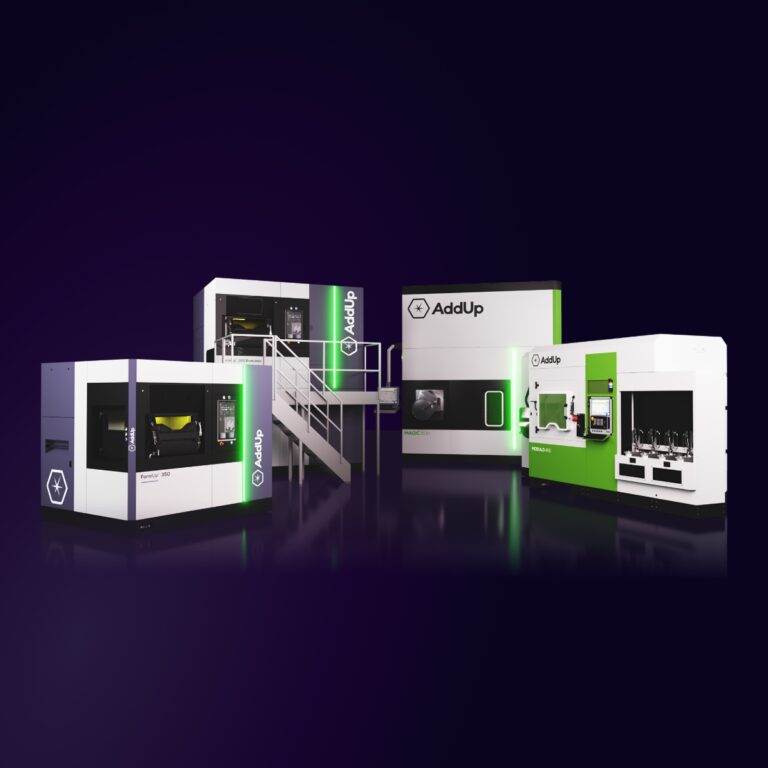
SMART SOFTWARE
Within the aerospace industry, the qualification and regulation of critical components is mandatory. AddUp is leading the way with in-process monitoring, providing confidence part quality with a full suite of quality assurance monitoring software to lessen, or even eliminate, the need for rigorous testing after a part is printed. From part preparation to simulation, monitoring, and production, every link of the AddUp digital chain offers a high level of performance with user-friendly software.
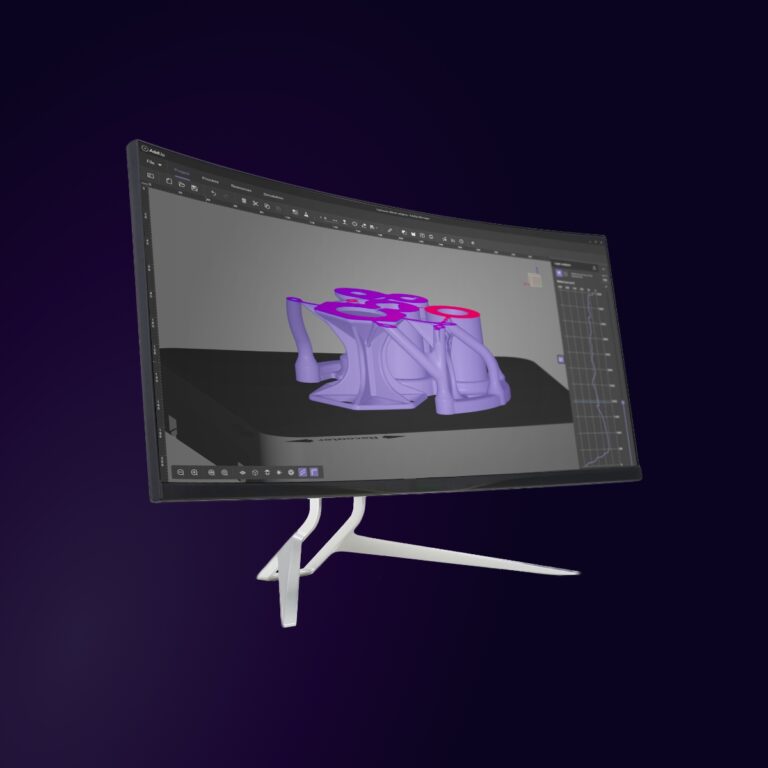
Get Started with AddUp
Realize the potential digital manufacturing has to offer. Get started with AddUp and learn how AM delivers innovative solutions to solve manufacturers toughest challenges.
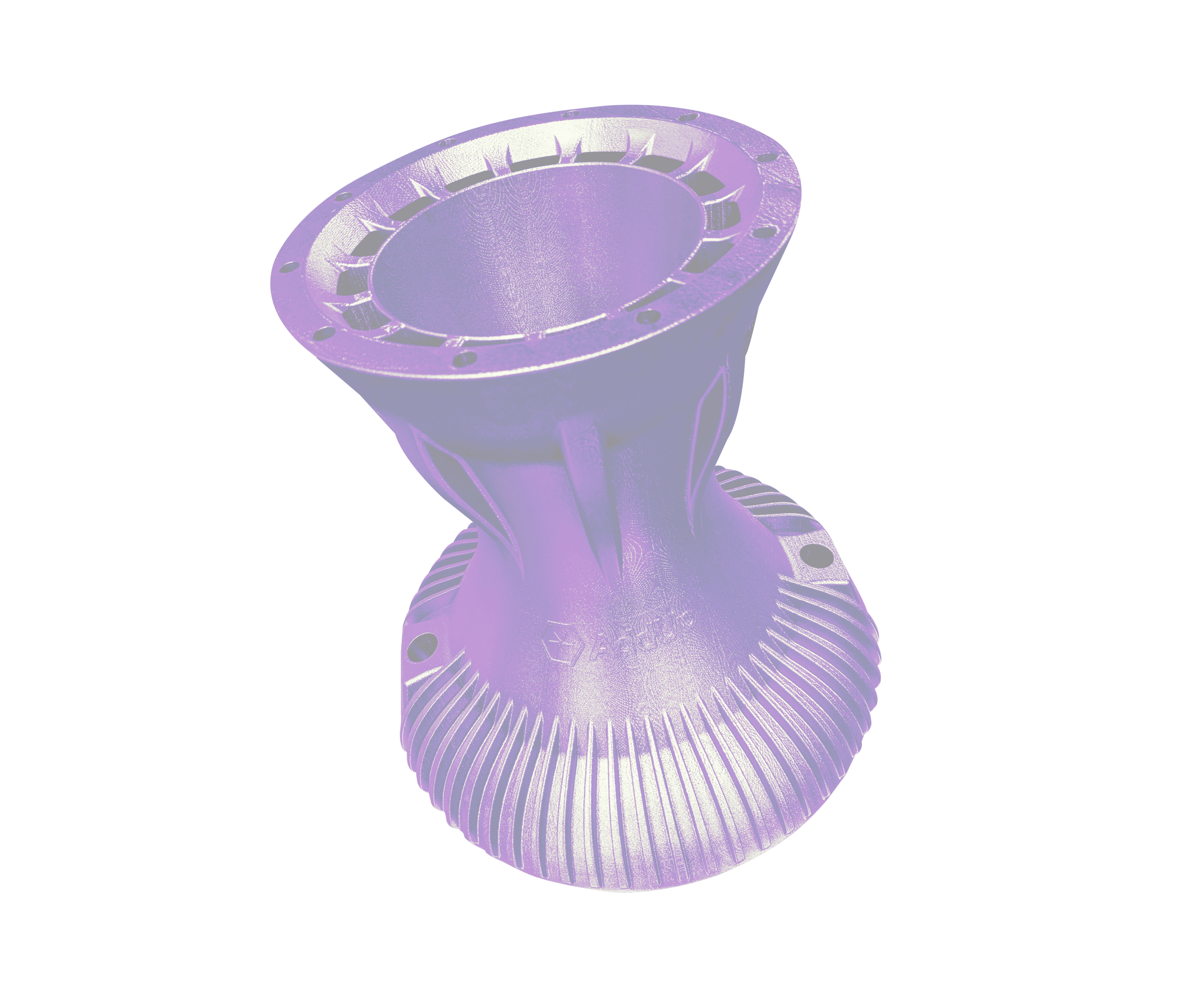