AddUp 3D printed a spherical tank that can hold the operating pressure of 60 bar for two-phase fluid loop applications using fluids in a supercritical state at maximum non-operating system temperature.
ADS (Airbus Defence and Space) partners with AddUp to produce a spherical tank that can hold the operating pressure of 60 bar for two-phase fluid loop applications using fluids in a supercritical state at maximum non-operating system temperature. Read the case study about the challenge and solutions of metal 3d printed parts.
INDUSTRY
Aerospace
CHALLENGE
To 3D print a sealed tank that can hold the operating pressure of 60 bar for fluid loop application.
KEY BENEFITS
- A single component
- Part printed with no support inside
- Reduce the mass of the part
Mass Reduction
Performance
History: AddUp and ADS
ADS (Airbus Defence and Space) is an Airbus Group division that is one of the world’s top 10 defense and space industry players. It is specialized in military aircraft, drones, missiles, space launchers, and artificial satellites. ADS wishes to evaluate the feasibility of additive manufacturing parts such as hollow stainless-steel spheres. The objective is to produce a sealed tank that can hold the operating pressure of 60 bar for two-phase fluid loop applications using fluids in a supercritical state at maximum non-operating system temperature.
This tank can be used in a two-phase heat exchanger. At ambient temperature, the working fluid contained in the system is above its critical temperature, meaning it is entirely gaseous. The purpose of this tank is to increase the volume of the fluid loop system to limit the internal pressure for a given temperature.
Challenges of printing a sealed tank
The existing technique to make the tank is using a cylinder and machined hemispherical shells welded together. This design makes the final part too massive, and the welded areas are overstressed during the time of pressurization. ADS asked AddUp to address these issues and produce a tank using metal 3D printing to free itself from the constraints of conventional processes. With this new design freedom, the tank can be spherical, an ideal geometry to withstand pressure. The biggest technical challenge in this project was to print a sphere without support inside.
The manufacturing specifications:
- 316L stainless steel material
- Withstand a 60-bar pressure
- A single component without assembly
- No internal supports
- As light as possible while handling the pressure requirements
- Spherical design
Solution for a 3D printed spherical tank
To manufacture the sphere, the FormUp® 350 was chosen because it can be equipped with a roller recoating system and fine powder. This machine in this configuration allows for large overhang surfaces to be built without supports.
The 316L stainless steel was chosen for this application for its corrosion resistance, which allows durability.
Results and benefits of additive manufacturing
AddUp , a metal 3D parts manufacturer, successfully printed the new geometry provided by ADS and did not need to modify it thanks to the capabilities of the FormUp® 350. The final dimensions are 78 mm internal diameter with a thickness of 2.2 mm.
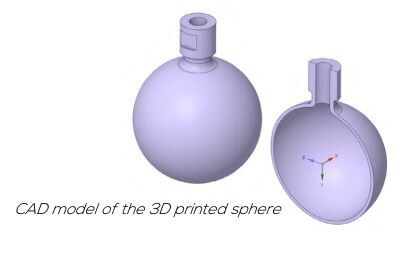
More information about Airbus Defence and Space here.
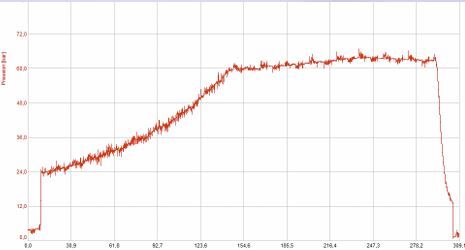
-
The combined use of the roller and the fine powder allowed the production of thin walls with a perfect surface finish. The surface inside the part is clean and does not need any post-processing.
-
The 3D-printed parts held the 60 bar water pressure for two minutes, enough to check the pressure containment.
-
The exterior of the new metal part has been machined to ensure a constant thickness over the entire sphere and to eliminate the surface defects inherent to the process.
“Airbus Defence and Space SAS has a large experience in developing innovative Additive Manufactured products with AddUp. This new demonstrator shows the technical expertise of AddUp to manufacture innovative designs to allow Airbus DS to propose breakthrough and high-value applications. This design would not have been possible without fine power/roller technology developed by AddUp. It opens a new door to more innovative designs”
- Delphine Carponcin, Additive Manufacturing Project Manager, Airbus Defence and Space