How reverse engineering process and metal 3D printing allow to produce an identical and durable strategic part for a boat.
CHALLENGE
Reproduce an identical part that is no longer in stock
SOLUTION
Reverse engineer the part (from a manual drawing to a digital CAD file) and additively manufacture it using the FormUp 350® Powder Bed Fusion machine from AddUp.
KEY BENEFITS
- Tolerances: +-0.4mm, depending on demand
- Similar mechanical characteristics, better durability
- Overall balance of the printed part maintained
Custom Shape
Lead Time
Integrated Features
Performance
Context
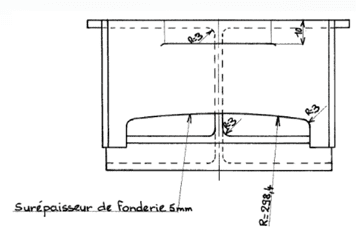
In 2018, the Ministry of the Armed Forces created the Defense Innovation Agency to promote innovation in the armed forces, with the priority to disseminate the latest technologies quickly. Under this driving force, the various services have all set up cells to boost innovation adapted to each profession. The Service de Soutien à la Flotte (Fleet Support Service), or SSF, in charge of piloting innovations for the maintenance of the French Navy’s fleet ships set up a similar initiative in 2020.
One of the French Navy’s challenges is to determine how to produce an out-of-stock part. To meet this demand, the Navy, the SSF, and the Service Logistique de la Marine (SLM, or Navy Logistics Service) needed a solid industrial group that has mastered the entire value chain. This is why the Navy turned to AddUp, a manufacturer of machines and parts, and an expert in metal 3D printing.
For the first test, the Navy chose an oil scraper for the propeller shaft line bearings of a Frigate, a part that plays an important role in the continuous lubrication of the bearings. This part is so essential for the operation of the Frigate and has the advantage of not presenting any critical mechanical stress for the safety of the ship, which authorizes such an experimental production attempt. Repeated contact with the splash plate and the bearing housing can lead to premature wear. This, along with the low stock of spare parts was a complementary and motivating factor for the choice of this part.
Additive Manufacturing Advantages
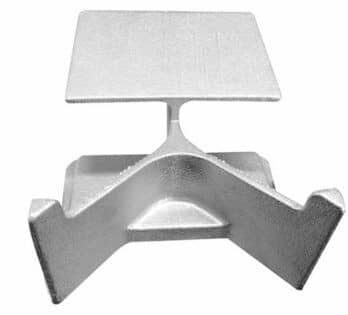
An identical part was 3D printed in aluminum. The original part was cast on a foundry layer and needed machining, which increased the production time. The new part was produced in one go, in one block, thus saving a significant amount of time. The use of a FormUp® 350 coupled with a fine powder coating roller has made it possible to produce a part with geometric precision and with a very good surface finish (superior to foundry) which has minimized the post-processing stages. AddUp has mastered the entire production chain: design, additive manufacturing, post-processing, and quality control.
“The experimentation of metal additive manufacturing with AddUp went well. The endurance tests on the ship were positive and AddUp is now referenced as a supplier of scrapers in the same way as other suppliers who produce this material using conventional techniques. The cost analysis shows that this production method is competitive. The delivery time is similar or even shorter. The collaboration was perfect and allows us to envisage other cases of application.” Jean-Marc QUENEZ French Navy Fleet Support Service Innovation