Die additive Fertigung bzw. der 3D-Druck ist für das Militär zu einem unverzichtbaren Werkzeug geworden, das Kosten- und Zeiteinsparungen, eine bessere Leistung der Lieferkette und eine höhere Einsatzbereitschaft ermöglicht.
Mit dem Versprechen, Kosten und Vorlaufzeiten zu reduzieren und gleichzeitig die Leistung von Produkten und Lieferketten zu verbessern, nutzt das Militär seit einigen Jahren die additive Fertigung. Die häufigsten Anwendungen im militärischen Bereich sind Prototyping, Teilefertigung, Werkzeugbau und Reparatur.
Ob für die Herstellung oder die Reparatur von Ausrüstungsgegenständen, der 3D-Druck hat sich wiederholt als geeignetes Produktionsverfahren für die Streitkräfte erwiesen. Jetzt bietet die additive Technologie noch effizientere Möglichkeiten zur Herstellung von Ersatzteilen auf Abruf, wodurch sich die Fertigungszeiten und Lieferströme verbessern.
Bei Einsätzen im Ausland sind die Langlebigkeit der Ausrüstung bzw. ihre Autonomie im Allgemeinen Eigenschaften und Qualitäten, die von den Einsatzkräften für den Einsatz oder die Stationierung besonders geschätzt werden. In dieser Richtung werden mehrere Anstrengungen unternommen, wie z.B. die Verringerung der logistischen Ströme, die eine Quelle der Verwundbarkeit darstellen, um die Gefährdung der Männer zu begrenzen und gleichzeitig die Autonomie der Einsatzkräfte zu stärken.
Wie kann der 3D-Druck dazu beitragen, die Einsatzbereitschaft der Ausrüstung auf einem Niveau zu halten, das die Kontinuität der Operationen und der wesentlichen Missionen gewährleistet?
Für die operative Unterstützung der eingesetzten Einheiten ist die Armee auf zwei wichtige Fähigkeiten angewiesen: Reparaturkapazität und Ersatzteilversorgung. Für diese beiden Mittel ist der 3D-Druck von großem Interesse, da er einen Gewinn an Autonomie und vor allem an Reaktionsfähigkeit ermöglicht.
Der Einsatz der additiven Fertigung soll die Reparatur- und Lieferkapazitäten bis hinunter zu den taktischen Unterstützungsebenen verbessern und beschleunigen. Es gibt viele potenzielle Anwendungen, wie z. B. die Wiederherstellung der Einsatzfähigkeit eines Fahrzeugs durch die Herstellung neuer Ersatzteile oder die Verringerung der mit den Vorräten verbundenen Logistikströme, insbesondere während eines Einsatzes.
Es ist sogar möglich, einen eventuellen Mangel an Lagerbeständen oder einen hohen Verbrauch an Ersatzteilen auszugleichen, zum Beispiel im Falle eines intensiven militärischen Engagements. Ein weiterer wichtiger Vorteil ist, dass die additive Fertigung auch die Herstellung von Teilen ermöglicht, die aus verschiedenen Gründen nicht mehr hergestellt werden können: Verlust von technische Kontrolle, Veralterung, Auslaufen der Lieferungen oder Mangel an Rohstoffen usw. Neue, leichtere Teile mit komplexen Geometrien, die in 3D gedruckt werden, profitieren von sehr guten Festigkeits- und damit Haltbarkeitseigenschaften, da sie aus innovativen Materialien hergestellt werden. Die Geräte werden daher weniger schwer zu tragen sein und eine längere Lebensdauer haben. Die Herstellung von Teilen mit Gitterstruktur ermöglicht es beispielsweise, ein mechanisches System leichter zu machen und gleichzeitig seine Festigkeit zu erhalten oder sogar zu verbessern.
Kurz gesagt, der 3D-Metalldruck kann sowohl zur Reproduktion vorhandener Teile für die Reparatur von Geräten als auch zur Herstellung neuer, optimierter Teile verwendet werden, die einen zusätzlichen betrieblichen Nutzen bieten. Die additive Fertigung verbessert die Reaktionsfähigkeit der Lieferkette und verringert den Lagerbestand, das Veralterungsrisiko und die Gesamtkosten.
Möglichst betriebsnahe Produktion
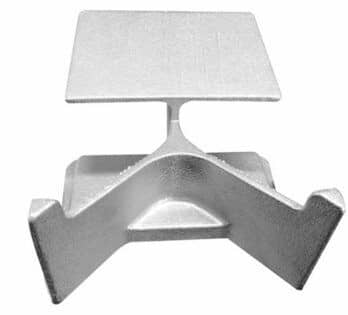
Der ständige Bedarf des Militärs an Wartungs- und Reparaturteilen für schweres Gerät während der Einsätze führt zu sehr hohen Kosten. Die Möglichkeit, die benötigten Teile schnell und einsatznah zu drucken, ermöglicht erhebliche Einsparungen bei Zeit und Produktionskosten.
AddUp antwortet auf dieses immer wiederkehrende Bedürfnis der Verteidigungsindustrie: Ersatzteile und Werkzeuge direkt auf dem Schlachtfeld herzustellen.
Im Rahmen von Militäreinsätzen ermöglicht die additive Fertigung den Einsatz von Kleinserien großer Plattformen, die für die Streitkräfte leicht zugänglich sind. Diese „mobilen Labors“, die an Einsatzorten zugänglich sind, sind ideal für die schnelle Herstellung von Ersatzteilen oder die Anpassung von Ausrüstung für das nahe gelegene Schlachtfeld.
Lesen Sie über eine Fallstudie der französischen Marine, die AddUp’s FormUp 350 einsetzt.
Produzieren Sie überall…
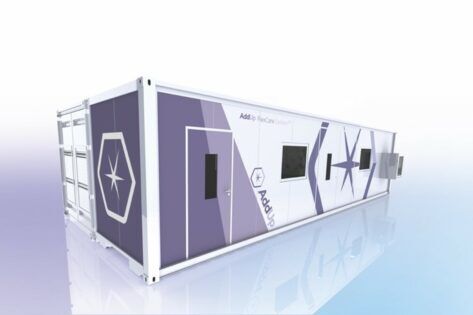
AddUp ist der erste Metall-3D-Druckmaschinenhersteller, der transportable additive Fertigungseinheiten anbietet. Mit dem AddUp Flex Care System TM können Teile bei Bedarf in der Nähe Ihres Betriebs hergestellt werden.
Diese selbstversorgten Einheiten können in den entlegensten Gebieten und unter den rauesten Bedingungen arbeiten. Sie umfassen eine oder mehrere additive Fertigungsmaschinen sowie Nachbearbeitungsmaschinen, um fertige Teile für den sofortigen Einsatz bereitzustellen. Autarkie ist zweifellos ein taktischer Vorteil in militärische Operationen, da sie die logistischen Kosten und die Anfälligkeit für Angriffe der gegnerischen Seite verringern.
In Situationen nach Konflikten, bei der Katastrophenhilfe oder beim Wiederaufbau kann die additive Fertigung lokalen Gemeinschaften helfen, indem sie die Reparatur und Wartung strategischer Ausrüstung erleichtert.
Schlussfolgerung
Im Verteidigungssektor werden additive Fertigungstechnologien in vielfältiger Weise eingesetzt: verschiedene Verfahren, verschiedene Materialien, Produktionsmittel usw. Es gibt zahlreiche Anwendungen wie die Wartung von Fahrzeugen, die Reparatur von Teilen, die Herstellung neuer hochleistungsfähiger und optimierter Teile und die Integration neuer Funktionalitäten. Das Militär nutzt die additive Fertigung von der Forschung bis zur Einsatzphase mit der Entwicklung von Prototypen, Werkzeugen und Funktionsteilen.