Across all of manufacturing, safety should be a top priority. That certainly holds true in the much newer world of metal additive manufacturing. In our realm, the majority of risks come from using metal powder – both in its raw form and the condensate byproduct it produces during the melting process. Using a fine feedstock, with the smallest particles being on the order of 1 micron, allows for fine features and other design freedoms but also presents most of the safety risks we face in Powder Bed Fusion. Michelin launched AddUp to drive the future of Powder Bed Fusion, and here we will look at their influence in improving the safety features on the newest fleets of machines.
Metal powder in it’s raw form is a hazard to the touch and through the air. Some particles are fine enough that human skin does not serve as a barrier, so the powder acts as a vessel for heavy metals to work their way inside the body. Finer particles also hang in the air for longer, where it becomes possible to enter through the lungs. With employee and customer safety always being front-of-mind at AddUp, the design of any 3D Printer being used in their facilities had to mitigate these health risks for their employees.
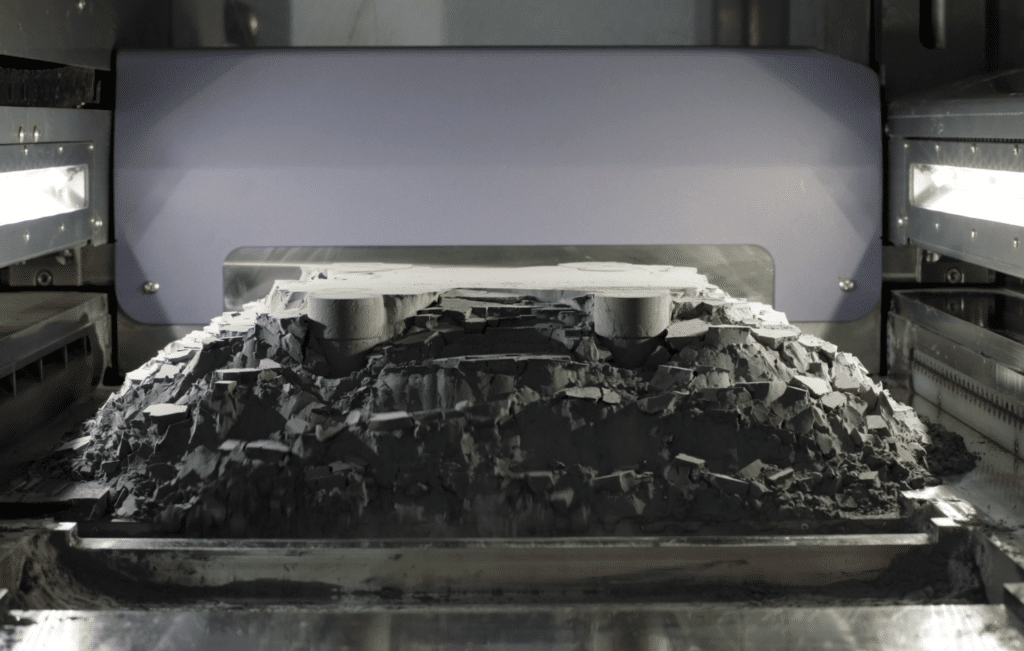
The question shifts to How can you minimize operator exposure to powder without sacrificing any functionality on the machine? AddUp’s answer is the Autonomous Powder Module, the powder handling system on the Form Up 350. The main components in the APM are the Glovebox, Hopper, Sieve Unit, and Feeding System, all of which are kept inert. Powder is loaded through the glovebox of the APM and is transferred via vacuum suction to the Hopper, which has a capacity of 59L. Prior to a build, powder will move from the Hopper and through the Sieve, with the Feeding System providing the sieved powder to the interior of the Form Up’s build chamber.
After the build completes the operator vacuums the remaining powder with an interior nozzle, sending that material back to the Hopper where it can be used for the next build. The APM contributes to maintaining a safe environment by separating the operator from the powder and keeping the powder away from oxygen at all times.
The single most dangerous product of Powder Bed Fusion is the condensate formed during the melting process. Condensate is flammable, an explosion risk, and readily reacts with oxygen – with the worst case scenario being when Titanium is the base material. A common solution is paper filters, but those must be serviced and replaced by a human. These filter changes are a source of many of the safety incidents. That risk inspired AddUp to move away from paper filters and partner with Herding Filtration. With the Herding system, fumes are collected in the Fluid Module and dispensed into a metal dust bin (both of which are kept inert). In addition to the condensate, Calcium Carbonate is used to passivate the hazardous substance and inhibit any sort of reaction. Swapping out the dust bin is a simple process that takes 1-2 minutes, and is much safer than changing a filter. Dust bins are replaced about twice a month, depending on machine usage, and the remainder of the Fluid Module can go multiple years without being serviced.
Powder management may be the most important aspect of safety in Metal AM, but other machine features can encourage a safe workplace as well. As the industry grew and expert users arose, their feedback was used to incorporate ideas that addressed their pain points. AddUp made cleaning the interior of the build chamber easier by incorporating multiple access doors. This allows for the entirety of the inside to be wiped down and thoroughly cleaned without uncomfortably stretching for the back corners. Similarly, the laser lenses are removable so that they can be cleaned outside the machine. From a software perspective, oxygen setpoints and alarms are set during creation of the build file so that they can be customized to alert the operator of any potential issue, or shut down if it becomes a safety issue.
As with any promising new technology, Metal Additive Technology has extremely enticing benefits. The industry is constantly trying to extract all they can from these machines without putting anyone at risk. Machines and processes should all be designed with safety in mind, but even advanced safeguards don’t replace responsible operators, proper PPE, and an appropriate facility setup. Watch the video below to see how we’ve integrated safety into the AddUp Solution Center in Cincinnati, Ohio.