The goal of the project is to verify the technical and economic feasibility of additive manufacturing of complex geometric replacement parts for equipment that is no longer manufactured.
The project aims to verify the technical and economic feasibility of producing additive manufacturing spare parts with complex geometries for equipment that is no longer manufactured and historically sold complete. The equipment in question is a material transfer bridge and a steam distributor block.
OBJECTIVE
Demonstrate the technical and economic feasibility of metal additive manufacturing to produce spare parts
RESULTS
- Design and mechanical characteristics are identical to the original part.
- Reduced production costs, compared to traditional manufacturing (machining)
- Creation of a new and more agile supply chain
- Reduced stock of spare parts
Context
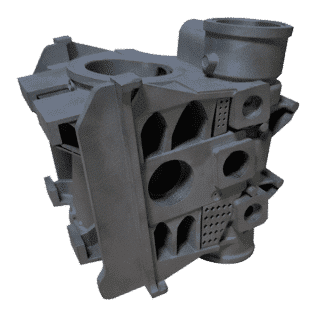
Different plants in the Orano group want their spare parts to be available at the right time and at a lower cost, to secure the installations and optimize their parts inventory management. In particular, the maintenance department of Orano Cycle Tricastin has to deal with the obsolescence of some equipment for which the supply time is very long. In the nuclear industry, the storage of spare parts for all those complex equipment represents an important investment.
The Project
The project aims to verify the technical and economic feasibility of additive manufacturing to produce metal parts with complex geometries for equipment that is no longer manufactured and historically sold complete. The equipment in question is a material transfer bridge and a steam distributor block.
To meet this demand, Orano needed to rely on a solid industrial group with a large machine pool and a mastery of the value chain. This is why Orano called upon AddUp, a French manufacturer of metal additive machines. The AddUp experts thus 3D printed, using PBF technology (Powder Bed Fusion – laser), nine models of 316L stainless steel parts as well as test specimens for mechanical tests (tensile and impact) and other quality controls.
Additive Manufacturing Benefits
- The cost of additive manufacturing compared to machining is lower: less material consumed, several parts printed on a single platform, and in a single operation.
- The ability to produce parts with complex geometry from a scanned model of the part (reverse engineering) for parts without a CAD file.
- The use of fine powder results in parts with high geometric accuracy and a good surface condition, even in internal channels.
Results
The full cost of producing 16 parts and 36 mechanical test specimens by additive manufacturing is equivalent to the cost of producing 3 parts by machining.
The AddUp Advantage
The use of fine powder with the FormUp350 machine allows for manufacturing parts with a good surface finish (especially for internal channels), as well as the creation of complex geometries. Control of the complete production chain: design, production, machining, post-processing, and inspection.