Metal additive manufacturing, specifically laser powder bed fusion (L-PBF) technology, offers new possibilities for the molding and tooling sectors. It enables the production of molds with complex geometries, interlocking parts, and conformal cooling channels, leading to improved productivity, reduced cooling times, and enhanced part quality.
Manufacturers in the molding and tooling sectors are now making extensive use of 3D printing. They use plastic 3D printing to make prototype injection or lost-wax molds, 3D sand printing to make inserts, or stack multiple mold layers to make stack molds. Metal additive manufacturing, on the other hand, is developing less rapidly. However, laser powder bed fusion (L-PBF) technology has several interesting advantages for these sectors.
New applications in the field of injection molding
PBF technology offers several ways to improve the injection molding process. First, the ability of the L-PBF process to produce parts with complex geometries makes it possible to consider new shapes. The walls of the mold that make contact with the plastic part have the possibility to gain complexity but are limited for two reasons; the need to access the surfaces with machining and polishing tools to reduce their roughness and the need to respect draft angles as the mold shapes must allow the part to be unmolded.
Nevertheless, there are still avenues to explore. As L-PBF technology allows for the manufacture of interlocking parts, mold designers can imagine new types of movement within their molds, by placing “drawers” (moving parts) in areas previously impossible to reach with conventional techniques. Reliability can also be improved. Elements assembled by welding or screwing are generally the weak points of molds used in large series, and metal 3D printing offers the prospect of making them in a single operation, and thus improving their lifetime.
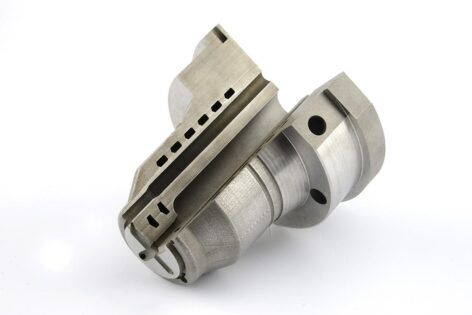
Manufacturers considering the use of metal additive manufacturing to produce injection molds should bear in mind that PBF technology is not well suited to the production of massive parts, for reasons of cost but also because of the accumulation of thermal stresses. It should therefore be avoided to produce complete molds, and its use should be limited to areas where it is of interest.
This constraint, which might seem to be a brake on the deployment of this technology in molds, offers interesting prospects. Designing molds in which the solid part is standard and the section close to the molding wall is printed has advantages. Firstly, it is the possibility of carrying out quicker changes of series, as the lead times for obtaining the molds are generally several months. Secondly, it is the opportunity to reduce downtime, as the storage of printed parts is less than the storage of complete molds. Finally, it is the prospect of envisioning small series production which would not have been profitable in view of the investment in a complete mold. Or, in the long term, to move towards the manufacture of customized products, a world that is currently difficult to access for plastic injection parts.
Productivity and quality gains
Before thinking about using metal 3D printing to develop new products and services, it can be useful to use it to improve what already exists. One of the key applications of L-PBF technology in the world of injection molding is a technique called “conformal cooling”. It consists of optimizing the cooling time of plastic parts in injection molds by creating channels that follow the shape of the part to be cooled. These channels are placed as close as possible to the molding wall and make it possible to reduce cooling times, therefore increasing production rates. In an injection cycle, the material cooling stage is generally the longest. It is by reducing this time that the greatest productivity gains can be obtained. Gains can also be made on the appearance of the injected parts, as placing channels in areas that are usually difficult to cool helps to avoid shrinkage or weld lines, which are problems caused by non-optimal cooling.
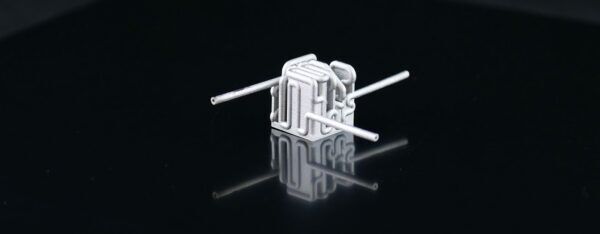
While injection molding engineers have always been able to design complex control circuits, they have been limited by the mold making techniques. For a long time, the only techniques available to create pipes in a block of metal were drilling, machining, and layering (the mold is designed in separate layers, each of which is milled and drilled so that the layers are joined together to create three-dimensional pipes). Today, with the techniques of additive manufacturing by laser fusion on powder bed, mold manufacturers have access to a total freedom of design for their regulation channels. It should be noted that the surface conditions of the parts produced by laser fusion on powder bed are particularly adapted to the creation of cooling channels: smooth enough not to generate turbulences in the channels, but rough enough to increase the exchange surface compared to channels made by drilling.
Another advantage of conformal cooling is that by placing control channels as close as possible to the mold cavity, the total volume of metal to be cooled is reduced. This allows the mold to reach its operating temperature more quickly and reduces the time from machine start-up to the first good part being produced, leading to productivity gains and a minimizes the number of defective parts.
Production support tools
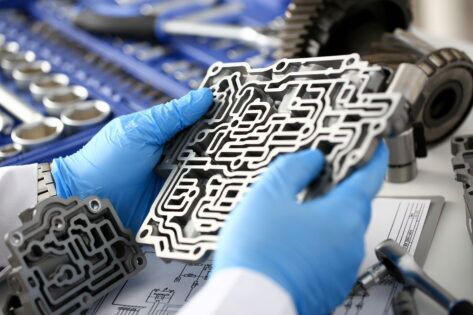
Whatever the reasons for a manufacturer’s interest in 3D printing, it is always the case that the experience gained from one project gives rise to other ideas, sometimes in other departments of the company. Significant gains can be generated if we look beyond the products sold to customers and the molds needed to manufacture them by considering the production tool. In any production workshop, there are a multitude of tasks that can be simplified, improved, or secured thanks to custom-made tools. From jigs that facilitate assembly operations, through lightweight hand tools with handles adapted to the hand of each operator, to coded tools that avoid errors during assembly… Additive manufacturing offers many ways to reduce production times, improve product quality, or reduce the risk of MSDs (musculoskeletal disorders).
The same is true for manufacturers who use robots or operate automated assembly lines: whenever a moving part can be lightened, this leads to less vibration, less wear and tear, lower energy consumption, and reduced production times. Additive manufacturing provides answers to these lightweight applications by creating recesses within volumes, creating lightweight structures (lattice structures) or utilizing topological optimization.
To develop all these “indirect” applications of additive manufacturing, and to use it to make “tools” in the broadest sense of the term, a good practice is to encourage all operators and technicians to share the culture of additive manufacturing in the company, not only in the design offices, so that all employees are able to propose ideas for improving the production tool.
Conclusion
The applications of metal additive manufacturing in the field of tooling should continue to develop in the years to come, especially as progress is being made every day on productivity, process control and the development of recipes for metals traditionally used by manufacturers in the sector. These applications will be very varied, as they may concern industrialization times, part quality, production rates, fixed assets and the services provided to customers.
TOOLING AND INJECTION