In June 2020, the French government launched a support plan for the aeronautics industry to help manufacturers in the sector overcome the consequences of the health crisis and encourage them to accelerate the reduction of the carbon footprint of their activities. (Plan de soutien à la filière aéronautique) 1.5 billion euros will be made available over the next three years to support research and development projects in this field.
3D printing and aeronautics: towards “cleaner” aircraft
Three main levers have been identified to move towards “cleaner” aircraft:
- reduction of fuel consumption
- the electrification of appliances
- the transition to carbon-neutral fuels such as hydrogen
In these three areas, 3D printing can provide answers to manufacturers who wish to overcome the performance limits of equipment made by conventional techniques.
The aerospace industry was interested in additive manufacturing (3D printing) from an early stage and has been using it for decades. It was first used to manufacture prototypes to shorten the development time of new aircraft. Then, in the race to make aircraft lighter, aircraft manufacturers began to print functional parts. Today, critical parts (e.g. engine parts) and even structural parts made by various 3D printing processes can be found on board aircraft.
According to a report by Market Research Future, the number of companies and suppliers certified for additive manufacturing in the aerospace industry is expected to grow by more than 20% per year until 2023. The AddUp group is one of these suppliers capable of meeting the requirements of the aerospace industry: our production workshop based in Salon-de-Provence (Bouches-du-Rhône, France) is certified NF EN 2100: 2018.
DED and L-PBF, two complementary technologies
Our range of machines are also suitable for aerospace applications. For example, DED technology is suitable for the repair of worn parts and is used for the refurbishment of aircraft engine parts. It can also be used to produce large parts, such as nozzles or complex tubing, at a lower cost than machining from scratch and with improved repeatability compared to boiler making.
Laser-Powder Bed Fusion (L-PBF) technology is used for the manufacture of smaller parts, but with great freedom of shape. This allows engineers to consider performance gains in many areas, such as weight reduction, improved fluid flow, and optimized heat exchange.
The following two recent application cases from the aeronautical sector illustrate the type of gains made possible by this technology.
A hydraulic manifold designed for 3D printing
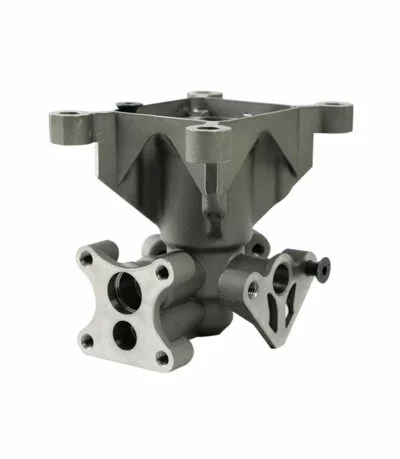
Recently, the Airbus group worked with AddUp and Hall32, a center for the promotion of industrial trades, on the optimization of a hydraulic manifold using metal additive manufacturing. The original part is a fluid manifold, traditionally machined from a titanium block. Thanks to the technique of topological optimization, AddUp and Hall32 managed to reduce the mass of the part by 85%, while improving the flow of fluids.
The project did not stop there! The part required a large quantity of supports to be manufactured, which implied time spent in printing (time spent manufacturing the supports) and machining (time spent removing the supports). The AddUp and Hall32 engineers therefore carried out a second optimization pass to consider the constraints linked to the process (this is called DfAM, for Design for Additive Manufacturing). In its final version, the fluid manifold is printed in 30 hours, compared to 52 hours in its first version, and the machining time has been reduced by 6 hours.
An innovative heat exchanger
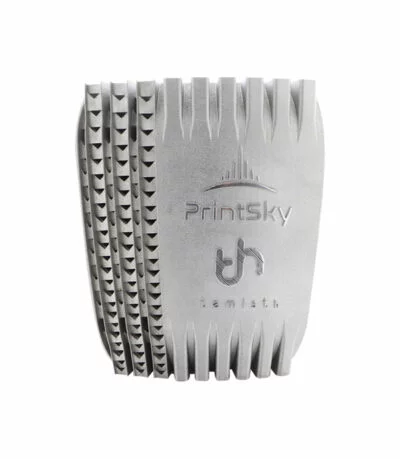
HEWAM is a heat exchanger concept developed by Printsky and Temisth. PrintSky is a joint venture between the AddUp group, an expert in metal additive manufacturing, and Sogéclair, one of the international leaders in the integration of high value-added solutions in the fields of aeronautics, space, civil and military transport. Temisth is a company specializing in the development of customized thermal solutions using additive manufacturing. The objective of the HEWAM project was to demonstrate the ability of both partners to design and manufacture an innovative heat exchanger using the PBF process.
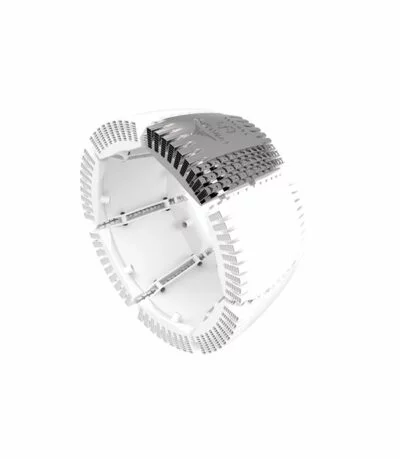
The production was entrusted to AddUp who 3D printed this aeronautical part on a FormUp 350 machine. AddUp’s experts used a fine-grained Inconel® 718 powder to produce thin walls with good surface finish, and thus achieve high thermal performance. These thin walls (150 µm) form channels with a complex geometry, which allows HEWAM to present a high heat exchange capacity in a reduced space.
Beyond performance, HEWAM also offers a new way of managing heat dissipation on board aircraft. This dissipation management is primarily thanks to its modular design. Several heat exchangers can be placed next to each other to deliver the thermal power required for the application. Furthermore, its curved shape allows HEWAM to be installed in the engine pylons while leaving space in the center for the cables needed to operate the engines. Its performance/space ratio and modularity make HEWAM an interesting alternative for aircraft manufacturers interested in optimizing heat exchange on board their aircraft.
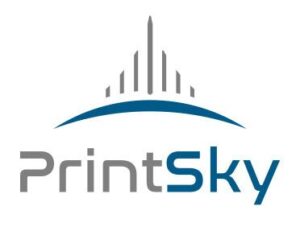
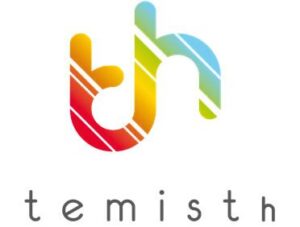
Other benefits of metal 3D printing
A functional system that used to require the assembly of several small parts can now be 3D printed in a single production run. No more assembly or welding is required, and the risk of breakage in mid-air is reduced. The use of certified materials also ensures that the printed parts are ready to use and able to withstand the rigors of a real-world application.
To prevent aircraft from being grounded, stocks of spare parts have always been provided. However, many of these parts are unused or even obsolete. 3D printing makes it possible to alleviate some of this problem by creating spare parts on demand, depending on the need and where they are needed.
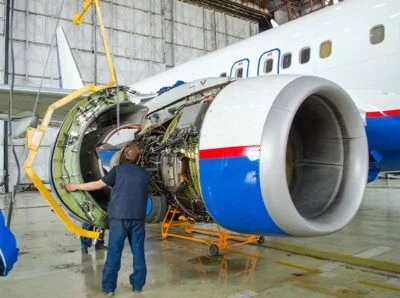
Metal 3D printing seems to have many advantages to allow the aeronautical industry to regain its momentum
From the integration of metal parts with complex geometries, to the reduction of aircraft weight using lightweight metals to save fuel, there are many benefits of additive manufacturing to meet the financial and environmental objectives of the aerospace industry.
By introducing Additive Manufacturing into production, topological optimization, low-cost complexity, fewer parts, lower inventories, and the entire value chain of the aeronautical sector will undergo a real evolution.
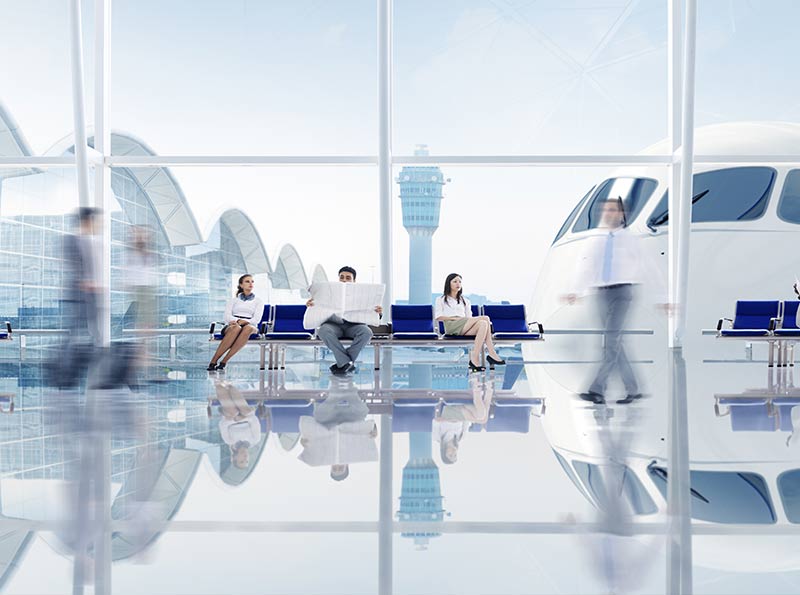