Development of new materials to be utilized with AM technology is a key step in fully realizing the potential AM has to offer.
Additive manufacturing (AM) is a revolutionary manufacturing technique that will reshape the future manufacturing sector. Design freedom, waste reduction and mass customization are some of the benefits of AM. Although AM technology may not be used by all manufacturers today, the potential ahead is massive. Development of new materials to be utilized with AM technology is a key step in fully realizing the potential AM has to offer.
In the AM technology evolution process, it is necessary to develop melting parameters for existing standard alloys and newly designed alloys so that the material properties meet or exceed conventional manufacturing techniques such as casting, forging, rolling and machining, etc.
In addition to material development, appropriate qualification is necessary to fabricate critical components for medical, aerospace and tooling applications. Material qualification can be very time-consuming and expensive depending on the application or industry. The first step in this process is establishing baseline melting parameters in which sufficient data needs to be collected to demonstrate that the material will function as required.
Material development for metal AM is a complex process that requires a thorough understanding of melting and re-solidification temperatures and corresponding microstructures. Melting strategies can have several specific focuses, such as part quality, productivity, and feature specifics, so a “one-size-fits-all” approach is not feasible. For application-specific product development the customer’s use case must be kept in mind for material development from start to finish.
The addition of new materials to the existing catalog requires rigorous testing and analysis to ensure that the printed part meets the quality requirements. This requires an immense amount of work in defining and executing the printing, testing and analysis protocols. This blog will explore some of the important considerations in melting parameters development.
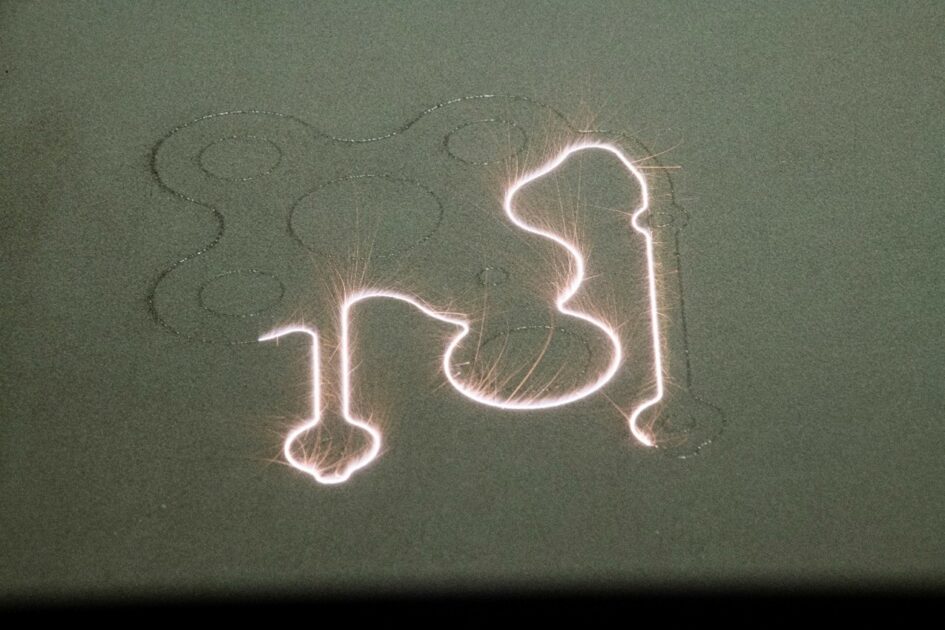
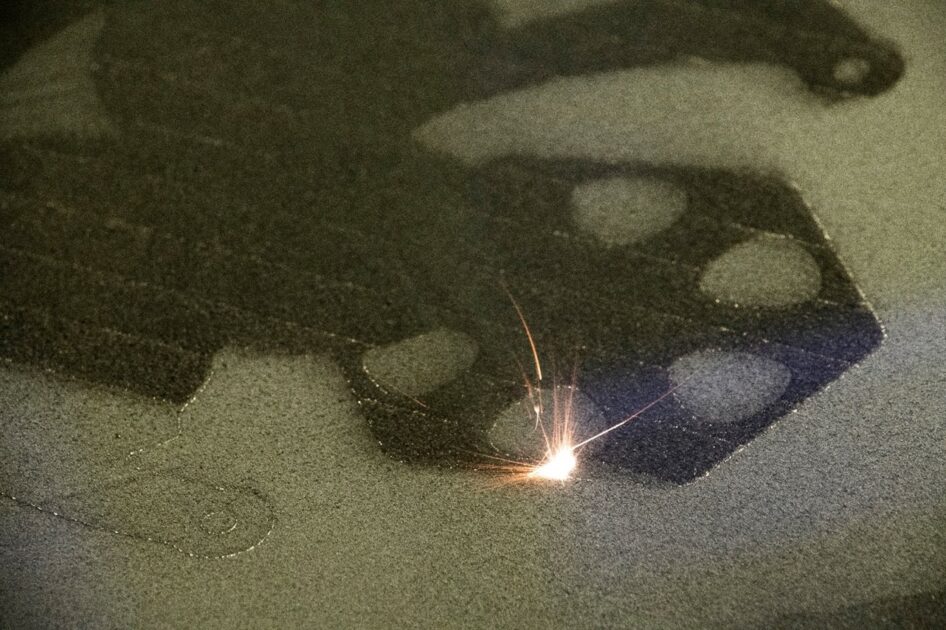
Feedstock Properties
Feedstock material selection is the first and foremost important step in the metal AM process. Key attributes of metal powder such as shape, size, flowability and chemical composition contribute to achieving high-quality parts. So, it is important to choose the correct powder depending on the required functionality of the part.
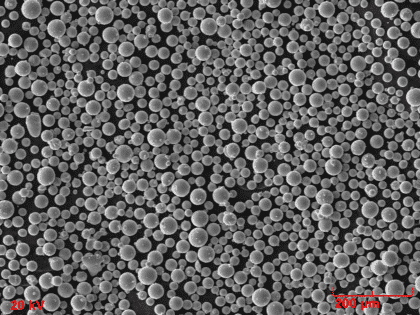
Melt Pool Dimensions
This aspect of development measures the physical characteristics of a single bead pass, as well as the melt pool dimensions of each bead. A statistically driven experimental approach combined with simulation analyses can be utilized in identifying the primary melting parameters to obtain the appropriate melt pool dimensions to achieve the required solid densities.
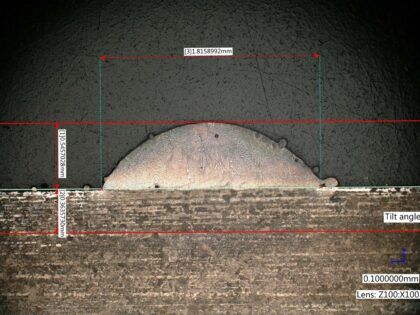
Solid Part Density
Solid part density is a measure of porosity inside of a printed part and builds off dialing in single beads by changing how they are printed next to each other. Layer thickness and laser scanning rotation angles significantly impact how these melting passes interact with each other. This directly impacts the density and microstructures of the printed parts. Solid part density can be tested with techniques such as metallography or MicroCT scan.
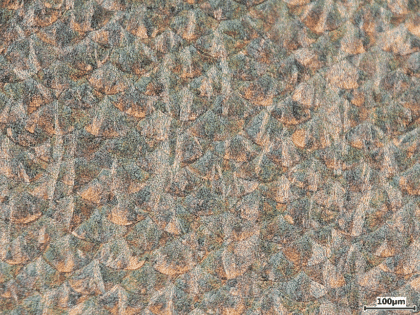
Material Performance
Printed material performance must be tested extensively when developing new melting parameters. This includes physical and mechanical data collection from various tests. In addition, checking for warpage and any other dimensional deviation of the printed part before and after post-thermal conditions is necessary. This helps in understanding the byproducts of internal stresses and the efficacy of post-thermal conditions on part geometry.
This preliminary dimensional, density, surface finish and tensile data validate the quality of the melting strategy before moving to an expensive application specific qualification process.
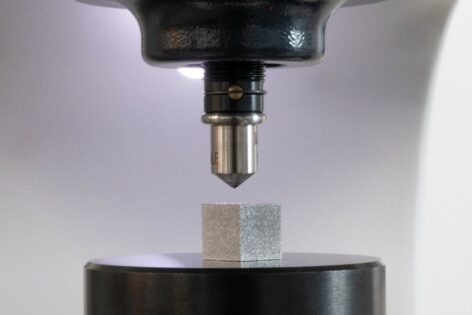
Specific Use-Case Optimization
While optimized baseline melting parameters are necessary to print most parts, if there are specific quality requirements extra measures need to be taken. It is critical to incorporate part production/quality requirements such as surface finish, productivity, and feature resolution, etc. from the inception of the development.
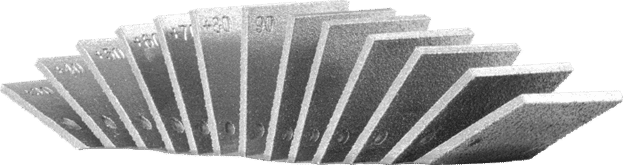
The AddUp Difference
AddUp’s catalog of materials includes a diverse mix of different alloys of steel, titanium, aluminum, Inconel, and more. We continuously work on developing and optimizing melting parameters for new materials to fit the needs of the industry. AddUp utilizes a fully data-driven approach and application specific inputs in developing new materials or changes to the existing melting strategies. With our expert materials engineering team combined with in-house testing capabilities, we can produce melting strategies for new or existing materials quickly and efficiently. In this process we are open to collaborating with industry partners and academic researchers.
Check out this video showcasing some of our material development process for Zeda in 17-4 PH Stainless Steel at our AddUp Solution Center in Cincinnati, OH.
Learn more about the capabilities of the FormUp 350.