Interview of WBA and AddUp Managers to explain the background and goals of a joint initiative of creating an AM Tooling Competence Center at the WBA in early 2023.
Original Interview by Martin Ricchiuti of FORM+Werkzeug
The WBA Aachen Toolmaking Academy supports tool and mold makers in developing technological innovations for the industry. AddUp, a joint venture established by Michelin and Fives, is a global OEM of multi-technology production systems and a market leader in additive solutions.
In the FORM+Tool interview with Prof. Wolfgang Boos, Managing Partner of the WBA, and Julien Marcilly, Deputy Chief Executive Officer at AddUp, the background and goals of the joint initiative of an AM Tooling Competence Center at the WBA, which will start in early 2023, are explained will start.
Finding Additive Solutions: Easy Entry to Additive Manufacturing
AddUp will make its FormUp 350 additive manufacturing system based on the LPBF process available to the WBA. With additive manufacturing, the potential for local tool and mold making is to be tapped, and the process chain is further developed.
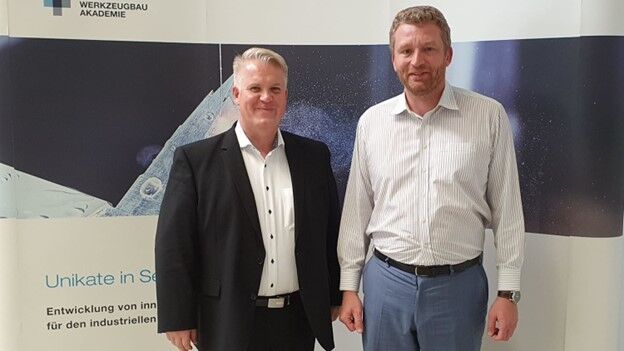
FORM+Tool: Mr. Marcilly, what are the goals of AddUp with the new AM Tooling Competence Center, and what role does AddUp play in the cooperation?
Marcilly: With our AddUp GmbH, founded in April 2022 in Aachen, we are pursuing the strategic goal of opening up the German market for metal 3D printing for us. So it is only logical to enter into a partnership with the WBA. We know that there is comprehensive competence for the needs of tool and mold making, which can make a significant contribution to further advancing acceptance among users and the technology itself. We will install our latest PBF system ‘FormUp 350‘ (Powder Bed Fusion), in a dedicated hall within the WBA’s demonstration tool shop and make it accessible to potential customers. Once the plant is installed, we will place three to four application engineers and plant operators there to accompany interested parties with their first steps with metal 3D printing on our system and on the way to the first required parts with all our know-how. In addition, further developments in PBF technology are to take place on this machine together with the experts from the WBA.
FW: Prof. Boos, is 3D printing a new field of technology for the WBA that you would like to develop with the support of AddUp?
Boos: So far, the focus at the WBA has been on the classic five technologies in toolmaking. However, about four years ago, together with the partners in our toolmaking community, we started to explore the market for 3D printing in a targeted manner for high-potential solutions for the requirements of toolmaking. We were very pleased when, in the context of corona-related digital workshops and discussions with AddUp, it became clear in 2021 that an AM Tooling Competence Center represents a win-win situation for both sides.
Because for the WBA, it is a compellingly logical step to introduce this sixth technology in tool and mold making. If a partner as strong as AddUp enters the community and also agrees to install a corresponding system on which you can not only improve and optimize parts but also the process together with experienced AddUp experts for the benefit of the user, then this is a remarkably successful constellation. We look forward to working closely with you.
FW: You talk about optimizing the PBF technology. What do you mean by that?
Boos: I think it’s essential to develop a feeling for handling the materials and what performance can be achieved with the systems under optimized conditions. At the same time, however, there are also issues, such as digitization, that need to be addressed. What can be implemented as a connection? You have to get to know a lot more about the material and process. We have therefore agreed that, in addition to the two partners, AddUp and WBA, we will also involve the entire community with around 85 companies.
In this way, a much larger number of impulses and ideas come about in terms of powder, process, components, and applications. In this way, requirements are defined that can be specifically tested. This is the ideal start to act together as a problem solver in the AM context.

FW: The equipment and staff come from AddUp; what does the WBA bring to the cooperation?
Boos: We are also contributing a 3D printing expert from the WBA who has accumulated expertise over the years. However, our focus will be on acquiring components and addressing tool and mold makers. AddUp acts as a partner who supports us in working out the best possible process for the production of all the required components. In addition, with our classic methods, we can complete the process chain in the context of post-processing of 3D-printed components. The AM Tooling Competence Center will have a unique selling proposition because we will cover the entire process chain right through to the ready-to-use 3D-printed tool component.
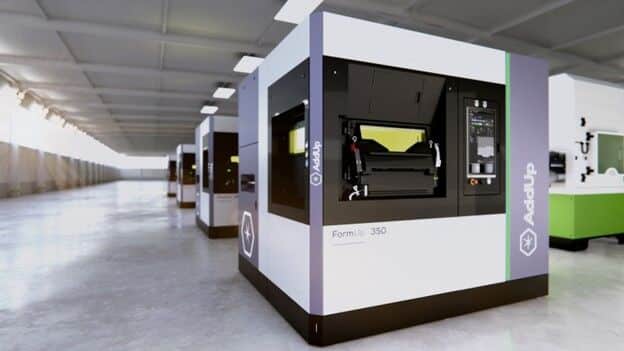
FW: To arouse the interest of tool and mold makers: What specific problem cases do you want to tackle?
Marcilly: There is enormous potential for use in terms of minimized cycle times in injection molding. Our system can process fine powder with a small grain size, which brings advantages in the production of conformal cooling channels and, as a result, increases the cost-effectiveness of injection molding. We have also already developed a new tool steel and manufactured the first parts, but this is just the beginning. We are in the process of developing special steels for mold inserts in the field of stamping and forming tool construction. Looking ahead, the focus is also on tools for medical technology applications and die-casting tools.
FW: How does this cooperation support the strategic orientation of the WBA, especially with the aforementioned topic of digitization?
Boos: For about five years, WBA’s range of services has included not only the five classic technologies in isolation but also the manufacture of individual components through to complete tools. This enables us to generate up to one million euros in sales per year. We will now expand this with the sixth technology in the form of a comprehensive consulting and manufacturing service for all aspects of 3D-printed metal components. From my point of view, this includes, in particular, the entire Industry 4.0 topic.
Where currently only structure-borne noise sensors or shot counters are integrated, I am convinced that we can reach a completely new level with appropriately printed 3D components and sensors integrated into them. There are still numerous approaches and research goals that we want to pursue together.
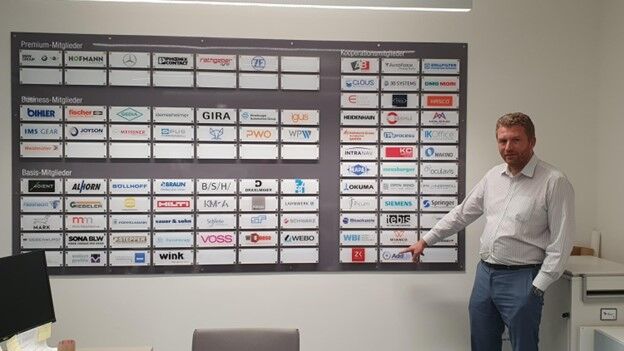
FW: What appeal is made to the tool and mold-making industry at this point?
Boos: A characteristic of the classic tool and mold maker is that he has to see it first to believe that it works. Choosing to start with the component you actually need would only make sense on a case-by-case basis because that requires previous knowledge, such as a design suitable for 3D printing. As a competence center, we want to develop unique solutions together with our customers. Our offer should be an ‘Easy Entry to Additive Manufacturing, with the appeal: “Call us, no matter what it is about in the context of 3D printing.”
Marcilly: The alternative would be for the customer to buy a system. That would be a huge investment to be able to do the first steps and experiments. In practice, this hurdle is too high. In contrast, here at the AM Tooling Competence Center is the machine with the combined expertise of Add Up and WBA, which the customer can use to try their hand at parts or test materials and designs. As a service provider, AddUp prints metal parts worth around 10 million euros in France, so there is already a lot of application expertise that you can tap into and that we make available. With the first experiences and successes, the step is an easy one to invest in your first own add-up system.
FW: When will the AM Tooling Competence Center go online?
Marcilly: The system is currently being installed. We are making a presentation at the AM Tooling Competence Center on October 25, 2022, with the first applications for our AddUp project and development partners. On October 26, all WBA members will receive a tour and presentation at the WBA Annual Meeting. The official opening is planned for early 2023 with a festive kick-off event.
Boos: It’s good that we already have a kind of pre-opening at the end of October for special AddUp customers and the WBA community. On October 27th, we also have the toolmaking colloquium with the EiP award ceremony. Here we can already set the first marker for companies open to new technologies.
Marcilly: We are also presenting the FormUp 350 at the Formnext trade fair in November and look forward to seeing interested parties at our stand E01 in hall 12.0.
FW: Thank you for the interview!
WBA Aachen Toolmaking Academy GmbH
D 52074 Aachen
info@werkzeugbau-akademie.de
www.werkzeugbau-akademie.de
AddUp Global additive solutions
F63118 CEBAZAT
contact@addupsolutions.com
Full interview in German read here