An additively manufactured camera support, designed to withstand acceleration and vibration during launch to space and to hold a camera and its lens in position during the production phases of a metal 3D printer.
“Metal3D“ project objective is to characterize the mechanical properties of a material shaped in microgravity. To carry out this experiment, two batches of test specimens are being produced by the same printer design. While the first batch will be produced in Toulouse in terrestrial gravity, the second will be built in space, more precisely in the Columbus module of the ISS (International Space Station), in microgravity.
GOAL
Position and hold a camera and its lens in position during the flight and manufacturing phases
APPLICATION
3 positioning axes for precise camera field adjustment. Designed to withstand acceleration and vibration during launch
CONTEXT:
“METAL3D“ PROJECT
MASS:
70 g
Mission
“Metal3D“ is a mission commissioned by ESA (European Space Agency) as a technology demonstrator. Its objective is to characterize the mechanical properties of a material shaped in microgravity. To carry out this experiment, two batches of test specimens are being produced by the same printer design. While the first batch will be produced in Toulouse in terrestrial gravity, the second will be built in space, more precisely in the Columbus module of the ISS (International Space Station), in microgravity. To produce these two prints, we have designed and manufactured two identical copies of a metal 3D printing machine capable of operating in both environments. The printer we have designed for this mission will therefore be the first to print metal parts in space.
Process
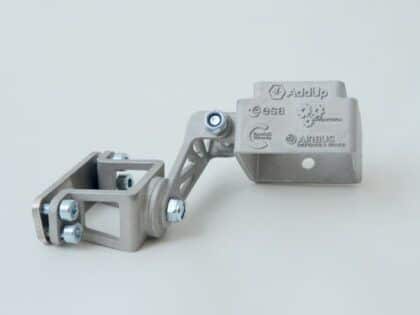
In the absence of gravity, the majority of current additive manufacturing processes are no longer usable. To make microgravity manufacturing possible, we choose to exploit the forces induced by surface tension. We use a laser as the energy source and steel wire as the raw material. The laser heats the substrate to create a liquid bath. In this liquid bath, we immerse the steel wire. By pushing the wire into the liquid bath, the latter also liquefies and increases the volume of the fusion bath. We then move the laser and therefore the liquid bath to the surface of the substrate while unwinding the wire in this bath so as to create a bead once the liquid bath has solidified. A layer is made up of one or more beads depending on the geometry of the part to be produced. Once the layer is finished, the process starts again using the previous layer as a substrate. In this way, layer by layer, a volumetric part is created.
For the process, we use a 316L wire. The laser and wire are fixed in the machine frame, it is the tabletop that is made mobile through 3 linear axes and 1 rotary axis. The machine is operated under nitrogen in order to limit the oxidation of the material and prevent the risk of combustion. As the access to nitrogen is limited in the ISS, this atmosphere is recycled throughout the manufacturing process by filtration and cooling.
Partners
The mission is being piloted by the Airbus Defense & Space teams. Cranfield University provides the laser, the optical chain, and the wire supply system to the system. Hightech provides the machine enclosure, which provides a sealed and cooling system, and the interfaces between the machine and the rack to which it is connected. Airbus, in addition to piloting the project, is managing the electronic and safety aspects of the machine.
On the mechanical side, AddUp is in charge of the internal structure and the mobile part of the machine. AddUp also manages the control board and the sensors that monitor the process. On the software side, AddUp has developed the machine’s PLC. This software has several functions, it allows communication with the ground by sending different types of data (measurements, photos, reports, etc.) from the machine and by executing the commands it receives.