25,000+
Implants used each year that are the result of 3D printing
20+
tibial trays are printed in less than a day
10000
Annual Throughput* per 4 laser AddUp FormUp® 350
16.76
Medium, 30μm powder (hrs)* per 4 laser AddUp FormUp® 350
This case study focuses on tibia trays in orthopedic manufacturing and the challenges faced in producing highly complex and customized implants. Additive Manufacturing (AM) using biocompatible materials like titanium offers a solution by allowing the production of unique implants in a shorter time frame.
INDUSTRY
Medical
CHALLENGE
3D print a plate of tibia implants in Titanium
KEY BENEFITS
- 3D Print customized metal parts
- Titanium is a durable & biocompatible material
- Quality and productivity improved
Custom Shape
Reduced Lead Time
Weight Reduction
Performance
History
To ensure the best possible patient care, modern medicine must explore the forefront of technology. The medical industry has demanding requirements: complexity, precision of parts, customization, biocompatible materials, and durability. One of the challenges in orthopedic manufacturing is to create an implant that has the capability to quickly integrate into the human body. This is called osseointegration and is not easily accomplished with standard manufacturing practices today. Some of these devices are specifically tuned to the patient’s specific need. These devices or implants used during surgery can be customized but require extensive development time and that is not always to the patient’s advantage. Additive Manufacturing (AM) makes it possible to produce unique, customized metal parts in a shortened time and at a reasonable price. There are more than 25,000 implants used each year that are the result of 3D printing. The most common material used in this process is titanium as it is one of the few materials that is both durable and acceptable to the human body. For all of these reasons, the medical field is a key industry leading the utilization that of AM technology today.
Challenges
The purpose of an orthopedic implant is to replace a bone function seamlessly for the duration of the patient’s life. To accomplish this, the implant must fully integrate with the patient’s bone and tissue structure. If traditional production methods are used, providing such implants and patient matched devices can be very expensive and time-consuming. Thanks to the advanced biocompatible materials available for use in AM, more and more medical applications are benefiting from this technology. Because of their geometric complexity and need for biocompatible material, these medical parts designed by OEM’s globally are impossible to manufacture using conventional processes.
The spine industry has been utilizing AM on a mass scale for years. This is thanks to the size and quantity of implants which can be situated onto a build plate coupled with the volume of implants needed needed by the market. The next medical application emerging for AM success are tibial trays. The challenge for tibial trays is that the throughput of standard AM machines makes the idea of producing enough implants of varying sizes and shapes improbable. The overarching need is to have a printer that can make enough tibial trays to meet OEM demands. Typical build plates can only hold 9-12 tibial trays. This is not conducive to meeting industry demands without adding a significant amount of capital equipment. Consider that the average size build plate industry wide is about 290 millimeters (11.5 inches) squared.
SOLUTIONS
AM technology can print highly complex and customized medical parts using a lattice structure to improve osseointegration, expedite production time and improve surface finish to reduce post-processing. AM allows for geometric complexity to create lattice structures for medical implants which creates a porous surface to improve bone integration while simultaneously reducing the weight of the implant. For traditional manufacturing, to achieve osseointegration it may be necessary to apply a coating to the titanium, which is expensive, time consuming, and difficult to validate. Additionally, AM reduces the manufacturing steps and number of components, therefore cutting down production times and costs.
The AddUp FormUp® 350, a metal 3D printer using powder bed fusion (PBF) technology, showcases its capabilities through the quality and productivity output for tibia trays.
The build plate on the AddUp FormUp® 350 is 350 millimeters squared and can hold more than two times the tibial trays compared to typical build plates available. The use of 4 lasers also offers a distinct advantage allowing 20+ tibial trays to be printed in less than a day. Throughput is such an integral part of manufacturing today. When space is limited and demand is high, machines like the AddUp FormUp® 350 are a welcomed technological addition. The FormUp 350 utilizes a powder roller technology which allows for geometric complexity using minimal supports and results in optimal surface finish and a reduction in post-process machining. This reduction saves time and overall production costs.
Results
The tibia tray implant manufactured on the FormUp 350 delivered a porous structure and optimal surface finish to improve overall bone integration. The extended build plate and powder roller technology allowed for increased production as well as time and cost savings thanks to less post-processing.
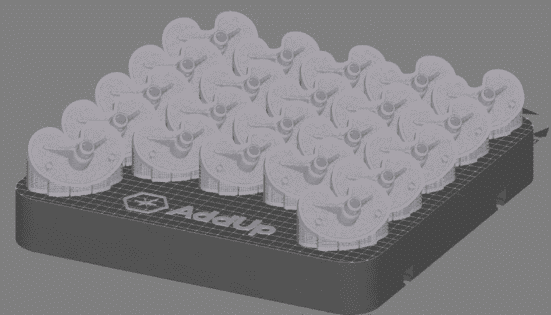
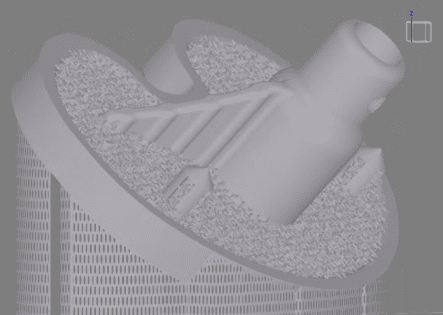
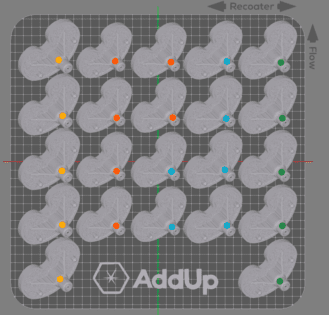
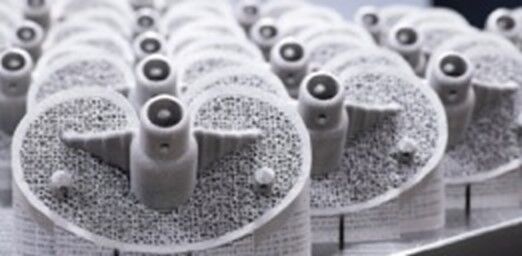
ANNUAL THROUGHPUT PER LASER BAR GRAPH
Running 1 shift per day for 52 weeks per year 1-1.5hrs from laser off to laser on (build flip)
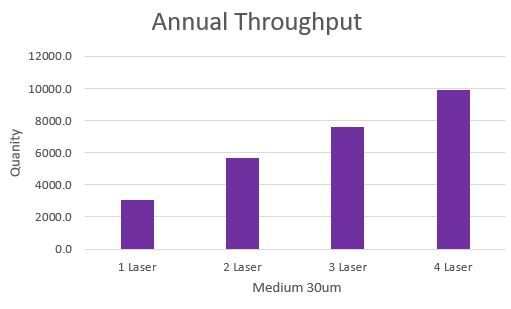
Increased production – larger build plate, fewer components and fewer manufacturing steps, including less post-processing, means production times are shortened!
Geometric complexity – the AddUp FormUp® 350 offers the freedom to design implants to be geometrically optimized using lattice structures and overhangs, all with minimal support structures.
Reduction in support structures – with the AddUp FormUp® 350, extensive support structures are no longer required, resulting in less post-processing machining, and therefore saving time and costs!
Optimal surface finish – thanks to the powder roller technology on the FormUp 350, the surface finish is ideal directly off the printer, resulting in less post-processing time and costs!
Functional integration – the AM process and materials create a porous structure and ideal surface finish which improves overall bone integration for medical applications.
Biocompatible materials – the FormUp 350 allows a variety of different materials to be used and has already optimized Ti64ELI at both 30 and 60 micron layers.
The FormUp 350 machine is ideal for medical applications because it provides an improved and cost-effective process to mass-manufacture highly complex and/or customized medical parts.
Volume
- Individual part: 25.604 cm3
- Full Build Plate: 25.604cm3 * 22 parts = 563.288 cm3
Bounding Box
- With orientation (image): 86.7 mm x 56.7 mm x 52.4 mm (XxYxZ)
1 LASER | 2 LASER | 3 LASER | 4 LASER | |
---|---|---|---|---|
Parts built per laser | 22 parts | 11 parts | 7-8 parts | 5-6 parts |
Time to build with 30-micron medium powder (melting + recoating) | 49.36 hours | 28.92 hours | 20.91 hours | 16.76 hours |
Medium, 30um powder (hrs) | 49.36 | 28.92 | 20.91 | 16.76 |
Annual throughput | 2612 | 4424 | 6077 | 7536 |