Additive manufacturing, or 3D printing, has become an essential tool for the military, offering cost and time savings, improved supply chain performance, and enhanced operational readiness.
With its promise to reduce costs and lead times while improving product and supply chain performance, the military has been using additive manufacturing for several years now. The most common applications in the military sector are prototyping, parts manufacturing, tooling and repair.
Whether for manufacturing or repairing equipment, 3D printing has repeatedly proven to be a suitable production method for military forces. Now, additive technology offers even more efficient ways to produce spare parts on demand, improving manufacturing times and supply flows.
In external operations the ability of equipment to last, or its autonomy more generally, are properties and qualities particularly sought after by forces for operational engagement or stationing. Several efforts are being made in this direction, such as reducing logistical flows, which are sources of vulnerability, to limit the exposure of men to threats while reinforcing the autonomy of deployed forces.
How can 3D printing help to maintain the operational readiness of equipment at a level sufficient to ensure the continuity of operations and essential missions?
For operational support to deployed units, the army depends on two major capabilities: repair capacity and spare parts supply capacity. For these two means, 3D printing represents an important interest allowing to gain in autonomy and especially in reactivity.
The use of additive manufacturing is intended to enhance and accelerate repair and supply capabilities down to the tactical support echelons. There are many potential applications such as restoring the usability of a vehicle, by producing new replacement parts or to reduce the logistical flows linked to supply stocks, particularly during an operation.
It is even possible to compensate for a possible shortage of stock or a large consumption of spare parts, for example, in the event of intense military involvement. Another important advantage is that additive manufacturing also makes it possible to produce parts that would no longer be manufactured for various reasons: loss of technical control, obsolescence, no longer being supplied or lack of raw materials, etc. New, lighter parts with complex geometries, printed in 3D, benefit from very good solidity and therefore durability properties because they are made from innovative materials. The equipment will therefore be less heavy to carry and will have a longer lifespan. For example, the production of lattice structure parts makes it possible to lighten a mechanical system while maintaining or even improving its strength.
In short, metal 3D printing can be used to reproduce existing parts for repairing equipment, as well as to create new, optimized parts that provide added operational value. Additive manufacturing improves supply chain responsiveness and reduces inventory, obsolescence risks and overall costs.
Producing as close to operations as possible
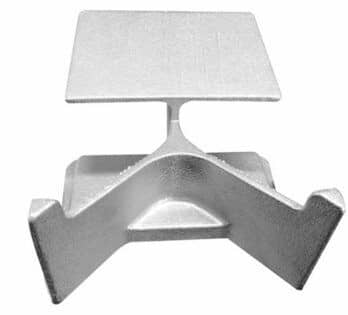
The constant need of the military for maintenance and repair parts for heavy equipment during missions leads to very high costs. The possibility of printing the necessary parts quickly and close to the action allows considerable savings in time and production costs.
AddUp responds to this recurrent need of defense industry: to manufacture spare parts and tools directly on the battlefield.
In the context of military operations, additive manufacturing allows the deployment of small batches of large platforms that are easily accessible to the armed services. These ‘mobile labs’ accessible at operational bases are ideal for quickly manufacturing spare parts or adapting equipment for the nearby battlefield.
Read about a Case Study from the French Navy utilizing AddUp’s FormUp 350.
Produce anywhere…
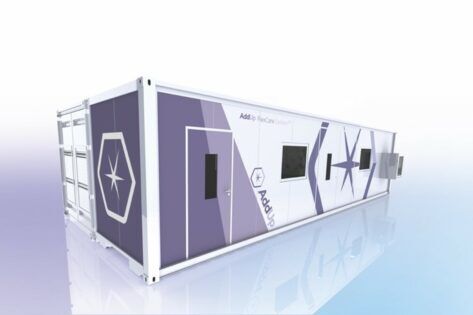
AddUp is the first metal 3D printing machine manufacturer to offer transportable additive manufacturing units. With The AddUp Flex Care System TM, parts can be produced on demand close to your operations. These self-powered units can operate in the most remote areas and harshest environments. They incorporate one or more additive manufacturing machines as well as post-processing machines to provide finished parts for immediate use. Self-sufficiency is undoubtedly a tactical advantage in military operations as it reduces logistical costs and vulnerability to attack from the opposing side.
In post-conflict, disaster support or reconstruction situations, additive manufacturing can help local communities by facilitating the repair and maintenance of strategic equipment.
Conclusion
The defense sector uses additive manufacturing technologies in many ways: different processes, different materials, means of production, etc. There are many applications such as vehicle maintenance, repair of parts, production of new high-performance and optimized parts and integrating new functionalities. The military uses additive manufacturing from research to the deployment phase, with the development of prototypes, tools and functional parts.