Powder Bed Fusion (PBF) is a widely adopted additive manufacturing technology that includes various processes used for both plastic and metal applications. In this blog, we’ll focus on the metal side of PBF, exploring Selective Laser Melting (SLM) and Electron Beam Melting (EBM), along with their material capabilities and industry uses.
PBF is the most popular of the metal additive manufacturing technologies and excels in producing complex, high performance components. The technology utilizes high-energy sources, lasers or electron beams, and has transformed the manufacturing industry by offering greater design freedom, efficient use of materials, and the ability to produce highly customized components.
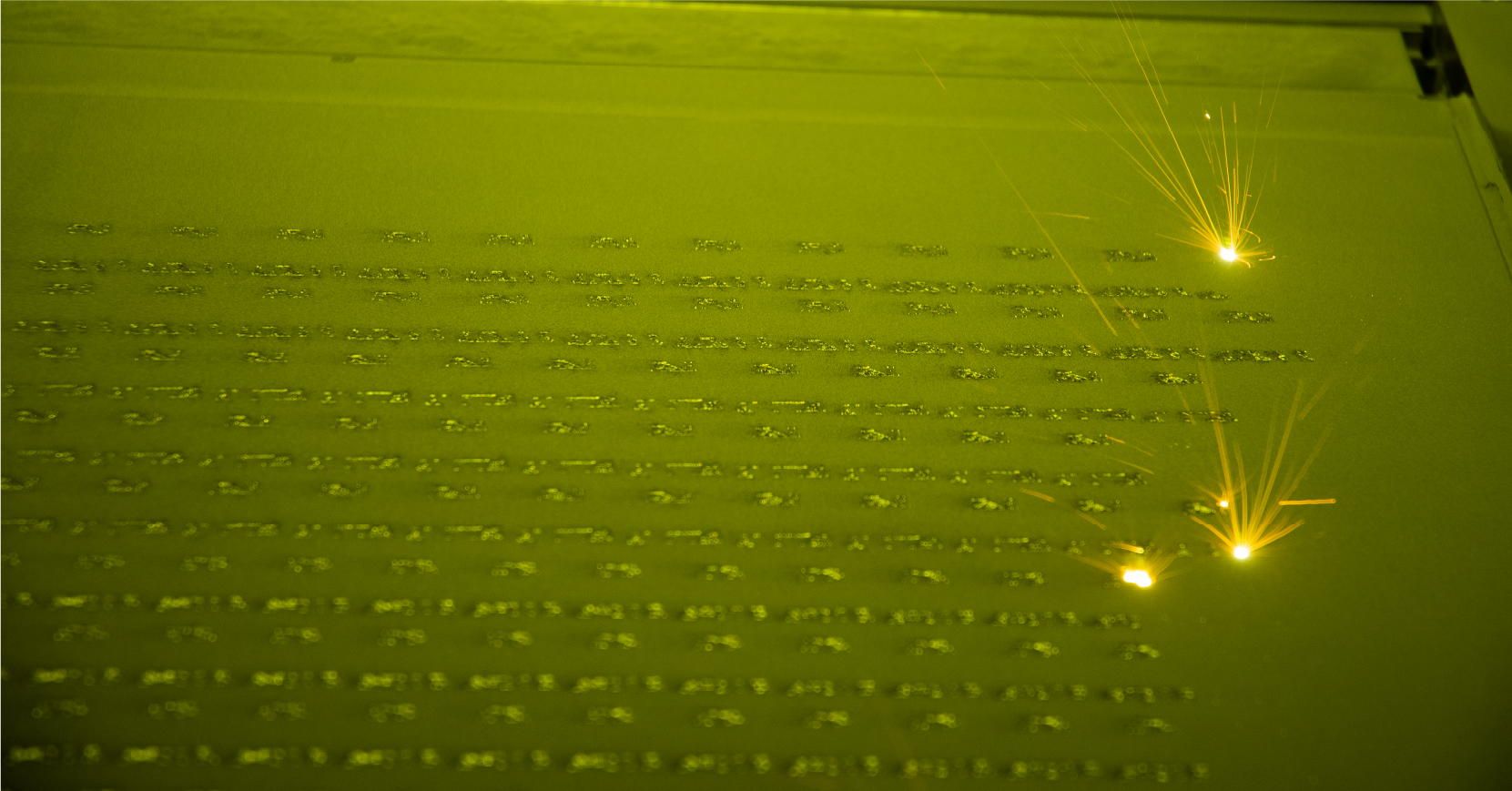
Selective Laser Melting (SLM)
Selective Laser Melting uses high-precision fiber lasers to fully melt metal powder, producing parts with nearly 100% density. This PBF process excels in producing highly intricate and complex components, such as internal channels and organic shapes that are difficult or impossible to create through traditional machining. The precision offered through this technology makes it ideal for applications requiring tight tolerances and sophisticated internal features. And its ability to support a broad range of metal alloys makes it a versatile solution for various industries and applications.
Electron Beam Melting (EBM)
Electron Beam Melting takes a different approach, operating in a vacuum environment with an electron beam as its energy source. This method is particularly effective for manufacturing larger components, offering enhanced build speeds and reduced residual stresses in finished parts. The vacuum environment eliminates oxygen exposure during melting, while elevated operating temperatures improve material properties for specialized applications. EBM’s advanced thermal management during the build process makes it a preferred choice for certain large-scale or high-performance parts.
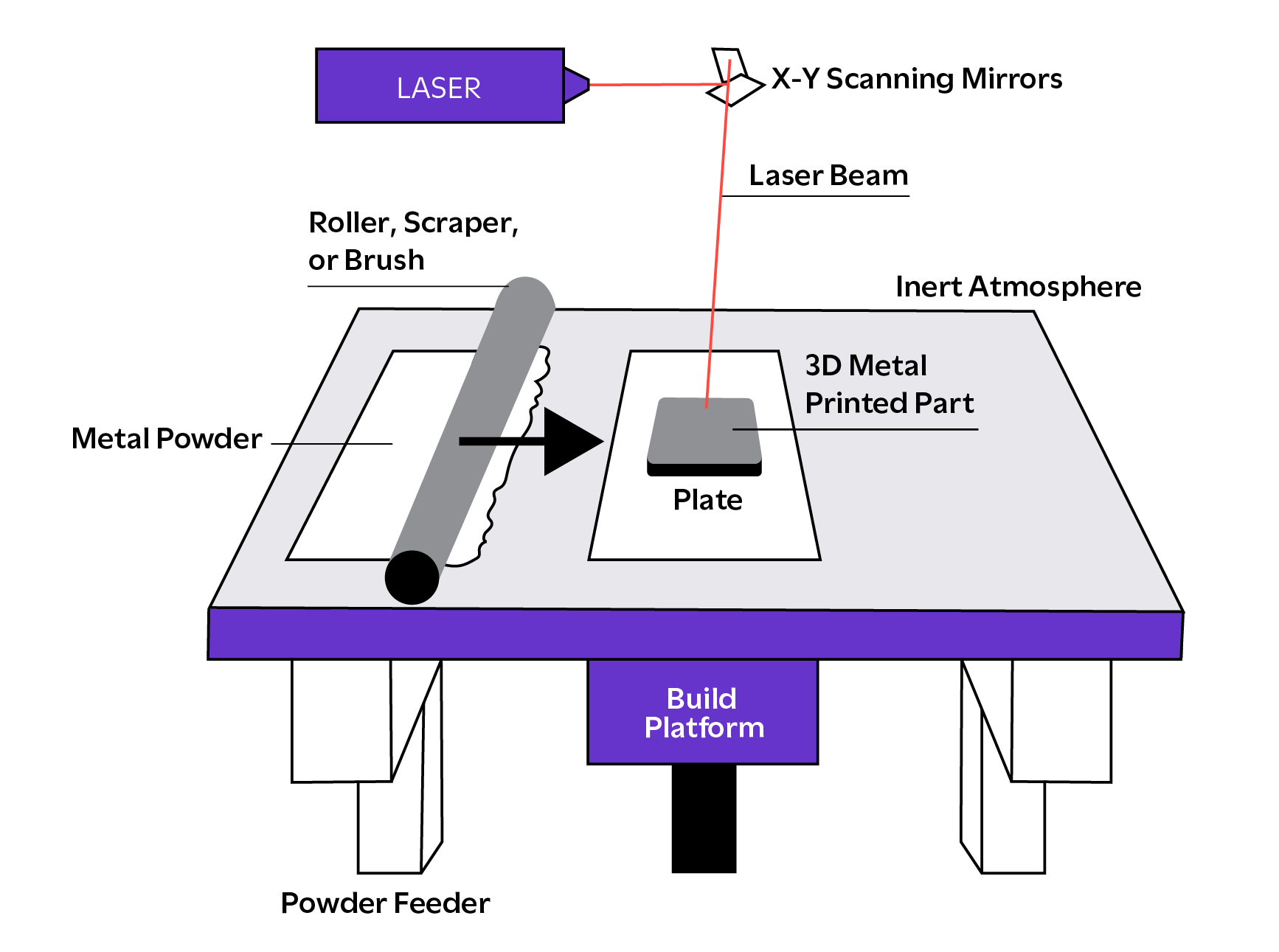
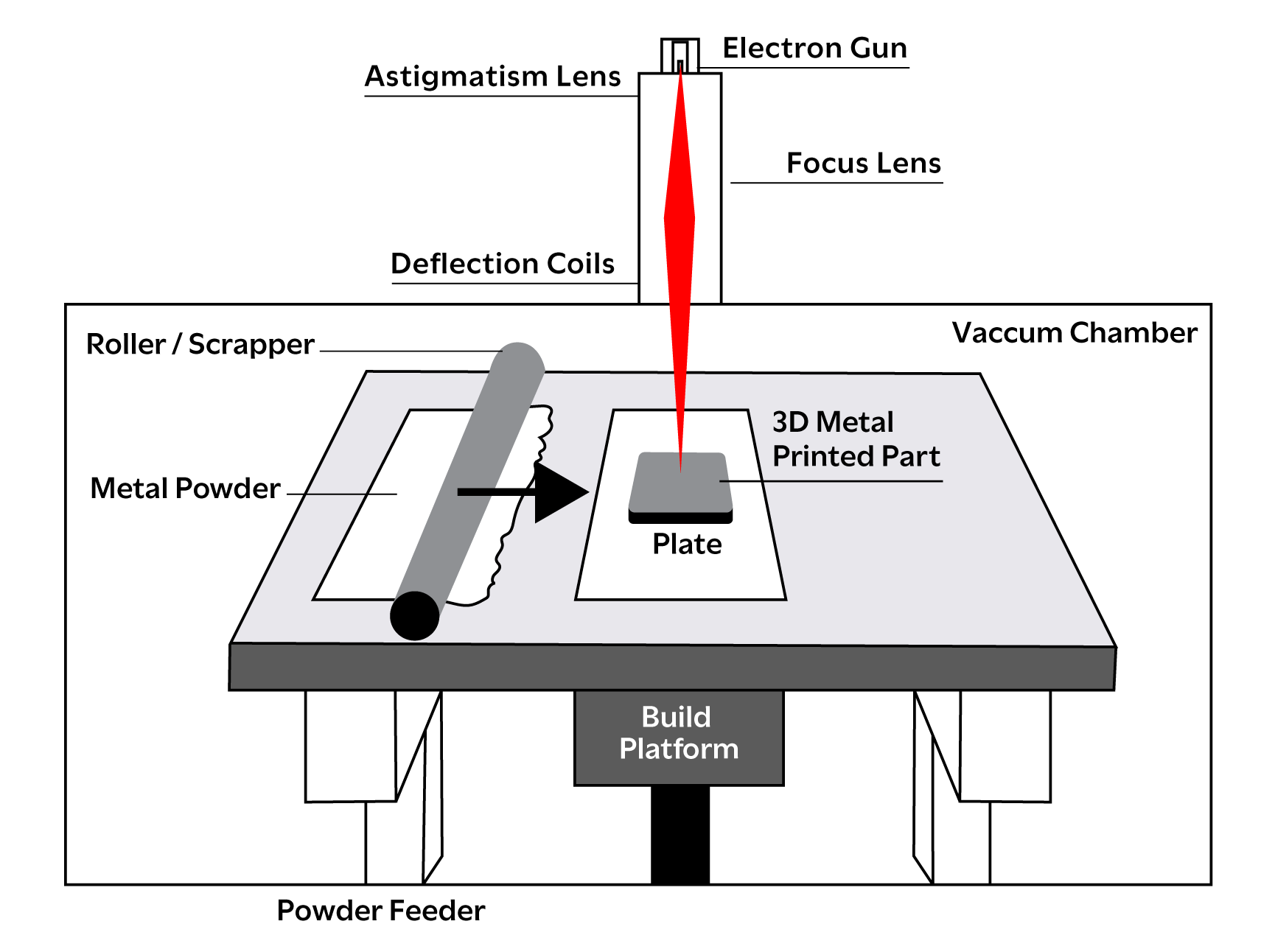
Material Capabilities and Applications
The expanding landscape for PBF enables manufacturers to precisely match materials with application requirements across various industries, with each alloy category offering unique advantages.
Stainless Steels
Among stainless steels, 316L SS has become a foundational material in PBF manufacturing, due to its excellent corrosion resistance, strength and robust mechanical properties. As a surgical grade steel, it is often used for medical instrumentation applications while its corrosion resistance makes it well-suited for fluid transfer applications. Additionally, 17-4 PH stainless steel offers high strength and hardness, making it an ideal material for medical instrumentation as well.
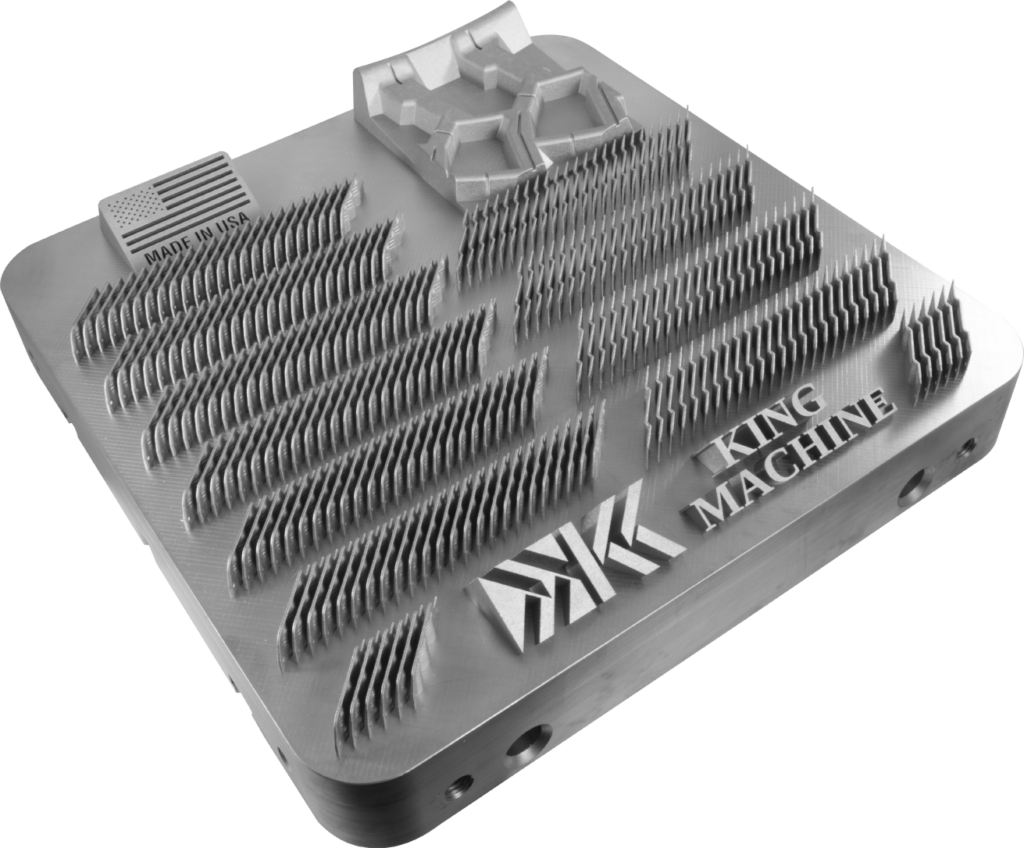
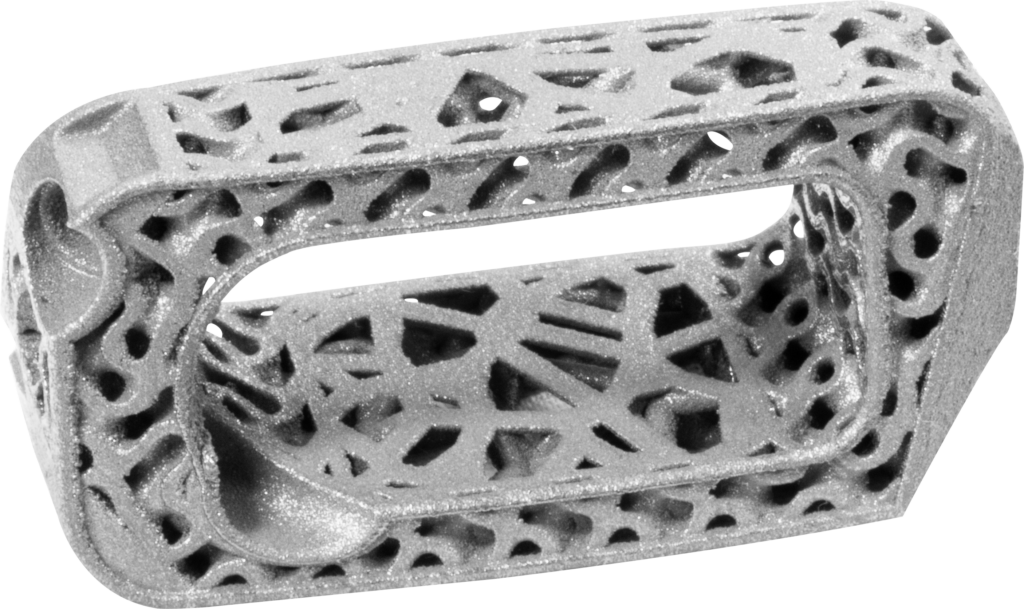
Titanium Alloys
Processing titanium alloys through Powder Bed Fusion has revolutionized high-performance applications, notably with Ti6Al4V. This alloy’s outstanding strength-to-weight ratio and low density make it invaluable in aerospace applications. Its medical-grade variant, Ti6Al4V ELI, features stricter purity levels and lower oxygen content, alongside trusted biocompatibility and superior fatigue properties, making it the preferred choice for orthopedic implants.
Aluminum Alloys
Aluminum alloys represent one of the fastest-growing material families for PBF, with ongoing development of new feedstock that combines printability with trusted alloys from traditional manufacturing. AlSi10Mg and F357 lead this evolution, offering excellent thermal properties and strength characteristics while maintaining superior processability. These alloys excel in heat transfer applications, where their unique properties can be fully utilized. These properties combined with their lightweighting advantages make them especially useful for applications in the aerospace, automotive and industrial industries.
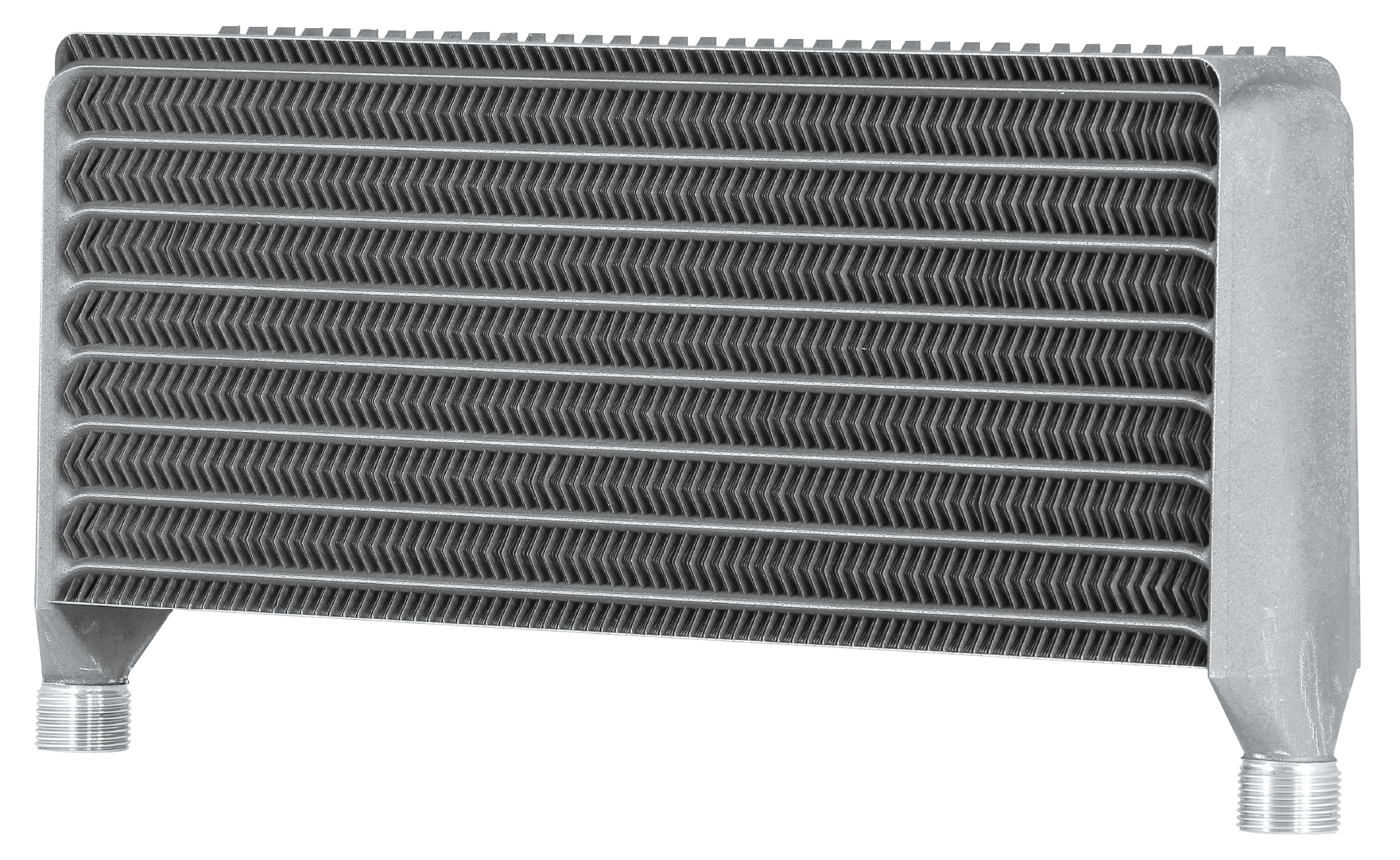
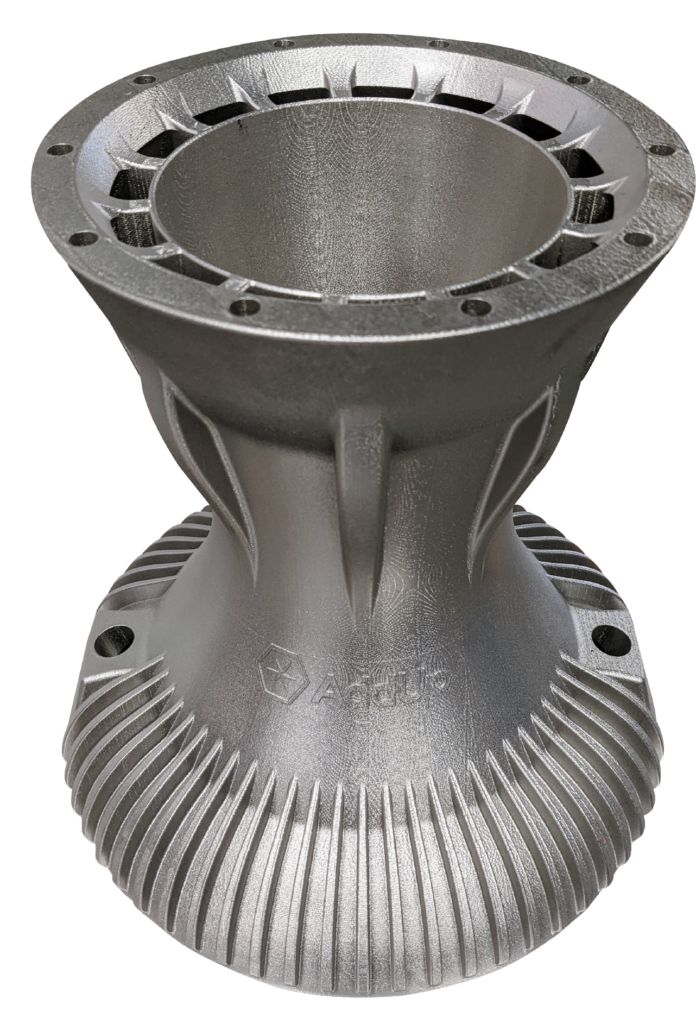
Nickel Superalloys
Nickel superalloys, particularly Inconel 625 and 718, demonstrate exceptional performance at high temperatures, making them essential in aerospace applications. While their mechanical performance may exceed requirements for less demanding industrial uses, they remain cost-effective options for many cases. These alloys often prove easier to process through PBF than traditional machining methods, offering an attractive alternative for complex components. The Inconel family leads this category, with ongoing development of next-generation nickel superalloys promising even better performance characteristics.
Industries Transforming through PBF
Powder Bed Fusion technology is enabling the production of highly complex, optimized components that traditional manufacturing methods cannot achieve. Its precision and ability to work with advanced materials are enhancing performance, reducing weight, and improving design flexibility across various sectors.
Future of PBF Implementation
Successfully implementing Powder Bed Fusion technology requires more than just acquiring a machine—it demands a strategic and comprehensive approach. Key steps include detailed process planning, material selection tailored to application needs, and rigorous quality control measures. Ensuring compliance with industry standards and regulations is critical for delivering consistent, high-quality parts.
As PBF technology evolves, advancements such as improved mechanical properties, larger build volumes, and optimized production workflows are set to drive significant gains in manufacturing efficiency. However, navigating this rapidly changing landscape can be daunting for manufacturers exploring additive manufacturing for the first time.
This is where AddUp can help. With our LevelUp offering, we guide customers through every stage of their additive journey. From application development and selecting the right additive technology to AM training, facility evaluation, and process optimization, our experts work alongside your team to ensure a smooth and successful transition to additive manufacturing. Whether you’re laying the foundation for your first AM operation or optimizing an existing setup, AddUp’s tailored services empower you to achieve your production goals with confidence