Hydraulic blocks are present in most machines and devices, throughout a variety of industries. In the case of this hydraulic block, the entire part is 3D printed in a single operation.
Hydraulic blocks are present in most machines and devices, throughout a variety of industries. In the case of this hydraulic block, the entire part is produced in a single operation. Read the case study about the advantages of additive manufacturing in 3d printing.
CHALLENGE
3D printing of an optimized hydraulic block, in one piece
RESULTS
In the following case, the mass was reduced by 82% and the length of the block was reduced from 495 mm to 348 mm while keeping the functional surfaces identical. The parallelepiped shape allows for the reworking of high-precision bores.
KEY BENEFITS
- 82% Mass Reduction
- 30% Size Reduction
- Creation of internal channels
Context
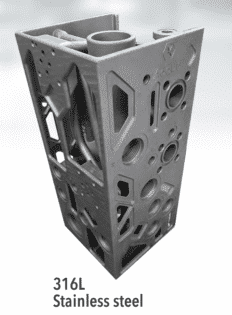
Hydraulic blocks are present in most machines and devices, throughout a variety of industries: aeronautics, energy, automotive, etc. (land or naval transport, aeronautics, space, energy, etc.).
The role of these parts is to distribute fluids, often under high pressure. The mass of hydraulic blocks plays an important role in many applications and their volume depends on how they are made.
In most cases, they are made by machining blocks of raw metal. The pipes are drilled and then plugged where necessary to ensure the fluid transfer function. The changes of direction are therefore made at 90°, which generates pressure losses, and the plugs are a risk of leakage.
The Advantages of Additive Manufacturing
Metal additive manufacturing allows pipes to be made without connections or blockages, and therefore without the risk of leakage or pressure loss. The structures that hold the pipes together are kept to a minimum to reduce mass.
In the case of this hydraulic block, the entire part is produced in a single operation, with its markings and threads. This part is successful because it can be produced quickly, it is l created with less material, therefore, reducing its weight and it can be used immediately.