Additive Manufacturing Heat Exchangers: Applications and Benefits
Additive manufacturing (AM) revolutionizes heat exchanger production by enabling complex geometries that maximize heat transfer efficiency far beyond what traditional manufacturing can achieve. With laser powder bed fusion (L-PBF), AM allows for higher surface area-to-volume ratios, improved thermal performance, and reduced weight.
However, achieving these benefits requires overcoming key technical challenges:
- Managing thermal stresses and deformations to maintain structural integrity
- Optimizing surface roughness for enhanced heat transfer and durability
Why Surface Finish Matters in L-PBF Heat Exchanger
Surface quality is critical for performance, safety, and longevity in metal 3D-printed heat exchangers.
A smooth, uniform surface finish:
- Reduces fatigue failure risks by minimizing stress concentrations and crack propagation
- Reduces flow resistance to improve thermal efficiency and heat dissipation
- Reduces fouling and contamination buildup, extending service life and simplifying maintenance
With L-PBF’s precise surface control, manufacturers can create high-performance heat exchangers that maintain efficiency over time, resist fouling, and support demanding thermal applications in aerospace, automotive, and industrial sectors.
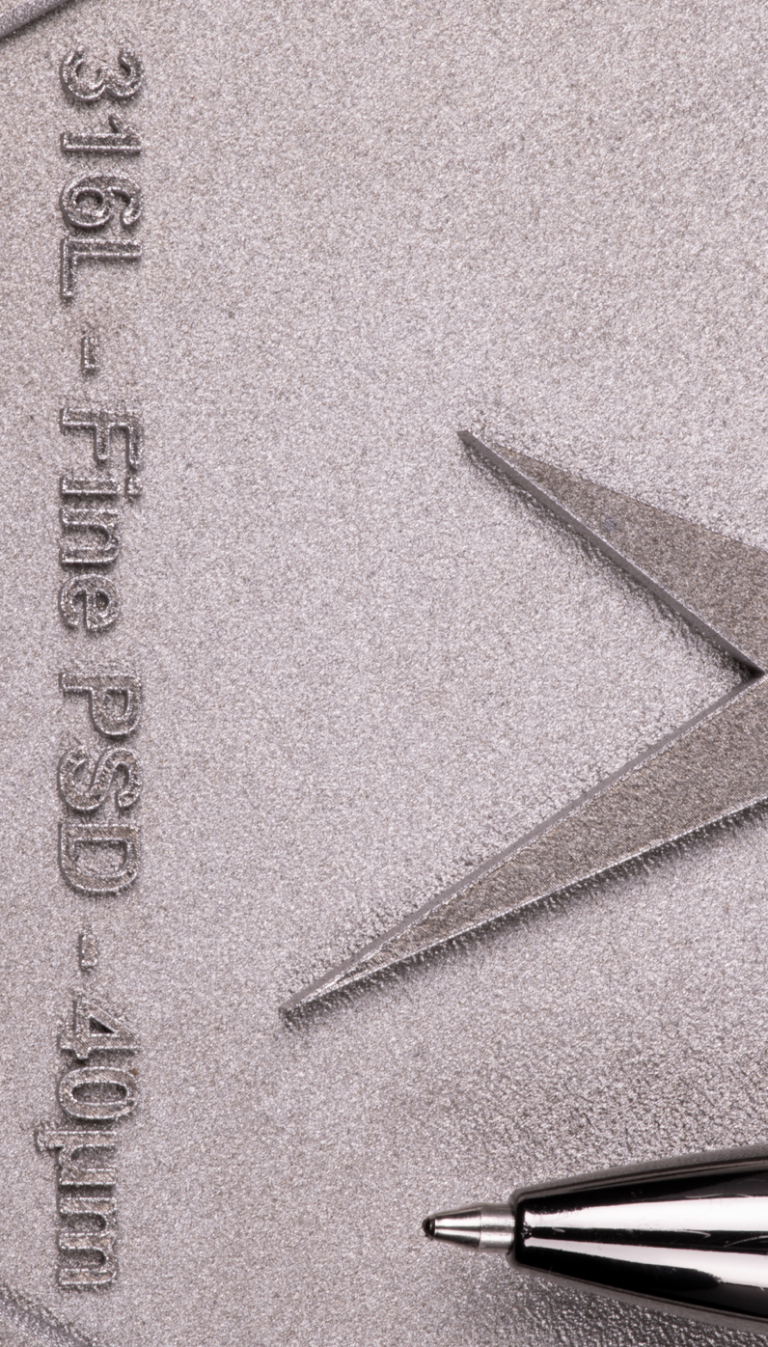
Materials for Heat Exchangers
Heat exchangers are often fabricated using metals that offer good thermal conductivity, mechanical strength, and corrosion resistance.
Below are some of the materials for heat exchangers that have been used on the FormUp 350 and their pros and cons:
316L SS
Affordable and corrosion-resistant, but limited strength for high-pressure or high-temperature applications.
Inconel 718
Exceptional high-temperature mechanical properties and corrosion resistance, but costly and has lower thermal conductivity.
AlSi7Mg and AlSi10Mg
Lightweight with excellent thermal conductivity, but lower strength and fatigue resistance.
Ti-6Al-4V
High strength-to-weight ratio and corrosion resistance, but relatively expensive with poor thermal conductivity.
AlSi7Mg Heat Exchanger
This project explores the use of Powder Bed Fusion (PBF) for manufacturing highly efficient heat exchangers. The goal was to optimize thermal performance and part compactness, leveraging the PBF process to create complex geometries with thin walls and efficient internal structures.
Read More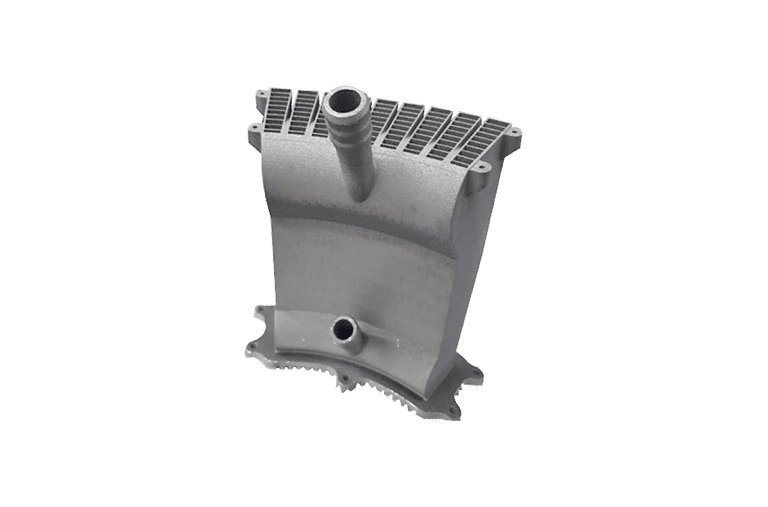
Objectives:
- Design a compact, high-performance heat exchanger.
- Utilize PBF for intricate, thermally efficient geometries.
Challenges Overcome:
- Achieving high thermal performance in a smaller volume.
- Creating precise, leak-tight geometries for high-performance cooling.
Results:
- Validation through thermal and leak-tightness testing.
- Successful demonstration of PBF’s capability for aerospace-grade heat exchangers.
FormUp Heat Exchanger
This initiative aimed to improve the cooling efficiency of the FormUp 350 through a compact, cost-effective additive solution.
Read More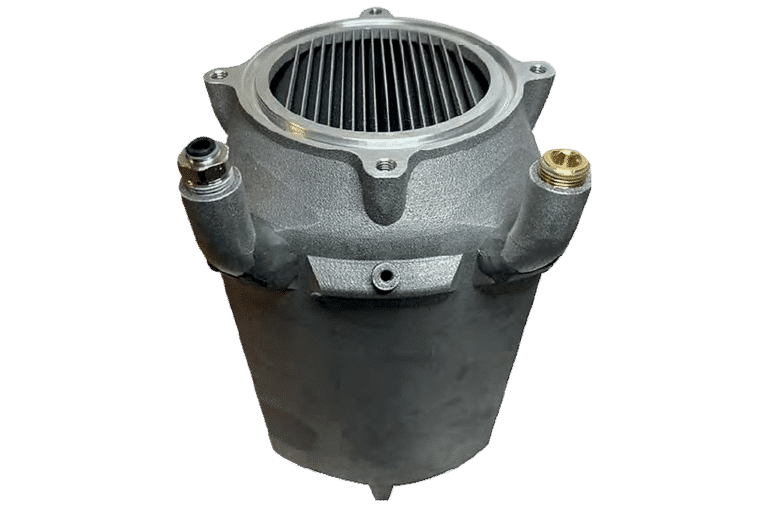
Objectives:
• Optimize heat dissipation for better efficiency.
• Reduce production costs and simplify design.
Challenges Overcome:
• Enhancing cooling efficiency with a compact design.
• Balancing cost reduction and performance.
Results:
• 64% size reduction and 6x lighter mass.
• Cost equivalent to traditional designs.
HEWAM Heat Exchanger
In this case study, Temisth and Printsky (joint-venture with AddUp and Sogeclair) worked to develop a Heat Exchange With Additive Manufacturing (HEWAM) from Inconel 718 for aerospace applications.
Read More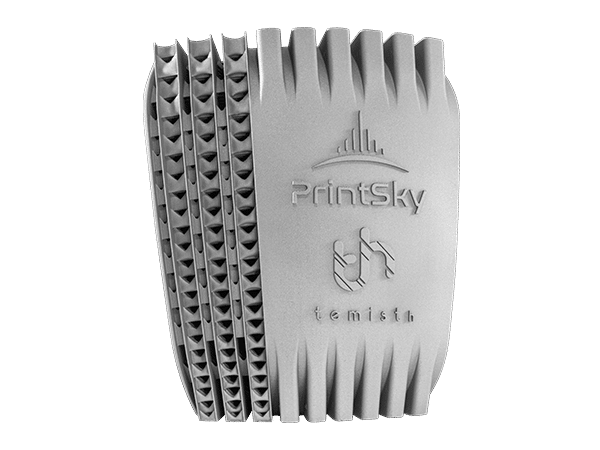
Objectives:
- Develop a double-curved heat exchanger compatible with aerospace systems.
- Optimize thermal performance and compactness through additive manufacturing (AM).
- Use AM to create complex channel shapes for improved heat transfer.
Challenges Overcome:
- Ensuring sufficient airflow through the heat exchanger while maintaining high heat transfer efficiency.
- Managing material constraints, using Inconel 718 for its thin-wall capabilities despite being heavier and less conductive than aluminum.
- Designing the heat exchanger to fit within the required aerospace surfaces and volumes.
Results:
- A modular, compact solution with reduced material use.
- Successfully tested, demonstrating excellent thermal performance and tightness.
NATHENA Project
The NATHENA project (2018–2022) brought together a consortium of industry leaders, SOGECLAIR Aerospace, AddUp, TEMISTh, and the Von Karman Institute for Fluid Dynamics (VKI), to revolutionize aerospace heat exchanger design using additive manufacturing (AM). With a €1.5M budget, the project aimed to develop compact, high-performance heat exchangers that optimize thermal efficiency, reduce weight, and meet stringent aerospace standards.
Read More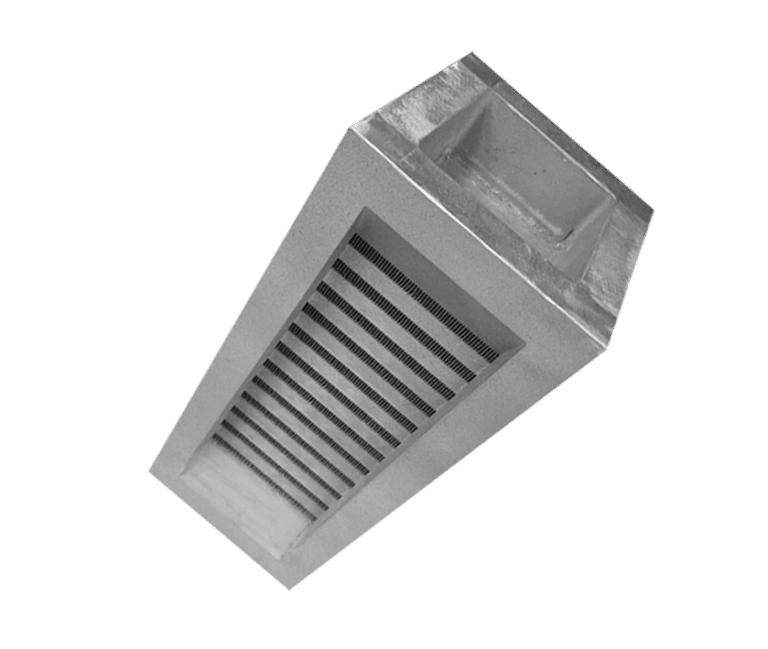
Objectives:
- Create adaptable, compact heat exchangers with optimized thermo-hydraulic performance and reduced mass.
- thin walls and complex internal fins.
- Use computational fluid dynamics (CFD) and rigorous testing to correlate design simulations with real-world performance.
Challenges Overcome:
- Surface Roughness and Pressure Drops
- Thermal Efficiency
Results:
- Heat exchangers achieved up to 30% greater thermal efficiency and reduced weight, with dimensions up to 350x350x350 mm.
- Experimental tests validated CFD simulations, ensuring designs met or exceeded aerospace standards.
Printsky Heat Exchanger Project
This Heat Exchanger project focused on using additive manufacturing to increase the Technology Readiness Level (TRL) of a new generation heat exchanger utilizing the power of the FormUp 350.
Read More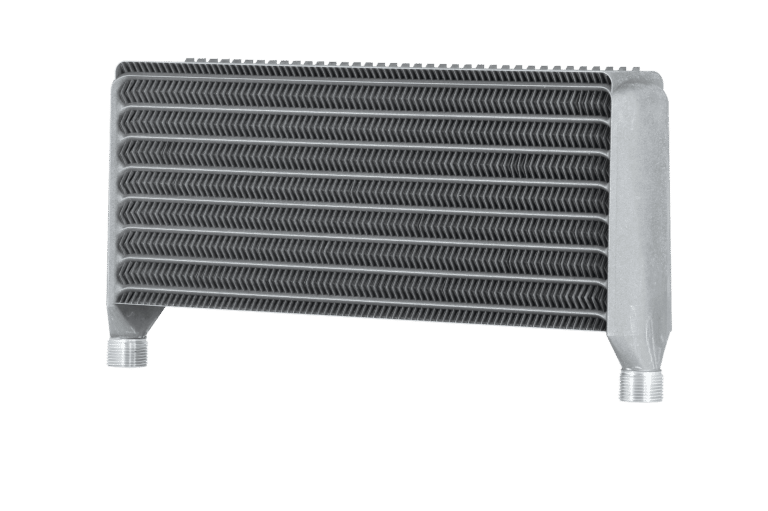
Objectives:
- Optimize heat exchange efficiency with additive manufacturing.
- Reduce mass while maintaining performance.
Challenges Overcome:
- Achieving intricate geometries and fine details in the heat exchanger.
- Overcoming limitations of traditional manufacturing processes.
Results:
- Improved thermal efficiency and part reduction.
- Demonstrated additive manufacturing advantages in aerospace applications.
FormUp 350
Every one of these heat exchanger successes was made possible by the FormUp 350. Its high-resolution capabilities (with continuous thin walls as low as 75 µm), advanced powder handling, safety, and modular 4-laser architecture make it a reliable platform for producing complex, high-performance thermal components.
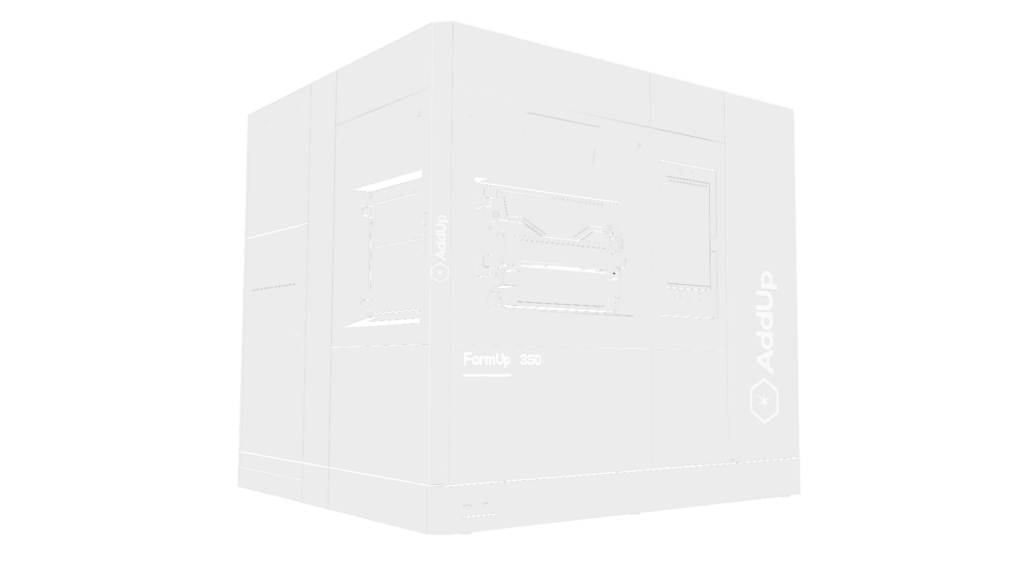
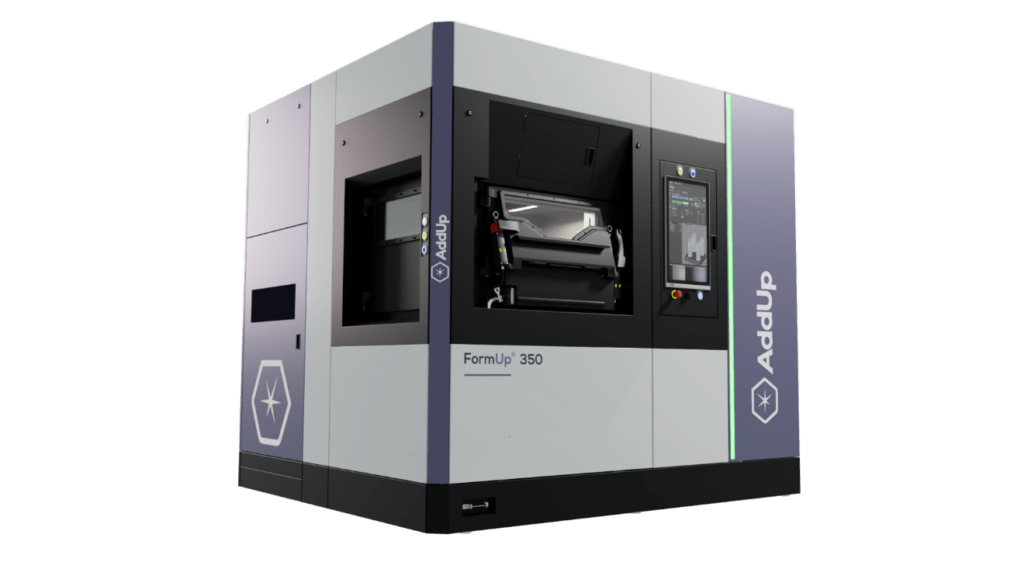
FormUp 350
Every one of these heat exchanger successes was made possible by the FormUp 350. Its high-resolution capabilities (with continuous thin walls as low as 75 µm), advanced powder handling, safety, and modular 4-laser architecture make it a reliable platform for producing complex, high-performance thermal components.
Get the Tech Specs