When DED technology allows printing parts with complex shapes without additional tooling.
A Greek manufacturer Spyros Panopoulos Automotive has asked AddUp to produce 3D-printed parts, including a 5-in-1 manifold. The challenge for AddUp was to create a design and 3D print of the entire system. Read the case study about how DED technology allows printing parts with complex shapes without additional tooling.
INDUSTRY
Motorsport – Automotive
CHALLENGE
To 3D print an innovative 5-in-1 manifold to optimize engine performance
KEY BENEFITS
- Complex geometry
- Printed part in one go
- Resistance to high temperatures
Printed In One Go
Creative Shape
Performance
History
The Greek manufacturer Spyros Panopoulos Automotive is working on the development of the first Ultracar in the world, named Chaos, that can speed up from 0 to 100 km/h in only 1.55 s. This pure performance is better than Formula 1. To push these boundaries, this exceptional car must be lightened significantly while keeping its high mechanical integrity. To achieve this goal, Spyros has asked AddUp to produce 3D-printed parts, including a 5-in-1 manifold.
The more advanced the engine, the more important the impact of the exhaust system carries on the overall engine performance. The exhaust system is a set of metal pipes that carry exhaust gases from the cylinder head to the outside of the vehicle. The exhaust manifold refers to the area where the primary pipes (from the cylinder head to the manifold) join to form a single pipe called the exhaust pipe. To improve the efficiency of the engine, the exhaust system must be optimized in terms of gas flow and acoustics – the movement of sound waves within the exhaust system itself.
Challenges
The challenge is to improve both the performance of the primary manifolds and the collector. In addition to streamlining the different gas flows into the exhaust to limit pressure losses, we must adjust the lengths and bending radii of each of the primary manifolds. These design changes will allow the engine to empty and fill much more efficiently to increase the torque, especially at high speeds. The challenge for AddUp will be to create the design and 3D print the entire system (primary plus collector).
SOLUTIONS
According to the conventional method, these collectors are usually manufactured in boiler making (bent tubes, welded tubes…) which is limited to using tubes of constant thickness and simple cross-sections.
Another drawback is these methods require tooling as well. The welds and other assemblies can fail at the introduced weak points because they are subject to high thermo mechanical stresses. With additive manufacturing, the entire system is printed in one go, so there is less risk of failure during operation.
As the part was large (380 mm x 240 mm), the AddUp experts chose to produce it on a Modulo 400 machine, using DED technology (directed energy deposition). DED is an additive process where metal feedstock (powder or wire) is fused onto a substrate or existing part with an energy source, often a laser. On the Modulo 400, a nozzle replaces a spindle on a 5-axis CNC mill, with the metal powder and laser beam aimed through different channels on the nozzle to meet and add material to the substrate or existing part.
DED technology allows printing part with complex shapes such as a changing cross-section and variable wall thickness, without using additional tooling. These features are difficult, if not impossible, to recreate outside of additive manufacturing.
Results
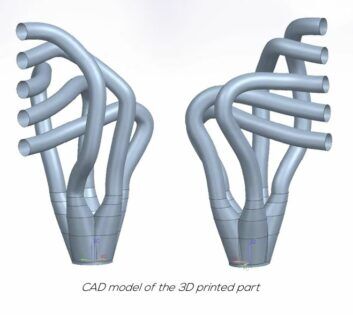
The selected metal for the manifolds is Inconel® 718, a superalloy with good oxidation resistance and high mechanical properties even above 800°C. To achieve maximum performance, the engines must operate at high temperatures and under high stresses; the characteristics of Inconel 718 allow the engineers to design a part that clears these obstacles while implementing a geometry with high performance in mind.
The choice of the DED tackles a dual issue of size and cost. The Modulo 400 is equipped with a small 10 Vx nozzle, which allowed us to obtain good surface quality across every feature of the large part. The final part, after 15 hours of production, has a 1 mm wall thickness and a constant cross-section but variable geometry along a tube with small radii of curvature. This type of result is impossible to obtain with a conventional method.