Additively Manufactured Static Mixer | Blog
Read how AddUp’s roller recoater and finer powder particle size distribution (PSD) provides finer features, improved surface finish and eliminates the needs for supports when producing a static mixer.
Written by: Nick Estock, Director of Applications and Business Development
Additive Manufacturing, like any manufacturing process, has its strengths and weaknesses. All processes typically have value-added steps and necessary secondary operations that are a consequence of their shortcomings. Support structures are one of these necessary evils of AM. They are part of the process but add no value to the final part. In fact, they decrease the value because support structures consume material and machine time but then need to be removed after printing. All of this reduces productivity and ultimately costs you money. So, let’s eliminate them! (OK, maybe minimize them..)
AddUp, a joint venture between Michelin and Fives, developed a system to do just that. Michelin has been utilizing AM since the early 2000s, long before I even knew what a 3D printer was (we didn’t have 3d printers or even smartphones when I was in high school). Michelin utilized the technology first to reduce the development cycle for their tire mold inserts, called sipes. Today, they produce over one million of these sipes a year for their production molds. Critically important features to these sipes are: the resolution down to 0.2mm features, shallow overhangs as low as 15 degrees, and surface finish as low as 4 Ra um, as printed.
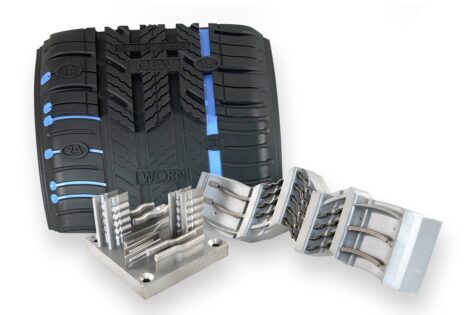
So, when Michelin embarked on this joint venture with Fives how did they achieve such a high level of quality? They did so by developing the FormUp 350 as the only industrial Powder Bed Fusion (PBF) machine to utilize a roller recoater in conjunction with a finer powder Particle Size Distribution (PSD). Typical PBF technologies use a PSD ranging from 25-63 um. The FormUp can effectively manage, distribute, and spread powders down to 5-25 um. By using finer powders and a roller, AddUp achieves a better packing density of their build bed up to 70% dense. Combine this with high quality open parameters and you have a recipe to build finer features, better surface finishes and yes less supports, hassle free and right out of the box! What do I mean “right out of the box”? I mean no secret sauce, no special parameters applied in certain areas, and no slowing down the process. Design it, apply your standard parameters, load it on the machine and go!
Let’s take a look an example, a static mixer our applications team developed to illustrate this point better.
What is a static mixer?
Wikipedia defines this as:
“a precision engineered device for the continuous mixing of fluid materials, without moving components.[1] Normally the fluids to be mixed are liquid, but static mixers can also be used to mix gas streams, disperse gas into liquid or blend immiscible liquids.”
In other words, it is a pipe where two or more fluids are introduced at the inlet and carried across a series of “static” elements such as plates or paddles to homogenize the fluids upon exit. Why is this a great additive application? Because you can optimize and customize the design for any given application. Why is a static mixer a difficult part to produce additively? Because the mixing elements pose a problem when printed using traditional AM guidelines. Standard design guidelines for AM means these elements would have to be printed at 45 degree angles. This limitation would require to either elongate the mixing region of the mixer itself and/or add many more elements to achieve the desired performance. Either of these options mean you are no longer leveraging the advantages of additive and what’s left is an ineffective expensive part.
Static Mixer with: | AddUp Static Mixer | Standard AM Guidelines (45˙ fins) | Reduction |
---|---|---|---|
Overall Height | 305 mm | 654 mm | 53% |
Material Needed | 738.5 cc | 1583.82 cc | 53% |
Build Time | 88 hours, 32 minutes | 189 hours, 51 minutes | 53% |
The AddUp Static Mixer increased productivity by 53%!
But, what if you didn’t have this limitation?
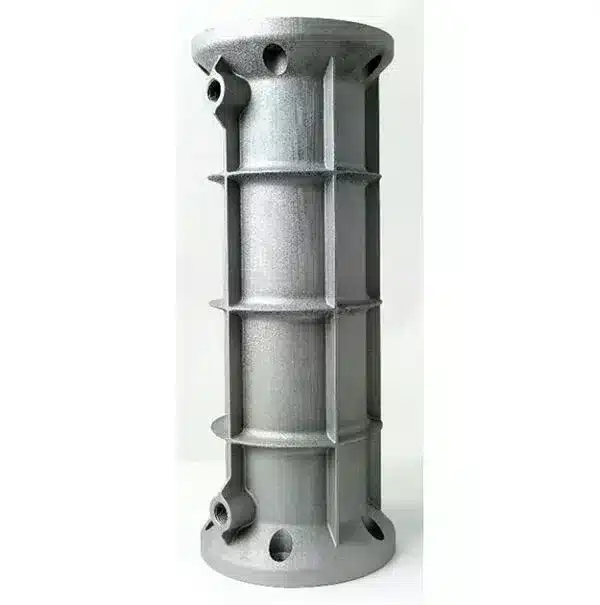
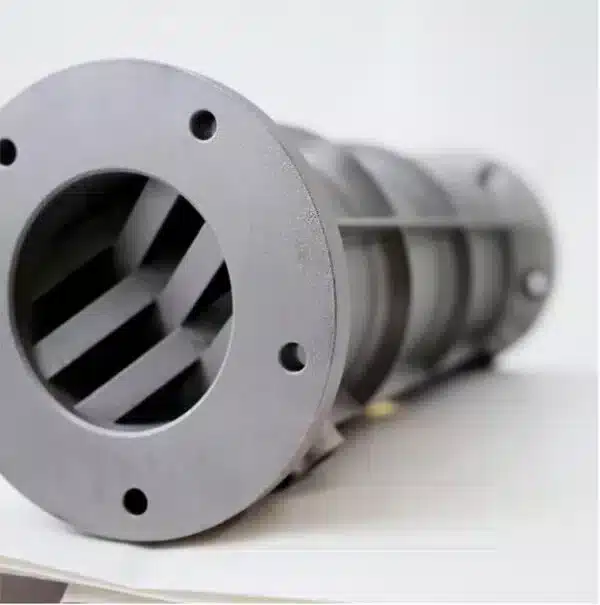
The static mixer shown here was printed without these limitations. Our engineers designed this mixer with elements as shallow as 25 degrees without any supports while still achieving an acceptable surface finish. Not only that but they designed it in less than two weeks and achieved a first-time yield. How was this possible? AddUp’s roller and fine powder configuration coupled with robust parameters provide new design freedoms for the AM process.
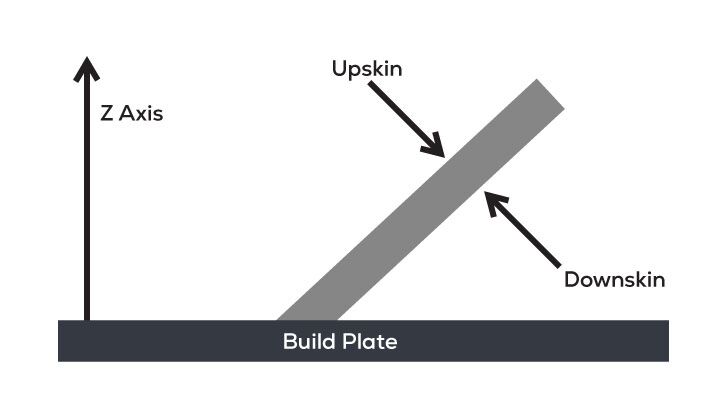
As shown in Exhibits A and B, using a roller system in conjunction with finer powder, the AddUp system can achieve a reduction in surface roughness by about 10 Ra um for any given upskin/downskin angle when compared to medium powder PSDs with blade recoater configurations.
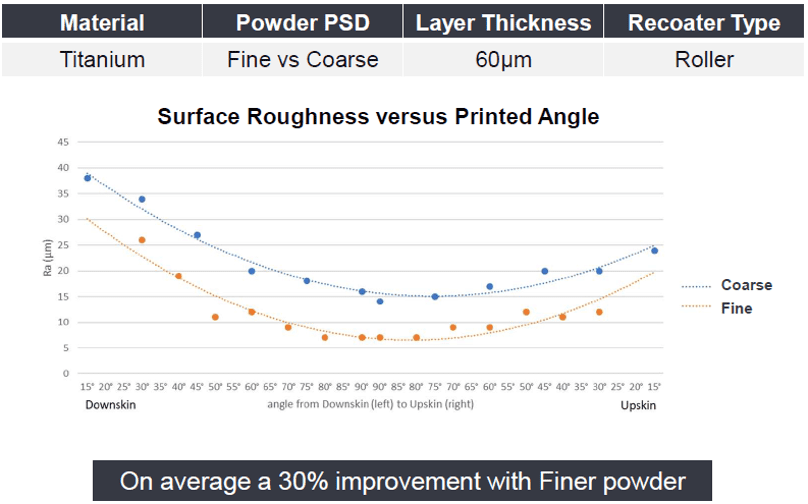
EXHIBIT A
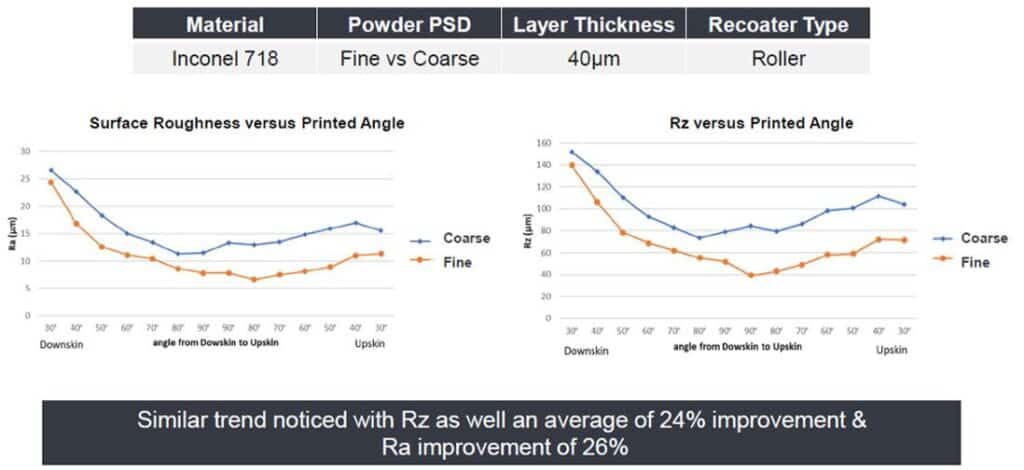
EXHIBIT B
Don’t forget, this was achieved right out of the box and hassle free! There are no special downskin parameters. There is no need for advanced development that can take months and countless hours of engineering and machine time to achieve. These results can be accomplished using our standard, highly productive, bulk and contour parameters. With other machine OEMs, enhanced surface finishes or extreme overhangs often come at the cost of slowing down your productivity. That’s because they are using less laser power at a reduced speed to achieve such results, thus slowing down your productivity. This also introduces additional variables into the mechanical properties of your part. Instead of having a singular set of parameters, yielding a known set of mechanical properties throughout the entire volume of your part, you have created areas that can potentially exhibit different behaviors. The AddUp system achieves these results thanks to a better packing density of our powder bed and our roller with fine powder configuration.
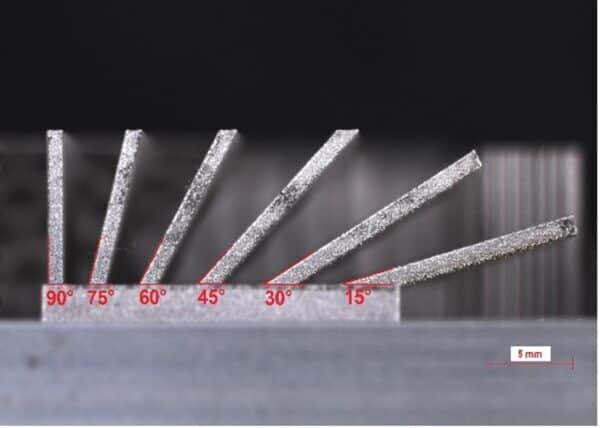
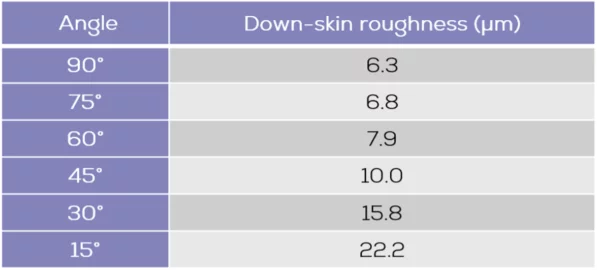
Think this is all too good to be true? Try me! We have just completed the renovation of our Cincinnati facility, serving not only as our US headquarters but also as a technical demonstration center. From powder to part, our workshop has the full capabilities to run benchmark, functional prototypes and even production parts. Our team is ready to support our customers just tip toeing into AM to turnkeying an industrialized application.
Use the form below to tell us about your project and we’ll show you the AddUp difference! We look forward to the opportunity to “un-support” your applications!