Die Entwicklung neuer Materialien, die mit der AM-Technologie verwendet werden können, ist ein wichtiger Schritt, um das Potenzial von AM voll auszuschöpfen.
Die additive Fertigung (AM) ist eine revolutionäre Fertigungstechnik, die den Fertigungssektor der Zukunft umgestalten wird. Designfreiheit, Abfallreduzierung und Massenanpassung sind einige der Vorteile von AM. Auch wenn die AM-Technologie heute noch nicht von allen Herstellern genutzt wird, so ist das Potenzial doch enorm. Die Entwicklung neuer Materialien, die mit der AM-Technologie verwendet werden können, ist ein wichtiger Schritt, um das Potenzial von AM voll auszuschöpfen.
Im Entwicklungsprozess der AM-Technologie müssen Schmelzparameter für bestehende Standardlegierungen und neu entwickelte Legierungen entwickelt werden, damit die Materialeigenschaften konventionellen Fertigungstechniken wie Gießen, Schmieden, Walzen und Bearbeitung usw. entsprechen oder diese übertreffen.
Neben der Materialentwicklung ist eine angemessene Qualifizierung erforderlich, um kritische Komponenten für Anwendungen in der Medizin, der Luft- und Raumfahrt und im Werkzeugbau herzustellen. Die Materialqualifizierung kann je nach Anwendung oder Branche sehr zeitaufwändig und teuer sein. Der erste Schritt in diesem Prozess ist die Festlegung der grundlegenden Schmelzparameter, für die ausreichend Daten gesammelt werden müssen, um nachzuweisen, dass das Material wie gewünscht funktioniert.
Die Materialentwicklung für Metall-AM ist ein komplexer Prozess, der ein gründliches Verständnis der Schmelz- und Rückverfestigungstemperaturen und der entsprechenden Mikrostrukturen erfordert. Schmelzstrategien können mehrere spezifische Schwerpunkte haben, z. B. Teilequalität, Produktivität und spezifische Merkmale, so dass ein „Einheitsansatz“ nicht möglich ist. Bei der anwendungsspezifischen Produktentwicklung muss der Anwendungsfall des Kunden bei der Materialentwicklung von Anfang bis Ende im Auge behalten werden.
Die Aufnahme neuer Materialien in den bestehenden Katalog erfordert strenge Tests und Analysen, um sicherzustellen, dass das gedruckte Teil den Qualitätsanforderungen entspricht. Dies erfordert einen immensen Arbeitsaufwand bei der Festlegung und Ausführung der Druck-, Test- und Analyseprotokolle. In diesem Blog werden einige wichtige Überlegungen bei der Entwicklung von Schmelzparametern untersucht.
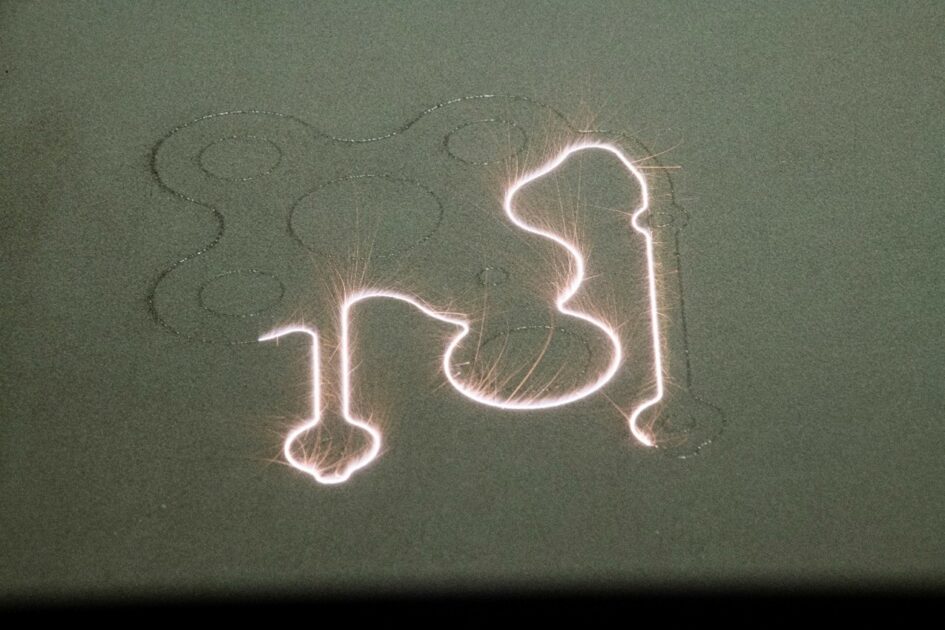
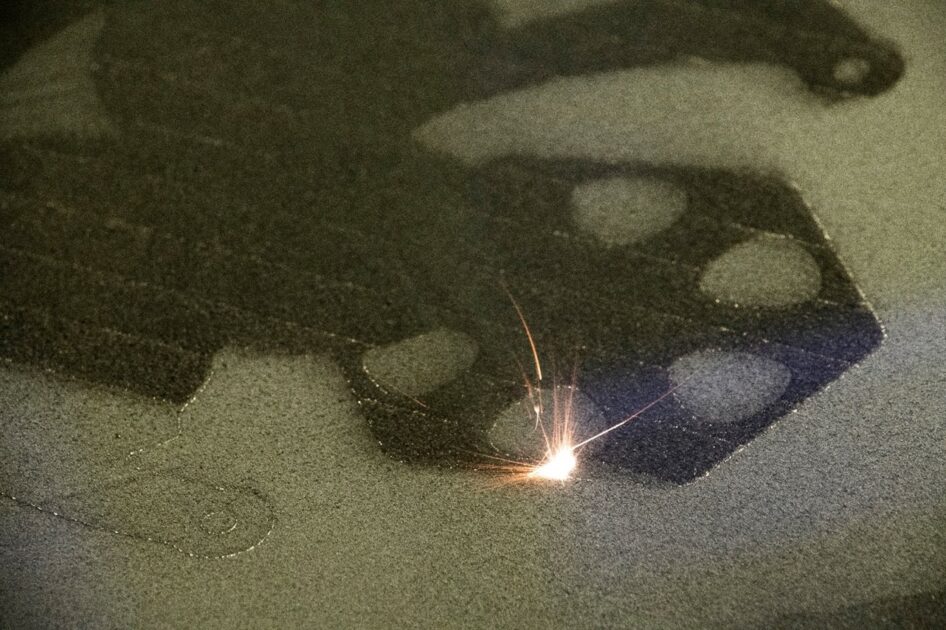
Eigenschaften des Rohstoffs
Die Auswahl des Ausgangsmaterials ist der erste und wichtigste Schritt im Metall-AM-Prozess. Schlüsseleigenschaften von Metallpulver wie Form, Größe, Fließfähigkeit und chemische Zusammensetzung tragen dazu bei, qualitativ hochwertige Teile herzustellen. Daher ist es wichtig, das richtige Pulver je nach der erforderlichen Funktionalität des Teils zu wählen.
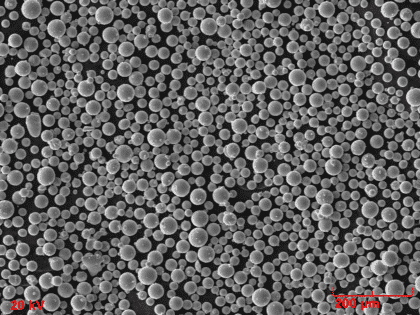
Melt Pool Abmessungen
Dieser Aspekt der Entwicklung misst die physikalischen Eigenschaften eines einzelnen Raupendurchgangs sowie die Schmelzbadabmessungen jeder einzelnen Raupe. Mit Hilfe eines statistisch gestützten experimentellen Ansatzes in Kombination mit Simulationsanalysen können die primären Schmelzparameter ermittelt werden, um die geeigneten Schmelzbadabmessungen zur Erreichung der erforderlichen Festkörperdichten zu erhalten.
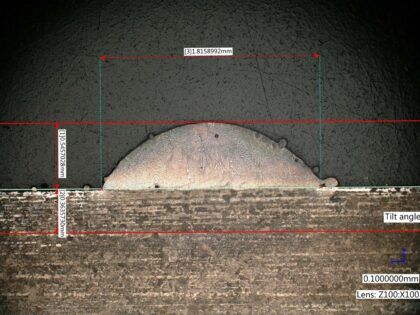
Feststoffteil-Dichte
Die Festkörperdichte ist ein Maß für die Porosität im Inneren eines gedruckten Teils und basiert auf der Einstellung einzelner Perlen, indem die Art und Weise, wie sie nebeneinander gedruckt werden, verändert wird. Die Schichtdicke und der Rotationswinkel des Laserscanners haben einen erheblichen Einfluss darauf, wie diese Schmelzgänge miteinander interagieren. Dies wirkt sich direkt auf die Dichte und die Mikrostrukturen der gedruckten Teile aus. Die Dichte fester Teile kann mit Techniken wie der Metallographie oder dem MicroCT-Scan geprüft werden.
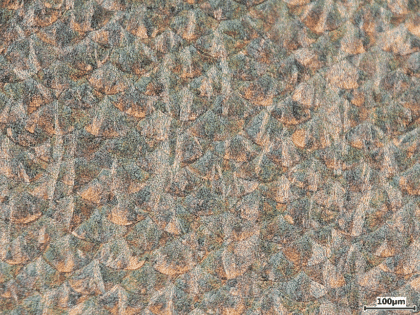
Leistung des Materials
Bei der Entwicklung neuer Schmelzparameter muss die Leistung des gedruckten Materials ausgiebig getestet werden. Dazu gehört die Erfassung physikalischer und mechanischer Daten aus verschiedenen Tests. Darüber hinaus müssen Verzug und andere Maßabweichungen des gedruckten Teils vor und nach den postthermischen Bedingungen geprüft werden. Dies trägt dazu bei, die Nebenprodukte der inneren Spannungen und die Wirksamkeit der postthermischen Bedingungen auf die Teilegeometrie zu verstehen.
Diese vorläufigen Daten zu Abmessungen, Dichte, Oberflächenbeschaffenheit und Zugfestigkeit bestätigen die Qualität der Schmelzstrategie, bevor ein teurer anwendungsspezifischer Qualifizierungsprozess durchgeführt wird.
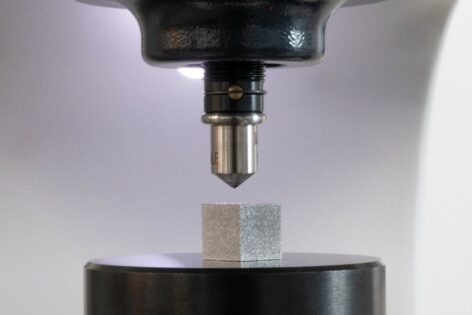
Spezifische Use-Case-Optimierung
Während für den Druck der meisten Teile optimierte Basis-Schmelzparameter erforderlich sind, müssen bei besonderen Qualitätsanforderungen zusätzliche Maßnahmen ergriffen werden. Es ist von entscheidender Bedeutung, dass die Anforderungen an die Teileproduktion/Qualität, wie Oberflächengüte, Produktivität, Merkmalsauflösung usw., bereits zu Beginn der Entwicklung berücksichtigt werden.
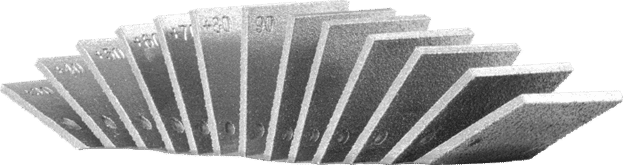
Der AddUp-Unterschied
Der Materialkatalog von AddUp umfasst eine vielfältige Mischung aus verschiedenen Stahl-, Titan-, Aluminium- und Inconel-Legierungen und mehr. Wir arbeiten kontinuierlich an der Entwicklung und Optimierung von Schmelzparametern für neue Materialien, um den Anforderungen der Industrie gerecht zu werden. AddUp nutzt einen vollständig datengesteuerten Ansatz und anwendungsspezifische Inputs bei der Entwicklung neuer Materialien oder Änderungen an den bestehenden Schmelzstrategien. Mit unserem Expertenteam für Werkstofftechnik in Verbindung mit unseren internen Prüfmöglichkeiten können wir schnell und effizient Schmelzstrategien für neue oder bestehende Werkstoffe entwickeln. Dabei sind wir offen für die Zusammenarbeit mit Industriepartnern und akademischen Forschern.
Sehen Sie sich dieses Video an, das einen Teil unseres Materialentwicklungsprozesses für Zeda in 17-4 PH Edelstahl in unserem AddUp Solution Center in Cincinnati, OH, zeigt.
Learn more about the capabilities of the FormUp 350.