This innovative design is tailored for curved surfaces and has demonstrated exceptional thermal performance. The entire heat exchanger was produced in a single manufacturing process, showcasing the efficiency and capability of AddUp’s approach.

For thermal equipment, additive manufacturing has a huge advantage. It allows the development of complex channel shapes, improving thermal performance and reducing volume. It also allows the manufacturing of shapes that are impossible to produce traditionally for this type of equipment (e.g. double-curved channels).
INDUSTRY
Aeronautics
CHALLENGE
3D print a heat exchanger with innovative design
KEY BENEFITS
- Modular heat exchanger concept
- A double-curved heat exchanger
- Part printed in one go with thin walls
- When damaged, replacement of the unit instead of the whole arrangement
Custom Shape
Assembly
Thin Walls
Performance
History
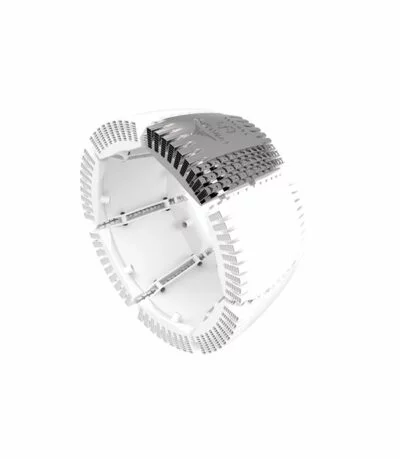
A heat exchanger is a system used to transfer heat between a source and a working fluid. Heat exchangers are used in both cooling and heating processes. Depending on the application, the fluids may be separated to prevent mixing or they could also be in direct contact. In the aeronautics industry, aircraft heat exchangers are used to take heat from the engine’s oil system to heat cold fuel. This improves fuel efficiency and also reduces the possibility of water becoming entrapped in the fuel, which could cause freezing.
Heat Exchanger With Additive Manufacturing or HEWAM is a project aiming to develop a heat exchanger using all the potential of additive manufacturing in a geometry that fits with a wide range of surfaces and volumes used in the aerospace industry. This project was developed by PrintSky and Temisth. PrintSky is a joint-venture between the AddUp group, an expert in metal additive manufacturing, and SOGECLAIR, one of the international leaders in the integration of high-value-added solutions in the fields of aeronautics, space, civil and military transport. Temisth is a company specializing in the development of customized thermal solutions using additive manufacturing.
PrintSky was in charge of the design aspect of the project, developing its own methodology to determine the characteristics of the metal part, in terms of mechanical, thermal, and manufacturability.
The production was then passed to the AddUp experts who 3D printed this aeronautical part on their FormUp® 350 machine. The goal was to produce a compact heat exchanger according to the PBF (Laser Powder Bed Fusion) process with an innovative shape and above all as efficient as “traditionally“ manufactured heat exchangers. And then, after the production, HEWAM was tested on a customized test loop developed by Temisth.
Challenges
The objective for HEWAM was to cool a liquid as oil entering the heat exchanger at 110°C with ambient air at -50°C. The mass flow rate of the oil is fixed. Air mass flow rate is given by the dynamic pressure of the air flow arriving in the area of the heat exchanger and the pressure drop characteristics of the device. The objective was to remove 2200W of the oil circulation (32g/s ~2,4 L/min) on one modulus of the heat exchanger by ensuring enough air flow through it. The main physical issue on this heat exchanger was to ensure enough airflow inside the heat exchanger with high heat transfer coefficient.
SOLUTIONS
The groups developed a specific methodology in order to ensure the thermal requirements with mechanical constraints and additive manufacturing feasibility for HEWAM. A specific design was created taking into account the variation of air temperature (from -50°C up to +25°C) and thus its density. The channel width was increased to limit air acceleration and pressure drop. In order to maintain thermal performances, the fins have an adaptative geometry along the air flow in order to consider air velocity and channel size changes. The physical design of the part was created to fit a wide range of surfaces and volume used in the aerospace industry. It was designed to include a double shape curve which allows this part to fit the curvature of aircraft engines.
HEWAM was printed twice, using two different materials. First, Inconel 718. This material is heavier than aluminum by more than 3 times and is less conductive, however for additive manufacturing, it presents more interesting characteristics. With Inconel, thin walls (<0.5mm) and fins (0.15mm) are possible without leakage. Designing the heat exchanger with these thin features allows for similar performance and weigh characteristics which are possible with aluminum.
A final advantage of this 3D printed part is the possibility of updating the exchanger with no need to develop a new tooling.
Results
The final result is a double-curved heat exchanger, suitable for curved surfaces with very successful thermal performance and printed in one go. A modular solution: exchangers can be arranged next to each other in order to deliver high exchange power. The curved shape is suitable for installation in aircrafts engine pylons. The testing validated the leakage (or tightness) of the part as well as its performance, both of which were very successful especially when compared with more conventional means of manufacturing.
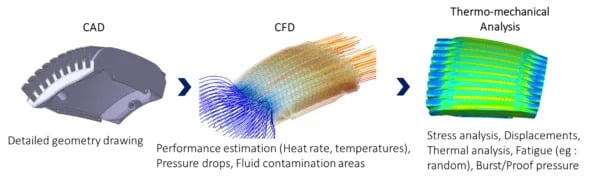
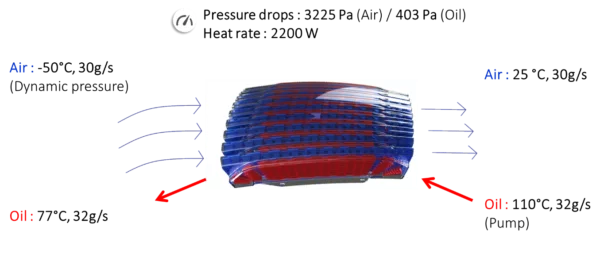
The testing validated the leakage (or tightness) of the part as well as its performance, both of which were very successful especially when compared with more conventional means of manufacturing.
For thermal equipment, AM has a huge advantage. It allows the development of complex channel shapes, improving thermal performance and reducing volume.
The AM process also offers the ability to manufacture shapes that are impossible to produce traditionally for this type of equipment (e.g. double-curved channels).
In addition, additive manufacturing technology also allows the Manufacture of a part from a single block, in one go. This avoids any other manipulation of the part that could alter it, such as assembly or machining. No welding either, which means no risk of fluid leakage in this new heat exchanger.
Lastly, because AM offers the ability to print in one piece, only the functional areas of the metal part are printed (fluid flow surfaces and fastening surfaces), resulting in significant material savings.
Read more about this part on the Temsith website
Temsith Site