Diese Fallstudie untersucht die Vorteile des Einsatzes von 3D-gedruckten Spritzgießwerkzeugen mit optimierten Kühlkanälen. Das Projekt zwischen Siebenwurst und AddUp zielte darauf ab, die Produktivität und Qualität im Spritzgießprozess zu verbessern.
INDUSTRY
Tooling
CHALLENGE
To improve the inserts on a mold using AM technology to increase thermal performance and decrease cycle time
KEY BENEFITS
- Near-contour cooling in the insert
- Reduction of time and cost production
- Quality improvement of the molded parts
Creative Shape
Function Integration
Performance
Welche Vorteile bietet eine 3D-gedruckte Spritzgussform für die additive Fertigung von Metall? Ein Formschieber ermöglicht eine komplexe Formgebung im Spritzgussverfahren, indem er vor dem Einspritzen des heißen Kunststoffs in d i e Form hineinfährt und nach dem Abkühlen wieder herausfährt, um Teile aus dem fertigen Kunststoffteil auszuwerfen. Dabei spielt eine schnelle Abkühlzeit des Kunststoffs eine entscheidende Rolle, um mehr Produktivität zu erreichen. Bisher konnten Kühlkanäle in den beweglichen Teilen von Werkzeugen nur in zwei sich kreuzenden Richtungen gebohrt werden. AddUp hat AM-optimierte Kühlkanäle in die Schieber integriert und ermöglicht so eine schnellere und sicherere Entformung.
Geschichte: Modell- und Formenbau bei Siebenwurst
Seit 1897 steht die Siebenwurst-Gruppe für höchste Qualität im Modell- und Formenbau. Diese einzigartige Kompetenz ist geprägt von Tradition und Innovation. Ein ungebrochener Pioniergeist, gepaart mit fundiertem Fachwissen, machen Siebenwurst heute zu einem gefragten Entwicklungspartner für Industrie und Forschung. Mit rund 700 Mitarbeitern weltweit erwirtschaften die Unternehmen an den Standorten Dietfurt im Altmühltal, München, Dillenburg, Rohr bei Nürnberg sowie in Mexiko, China und der USA einen Gesamtumsatz von 100 Millionen Euro.
Herausforderungen beim 3D-Druck
Siebenwurst arbeitete mit AddUp an einem WBA-Projekt, und die Herausforderung bestand darin, das Kühlsystem speziell nach AM-Vorschlägen zu gestalten. Anschließend sollte Siebenwurst die neue Metallteilgeometrie mit der Thermo-Software auf Funktionalität simulieren.
Dies waren die Punkte, mit denen sie bei der herkömmlichen Herstellung zu kämpfen hatten: Komplexe Produktion mit mehreren verschiedenen Geräten, was die Bearbeitungszeit verlängert Keine Kontrolle der konturnahen Temperatur. Hotspots in der Form können durch eine konturnahe Temperaturregelung reduziert werden. Eine bessere Temperaturkontrolle führt zu einer kürzeren Zykluszeit, und die erhöhte Produktivität gleicht d i e zusätzlichen Kosten des additiven Metallherstellungsprozesses aus.
Das Ergebnis des Spritzgießens ist ein Kunststoffteil mit weniger Verzug und besserer Qualität. Bei der herkömmlichen Herstellung verbleiben die Teile länger in der Form, damit sie ausreichend abkühlen können, um die gewünschte Temperatur zu erreichen. Jetzt werden die Teile bei der gleichen Temperatur ausgeworfen, die der Verfestigung des Kunststoffs entspricht, aber diese Temperatur wird in kürzerer Zeit erreicht.
Dieses Projekt zwischen Siebenwurst und AddUp bestätigt, dass die additive Fertigung einen wirtschaftlichen und qualitativen Mehrwert bringt. Derzeit konstruieren die Ingenieure Teile für die konventionelle Produktion und nutzen noch nicht alle Vorteile der additiven Fertigung.
Anhand eines traditionell hergestellten Originalteils schlugen die Experten von AddUp ein neues Design vor, das effiziente interne Kanäle enthielt. Siebenwurst führte dann eine thermische Simulation des Bauteils durch, und AddUp passte das Kanaldesign entsprechend den Ergebnissen an.
Lösung für AM-optimierte Kühlkanäle
AddUp hat AM-optimierte Kühlkanäle in die Schieber integriert, um so eine schnellere und sicherere Entformung zu ermöglichen. Mit Hilfe neuester Simulationssoftware und thermischer Designoptimierung war es möglich, die Kühlkanäle bereits vor der Montage perfekt zu gestalten.
Siebenwurst verwendete PM420 / 1.2083, einen Standardwerkzeugstahl, den AddUp auf seinen LPBF-Maschinen (Laser Powder Bed Fusion) verarbeiten kann. PM420 / 1.2083 ist im Kunststoffspritzguss bereits weit verbreitet und den Formenbauern bekannt.
Ergebnisse und Vorteile der additiven Fertigung
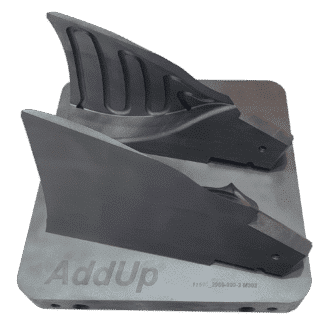
Neben einer Härte von 52HRC zeichnet sich dieser Stahl durch eine gute Korrosionsbeständigkeit aus und lässt sich zudem leicht polieren. Anschließend wurde die neue Form auf einer PBF-Maschine von AddUp, der FormUp® 350 New Generation, mit einem produktiven Rezept unter Verwendung von 4 Lasern hergestellt. Zwei Teile wurden dann in 130 Stunden 3D-gedruckt (1 normales + 1 geöffnetes).
Bei der ersten thermischen Simulation war AddUp in der Lage, die Kanäle so nah wie möglich an der Gussoberfläche zu entwerfen. Die neueste Simulation zeigt, dass das neue Design die heißen Stellen um etwa 15°C reduziert.
- Bessere thermische Leistung
- Kühlkanal nahe der Oberfläche
- Reduzierung von Zykluszeit und Defekten
- Verbesserung der thermischen Homogenität
Erfahren Sie mehr über die Siebenwurst Gruppe hier.