Medical Implants: Better Surface Finish For Better Patient Outcomes
Large spinal fusion devices are conventionally printed on smaller format machines using Powder Bed Fusion (PBF) or machined out of polyetheretherketone (PEEK) bar stock. When manufactured additively, these larger spine implants are typically printed on small format machines with a small build plate and only 1-2 lasers. They are also typically printed with their anterior face upwards in Z. This orientation in combination with the multi-step process creates a worst-case scenario. The price increases because most of the cost is driven from the production process itself. Although the cost is high, benefits that Additive Manufacturing (AM) large spinal implants are realized through the lattice design and surface roughness, providing osseointegration which leads to better patient outcomes.
Another benefit to AM spinal fusion devices comes from the material. AM allows for printing in titanium with a greater fracture toughness and higher ultimate tensile strength. When produced using PEEK, these types of implants lack ideal osseointegrative features. This coupled with an unstable material supply chain creates challenges when manufacturing large spinal fusion devices using PEEK. For these reasons, producing these implants additively is often preferred.
Read The Case Study
Let AddUp Support You Through Your Additive Journey
Our Satisfied Customers
“AddUp has demonstrated a set of capabilities that enable us to address unique design and application challenges faced by our growing base of aerospace, space, and defense customers.”
Greg Morris
“AddUp group has enabled our complex designs to become a reality using metal Additive Manufacturing, a state-of-the-art process. This will change the way we create and customize a motorcycle. Our creativity is now limitless, which was impossible with traditional metal manufacturing processes.”
Simon Dabadie
“The AddUp team has proven to live within their proclaimed values… delivering a beneficial experience, being a trusted partner, and encouraging innovation. As I navigate through projects, I have been impressed with the level of attentiveness and service they exhibit. Each interaction is laced with education, professionalism, and care.”
Shannon VanDeren
“The FormUp350 is one of the only machines on the market that can run both the typical LPBF powder cut and a much finer cut of powder. This gives us flexibility to meet certain challenging applications we may come across in the future.”
Rachel Levine
“The only French manufacturer of powder bed laser fusion machines (LPB-F) offering rare expertise both on the process and its applications with a machine capable of safely producing high quality parts in a repeatable and reliable way.”
Jean-Christophe Augé
“As an early adopter of AddUp machines, I really appreciate capabilities and proactive team spirit, to deliverer parts in a serial mode.”
Aurelien Fussel
“We chose AddUp as our machinery partner for our recent project due to their High-Quality Products and Innovative Technology. AddUp’s commitment to research and development leads to cutting-edge solutions, like the Modulo 400 system, which offers versatility and high-quality results. This aligns perfectly with our vision at the Application Center for Additive Manufacturing at Research Institutes of Sweden AB, where we aim to lead in applied research and collaborate on new materials and solutions for the market.”
Seyed Hosseini
“AM is in a state of exponential growth with the biggest challenges in adoption being qualification and certification. NSL is focused on partnering with companies who are passionate about driving innovation for metal 3D printing.
Over my past three years working with AddUp they have demonstrated a commitment to industrializing additive technology. The evolution of the FormUp 350 has made significant advancements in its full-field, 4-laser system and its monitoring suite which helps to accelerate the qualification process. Advancements like this prove AddUp to be a major player in the growing AM industry.”
Ed Herderick
Think Smart. Manufacture Different.
With more than 20 years experience in Additive Manufacturing, our machines have been designed to master detail and optimize productivity.
From the industrial roots of our founding partner companies, Michelin and Fives, to technology built for the future, AddUp machines provide innovative solutions to manufacturers’ challenges. Pressed to find cheaper, smarter, and faster ways to meet market demands, manufacturers are looking for a reliable partner to guide them along their additive manufacturing journey. They want a guide who, beyond machines, provides a new vision of manufacturing for the future. AddUp is that guide.
In applying our industrial experience in building complex parts with our reliable and repeatable additive manufacturing machines, we help customers manufacture in a safer, cleaner, and more efficient way through digital manufacturing.
Ask An AddUp ExpertAddup Success Stories
The use cases for additive manufacturing are as varied as the number of manufacturers. With benefits such as the ability to serially produce complex parts, manufacturers constantly look to additive manufacturing to produce new parts in better ways.
Aerospace
Cassegrain Antenna
Ready-for-Flight Antenna in Powder Bed Fusion Thales Alenia Space is a french aerospace manufacturer that has played a significant role in space exploration for more than 40 years. As new […]
Michelin Tires Sipes
Discover how Michelin produces over one million tire sipes a year for their production molds using metal 3D printing When Michelin found that the metal AM machines on the market did not meet their high-quality…
Rocket Nozzle
AddUp optimized the design of a rocket nozzle to improve the performance of a micro-launch vehicle. Metal additive manufacturing can lead to fuel and production savings in aerospace. In this case…
Spine Implants
This case study focuses on spine implants and the challenges faced in their manufacturing process today. Additive Manufacturing (AM) offers benefits such as lattice design and surface roughness, leading to…
Aerospace
Isogrid Case Study
Combining Traditional Manufacturing with Additive – Adding Features with Directed Energy Deposition
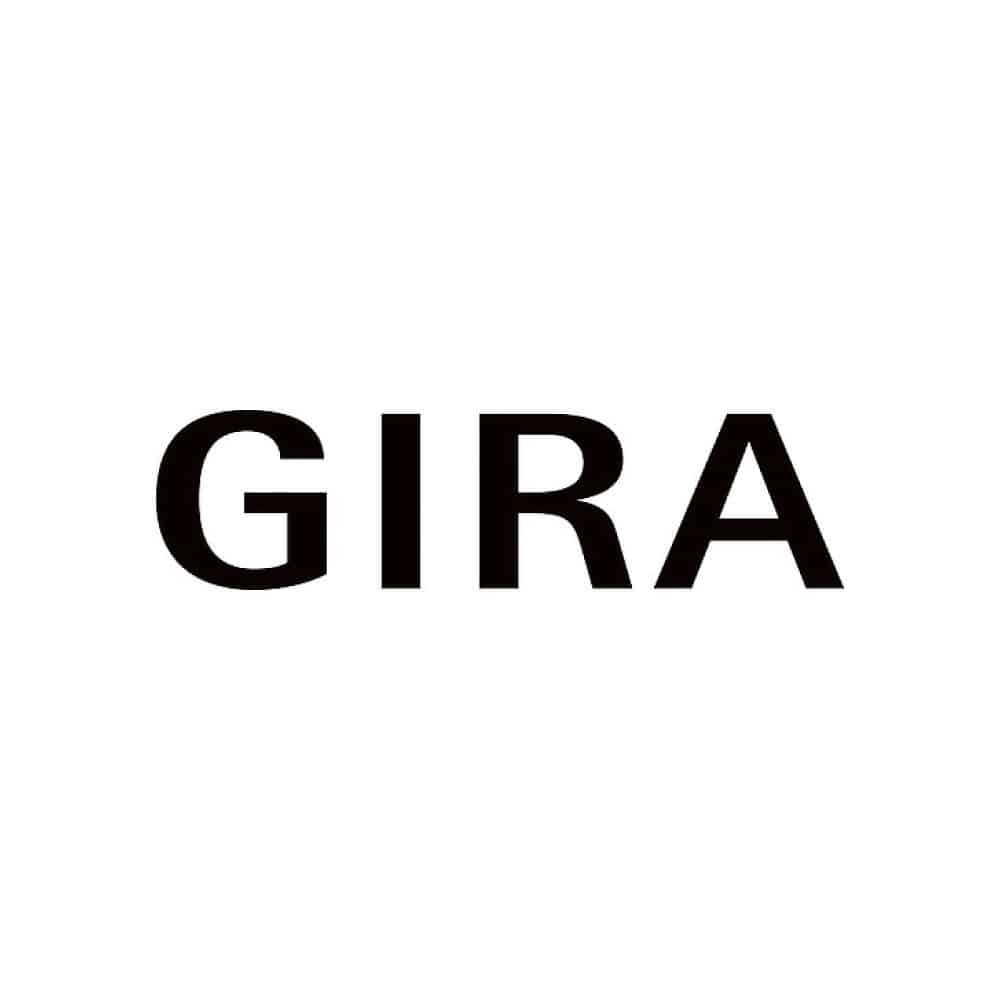
Tooling
Gira Socket Injection Mold Case Study
An improvement in temperature control are guaranteed by employing intricate complex conformal cooling channels using the design freedom of AM.
Automotive
Multi-Metal, Multi-Technology Piston Head
This case study presents the development of multi-metal, multi-technology piston head The goal was to improve wear resistance and performance, as well as internal cooling channels.
Metal 3D Printing
FormUp Heat Exchanger
This case study presents the development of an optimized heat exchanger for the Form Up® 350 machine,. The goal was to improve heat dissipation and adapt the dimensions for easy installation.