As Powder Bed Fusion (PBF) technology matures, its capabilities meet the needs of more and more industries. One of the faster growing sectors is Additive’s involvement in Aluminum Die Casting. Here, we explore how improvements made in Surface Finish can service the Die Casting industry.
Tooling has an important purpose: to create high-quality end use parts. While the GD&T minutia of the final part may be pored over for months, less attention is paid to the tools themselves, as long as they can get the job done. In an industry where technology and workflow has been stable, Additive Manufacturing has to showcase clear-cut advantages to disrupt the tooling space. Whereas traditional manufacturing has handled toolmaking with relative ease, designers using AM will need to examine each application with a fine-toothed comb to best exhibit how AM can push the boundaries of tool performance. This is made more challenging by the limited material portfolios of Powder Bed Fusion (which are expanding!), meaning we aren’t always replacing an existing tool with a matching material. Improving molds via the design freedoms awarded by 3D Printing is not enough, the new tools must be optimized for surface finish as well.
Why care about surface finish?
Surface finish plays a key role in wear performance of the tool and reducing the post-processing burdens of the part and/or tool. Let’s dive into what this means for the Aluminum Die Casting industry:
Wear Performance: One of the most basic metrics for tools – how long do they last before they need to be retouched or replaced? Tool life can be measured in number of shots, total parts produced, time spent on an active production line, or in various other ways. Clearly, it is advantageous for molds and tools to last longer, as the manufacturer would like to spend as little time making tools and instead make the revenue-producing parts. Surface finish is critical for achieving best possible wear performance, as wear failures often start as small imperfections on the surface of the tool itself. Better surface finish means the part-mold interaction takes place at a smoother area with smaller stress concentrators, and therefore working for longer before needing to be replaced.
Sometimes it is acceptable to use an as-printed surface in a tool, but some applications require a finish that can’t be achieved with 3D Printing. In Die Casting, for example, molds are normally shot-peened or bathed in chemicals before use. The better the surface finish these molds can start with, the less time they spend being processed before use. By achieving a better out-of-the-box surface, you’re saving on time and resources needed to create a final product.
Surface finish is a key area of focus for Powder Bed Fusion, and more opportunities will present themselves to the industry once strides are made in this field. AddUp is leading this pursuit by implementing a combination of a Roller Recoater and fine powder in the FormUp 350. Only a roller is capable of handling fine powders (ie 5-25um) without them clumping together. The finer media paired with a compacted powder bed creates a consistent, better controlled melt, leaving behind as-printed surface finishes as smooth as 3um Ra. Attaining these finishes without sacrificing productivity is a huge step towards more widespread comprehension of Powder Bed Fusion as a viable production tool, including the tooling industry.
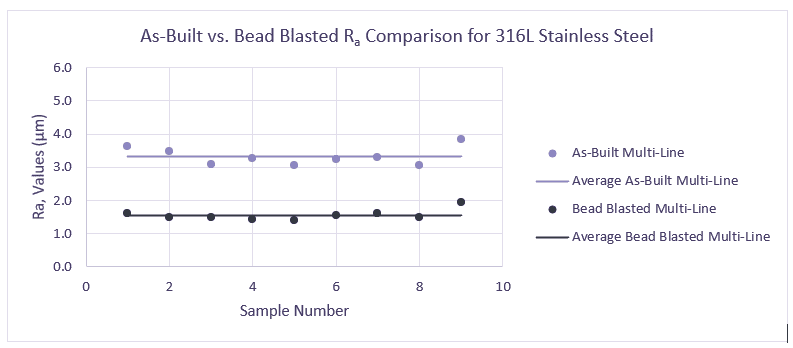
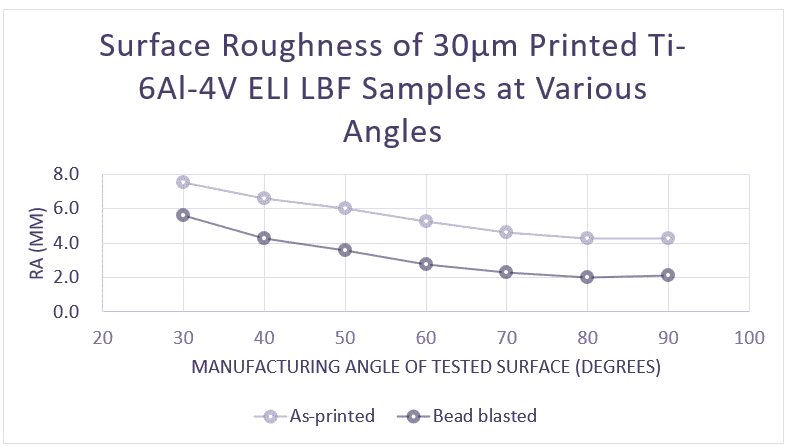