AddUp’s FormUp 350 additive manufacturing technology revolutionizes acetabular cup production by offering efficient Laser Powder Bed Fusion (LPBF) capabilities that outperform traditional methods and Electron Beam Technology (EBM).
Introduction
Acetabular cups, essential components of total hip replacements, have traditionally been manufactured through casting and forging. Although effective, this method was cumbersome and costly, necessitating long lead times and complex validations. However, AddUp’s groundbreaking FormUp 350 has transformed this narrative, showcasing how additive manufacturing technologies can revolutionize the field.
Traditional Manufacturing Process
Historically, the production of acetabular cups relied on the lost wax method, a labor-intensive process resulting in slow turnaround times and additional, costly processing stages. The final product required a porous structure that was both expensive to manufacture and challenging to validate, posing a significant hurdle to progress in the field.
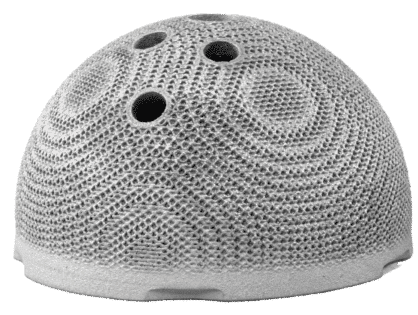
The Advent of Additive Manufacturing and the Limitations of Electron Beam Technology
Additive manufacturing brought a significant shift in acetabular cup production, with Electron Beam Technology (EBM) offering a promising alternative to traditional methods. However, EBM presented challenges, such as unpredictable failures and complex validation processes, which could escalate the overall time and cost of production.
The Game-Changing Impact of AddUp’s FormUp 350: A Superior Leap in Acetabular Cup Manufacturing
In the pursuit of more efficient and precise manufacturing methods, AddUp’s FormUp 350 has emerged as a superior alternative to EBM. This innovative machine, operating on Laser Powder Bed Fusion (LPBF) technology, delivers closer net shape parts with no supports needed, dramatically reducing post-processing and lead times. It offers a larger build plate and more lasers than EBM printers, potentially doubling the throughput and optimizing production processes.
Notably, the FormUp 350 features a fine feature resolution and a roller recoater, enabling the printing of a lattice structure within the implant. This key feature significantly enhances osseointegration, leading to longer-lasting implants and improved patient outcomes.
Revolutionizing the Medical Device Industry: The Impact of FormUp 350
AddUp’s FormUp 350 has profoundly impacted the medical device industry. By shortening lead times and enhancing precision, this machine enables manufacturers to respond swiftly to market demands and deliver superior quality products. The capability to print lattice structures not only enhances the performance of the implants but also improves patient outcomes. This development leads to fewer revision surgeries, resulting in cost savings for both patients and healthcare providers.
Conclusion
The FormUp 350 from AddUp delivers throughput capabilities currently unchallenged on the market. This can be seen in the below Hip Cup Productivity Study. Parts shown were printed with a compression roller technology in 30um layers of Ti6Al4V ELI. Compared to EBM technology, the AddUp 350 has a shorter run time of 12:41 compared to 15:23 (EBM) which leads to an improved annual throughput of 9,309 (16,403 LPBF, 7,094 EBM). As the medical device industry continues to evolve, this concrete evidence of the FormUp 350’s superiority underscores its transformative potential in the future of hip replacement surgeries and beyond.