Combining Traditional Manufacturing with Additive –
Adding Features with Directed Energy Deposition
INDUSTRY
Aerospace
CHALLENGE
Can Directed Energy Deposition provide an optimized, cost effective solution in a market already proven out by Powder Bed Fusion?
NO SUPPORTS
CREATIVE SHAPE
REDUCED LEAD TIME
MASS REDUCTION
History
Rocket nozzles were traditionally manufactured using subtractive processes like milling and turning, but these techniques are usually limited to less complex nozzles today. Additive manufacturing has steadily seen adoption in the aerospace industry since the mid 2000s using Powder Bed Fusion technologies, when Aerospace companies started recognizing the benefits of PBF for rapid prototyping, creating complex components, and producing flight-critical parts.
Challenge
While powder bed fusion technology can create custom, optimized rocket nozzles, it is difficult to print large-scale components and lacks the ability to add to or repair features on a pre-existing part.
Solution
Directed Energy Deposition is well-suited for manufacturing larger and bulkier components. The Magic 800 was selected to test the feasibility of an optimized rocket nozzle concept due to it’s large, 1200 x 800 x 800 mm build volume and ability to add additional features. As printing an entire jet engine cone would have been excessively expensive to prototype with DED alone, the process instead used a combination of additive and traditional technologies. An isogrid, which helps create an ultra strong, but lightweight structure that is widely used in the aerospace industry, would be added to a traditionally manufactured hopper cone.
Results
We began this proof of concept project by purchasing a large, pre spun 304 stainless steel hopper cone from a local manufacturer for $600*.
The cone was secured onto the baseplate of the M800, and the isogrid structure was fused directly onto the surface using powder Inconel 625, a material well known in the aerospace industry for it’s strength and resistance to high temperatures. The pattern took a total of 16 hours to complete in 5-Axis configuration with a minimum wall thickness of 0.8mm.
After cooling, the part was removed from the machine and the top point of the cone was cut off to add the vase structure. This last section was printed in only 2 hours without any supports. DED has proven it’s capabilities to combine two different materials and manufacturing techniques to create a more cost efficient solution.
The final build was completed in 18 total print hours and sits at a finished size of 32 x 30 inches.
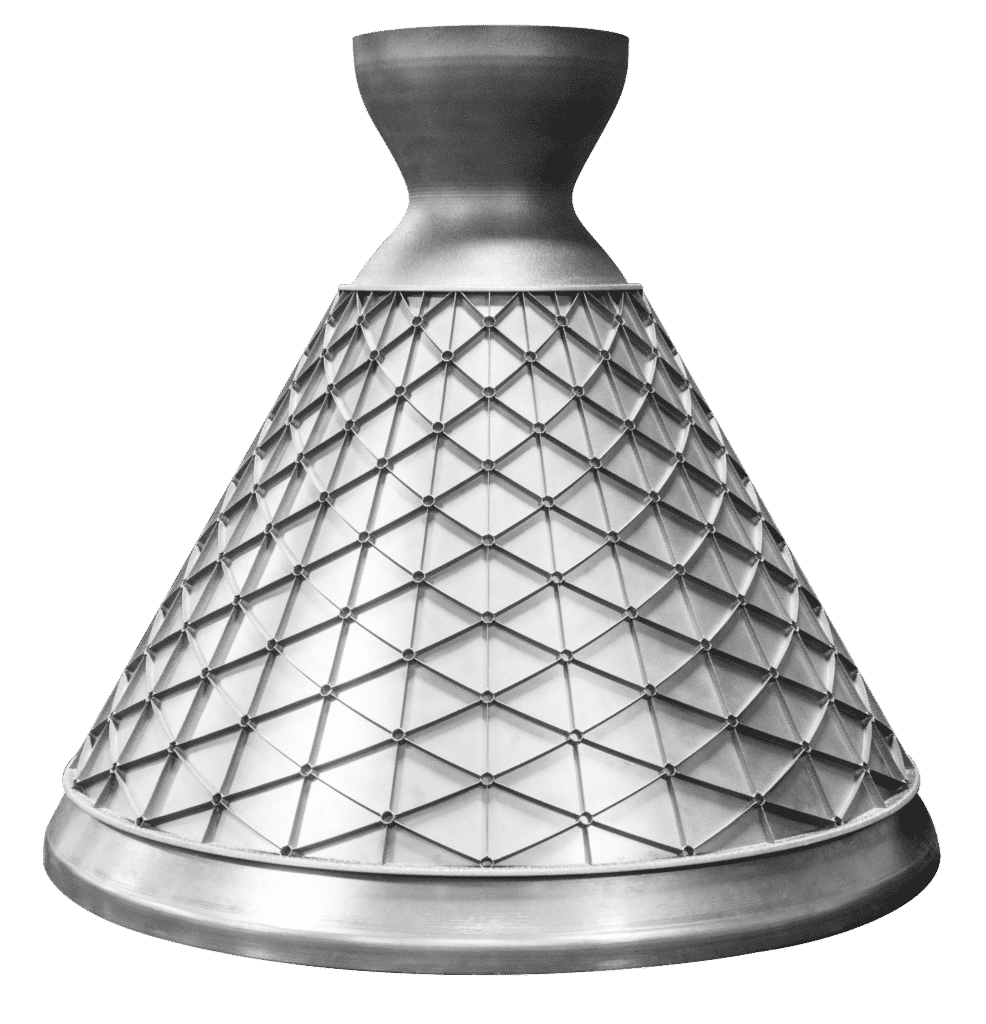
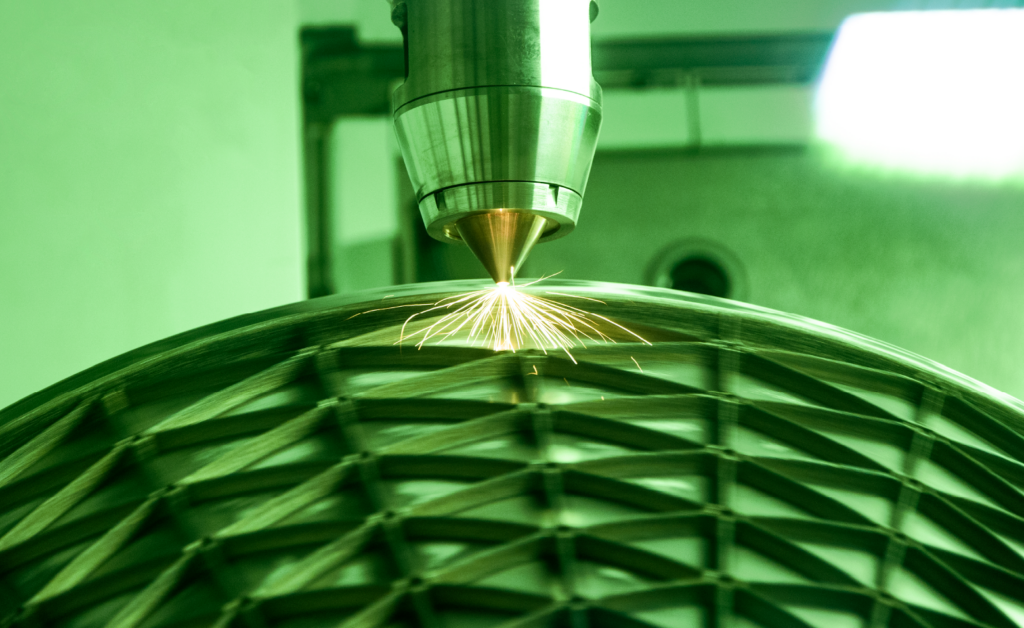
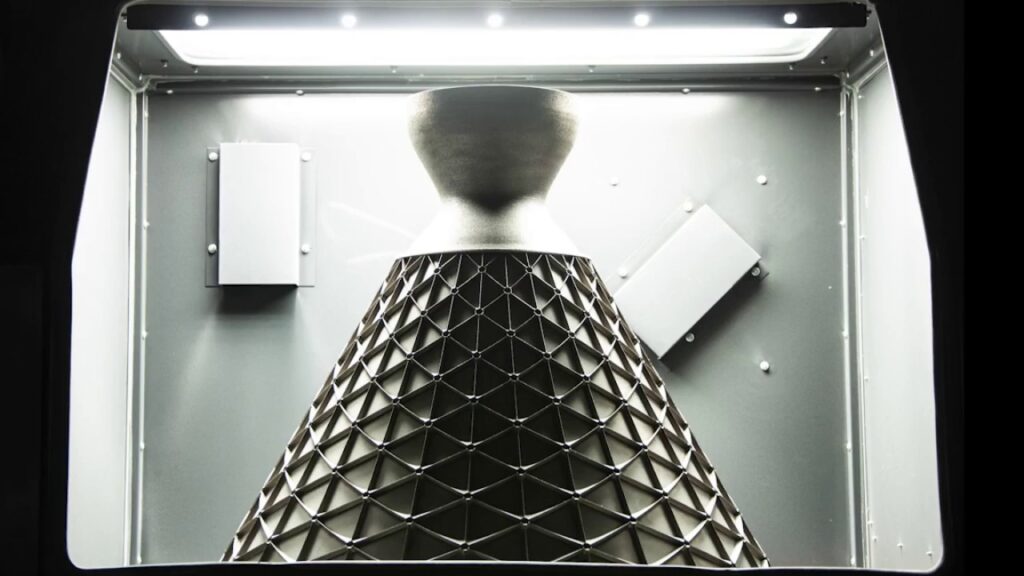
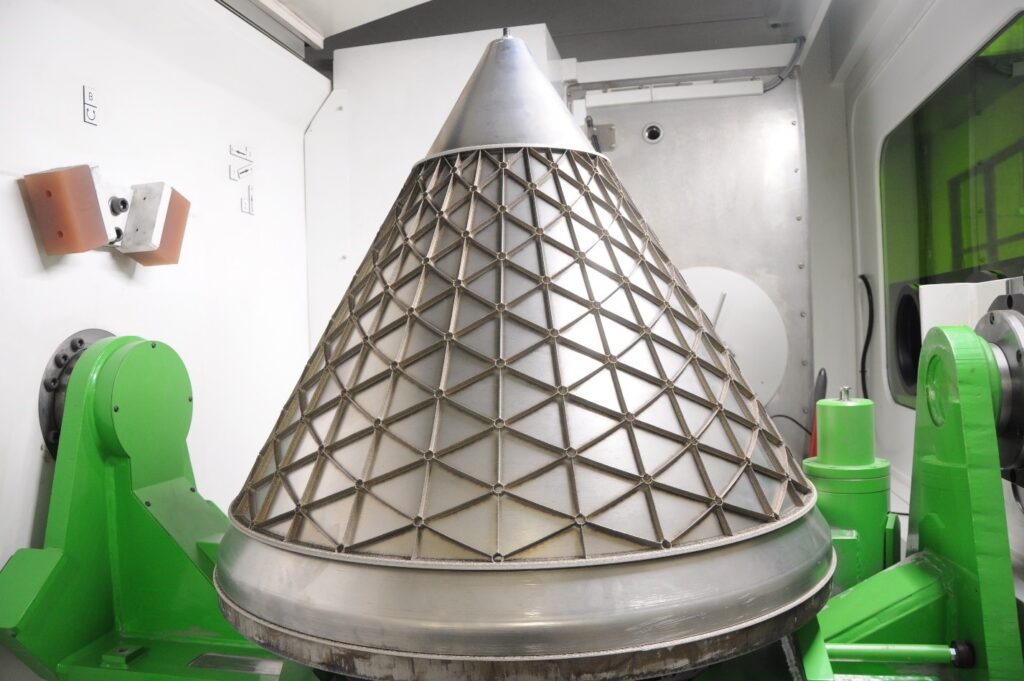
-
Reduced weight
-
Larger material selection
-
Reduced waste