WHY ADDUP
AddUp is an expert of two metal AM technologies built off more than 200 years of industrial experience. When you choose AddUp, you’ll experience best in class safety on a repeatable, reliable platform. AddUp machines offer a host of technological advantages working in synergy to produce the very best products – without compromising quality or productivity.

Proud Heritage
AddUp combines Michelin’s expertise in industrial part manufacturing with Fives expertise in industrial machine design. We understand the world of manufacturing because we were born from it.
Proven Track Record
Our machines are repeatable and reliable. Every day parts are produced on AddUp machines. You can find them on satellites, aircrafts, trains, automobiles and even in the human body.

Better Surface Finish
Thanks to our roller recoater technology, you achieve a smoother surface finish with fine features and less supports, reducing your need for post-processing.

Open Parameter Machines
Some competitors keep the workings of their machines secret, but we don’t. Do more with our open platform where you can easily twist and turn the knobs as you see fit.
Safer Powder Handling
Our Autonomous Power Module (APM) takes care of the full powder management, limiting exposure to powder and making our machines safer for operators.
Quality Assurance Software
Our comprehensive suite of AM software and most advanced technologies offer traceability to provide you increased confidence in part quality.
“The AddUp team has proven to live within their proclaimed values… delivering a beneficial experience, being a trusted partner, and encouraging innovation. As I navigate through projects, I have been impressed with the level of attentiveness and service they exhibit. Each interaction is laced with education, professionalism, and care.”
Shannon VanDeren
“Too often partnerships are constrained by mistrust and an unwillingness to share information, but the AddUp team has really committed to the partnership with open minds and a shared goal to drive towards large scale part production. Not to mention the FormUp opens the door to productivity improvements with its quad laser setup, open parameters, and long-life filter.”
Rachel Levine
“With AddUp as a partner, we are trying to push metal 3D printing technology to its limits in terms of part sizes and associated material health. The quality of AddUp’s printing systems as well as the expertise and motivation of the teams have allowed us to move forward in an open and efficient way.”
Francois Billig
“We chose AddUp as our machinery partner for our recent project due to their High-Quality Products and Innovative Technology. AddUp’s commitment to research and development leads to cutting-edge solutions, like the Modulo 400 system, which offers versatility and high-quality results. This aligns perfectly with our vision at the Application Center for Additive Manufacturing at Research Institutes of Sweden AB, where we aim to lead in applied research and collaborate on new materials and solutions for the market.”
Seyed Hosseini
“As an early adopter of AddUp machines, I really appreciate capabilities and proactive team spirit, to deliverer parts in a serial mode.”
Aurelien Fussel
“The only French manufacturer of powder bed laser fusion machines (LPB-F) offering rare expertise both on the process and its applications with a machine capable of safely producing high quality parts in a repeatable and reliable way.”
Jean-Christophe Augé
CERTIFICATIONS
AddUp operates with a strong focus on quality, efficiency and customer-centricity. AddUp’s processes and systems have been reviewed and validated for compliance to applicable ISO standards. We hold multiple certifications around the globe and can help speed up the process of qualifying your part applications based on the needs for your specific industry.
Industries We Serve
INDUSTRY FOCUSOur machines were designed to provide maximum productivity and throughput in a serial manufacturing environment. Our reliable and repeatable platform coupled with in-process monitoring solutions provide peace of mind for manufacturers across a variety of industries and applications.
INDUSTRY FOCUSMedical
Producing implants or other medical applications requires numerous regulatory approvals. Additive manufacturing makes it possible to produce unique, customized metal medical parts in a short time and at a reasonable price.
TOOLING & MOLDING
Parts made through additive manufacturing can work more efficiently, like by increasing cooling. Metal 3D printing can also increase productivity by allowing you to print proof of concepts and finalized designs on demand.
AEROSPACE & AERONAUTICS
Our industry-qualified metal 3D printers can produce lighter parts that can be safely used on aircraft. We have also partnered with a renowned aeronautical engineering firm dedicated to the industrialization of metal additive manufacturing projects for the aeronautics, space, and defense industries.
OTHER INDUSTRIES
Additive manufacturing allows manufacturers across industries to produce innovative parts that they couldn’t make through traditional manufacturing.
Get Started on your AM Journey
Realize the potential digital manufacturing has to offer. Get started with AddUp and learn how AM delivers innovative solutions to solve manufacturers toughest challenges.
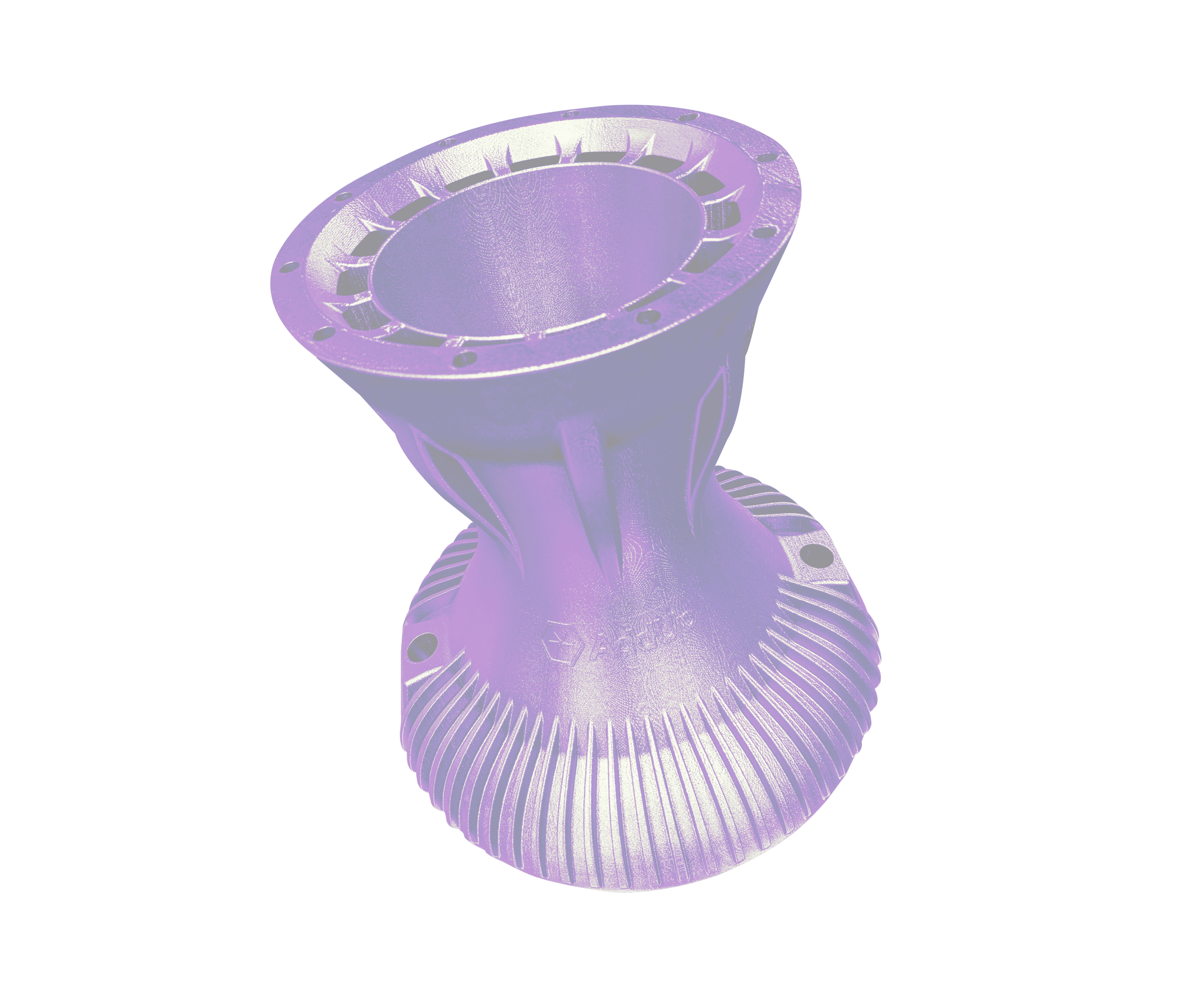