This case study explores the benefits of using 3D printed injection molds with optimized cooling channels. The project between Siebenwurst and AddUp aimed to improve productivity and quality in the injection molding process.
INDUSTRY
Tooling
CHALLENGE
To improve the inserts on a mold using AM technology to increase thermal performance and decrease cycle time
KEY BENEFITS
- Near-contour cooling in the insert
- Reduction of time and cost production
- Quality improvement of the molded parts
Creative Shape
Function Integration
Performance
What are the metal additive manufacturing benefits of a 3D printed injection mold? A mold slide enables complex forming in the injection molding process by moving into the mold before injecting the hot plastic and moving out again after cooling to eject parts from the finished plastic part. Here, a fast cooling time of the plastic plays a decisive role in achieving more productivity. Until now, cooling channels in the moving parts of molds could only be drilled in two directions crossing each other. AddUp has integrated AM-optimized cooling channels into the sliders to thus enable faster and safer demolding.
History: model and mold making at Siebenwurst
Since 1897, the Siebenwurst Group has stood for the highest quality in model and mold making. This unique expertise is characterized by tradition and innovation. An unbroken pioneering spirit, coupled with in-depth specialist knowledge, make Siebenwurst a sought-after development partner for industry and research today. With around 700 employees worldwide, the companies generate total sales of 100 millions euros at the locations like Dietfurt in the Altmühltal, Munich, Dillenburg, Rohr near Nuremberg, as well as in Mexico,
China and the USA.
Challenges of 3D printing design
Siebenwurst worked with AddUp on a WBA project, and the challenge was to design the cooling system specifically according to AM suggestions. Then Siebenwurts should simulate the new metal part geometry for functionality using Thermo software.
These were the points they struggled with using traditional manufacturing: Complex production using multiple different pieces of equipment, increasing processing time No control of near-contour temperature. Hotspots in the mold can be reduced via near-contour temperature control. Better temperature control leads to a reduced cycle time and increased productivity offsets any additional costs from the metal additive manufacturing process.
The result of injection molding is a plastic part with less warpage and better quality. With traditional manufacturing, the parts stay in the mold for longer to allow for adequate cooling to reach the desired temperature. Now, the parts are ejected at the same temperature, which corresponds to plastic solidification, but this temperature is attained in a shorter time.
This project between Siebenwurst and AddUp confirms that additive manufacturing brings added value economically and in terms of quality. Currently, the engineers are designing parts for conventional production and not yet taking advantage of all that additive manufacturing offers.
Using a traditionally produced original part, AddUp’s experts proposed a new design to incorporate efficient internal channels. Siebenwurst then performed a thermal simulation of the part, and AddUp adjusted the channel design according to the results.
Solution for AM-optimized cooling channels
AddUp has integrated AM-optimized cooling channels into the sliders to thus enable faster and safer demolding. Using the newest simulation software and thermal design optimization, it was possible to design the cooling channels perfectly prior to assembly.
Siebenwurst used PM420 / 1.2083, a standard tool steel that AddUp can process on their LPBF (Laser Powder Bed Fusion) machines. PM420 / 1.2083 is already common in plastic injection molding applications and well-known to mold makers.
Results and benefits of additive manufacturing
In addition to a hardness of 52HRC, this steel impresses with good corrosion resistance and also ease in polishing. Next, the new mold was produced on an AddUp’s PBF machine, the FormUp® 350 New Generation with a productive recipe using 4 lasers. Two parts were then 3D printed (1 normal + 1 opened) in 130 hours.
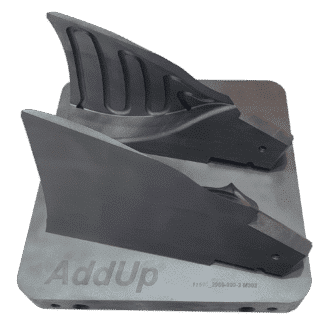
With the initial thermal simulation, AddUp was able to design channels as close as possible from the molding surface. The latest simulation shows that the new design descrase the hot spots by around 15°C ( 59°F ).
- Better thermal performance
- Cooling channel close to the surface
- Reduction of cycle time and defects
- Improvement of thermal homogeneity
Learn more about the Siebenwurst Group here.