AddUp’s Metal Additive Manufacturing Resources
Your one-stop destination for a wealth of information, support, and expertise in metal additive manufacturing.
ADDUP ACADEMY
Learn from our experts about additive manufacturing or take a deep dive into our technology. AddUp Academy offers tailor made training paths for all levels of maturity on demand for your convenience.
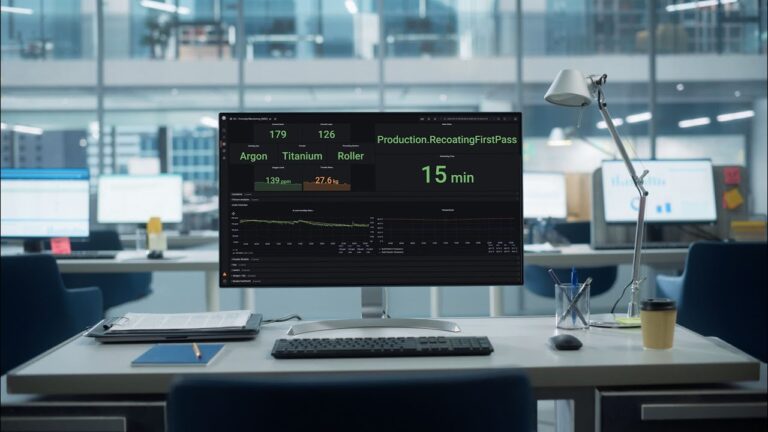
CUSTOMER PORTAL
AddUp’s customer portal brings together all the information related to your equipment. Submit service requests with traceability, manage your equipment including software and licenses, and access our knowledge base, all within this portal.
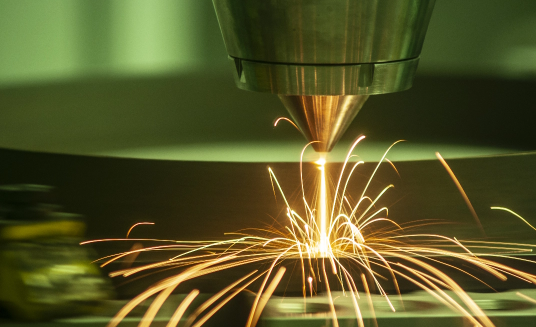
Step Into The Future Of Metal Manufacturing
Today’s metal 3D printers unlock designs impossible with conventional methods, offering unparalleled precision and complexity. Blending groundbreaking innovation and expertise, AddUp is leading the evolution of metal additive manufacturing
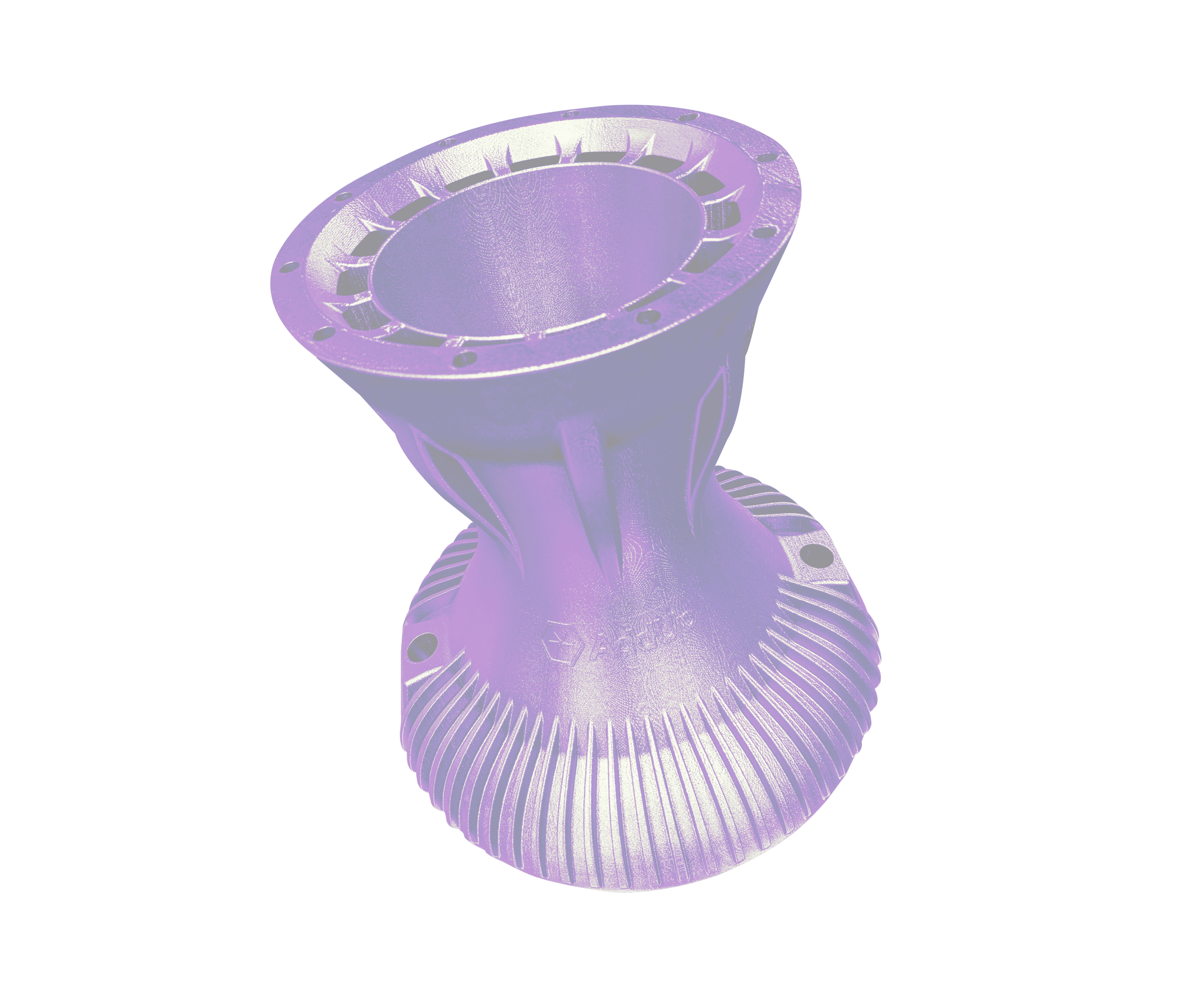