See how to improve the cooling of the inserts on a mold using additive technology while increasing the mold’s performance and decreasing the cycle time.
Short injection times are crucial for profitability in the mold industry, especially in the case of injection molds. Zahoransky AG, a German manufacturer of injection molds, needed a mold insert with eight bores with mold rings. Read the case study about a joint project of Zahoransky and AddUp on how to improve the cooling of the inserts on a mold using additive technology while increasing the mold’s performance and decreasing the cycle time.
INDUSTRY
Tooling
CHALLENGE
To improve the cooling of the inserts on a mold using AM technology while increasing the performance of the mold and decreasing the cycle time.
KEY BENEFITS
- Ready to use mold after heat treatment
- Near contour cooling in the insert
- Reduction of time & cost production
Creative Shape
Function Integration
Lead Time
Performance
History
In the mold industry, and especially in the case of injection molds, short injection times are crucial for profitability. They decide how many injection molding machines and molds you need and how high the final price of the part will be. The cooling system in the contour core insert has the most significant influence on these times. Today, the cooling channels are often still produced conventionally by drilling in 2D and cannot always run close to the contour and thus cool evenly and quickly.
Zahoransky AG, headquartered in Todtnau-Geschwend, Baden-Württemberg/Germany, is a manufacturer of injection molds, blister packaging machines, and production equipment. Zahoransky is the world market leader in mold and tool-making for the toothbrush industry. Around 80 percent of the world’s toothbrush molds come from Zahoransky.
Challenges
Zahoransky needed a mold insert with eight bores with mold rings. Up to now, these have had to be well cooled and elaborately sealed using O-rings. The challenge was to improve the cooling of the inserts using additive manufacturing technology in such a way that the cycle times and productivity of the molds would be significantly increased. The complex assembly of the O-rings was to be eliminated, thus reducing manufacturing costs.
The quality of the parts was to be maintained in the usual form. And in addition, the molds needed to be constructed with a steel material qualified for injection molding and had the corrosion and wear resistance for this production.
SOLUTIONS
AddUp optimized the cooling channels and designed them as closely as possible to the original contours using AM 3D options, including unique AddUp Manager adaptive strategies skills. All channels needed the same length and cooling capacity to ensure uniform cooling. AddUp utilized simulation software and thermal design optimization to ensure accurate and uniform cooling for this mold.
Next, the new mold was printed on AddUp’s PBF machine (Laser Powder Bed Fusion), the FormUp ® 350 New Generation, using a productive AM build-up strategy with four lasers. This mold was printed in just 30 hours.
Results
AddUp significantly reduced the production time for this mold when compared to traditional manufacturing time. Post-processing for this mold was also significantly reduced thanks to the roller technology offered on the AddUp FormUp 350.
AddUp’s unique combination of fine powder and a roller re-coater provides a superior surface finish, significantly reducing the time needed for post-processing. The mold was printed using a steel material 1.2709/Margin300. This material is a qualified tool steel offering good tool life in the mold.
Zahoransky was pleased with the quality of the mold as well as the production time.
The next step in this project is for another prototype to be manufactured with additional optimizations and in a newly developed tool steel 1.2083/PM420. This new material is a qualified injection molding steel widely used and offers good corrosion and wear resistance.
For more information about additive manufacturing technology for the tooling and molding industry, please do not hesitate to contact us.
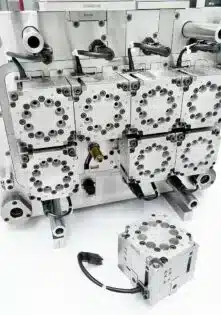
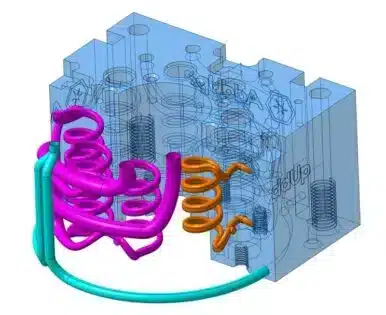