The project, “Development of Manufacturing, Heat Treatment, and Surface Finishing Guidelines to Yield Ready-to-Use IN-718 Additive Manufacturing Components,” aims to leverage laser powder bed fusion (LPBF) and surface finishing technologies to produce IN-718 components for legacy armament systems.
CINCINNATI, OH – May 23, 2023 – AddUp, Inc. has joined $1.5M research contract “Development of Manufacturing, Heat Treatment, and Surface Finishing Guidelines to Yield Ready-to-Use IN- 718 Additive Manufacturing Components” through the United States Air Force (USAF) and the Small Business Innovation Research (SBIR) program led my REM Surface Engineering (REM).
The United States Air Force (USAF) is constantly seeking innovative solutions to enhance the readiness and performance of its armament systems. In pursuit of this goal, a project titled “Development of Manufacturing, Heat Treatment, and Surface Finishing Guidelines to Yield Ready-to-Use IN-718 Additive Manufacturing Components” was proposed and awarded. This project, funded through a Direct to Phase II Small Business Innovation Research (SBIR) contract, aims to harness the potential of laser powder bed fusion (LPBF) and surface finishing technologies to produce IN-718 components for legacy armament systems. This endeavor is researching the impact of various heat treatment and printing parameter combinations in association with REM’s surface finishing technology on a component’s mechanical properties such as tensile strength and fatigue life. AddUp and Zeda (formerly PrinterPrezz and Vertex Manufacturing) are providing critical support to this project which aims to provide the USAF with set of manufacturing guidelines to maximize the capabilities of LPBF to meet fleet readiness and sustainment goals.
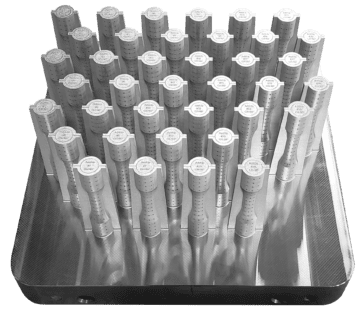
The Significance of Fatigue Strength in IN-718 Material for the USAF:
Fatigue strength plays a critical role in ensuring the reliability and longevity of components used in demanding applications within the USAF. IN-718, a nickel-based superalloy known for its exceptional mechanical properties and resistance to high temperatures and corrosive environments, has gained significant importance in aerospace and defense industries.
The combination of fine powder and a roller recoater in AddUp’s FormUp 350 machine provides a synergistic effect on surface finish improvement, leading to enhanced fatigue properties in IN-718 material. By achieving a more uniform powder layer, reducing surface irregularities, and minimizing defects, the fatigue resistance of the printed components is significantly improved. This is particularly crucial in aerospace and defense applications, where fatigue performance is critical for long-term structural integrity and operational reliability.
Collaboration for Fatigue Testing:
To ensure the integrity and reliability of the IN-718 AM components, fatigue testing is a crucial step. AddUp, in collaboration with Zeda, will manufacture IN-718 fatigue specimens using LPBF technology with AddUp’s FormUp 350. These specimens will be utilized in REM’s testing matrix to establish expected material properties of LPBF components with several levels of surface finish and with different manufacturing and heat treatment parameters. Through this collaborative effort, the project seeks to validate the fatigue strength of IN-718 AM components manufactured via AddUp’s FormUp 350 LPBF technology.
Impact and Benefits:
The Development of Manufacturing, Heat Treatment, and Surface Finishing Guidelines to Yield Ready-to-Use IN-718 Additive Manufacturing Components project represents a significant step forward in advancing the USAF’s capabilities and readiness. By leveraging the capabilities of LPBF technology and conducting rigorous fatigue testing, this project strives to enhance the performance, reliability, and cost-effectiveness of Aerospace and Defense components reducing downtime and ensuring mission-critical operations can proceed smoothly.
AddUp’s FormUp 350 PBF machine is modular and scalable to provide the highest productivity while ensuring user safety. The DED machines are designed for industrial
production and equipped with in-house designed and developed nozzles to provide maximum precision and high productivity. To provide customers with a true Industry 4.0 solution, AddUp also provides a complete monitoring solution providing quality assurances after each and every
build.
AddUp is headquartered in Cébazat, France, with its North American subsidiary based out of Cincinnati, Ohio. In addition to machine design and manufacturing, the AddUp group also offers part production, POC production, metal AM consulting services, AM training, and design for AM, making AddUp your one-stop for metal AM. To learn more, visit www.addupsolutions.com.
About Zeda, Inc.
Zeda (formerly PrinterPrezz / Vertex Manufacturing) is a leading technology solutions company. Our objective is to better lives by investing in cutting-edge technologies, innovative companies, and groundbreaking ideas. Our foundation combines expertise from diverse industries, including AM, nanotech, precision manufacturing, and incubating new ideas. From life-changing medical devices to the foremost advancements in space, our mission is to build it all better together. For more information, www.z8a.com
About REM Surface Engineering
REM Surface Engineering is a global provider of surface engineering solutions to NASA, the DOD, and commercial industries for both traditional/subtractively manufactured components as well as additively manufactured components. REM is a US-based small business with sister companies in the UK and Germany.
REM’s Extreme ISF® Process, is a suite of subtractive, isotropic superfinishing processes tailored to the metal additive manufacturing industry. The technology is capable of reducing the extreme surface roughness associated with metal additive manufacturing while removing or remediating surface and near surface defects such as voids and v-notch failure points and/or providing a mirror-like aesthetic appearance. The process is applicable to external surfaces as well as internal, none-line-of-sight surfaces. Applicable alloys include Aluminum, Copper, Stainless Steel, and Titanium alloys as well as Nickel-Based Superalloys, and Refractory Alloys. REM offers the Extreme ISF Process as an outsourced solution or as a complete technology installation.
REM’s ISF Technologies have been used to enhance the performance of parts in many industries, providing benefits such as reduced friction and wear, improved bending fatigue and improved corrosion resistance. All REM locations operate under an ISO 9001:2015 and AS9100:2016 Rev. D certified Quality Management System. For more information, visit www.remchem.com.